Come funziona la fabbrica Toyota con le stampanti 3D Zortrax
Gli stabilimenti Toyota in Polonia utilizzano una stampante 3D Zortrax M300 Plus per realizzare maschere di produzione su richiesta.
Secondo Toyota, l’investimento nella tecnologia di stampa 3D si è ripagato entro un anno.
Il vantaggio chiave della tecnologia di stampa 3D Zortrax, secondo gli ingegneri Toyota, è la sua agilità.
Gli stabilimenti di produzione Toyota in Polonia sono specializzati nell’assemblaggio di propulsori ibridi e convenzionali che finiscono nelle auto spedite in tutta Europa. Le fabbriche polacche impiegano oltre tremila persone e hanno una produzione significativa. Ecco come vengono utilizzate le stampanti 3D Zortrax per ottimizzare i costi e ridurre i tempi di consegna in una delle più grandi fabbriche automobilistiche in Europa.
Cosa fanno le stampanti 3D Zortrax in Toyota
“Cominciamo con quello che è il compito principale di cui siamo responsabili qui in Polonia. Toyota è un enorme produttore globale e operiamo come parte di un sistema di produzione più ampio con vari stabilimenti specializzati situati in tutto il mondo. Il nostro lavoro è assemblare motori per auto Toyota”, afferma Łukasz Kondek, un ingegnere di stampa 3D che lavora presso lo stabilimento Toyota. Questi motori sono realizzati con parti fornite da altri stabilimenti Toyota situati in tutta Europa.
Coperchio della leva della valvola stampato in 3D realizzato nello stabilimento Toyota con la stampante 3D Zortrax M300 Plus.
“Questo profilo di produzione si traduce direttamente in ciò per cui utilizziamo le stampanti 3D. La stragrande maggioranza dei modelli che stampiamo sono vari dime e fissaggi”, afferma Kondek, che poi prosegue spiegando come vengono classificate le dime nella sua struttura. Ci sono:
Maschere di posizionamento, utilizzate per confermare che le parti da assemblare siano nella posizione corretta l’una rispetto all’altra.
Maschere di assemblaggio, che vengono utilizzate per rendere l’assemblaggio di parti diverse più facile, veloce e ripetibile.
Strumenti di assemblaggio, che vengono utilizzati per eseguire determinati compiti durante l’assemblaggio come l’applicazione di lubrificanti a parti specifiche degli alberi lasciando altre aree non lubrificate.
Guarnizioni e coperchi, che vengono utilizzati per evitare che polvere e altri oggetti entrino nelle cavità delle parti del motore durante lo spostamento da una postazione di lavoro all’altra.
“Naturalmente, non tutto può essere stampato in 3D e spesso utilizziamo varie tecnologie di produzione per realizzare un singolo jig o strumento. Ad esempio, ci sono parti che hanno corpi stampati in 3D su macchine Zortrax, ma i punti di contatto con le superfici metalliche sono realizzati in modo tradizionale con materiali particolarmente resistenti all’usura. In questo modo possiamo mantenere la velocità e l’efficienza economica della stampa 3D e ottenere una durata superiore”, afferma Kondek. Di seguito sono riportati tre esempi scelti di maschere e strumenti stampati in 3D nello stabilimento di produzione Toyota.
Coperture delle leve delle valvole stampate in 3D
Quando il motore viene trasportato da una stazione di assemblaggio all’altra, le leve delle valvole del motore devono essere mantenute in una posizione. Quindi, gli ingegneri Toyota utilizzano coperture progettate su misura per mantenere ferme quelle leve. Inoltre, l’intero set, una volta installato, impedisce al motore di cadere dalla piattaforma su cui viene trasportato. All’arrivo alla stazione di assemblaggio corretta, le coperture vengono rimosse.
Prototipo della copertura della leva della valvola stampata in 3D nello stabilimento Toyota con la stampante 3D Zortrax M300 Plus con filamento Z-ABS.
“Questo è un ottimo esempio di ciò di cui è capace la stampa 3D”, afferma Kondek. Secondo lui, il suo team ha rapidamente ripetuto 12 diversi design di quelle coperture per ottimizzarle sia in termini di resistenza che di peso. Durante un solo turno, Kondek ha potuto eseguire tre diverse modifiche alla geometria e stampare in 3D due versioni consecutive di questa maschera sulla stampante 3D Zortrax M300 Plus .
“I coperchi delle leve delle valvole mostrano il vantaggio della tecnologia di stampa 3D quando si tratta di rapide modifiche alla geometria e di apportare modifiche al design al volo”, afferma Kondek.
Maschera di posizionamento stampata in 3D
Un’altra categoria di maschere stampate in 3D sulla Zortrax M300 Plus attualmente in uso presso lo stabilimento Toyota è quella delle maschere di posizionamento. “Esistono varie maschere di questo tipo che utilizziamo nella catena di montaggio per verificare che le parti siano assemblate correttamente”, afferma Kondek.
Maschera di posizionamento stampata in 3D presso lo stabilimento Toyota sulla stampante 3D Zortrax M300 Plus.
Il vantaggio principale dell’utilizzo di maschere di posizionamento stampate in 3D è la loro durata sorprendentemente lunga e un’opzione per incorporare altre tecnologie di produzione nel design. Nel progetto CAD mostrato di seguito, i componenti grigi erano realizzati in metallo, mentre i perni gialli dovevano essere lavorati a CNC in nylon. Il corpo della parte, di colore rosso, è stampato in 3D.
“La cosa interessante di questo particolare jig è che è stato consegnato ai team che lavorano sulla catena di montaggio come prototipo di parti di prova internate per subire ulteriori aggiustamenti”, afferma Kondek. Secondo lui in questa fase del processo di prototipazione le tolleranze erano leggermente diverse e la maschera mancava di cuscinetti scorrevoli adeguati. Nonostante ciò, era stato usato per sei mesi, tutti i giorni, prima che si rompesse.
Progettazione CAD di una maschera di posizionamento da stampare in 3D presso lo stabilimento Toyota con la stampante 3D Zortrax M300 Plus. I jig completamente assemblati hanno punti di contatto in nylon (contrassegnati sul disegno in giallo).
“E quando si rompe, potremmo utilizzare la stessa stampante 3D Zortrax M300 Plus per realizzarne un’altra in sole 7 ore. Effettuare sostituzioni a questo ritmo sarebbe stato impossibile senza stampanti 3D a bordo”, afferma Kondek.
Prototipazione di maschere di grandi dimensioni
La copertura del blocco motore è una maschera che mostra flussi di lavoro più avanzati in cui uno strumento di destinazione è più grande di uno spazio di lavoro disponibile in una stampante 3D e in cui vengono utilizzate stampanti 3D separate per la prototipazione e la fabbricazione del componente finale.
Parte della copertura del motore stampata in 3D nello stabilimento Toyota prima di rimuoverla dalla piattaforma di costruzione di una stampante 3D Zortrax M300 Plus.
“Lo scopo di questa maschera è sigillare le cavità tecnologiche nel blocco motore durante i processi di assemblaggio. Impedisce che strumenti, viti e altri oggetti cadano in queste cavità, il che è assolutamente fondamentale per il funzionamento del motore finale”, afferma Kondek.
Secondo lui, i prototipi di questo jig sono stati realizzati con la stampante 3D M300 Plus. Ciascuno dei prototipi è stato stampato in 3D in più parti che sono state poi assemblate. L’utilizzo di M300 Plus è stato il modo più conveniente per mettere a punto il progetto e costruire più prototipi per i controlli della geometria.
La copertura del motore è troppo grande per la stampa 3D in un unico pezzo anche su una stampante 3D M300 Plus abbastanza grande. Ecco perché Toyota lo realizza in più parti che vengono assemblate una volta terminata la stampa.
Infine, il componente per l’uso finale è stato stampato in 3D su una macchina industriale con un materiale ad alte prestazioni che non poteva essere supportato su M300 Plus a causa della sua architettura aperta. “Per tali applicazioni abbiamo bisogno di stampanti 3D più grandi, Zortrax Endureal è un buon esempio, con un’architettura chiusa che garantisce una temperatura stabile nella camera di stampa per evitare deformazioni e restringimenti che possono influire gravemente sulle stampe di grandi dimensioni”, afferma Kondek.
Risparmio di tempo e costi
“Usiamo stampanti 3D ormai da anni. Erano già qui quando sono arrivato a lavorare alla Toyota quattro anni fa”, afferma Kondek. Secondo lui, le maschere stampate in 3D oggi venivano realizzate da una divisione di utensili separata dotata di macchine CNC e altri strumenti di produzione sottrattiva. La fabbricazione di progetti più impegnativi è stata semplicemente affidata a subappaltatori esterni.
Una parte di una maschera per l’applicazione di grasso su parti automobilistiche realizzata da Toyota sulla stampante 3D Zortrax M300 Plus.
“Ovviamente, l’utilizzo di tali strumenti ha fortemente limitato ciò che potevamo fare dal punto di vista del design. Ogni volta che pensavamo a un nuovo jig, dovevamo pensarci due volte se potesse essere fabbricato o meno. Le stampanti 3D risolvono questo problema”, spiega Kondek. Aggiunge che attualmente oltre il 95% delle maschere stampate in 3D prodotte nello stabilimento Toyota sono prodotte con la tecnologia LPD. Il resto è stampato in 3D con altre tecnologie di stampa 3D.
Finora, secondo Kondek, l’investimento in attrezzature per la stampa 3D si è completamente ripagato entro un anno. “La stampa 3D non riguarda tanto la velocità di fabbricazione, in quanto questa non è la tecnologia più veloce in circolazione. Ma è certamente il più agile. Non abbiamo bisogno di immagazzinare pezzi di ricambio in quanto possono essere stampati in 3D su richiesta. Possiamo ottimizzare i progetti come vogliamo, perché le stampanti 3D possono fabbricare quasi tutte le possibili geometrie. Finalmente possiamo iniziare subito a stampare. Non abbiamo bisogno di aspettare che una divisione attrezzaggio, o un subappaltatore esterno, abbia risorse disponibili per lavorare sui nostri incarichi. I nostri tempi di consegna sono scesi da settimane a giorni e in alcuni casi a ore”, afferma Kondek.
Sistemi di stampa 3D per fabbriche automobilistiche
La stampante 3D M300 Plus attualmente utilizzata da Toyota fornisce funzionalità di stampa 3D di base per applicazioni di produzione. In combinazione con altre soluzioni di stampa 3D Zortrax, tuttavia, può funzionare come elemento costitutivo di base in sistemi di produzione additiva più avanzati. Ecco un paio di esempi fattibili.
Stampanti 3D Zortrax Endureal al centro e sulla destra e stampanti 3D Zortrax M300 Plus sullo sfondo.
Un esempio di configurazione di stampa 3D con la stampante 3D Zortrax Endureal Zortrax Inkspire 2 3D, le stampanti 3D Zortrax M300 Plus e M200 Plus e i dispositivi di post-elaborazione Zortrax Curing Station e Zortrax Cleaning Station.
Stampanti 3D Zortrax Endureal al centro e sulla destra e stampanti 3D Zortrax M300 Plus sullo sfondo.
Un esempio di configurazione di stampa 3D con la stampante 3D Zortrax Endureal Zortrax Inkspire 2 3D, le stampanti 3D Zortrax M300 Plus e M200 Plus e i dispositivi di post-elaborazione Zortrax Curing Station e Zortrax Cleaning Station.
Stampanti 3D Zortrax Endureal al centro e sulla destra e stampanti 3D Zortrax M300 Plus sullo sfondo.
L’aggiunta del dispositivo di levigatura del vapore intelligente Zortrax Apoller all’officina di stampa 3D della fabbrica consente di levigare costantemente grandi quantità di maschere stampate in 3D. La levigatura dei vapori con MEK o vapori di acetone rende sicuramente i modelli stampati in 3D più belli ma li rende anche meno permeabili. Diventano semplicemente impermeabili. Questa permeabilità fortemente limitata è fondamentale nella realizzazione di maschere progettate per essere riempite con oli o altri grassi. L’Apoller è stato progettato per una grande produttività e in una sessione di levigatura della durata di circa 3 ore può levigare più maschere diverse. È inoltre certificato ATEX e può essere implementato in sicurezza in fabbrica.
I filamenti polimerici standard come l’ABS a volte possono rivelarsi troppo deboli per le parti destinate a lavorare sotto carichi pesanti, sopportare un’usura significativa o sopportare temperature molto elevate. Questo problema può essere risolto con Zortrax Endureal, una stampante 3D industriale progettata per funzionare con polimeri ad alte prestazioni come Z-PEEK o VICTREX AM™ 200 che mantengono le loro proprietà a temperature superiori a 300 gradi Celsius e raggiungono valori di resistenza alla trazione superiori a 90 MPa .
Infine, quando i requisiti termici e meccanici dei progetti vanno ben oltre ciò che è possibile anche con i polimeri più resistenti sulla Terra, l’Endureal può fare un’altra cosa. Può realizzare parti in acciaio. Nello specifico, Endureal funziona con filamenti di polvere metallica BASF Ultrafuse® 316L e BASF Ultrafuse® 17-4 PH che, dopo una post-elaborazione in due fasi sviluppata da BASF ed eseguita da Elnik Systems GmbH, diventano acciaio inossidabile 316L completamente funzionante o indurito per precipitazione 17-4 acciaio. Questi materiali sono disponibili in Zortrax Full Metal Package 316L e Zortrax Full Metal Package 17-4 PH, kit contenenti tutto il necessario per realizzare parti in acciaio sulla stampante Endureal 3D.
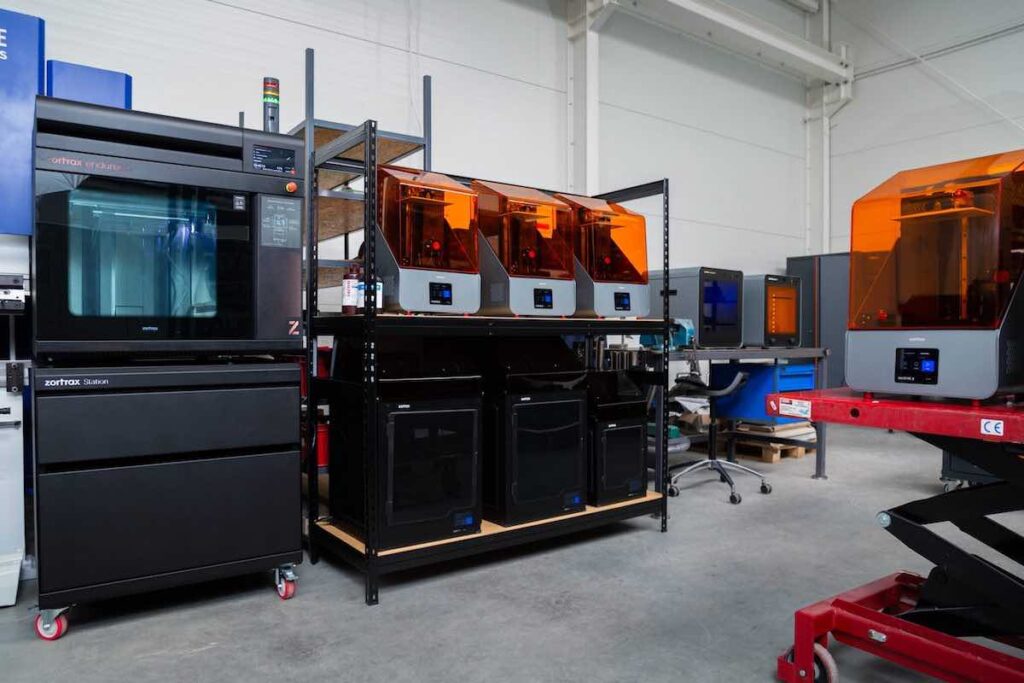