La Cattedra di Materiali Ceramici presso l’Università di Bayreuth, in collaborazione con il Plastics Center SKZ, il più grande istituto di materie plastiche d’Europa, sta studiando un modo economico e sostenibile di produrre ceramiche SiSiC. L’innovativo progetto di ricerca finanziato dal BMWK intitolato “Stampa 3D di WPC per la produzione di componenti SiSiC complessi di forma quasi netta” analizza la conversione di corpi verdi WPC prodotti in modo additivo in ceramiche di alta qualità. Lo presenteremo in modo più dettagliato.
Applicazioni in condizioni estreme, come temperature superiori a 800 °C con contemporanea abrasione e atmosfera corrosiva, sono possibili solo con la ceramica tecnica. La più importante ceramica non ossidica è il carburo di silicio (SiC), un materiale ad alte prestazioni che può essere prodotto come carburo di silicio infiltrato di silicio (SiSiC) utilizzando il processo di infiltrazione fusa. Convenzionalmente, per la sagomatura vengono utilizzati metodi di pressatura. A causa della polvere di SiC molto dura, tuttavia, questo processo di produzione del corpo verde porta a un’elevata usura dell’utensile ed è anche limitato in termini di design geometrico.
In un progetto di ricerca avviato di recente dell’Università di Bayreuth e della SKZ chiamato ” stampa 3D di WPC per la produzione di componenti SiSiC complessi di forma quasi netta “, è allo studio un nuovo percorso di processo per produrre ceramiche in modo più efficiente in termini di costi, più in modo sostenibile e con una maggiore libertà di geometria. Lo riferisce la SKZ in un comunicato stampa alla rivista 3D-borderless. La particolarità dell’approccio scelto risiede nel fatto che per la produzione di pasta verde viene utilizzato un materiale termoplastico processabile.
Componenti SiSiC rappresentativi, fabbricati in modo convenzionale basati su corpi verdi WPC dopo siliconizzazione liquida a oltre 1420 ° C (diametro dei componenti anteriori: 75 mm) (Immagine © Chair of Ceramic Materials presso l’Università di Bayreuth).
Ecco come funziona il processo
Jalena Best, ricercatrice associata presso la Cattedra di Materiali Ceramici presso l’Università di Bayreuth, spiega:
“In primo luogo, il corpo verde è costituito da granulato WPC (Wood Polymer Composite). Questo viene pirolizzato in azoto a temperature superiori a 1000 ° C, risultando in un corpo di carbonio puro. È importante per il prodotto finale che il corpo in carbonio sia il più dimensionalmente stabile e privo di bolle possibile. Infine, il corpo in carbonio viene infiltrato con silicio liquido. Durante questa fase del processo, il silicio reagisce con il carbonio per formare carburo di silicio, che forma una ceramica SiSiC”.
La fattibilità di questo percorso di processo è già stata ampiamente dimostrata in due precedenti progetti di ricerca. Nel progetto appena avviato, le possibili applicazioni sono da ampliare.
Il professor Schafföner, titolare della cattedra di materiali ceramici, afferma:
“Il progetto di ricerca contribuisce al raggiungimento degli obiettivi sociali risparmiando risorse ed energia grazie a questo innovativo percorso produttivo. Inoltre, la combinazione di produzione additiva, composto termoplastico a base di legno e l’obiettivo di produrre una ceramica SiSiC biogenica con un contorno ravvicinato è nuova ed economicamente interessante”.
Produzione quasi a forma di rete utilizzando la produzione additiva
Moritz Grünewald, scienziato del gruppo di sviluppo materiale presso SKZ, commenta quanto segue:
“L’obiettivo del nuovo progetto è ora quello di lavorare il materiale, che è altamente riempito di legno, utilizzando la produzione additiva. Per poter elaborare il composto materiale sulla stampante 3D, deve avere proprietà speciali”.
La produzione additiva consente una produzione quasi a forma di rete e quindi una minima post-elaborazione necessaria del materiale duro. Inoltre, attraverso la stampa 3D è possibile ottenere integrazioni funzionali completamente nuove, come componenti graduati, il che significa che è possibile implementare nuove applicazioni.
La modellatura additiva deve essere studiata utilizzando due metodi: Fused Deposition Modeling (FDM) e Fused Granular Fabrication (FGF). Entrambi i metodi sono caratterizzati da costi dei dispositivi relativamente bassi e consentono quindi alle aziende di adottare la tecnologia con bassi costi di acquisizione. Le aziende interessate sono invitate a partecipare al comitato relativo al progetto e a ricevere informazioni più dettagliate sul progetto.
Progetto di ricerca finanziato dal BMWK
Il progetto “Stampa 3D di WPC per la produzione di componenti SiSiC complessi a forma di rete vicina” 22307 N dell’associazione di supporto per la Süddeutsche Kunststoff-Zentrum eV FSKZ è finanziato dal gruppo di lavoro delle associazioni di ricerca industriale (AiF) nell’ambito del programma per la promozione della ricerca industriale congiunta (IGF) finanziato dal Ministero Federale dell’Economia e dell’Energia (BMWK).
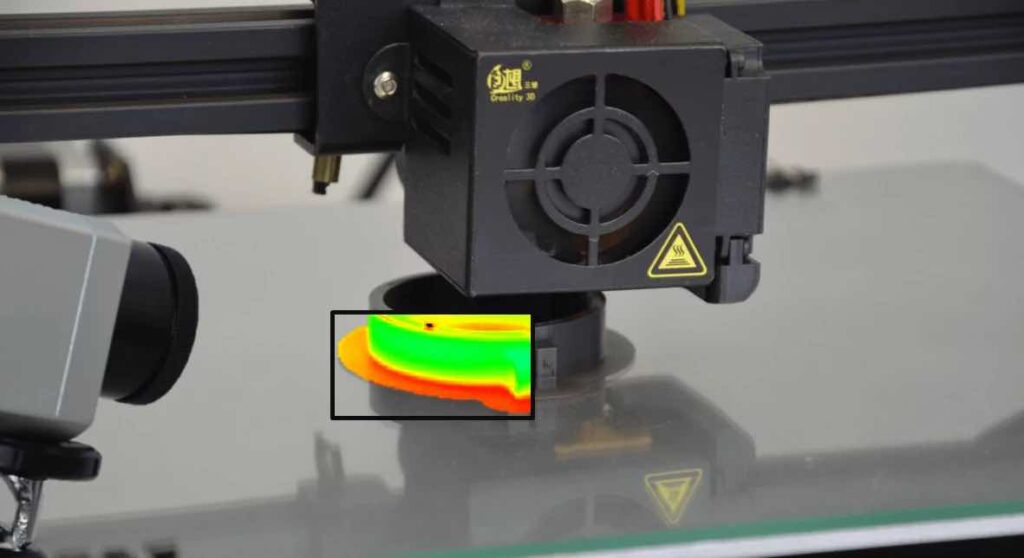