Gli ingegneri hanno creato stampanti 3D intelligenti in grado di rilevare e correggere rapidamente errori, anche in progetti mai visti prima, o materiali sconosciuti come ketchup e maionese, imparando dalle esperienze di altre macchine.
Gli ingegneri, dell’Università di Cambridge, hanno sviluppato un algoritmo di apprendimento automatico in grado di rilevare e correggere un’ampia varietà di errori diversi in tempo reale e può essere facilmente aggiunto a macchine nuove o esistenti per migliorarne le capacità. Le stampanti 3D che utilizzano l’algoritmo potrebbero anche imparare a stampare nuovi materiali da sole. I dettagli del loro approccio a basso costo sono riportati nella rivista Nature Communications .
La stampa 3D ha il potenziale per rivoluzionare la produzione di parti complesse e personalizzate, come componenti di aeromobili, impianti medici personalizzati o persino dolci intricati, e potrebbe anche trasformare le catene di approvvigionamento manifatturiere. Tuttavia, è anche vulnerabile a errori di produzione, da imprecisioni su piccola scala e debolezze meccaniche fino a errori di costruzione totali.
Attualmente, il modo per prevenire o correggere questi errori è che un lavoratore specializzato osservi il processo. L’operatore deve riconoscere un errore (una sfida anche per l’occhio allenato), interrompere la stampa, rimuovere la parte e regolare le impostazioni per una nuova parte. Se viene utilizzato un nuovo materiale o una nuova stampante, il processo richiede più tempo man mano che il lavoratore apprende la nuova configurazione. Anche in questo caso, gli errori potrebbero non essere rilevati poiché i lavoratori non possono osservare continuamente più stampanti contemporaneamente, soprattutto per le stampe lunghe.
“La stampa 3D è impegnativa perché c’è molto che può andare storto, e quindi molto spesso le stampe 3D falliscono”, ha affermato il dottor Sebastian Pattinson del Dipartimento di Ingegneria di Cambridge, autore senior del documento. “Quando ciò accade, tutto il materiale, il tempo e l’energia che hai usato sono persi.”
Gli ingegneri hanno sviluppato il monitoraggio automatizzato della stampa 3D, ma i sistemi esistenti possono rilevare solo una gamma limitata di errori in una parte, un materiale e un sistema di stampa.
“Ciò che serve davvero è un sistema di ‘auto senza conducente’ per la stampa 3D”, ha affermato il primo autore Douglas Brion , anche lui del Dipartimento di Ingegneria. “Un’auto senza conducente sarebbe inutile se funzionasse solo su una strada o in una città: deve imparare a generalizzare in diversi ambienti, città e persino paesi. Allo stesso modo, una stampante “senza driver” deve funzionare per più parti, materiali e condizioni di stampa”.
Brion e Pattinson affermano che l’algoritmo che hanno sviluppato potrebbe essere l'”auto senza conducente” che gli ingegneri stavano cercando.
“Ciò significa che potresti avere un algoritmo in grado di esaminare tutte le diverse stampanti che stai utilizzando, monitorando costantemente e apportando modifiche secondo necessità, fondamentalmente facendo ciò che un essere umano non può fare”, ha affermato Pattinson.
I ricercatori hanno addestrato un modello di visione artificiale di apprendimento profondo mostrandolo circa 950.000 immagini catturate automaticamente durante la produzione di 192 oggetti stampati. Ciascuna delle immagini è stata etichettata con le impostazioni della stampante, come la velocità e la temperatura dell’ugello di stampa e la portata del materiale di stampa. Il modello ha anche ricevuto informazioni su quanto queste impostazioni fossero lontane da buoni valori, consentendo all’algoritmo di apprendere come si verificano gli errori.
“Una volta addestrato, l’algoritmo può capire semplicemente guardando un’immagine quale impostazione è corretta e quale è sbagliata, ad esempio un’impostazione particolare troppo alta o troppo bassa, e quindi applicare la correzione appropriata”, ha affermato Pattinson. “E la cosa interessante è che le stampanti che utilizzano questo approccio potrebbero raccogliere continuamente dati, quindi anche l’algoritmo potrebbe migliorare continuamente”.
Utilizzando questo approccio, Brion e Pattinson sono stati in grado di realizzare un algoritmo generalizzabile, in altre parole, può essere applicato per identificare e correggere errori in oggetti o materiali sconosciuti, o anche in nuovi sistemi di stampa.
“Quando stampi con un ugello, indipendentemente dal materiale che stai utilizzando – polimeri, cemento, ketchup o altro – puoi ottenere errori simili”, ha affermato Brion. “Ad esempio, se l’ugello si muove troppo velocemente, spesso si ottengono macchie di materiale o se si sta spingendo fuori troppo materiale, le linee stampate si sovrapporranno formando delle pieghe.
“Gli errori che derivano da impostazioni simili avranno caratteristiche simili, indipendentemente dalla parte stampata o dal materiale utilizzato. Poiché il nostro algoritmo ha appreso le caratteristiche generali condivise tra diversi materiali, potrebbe dire “Oh, le linee stampate stanno formando delle pieghe, quindi probabilmente stiamo spingendo fuori troppo materiale”.
Di conseguenza, l’algoritmo che è stato addestrato utilizzando un solo tipo di materiale e sistema di stampa è stato in grado di rilevare e correggere errori in diversi materiali, dai tecnopolimeri al ketchup e alla maionese, su un diverso tipo di sistema di stampa.
In futuro, l’algoritmo addestrato potrebbe essere più efficiente e affidabile di un operatore umano nell’individuare gli errori. Questo potrebbe essere importante per il controllo della qualità nelle applicazioni in cui il guasto dei componenti potrebbe avere gravi conseguenze.
Con il supporto di Cambridge Enterprise, il braccio commerciale dell’Università, Brion ha costituito Matta , una società spin-out che svilupperà la tecnologia per applicazioni commerciali.
“Stiamo rivolgendo la nostra attenzione a come questo potrebbe funzionare in settori di alto valore come quello aerospaziale, energetico e automobilistico, dove le tecnologie di stampa 3D vengono utilizzate per produrre parti costose e ad alte prestazioni”, ha affermato Brion. “Potrebbero volerci giorni o settimane per completare un singolo componente al costo di migliaia di sterline. Un errore che si verifica all’inizio potrebbe non essere rilevato fino al completamento e all’ispezione della parte. Il nostro approccio individuerebbe l’errore in tempo reale, migliorando notevolmente la produttività di produzione”.
La ricerca è stata supportata da Engineering and Physical Sciences Research Council, Royal Society, Academy of Medical Sciences e Isaac Newton Trust.
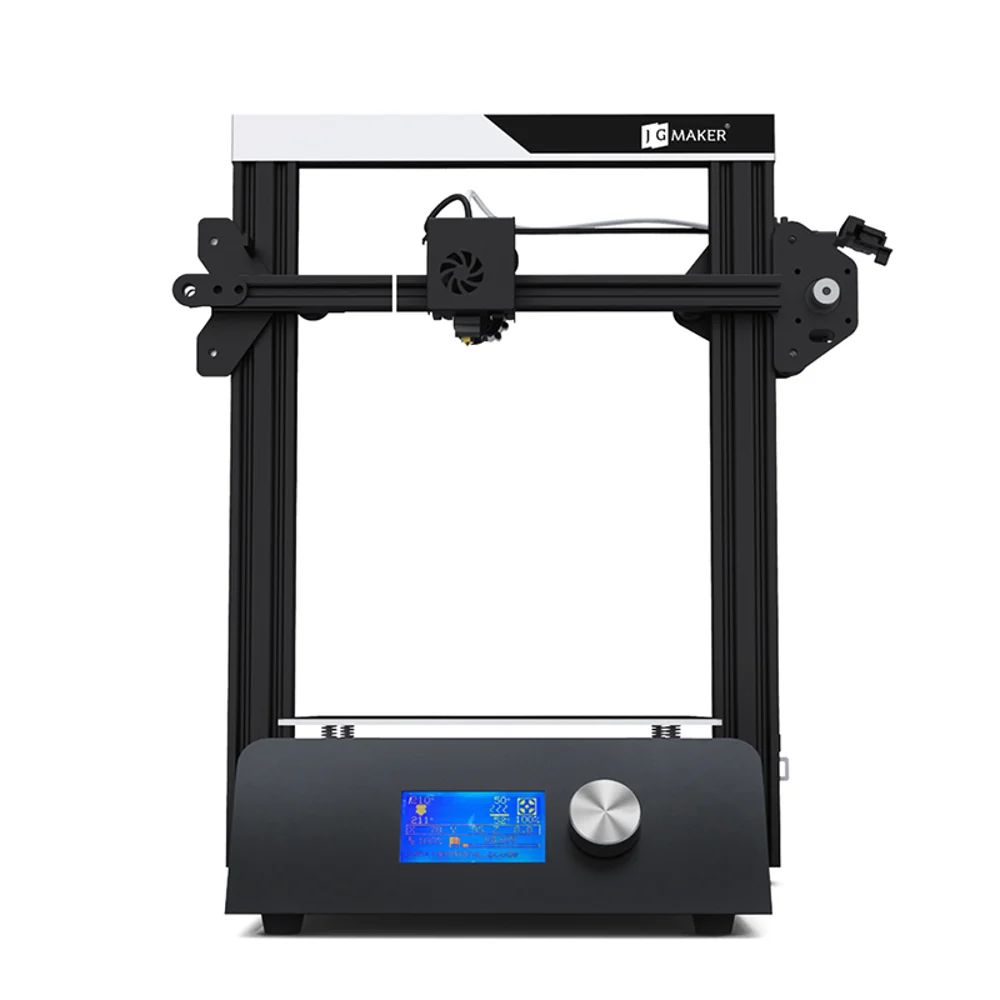