Il Delta Racing Team della Mannheim University of Applied Sciences ha collaborato con il produttore di stampanti 3D Eplus 3D con sede a Hangzhou per produrre parti di uso finale per l’ evento Formula Student Electric di quest’anno .
Formula Student è un concorso di progettazione ingegneristica che vede gli studenti universitari costruire le proprie auto da corsa. Le squadre vengono quindi affrontate l’una contro l’altra in un evento di corse annuale con una pista in stile Formula 1.
Utilizzando una stampante 3D in metallo EPlus 3D EP-M250Pro, il Delta Racing Team ha integrato per la prima volta un set di portaruota in alluminio topologicamente ottimizzati nella sua auto da corsa. Secondo quanto riferito, le parti stampate in 3D hanno portato a un risparmio di peso di oltre il 50% rispetto ai componenti originali fresati a CNC, un enorme vantaggio in termini di prestazioni nel mondo degli sport motoristici.
Non è un segreto che in pista il peso gioca un ruolo importante nelle prestazioni di un veicolo. Da quando esistono gli sport motoristici, le squadre di corse si sono sforzate di alleggerire ogni componente delle loro auto, spremendo ogni millisecondo possibile da un design. Ciò include il supporto della ruota, che ha il compito di supportare il cuscinetto della ruota di un’auto, e quindi anche la ruota stessa. Serve ad assorbire e trasmettere le forze tra l’asfalto e il resto del telaio dell’auto.
Per la serie di gare di quest’anno, il Delta Racing Team ha utilizzato una tecnica di progettazione assistita da computer chiamata ottimizzazione della topologia per ottimizzare i componenti del portaruota. L’approccio funziona simulando computazionalmente i carichi sperimentati da una parte e generando una geometria più adatta ad affrontarli, il tutto eliminando qualsiasi materiale non necessario per massimizzare le prestazioni della parte.
In totale, il team corse di Mannheim ha eseguito un totale di 18 casi di carico per informare il progetto, incluso il massimo impatto verticale, frenata in una buca, frenata in retromarcia e un caso di curvatura estrema.
Prima che i supporti delle ruote potessero essere stampati in alluminio, sono stati prototipati in PLA a basso costo su una stampante 3D FDM. Ciò ha dimostrato la producibilità del progetto e le parti finali sono state fabbricate su un sistema di fusione a letto di polvere EP-M250Pro di livello industriale.
Per rimuovere la struttura dalla piastra di costruzione, il team ha ricotto la piattaforma in un forno a vuoto per ridurre le sollecitazioni all’interno delle parti. Quindi, con l’ausilio di una macchina elettroerosione, i componenti sono stati sollevati dalla lamiera e le strutture di supporto sono state rimosse. Le fasi finali della post-elaborazione prevedevano la sabbiatura delle parti stampate in 3D per migliorare la qualità della superficie e la lavorazione di alcuni bordi su un CNC a 5 assi per perfezionare la precisione dimensionale.
Quando tutto è stato detto e fatto, i portaruota stampati in 3D pesavano 550 g ciascuno, una riduzione del 50% rispetto alle controparti prodotte in modo convenzionale dell’anno precedente. Con il nuovo design, tutte le forze attorno alla ruota appartenevano a masse non sospese, nel senso che agivano direttamente sul veicolo senza essere ritardate da molle e ammortizzatori. La significativa riduzione delle masse non sospese ha determinato un notevole aumento dell’agilità e della maneggevolezza.
I settori automobilistico e automobilistico sono stati i principali utilizzatori della stampa 3D negli ultimi anni. All’inizio di quest’anno, il team NASCAR Stewart-Haas Racing si è rivolto alla stampa 3D per produrre pedali dei freni finali più leggeri del 32% rispetto alle loro controparti convenzionali. Lavorando con Autodesk, il team è riuscito a utilizzare il software di progettazione generativa Fusion 360 per migliorare anche la rigidità e la sicurezza complessiva dei componenti.
Altrove, il team Kawasaki Puccetti Racing ha recentemente integrato la scansione 3D e la stampa 3D nei suoi flussi di lavoro quotidiani , rivelando che ha utilizzato la produzione additiva per vincere il Round 5 del Campionato Mondiale Superbike in Italia nel 2019. In particolare, il team ha utilizzato una RangeVision Scanner 3D per scansionare la sua moto da corsa Kawasaki e ottimizzato la carenatura del modello 3D utilizzando algoritmi di modellazione aerodinamica.
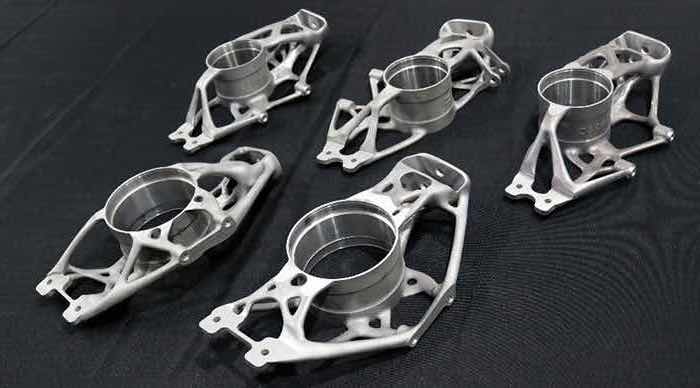