COMUNICATO STAMPA
Maschera a filamento: stampa 3D con maschere riciclate
Come prima linea di difesa contro la diffusione del COVID-19, la mascherina, una semplice copertura indossata per ridurre la diffusione di agenti infettivi, ha colpito la vita di miliardi di persone in tutto il mondo. Si stima che ogni mese vengano utilizzate 129 miliardi di mascherine, di cui la maggior parte sono progettate per essere monouso. Naturalmente, ciò rappresenta una sfida di immensa portata per mitigare l’impatto dei dispositivi di protezione individuale (DPI) in disuso sul nostro ambiente.
Il nostro laboratorio qui all’Università di Bristol si concentra principalmente su questioni relative alla prototipazione rapida. Siamo stati coinvolti in numerosi progetti di tipo “hack the pandemic” sin dallo scoppio del COVID-19, condividendo la nostra conoscenza della prototipazione rapida con la comunità dei maker in generale. Pertanto, i nostri lavori sotto il titolo di Project Clean Access (PCA), un’iniziativa di laboratorio DMF finanziata dalla Royal Academy of Engineering, hanno precedentemente contribuito a progetti per interventi fisici a basso costo per ridurre la trasmissione di COVID-19.
Tuttavia, poiché le restrizioni vengono lentamente revocate e un senso di normalità ritorna in molti campus in tutto il Regno Unito, è evidente che ora stiamo affrontando un problema completamente diverso; la pervasività dei rifiuti di DPI nel nostro ambiente locale.
Possiamo trasformare i rifiuti dei DPI in qualcosa di utile per la società?
Nel corso degli anni abbiamo esaminato a fondo le tecnologie, i metodi e i materiali di stampa 3D e dopo aver realizzato che la comune maschera facciale blu non è ” una sorta di carta” ma di solito un prodotto a base di polimeri con un’alta percentuale di polipropilene (PP), abbiamo ha iniziato a riflettere sulla possibilità di trasformarlo in qualcosa con cui potremmo stampare in 3D su una stampante desktop.
Ciò ha sollevato per noi una domanda interessante: possiamo trasformare i rifiuti dei DPI in qualcosa di utile per la società, trasformando le mascherine usa e getta in un filamento per la stampa 3D?
Gli inquinanti dei DPI sono un problema globale. Questo è stato fotografato a Bristol, nel Regno Unito
Le sezioni seguenti di questo post documentano le varie fasi e i risultati di interesse nel passaggio dalla maschera facciale al filamento.
L’acquisto di mascherine
L’equipaggiamento
in lavorazione
Estrusione del filamento
Stampa con mascherine
Risultati e discussione
Ringraziamenti
3,400,000,000
Numero di mascherine o protezioni per il viso scartate giornalmente secondo uno studio recente
Articolo del National Geographic
1: L’acquisto di mascherine
Ci siamo messi in contatto con Hardshell UK , un produttore leader di DPI con sede a Cardiff, desideroso di essere coinvolto e che ha fornito in modo molto generoso 1 kg di maschere facciali in polipropilene di tipo IIR gratuitamente! Le mascherine (nella foto sotto) sono prodotti chirurgici certificati e conformi alle norme EN14683:2019 Tipo IIR.
Una scatola di mascherine chirurgiche di tipo IIR
SPECIFICHE DELLA MASCHERA
Lunghezza maschera: 175 mm
Larghezza maschera (prima piega): 175 mm
Larghezza maschera (dopo la piega): 95 mm
Lunghezza del filo del naso: 100 mm
Lunghezza anello auricolare (un lato): 180 mm
CARATTERISTICHE
Filo nasale unipolare in PP da 3 mm integrato e regolabile con anima in acciaio da 0,5 mm
Anello auricolare in fibra non tessuta saldato ad ultrasuoni da 3 mm (senza lattice)
Struttura a tre strati:1° strato: PP Spunbond 25 gsm (Blu)
2° strato: PP Meltblown 25 gsm
3° strato: PP Spunbond 25 gsm (bianco)
Le mascherine utilizzate in questo lavoro erano difetti di fabbricazione e non idonee alla vendita. I problemi più comuni sono le saldature dell’anello dell’orecchio fallite e l’occasionale filo nasale mancante.
2: L’attrezzatura
Dopo aver studiato i metodi per produrre un filamento, abbiamo trovato frequenti menzioni del kit Filastruder , un prodotto open source progettato per la comunità dei produttori per riciclare i rifiuti di plastica stampati in un filamento per la stampa 3D. La macchina offre un design semplice ma funzionale con la possibilità di modificare le parti secondo necessità. Il kit vanta anche una vasta comunità online di utenti che condividono configurazioni, progetti di parti ed esperienza con l’estrusione di una gamma di polimeri/polimeri sia convenzionali che più esotici.
SPECIFICHE
Motore GF45 : 12 V CC, 8 giri/min, coppia 15,6 Nm, 1,6 A
Tasso di estrusione tipico: 5-8 ore per kg (2,2 libbre) (10-36 pollici/min, a seconda del diametro, del materiale e della temperatura)
Temperatura di estrusione: temperatura ambiente fino a 260°C.
Alimentazione: 110-240 V CA, 50/60 Hz, 60 watt di picco, 50 watt in media (costo elettrico: ~ £ 0,07 per kg estruso)
L’immagine sopra mostra l’assemblaggio barebone del kit Filastruder prima di aggiungere il controller e il cablaggio. Abbiamo inoltre acquistato il kit gratuito ‘Filawinder’, un dispositivo che aiuta ad avvolgere il filamento e aumenta la consistenza diametrale del materiale estruso. In totale entrambi i dispositivi costano circa £ 345 più spese di spedizione dagli Stati Uniti.
Un video del kit assemblato è mostrato nella sezione 4.
Plastica mascherata!”Mascherine, guanti e salviette sono realizzati con più fibre di plastica, principalmente polipropilene, che rimarranno nell’ambiente per decenni, forse secoli, frammentandosi in microplastiche e nanoplastiche sempre più piccole. Una singola maschera facciale può rilasciare fino a 173.000 microfibre al giorno nei mari, secondo uno studio in Environmental Advances.” National Geographic.×IGNORA AVVISO
3: Elaborazione
Ci siamo resi conto attraverso le prime sperimentazioni che la composizione fibrosa delle maschere rappresentava una sfida a qualsiasi metodo convenzionale di riciclaggio della plastica. Anche altri ricercatori identificano questa come la causa di molte “macchine intasate”. Per ovviare a questo problema introduciamo un passaggio prima della macinazione in cui le maschere vengono riscaldate e pressate per formare un foglio duro; l’idea è che portando il materiale al suo punto di transizione vetrosa possiamo fondere le fibre di polipropilene per creare qualcosa con più rigidità. Per fare questo abbiamo semplicemente utilizzato un ferro da stiro e della carta antiaderente.
I fogli rigidi sono stati quindi frantumati in pezzetti più piccoli per essere lavorati attraverso un frullatore (Breville Blend Active da 300 W) ottenendo i fini granuli di PP blu maschera facciale nella foto a destra. Per confronto, viene mostrato anche il materiale ABS campione fornito da Filastruder. Questo processo di aumento della rigidità migliora i risultati dell’estrusione riducendo l’instabilità della pressione nella canna dell’estrusore di filamento e, inoltre, impedisce alle fibre di inceppare la macchina. I granuli blu sono ciò che inseriamo nell’estrusore per produrre il filamento.
Per affrontare le preoccupazioni relative a qualsiasi contaminazione del materiale prodotto, va notato che le maschere vengono riscaldate durante tutto il processo di estrusione a una temperatura molto superiore a quella a cui è stato dimostrato che SARS-CoV-2 sopravvive. Un’altra questione da considerare è la pre-elaborazione delle maschere, ad esempio la rimozione di passanti per le orecchie e cinturini metallici per il naso. Questi sono abbastanza facili da rimuovere manualmente, anche se potrebbero presentare difficoltà nell’automazione del processo di smistamento/preparazione. È possibile che in futuro agli utenti venga richiesto di separare queste parti prima del riciclaggio.
4: Estrusione del filamento
Come promesso nella sezione 2, questo video mostra la nostra configurazione più recente del kit di estrusione del filamento in azione. Optiamo per il montaggio verticale del Filastruder e stampiamo una tramoggia verticale per lavorare con questa disposizione.
Impostazioni di estrusione
Temp. ugello : 170 C
Voltaggio: 11V (abbassato per ridurre la velocità)
Ampere : 1,6 (limitato di corrente)
Raffreddamento : acceso
Diametro del foro dell’ugello : 1,75 mm
Filawinder: velocità automatica
Questa configurazione ha prodotto buoni risultati, tuttavia ci sono ancora problemi con il raggiungimento di un diametro del filamento coerente.
Tuttavia, 7 metri di filamento ” utilizzabile ” sono stati in bobina con un diametro medio di 1,5 mm (-0,25 mm al di sotto dello standard di 1,75 mm). I risultati iniziali indicano che con un ulteriore perfezionamento sarà possibile ottenere il diametro desiderato entro una ragionevole tolleranza. Al momento della stesura di questo post, l’ugello standard è già stato perforato da 1,75 mm a 1,9 mm e le parti per un’alimentazione verticale motorizzata vengono stampate in 3D. Il miglioramento di questi aspetti del sistema dovrebbe avvicinarci al diametro ideale del filamento di 1,75 mm.
Utilizziamo questo primo lotto di filamento per eseguire alcuni test in fase iniziale con una stampante 3D desktop Fused Filament Fabrication (FFF).
5: Stampa con maschere facciali
Il polipropilene (PP) è notoriamente difficile da stampare in 3D in quanto non si lega bene alle comuni piattaforme di costruzione di stampanti. Tuttavia, si lega bene a se stesso, PP. Un trucco è quindi quello di stampare su normale nastro trasparente poiché spesso si tratta anche di PP. Utilizzando questo metodo è stato sorprendentemente semplice stampare in 3D con il nostro rudimentale stock di filamento su una macchina a basso costo. È molto evidente che attualmente i problemi risiedono nella produzione del filamento e non nella stampa 3D con esso.
Impostazioni di stampa
Stampante: Creality Ender 3 max
Temp. ugello : 235 C
Temperatura letto : 100 C
Velocità di stampa: 40 mm/s (lenta)
Velocità della ventola: 100%
Retrazione: 4 mm (Bowden)
Velocità di retrazione: 30 mm/s
Portata: 350% (considerare il filamento più sottile)
Troviamo che queste impostazioni abbiano funzionato bene considerando l’incoerenza nel diametro del filamento.
Sebbene non sia molto utilizzato come materiale nella stampa 3D, alcune proprietà del PP lo rendono un’alternativa che vale la pena esplorare. Questi includono la durabilità dei materiali e la resistenza agli agenti chimici e alla fatica. Il polipropilene è anche adatto per alimenti e microonde.
Oltre ai punti precedenti, il PP è uno dei polimeri più comuni in uso. Da un punto di vista ambientale l’uso del Polipropilene riciclato, e dei polimeri in generale, rappresenta un’opportunità per ridurre il consumo di materiale vergine nei processi di prototipazione rapida come la stampa 3D e lo stampaggio a iniezione.
Circa un terzo di una maschera facciale è stato utilizzato per stampare in 3D questa parte
6: Risultati e discussione
Sebbene sia necessario un ulteriore lavoro per migliorare le tolleranze del nostro filamento estruso, la parte stampata in realtà non ha un aspetto così male… il che è alquanto sorprendente, dato che è interamente stampata in 3D con maschere usa e getta.
Naturalmente, queste sono condizioni abbastanza idealizzate, le nostre maschere sono al 100% in polipropilene e non sono mai state indossate. Posizioniamo quindi questo lavoro come un passo verso una migliore comprensione delle sfide nel riciclaggio di questo tipo di DPI e ispiriamo anche gli altri a interessarsi a questo problema.
Le aree che identifichiamo per il lavoro futuro includono:
Questo processo sarebbe fattibile su scala più ampia?
La lavorazione di materiali misti, ad es. una gamma di maschere di tipo simile potrebbe essere passata attraverso la stessa macchina e questo produrrebbe qualcosa di utile?
La natura fibrosa di queste maschere potrebbe essere sfruttata per l’uso nei compositi?
Quali sono le migliori pratiche per la raccolta dei rifiuti di DPI per il riciclaggio?
Le istituzioni (come le università) potrebbero creare la propria economia circolare dei DPI? Supervisionare la distribuzione, la raccolta e il riciclaggio dei DPI.
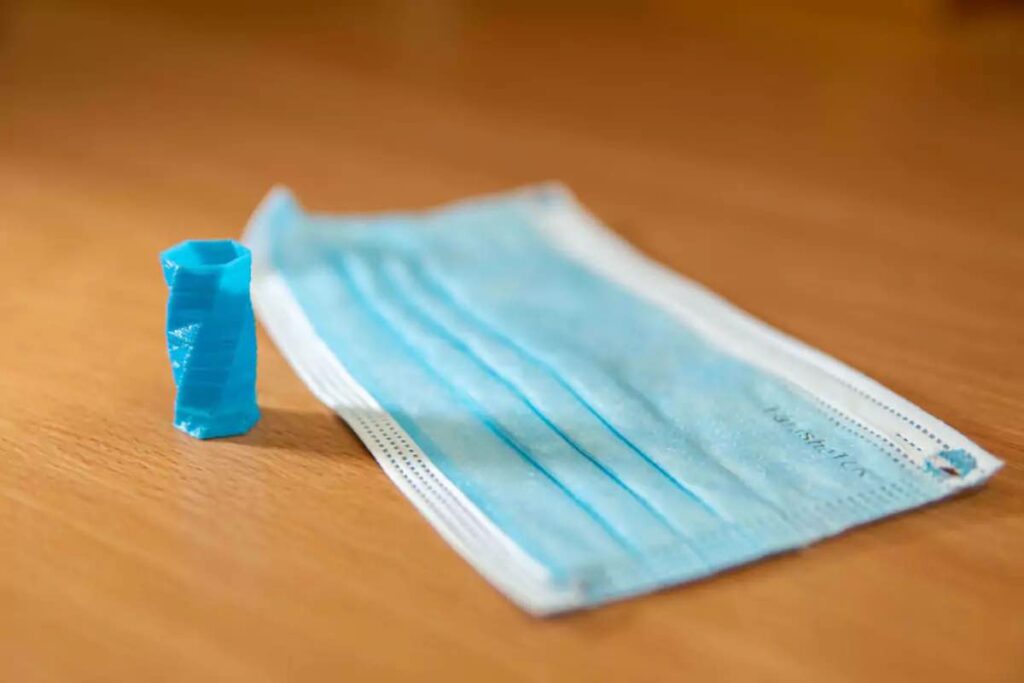