la stampa 3D nella nuova Peugeot 308
Peugeot reinventa gli accessori per auto grazie all’innovativa tecnologia di stampa 3D e a un nuovissimo polimero flessibile
Peugeot reinventa gli accessori per auto grazie all’innovativa tecnologia di stampa 3D e a un nuovissimo polimero flessibile . Disponibile nello shop PEUGEOT LIFESTYLE , una gamma di accessori tra cui un porta occhiali da sole, un porta lattine e un porta telefono/carte è stata creata appositamente per la nuova Peugeot 308. È la prima volta che la tecnologia di stampa 3D viene utilizzata sugli accessori per auto , un’innovazione che sembra molto promettente per l’intera industria automobilistica.
Questi accessori sono il risultato di uno sforzo congiunto dei team di progettazione, prodotto e ricerca e sviluppo di Peugeot in collaborazione con HP Inc., Mäder ed ERPRO . Sono stampati in 3D utilizzando la nuova tecnologia di stampa 3D HP Multi Jet Fusion (MJF). L’obiettivo è quello di offrire prodotti innovativi, piacevoli al tatto, leggeri, solidi e facili da usare , che valorizzino il benessere interno offerto dalla 308 e dal suo nuovo Peugeot i-Cockpit.
Un passaggio all’innovazione industriale
L’obiettivo dei designer all’inizio del progetto era quello di rendere gli accessori più visibili e attraenti innovando e utilizzando materiali moderni .
La gamma degli accessori è stata elaborata dopo un’analisi dettagliata di come i clienti utilizzano il rimessaggio in auto. Poiché i materiali tradizionali non soddisfacevano le specifiche, il team “Colori e materiali” di Peugeot Design ha collaborato con i suoi partner per sviluppare un materiale con un aspetto più innovativo. La stampa 3D era la soluzione ovvia.
Flessibile ed ecologico: la tecnologia del futuro.
La stampa 3D è uno dei pilastri fondamentali della quarta rivoluzione industriale . Con questa nuova tecnologia è possibile aumentare la flessibilità , adattandosi alle esigenze di un mercato sempre più esigente e imprevedibile. Tutti i tipi di oggetti e accessori personalizzati possono essere prodotti senza bisogno di costosi stampi e strumenti di produzione .
La stampa 3D è anche migliore per l’ambiente , una caratteristica molto importante nella nostra ricerca di processi di produzione sostenibili che risparmino risorse e rifiuti . Il suo utilizzo sta diventando sempre più diffuso e sta rivoluzionando il sistema produttivo in molti settori. In effetti, la produzione additiva sta diventando un’alternativa alle tecniche di produzione come lo stampaggio a iniezione .
Perché abbiamo fatto questa scelta?
La stampa 3D offre molti vantaggi aggiuntivi:
Libertà di progettazione : meno vincoli di produzione e infinite possibilità di complessità delle parti (a causa dell’assenza di stampaggio a iniezione). La stampa 3D apre nuovi spazi creativi per i designer.
Strutture ottimizzate : peso ridotto , maggiore resistenza , minor numero di assemblaggi, flessibilità grazie all’utilizzo della rete.
Produzione agile : infinite possibilità di personalizzazione, produzione in serie con tempi di consegna ridotti e nessuna necessità di stoccaggio grazie alla produzione “on demand”.
Inoltre, questa tecnologia è in continua evoluzione, sia in termini di materiali utilizzati che di metodi di produzione. E i costi di produzione continuano a scendere.
Un materiale estremamente innovativo.
In pochi mesi, i team hanno sviluppato insieme un nuovo polimero che presenta 3 vantaggi principali:
Flessibilità : un polimero flessibile, malleabile e robusto,
Velocità : il processo di fabbricazione è molto breve e su misura,
La qualità del rendering : dettagli estremamente accurati grazie a molecole molto fini.
Il materiale flessibile utilizzato è il poliuretano termoplastico Ultrasint (TPU), frutto di una partnership tra HP Inc. e BASF . Questo materiale offre parti durevoli, resistenti e flessibili. È un materiale perfetto per parti che assorbono gli urti che richiedono un’elevata elasticità e per strutture flessibili a maglia. Il materiale può essere utilizzato per produrre parti con un’elevata qualità superficiale e un livello di dettaglio molto elevato .
L’uso del TPU negli interni di un’auto è un nuovo approccio, che è stato brevettato dal Gruppo STELLANTIS .
I segreti di una manifattura rivoluzionaria
Peugeot ha scelto di utilizzare la tecnologia di stampa 3D HP Multi Jet Fusion (MJF). HP Multi Jet Fusion è una nuovissima tecnologia di produzione additiva strato per strato su letto di polvere. Peugeot è stata una delle prime a utilizzare questa tecnologia nello sviluppo della gamma di accessori 3D.
Come funziona la produzione additiva?
Il processo inizia con il trasferimento di un file CAD digitale (computer aided design) su una stampante 3D, in questo caso una stampante 3D HP Multi Jet Fusion. Il processo funziona depositando un legante su una polvere combinando:
Un legante per fondere la polvere
Un agente specifico, noto come detailer per “levigare” la superficie.
Fase di stampa:
HP Multi Jet Fusion utilizza una testina di stampa per applicare selettivamente agenti di fusione e dettagli su un letto di polvere polimerica, che viene poi fuso da elementi riscaldanti per formare uno strato solido.
Dopo ogni strato (80 µm di spessore), viene aggiunta altra polvere al letto precedente e il processo si ripete fino al completamento della parte.
Fase di post-elaborazione:
Quando la costruzione è completa, l’intero letto di polvere con le parti incapsulate viene inviato a una stazione di lavorazione dove la maggior parte della polvere rimanente viene rimossa mediante aspirazione sotto vuoto;
Le parti vengono quindi sabbiate per rimuovere i residui di polvere prima di passare al reparto di finitura, dove vengono verniciate per migliorarne l’estetica.
La stampa 3D ha un futuro in Peugeot
La stampa 3D è ancora agli albori nel settore automobilistico. Questa tecnologia è destinata ad essere sviluppata in serie, non solo sulla gamma di accessori, ma anche su parti più tecniche dei prossimi modelli Peugeot. I vantaggi di questa tecnologia offrono infinite possibilità.
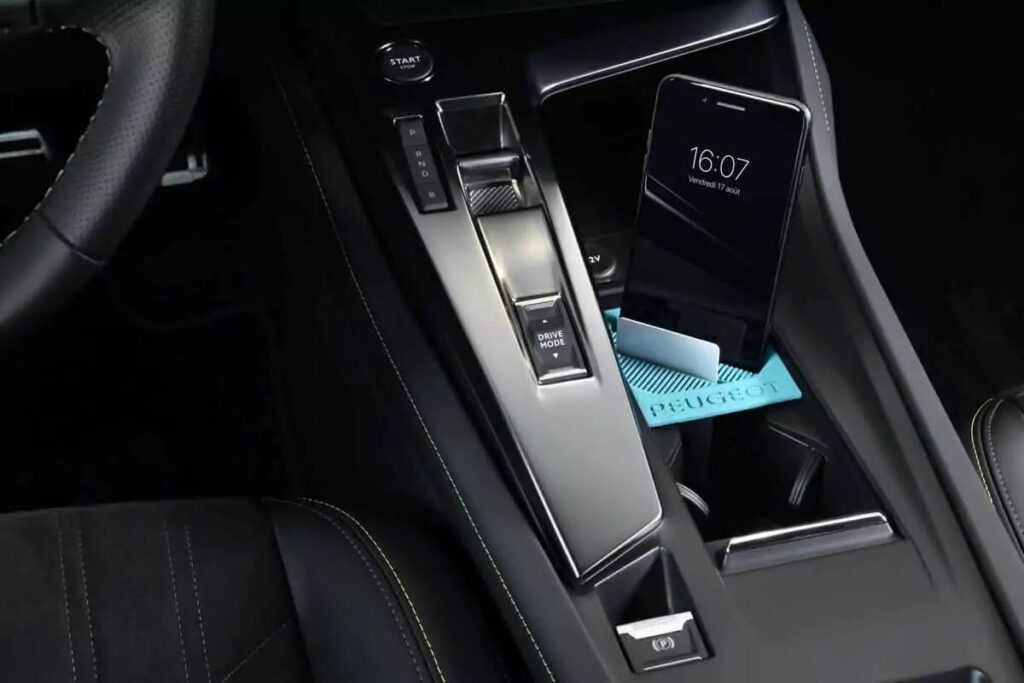