Progetto di Ridisegno del Dispositivo Anti-Assorbimento Olio
Gli studenti di ingegneria della Louisiana State University (LSU) hanno collaborato con ExxonMobil per riprogettare un componente critico impiegato in macchine rotanti: il “Machinery Anti-Wicking Device”. L’obiettivo era impedire che l’olio lubrificante risalisse lungo i fili dei termocoppie, compromettendo la strumentazione. La soluzione tradizionale prevedeva lavorazioni meccaniche a partire da un pezzo in alluminio pieno; il nuovo approccio sfrutta la stampa 3D a letto di polvere di metallo (Laser Powder Bed Fusion – L-PBF) per ottenere geometrie più performanti in un’unica fase di stampa.
Tecnologia e Materiali Impiegati
Per la produzione del componente, è stata adottata la tecnologia L-PBF su impianto Nikon SLM®280, capace di operare con più sorgenti laser simultanee e di raggiungere elevate velocità di costruzione volumetrica. Il materiale scelto è una lega metallica ad alte prestazioni, specificamente ottimizzata per garantire resistenza alla corrosione e stabilità dimensionale a elevate temperature. La polvere metallica viene sinterizzata strato dopo strato: i laser fondono con precisione zone selezionate, permettendo di integrare sistemi di tenuta modulare e nervature interne di rinforzo, impossibili da realizzare con la lavorazione tradizionale.
Ruolo dei Partner Coinvolti
ExxonMobil, attraverso il suo stabilimento di Baton Rouge, ha finanziato il progetto nell’ambito di attività didattiche volte a innovare i processi di manutenzione industriale. Nikon SLM Solutions ha fornito la macchina 3D e l’expertise per il design-for-additive-manufacturing, curando la validazione delle impostazioni di stampa. Howco Additive, specialista nella fornitura di servizi di stampa metallica, ha affiancato gli studenti nella ottimizzazione dei parametri di build e nel post-processing termico, assicurando la qualità metallurgica del pezzo.
Attività del Gruppo Capstone
La squadra, denominata Capstone Team 54, era composta dagli studenti Brennon Broussard, Jude Rogers, Matthew Shannon, Garrett Valley e Robin Torres. Il team ha condotto analisi strutturali mediante simulazioni agli elementi finiti, verificando il comportamento del componente in condizioni di esercizio. Cody Durand e Brenna Dowrey di Nikon SLM Solutions hanno supportato la progettazione delle connessioni interne, mentre David Ramirez di Howco Additive si è occupato della calibrazione finale e delle prove di durezza e tenuta.
Vantaggi del Nuovo Design
-
Tempi di Produzione Ridotti: la stampa 3D ha consentito di passare da tempi di attesa di mesi, necessari per le lavorazioni meccaniche, a tempi di poche giornate.
-
Modularità: il componente è stato suddiviso in sezioni intercambiabili, facilitando operazioni di manutenzione e sostituzione mirata.
-
Migliore Tenuta: i nuovi elementi di giunzione e le guarnizioni integrate sono stati riprogettati per garantire un coefficiente di permeazione dell’olio inferiore rispetto alla versione precedente.
-
Resistenza Meccanica: i test di fatica e di pressione hanno confermato un aumento significativo della durata operativa.
Impatto sul Settore Energetico
Questa iniziativa si inserisce nel più ampio contesto delle strategie di ExxonMobil per migliorare l’affidabilità degli impianti e ridurre i costi di manutenzione. L’adozione di tecnologie additive si estende oggi a componenti di turbomacchine, sistemi di iniezione e accessori per l’estrazione di idrocarburi, con potenziali ricadute positive in termini di sostenibilità operativa.
Profilo delle Aziende
-
ExxonMobil: tra le principali compagnie energetiche mondiali, attiva in esplorazione, produzione e raffinazione. L’impianto di Baton Rouge è uno dei più grandi complessi petrolchimici degli Stati Uniti.
-
Nikon SLM Solutions: sede centrale in Germania, sviluppa sistemi di stampa 3D metallica con configurazioni fino a 12 laser, pensati per settori quali aerospaziale, automotive e medicale.
-
Howco Additive: divisione di Howco Resources, fornisce servizi di stampa metallica e consulenza per la progettazione orientata alla manifattura additiva; gestisce centri di produzione certificati per componenti di altissima affidabilità.
Riconoscimenti Accademici
Il progetto è stato insignito del Ben Burns Jr. Memorial Award per il miglior progetto Capstone e del premio per la migliore relazione finale nel College of Engineering della LSU, a conferma del valore tecnico e formativo dell’esperienza.
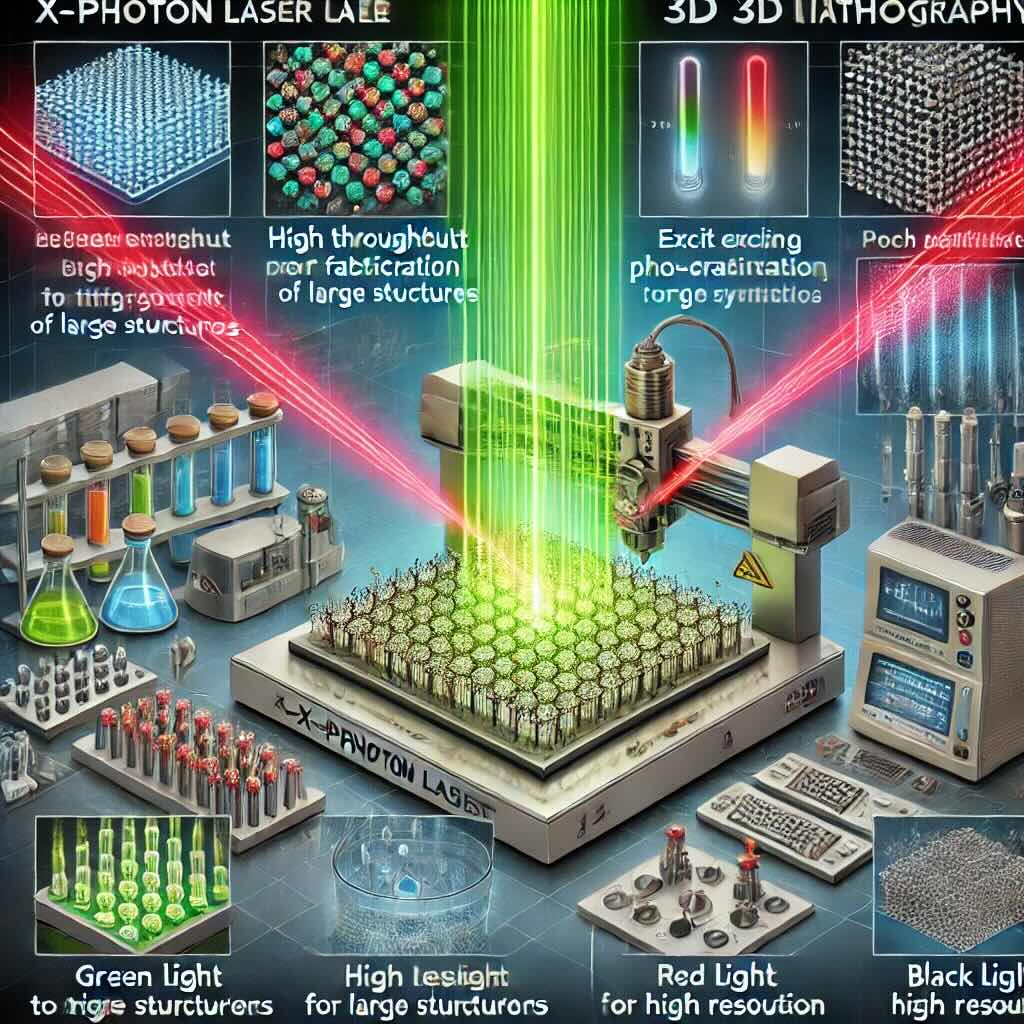