Innovazione nella Stampa a Trasferimento a Secco
Gli studiosi dell’Institute for Basic Science (IBS) in Corea del Sud hanno ideato una nuova tecnica di stampa a trasferimento a secco destinata ai dispositivi elettronici flessibili. Questo metodo, sviluppato dal Prof. KIM Dae-Hyeong, dal Dr. LEE Sangkyu (Centro IBS per la ricerca sulle nanoparticelle) e dal Prof. KIM Jihoon (Università di Pusan), permette il trasferimento di materiali elettronici di alta qualità senza danneggiarli, segnando un progresso significativo nel settore.
Sfide nei Materiali Elettronici
Tradizionalmente, i materiali elettronici di alta qualità richiedono sintesi e lavorazione a temperature elevate per ottenere le strutture cristalline e le proprietà elettriche desiderate. Tuttavia, queste alte temperature complicano la lavorazione diretta su substrati flessibili o estensibili. Pertanto, per costruire dispositivi flessibili o estensibili, l’elettronica deve essere trasferita dal substrato rigido a quello morbido. Le tecnologie di stampa transfer esistenti presentano problemi come l’uso di sostanze chimiche nocive e potenziali danni meccanici durante il processo di trasferimento.
Limiti delle Tecnologie Esistenti
Diversi metodi sono stati sviluppati per affrontare queste problematiche, tra cui processi laser o termici e delaminazione in acqua. Tuttavia, questi approcci richiedono attrezzature costose, necessitano di ulteriori passaggi di post-elaborazione o sono limitati a specifici ambienti operativi. Inoltre, risulta complesso utilizzare la stampa transfer convenzionale per materiali elettronici di alta qualità che richiedono trattamenti termici per formare strutture cristalline.
Soluzione Innovativa
Il team di ricerca ha sviluppato un metodo di stampa a trasferimento a secco senza danni, controllando lo stress all’interno dei film sottili. Questo nuovo approccio permette di trasferire film sottili di metalli e ossidi, lavorati ad alte temperature, su substrati flessibili senza danneggiarli. Regolando i parametri di sputtering, il gruppo ha controllato il tipo e l’entità dello stress all’interno del film sottile. Hanno creato strutture a doppio strato con sollecitazioni variabili per massimizzare il gradiente di sollecitazione e applicato ulteriore trazione tramite deformazione esterna, massimizzando la velocità di rilascio dell’energia di deformazione e consentendo una delaminazione affidabile superando la resistenza interfacciale tra la pellicola sottile e il substrato.
Vantaggi della Nuova Tecnica
“Il nostro metodo di trasferimento evita l’uso di sostanze tossiche, riduce al minimo i danni al dispositivo ed elimina la necessità di post-elaborazione, accorciando i tempi di trasferimento”, ha dichiarato il dott. SHIN Yoonsu, primo coautore. “Può trasferire ampie aree e modelli su scala microscopica, rendendolo estremamente versatile”.
Applicazioni e Prospettive Future
Il team ha dimostrato che maggiori gradienti di stress all’interno dei film sottili generano momenti flettenti maggiori, facendoli arricciare e trasformarsi da un film sottile bidimensionale (2D) in una struttura tridimensionale (3D). La configurazione delle strutture 3D può essere regolata tramite il modello dello strato adesivo durante la stampa a trasferimento, consentendo la progettazione e la fabbricazione delle strutture desiderate per soddisfare vari requisiti.
Il dottor LEE Sangkyu, uno degli autori corrispondenti, ha sottolineato: “La chiave di questa ricerca è lo sviluppo di una tecnica di stampa a trasferimento a secco senza danni, controllando unicamente le proprietà del materiale, a differenza degli studi precedenti”. Ha aggiunto: “Abbiamo in programma ulteriori ricerche sulla fabbricazione di diversi dispositivi 3D, sfruttando la tecnologia per trasformare film sottili 2D in strutture 3D, oltre i semplici dispositivi a batteria flessibile 2D dimostrati nell’articolo”.
“La tecnologia di stampa a trasferimento ha applicazioni in campi quali l’elettronica flessibile, l’optoelettronica, la bioelettronica e i dispositivi energetici. Il nostro metodo offre vantaggi significativi per la produzione di strutture funzionali a film sottile 2D e 3D ad alta densità senza danni, avvantaggiando notevolmente lo sviluppo di nuovi dispositivi elettronici ad alte prestazioni”, ha osservato il Prof. KIM Dae-Hyeong.
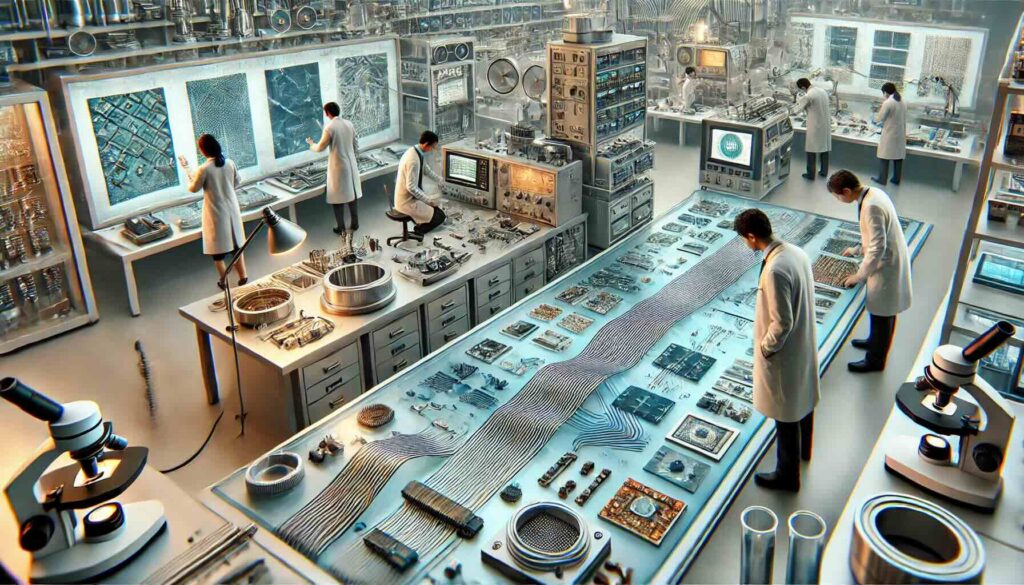