COMUNICATO STAMPA
La stampa 3D potenzia e accelera la ricerca e lo sviluppo di nuovi dispositivi medici:
grazie alle stampanti Formlabs, Coalesce Product Development crea inalatori innovativi e a basso costo
Secondo l’Organizzazione Mondiale della Sanità, circa 262 milioni di persone nel mondo soffrono di asma, che nel 2019 ha causato quasi mezzo milione di morti. Per chi soffre di problemi respiratori come l’asma o la broncopneumopatia cronica ostruttiva (BPCO), è necessario un dispositivo di inalazione per facilitare la respirazione. I farmaci per via inalatoria possono controllare i sintomi dell’asma e consentire alle persone affette da questo disturbo di condurre una vita normale e attiva. Sfortunatamente, l’accesso e l’accessibilità economica rappresentano per molti ancora una barriera in diverse parti del mondo. Gli studi pubblicati negli Annals of American Thoracic Society e nel Journal of Allergy and Clinical Immunology hanno stimato i costi annuali per persona per il trattamento dell’asma tra 1.800 e 4.900 dollari per le sole prescrizioni di farmaci e inalatori, inclusi i costi diretti (ad es. medicine e visite dal medico) – e costi indiretti (es. assenze dal lavoro).
L’azienda britannica di dispositivi medici Coalesce Product Development cerca di affrontare alcuni di questi problemi. La società sviluppa nuovi dispositivi innovativi per la somministrazione di farmaci, inclusi inalatori e iniettori, da utilizzare con prodotti per inalazione generici che offrono un valore aggiunto rispetto alle alternative di marca che possono costare oltre 380 dollari al mese.
Gli inalatori devono essere utilizzabili da un’ampia fetta della società, dagli adolescenti ai pazienti anziani con comorbilità. Pertanto, le dimensioni, la forma e l’interfaccia utente precise di ogni nuovo inalatore devono essere progettate e testate con molta attenzione. Per raggiungere questo obiettivo, il team di Coalesce ha deciso di adottare stampanti 3D interne per prototipare, testare e creare vari dispositivi in una moltitudine di forme e dimensioni diverse. Per testare ogni prodotto in fase di sviluppo, l’azienda sviluppa anche i propri banchi di prova, maschere e dispositivi stampati sempre in 3D.
Investire nell’ecosistema Formlabs per la produzione di dispositivi medici
Coalesce ha investito per la prima volta nella stampante 3D stereolitografica Form 2 quando è stata rilasciata nel 2015. A quel tempo, il team faceva ancora molto affidamento sull’outsourcing per i prototipi, aspettando giorni affinché le loro parti venissero consegnate. Con l’adozione della Form 2 i tempi sono cambiati.
Coalesce ha utilizzato la Form 2 per sviluppare e prototipare l’architettura cruciale per diversi dispositivi inalatori e autoiniettori. Ad esempio, per i casework del suo dispositivo elettronico di profilatura del respiro (BPD), i progettisti hanno scelto la resina bianca per la sua finitura liscia e le proprietà meccaniche, che hanno permesso loro di forare e aggiungere inserti in ottone.
“La stereolitografia offre un buon equilibrio tra risoluzione delle caratteristiche, finitura superficiale, durata, scelta dei materiali e precisione dimensionale. Poiché sviluppiamo dispositivi con parti mobili, avevamo bisogno di un modo efficace per prototipare piccoli meccanismi internamente. Abbiamo tenuto d’occhio i progressi della tecnologia di stampa 3D negli ultimi anni e ci è piaciuto l’approccio di Formlabs. Quando è stata rilasciata la Form 2, ne abbiamo ordinata una immediatamente, seguita da una seconda solo poche settimane dopo”, ha dichiarato Vinnay Chhabildas, Industrial Designer at Coalesce.
Inizialmente, i prototipi stampati in 3D sono stati utilizzati per sviluppare l’architettura esterna del BPD. Quando è stata la perfezione nel design, le parti stampate sono state dipinte e portate alla conferenza Drug Delivery to the Lungs (DDL), una riunione annuale di specialisti della somministrazione di farmaci polmonari e nasali. I prototipi BPD sembravano così realistici che venivano spesso confusi con un prodotto finale.
Alla fine, gli stessi prototipi di dispositivi sono stati utilizzati in uno studio clinico sulla funzione polmonare. I risultati hanno mostrato quanta variazione può verificarsi tra diversi profili di inalazione.
L’utilizzo di fornitori di terze parti sarebbe costato circa 20 volte di più rispetto al costo grezzo della stampa delle parti realizzata internamente. I casework del BPD costano 11 sterline per la produzione con la Form 2 rispetto a circa 250 sterline se esternalizzate. Secondo Vinnay, tuttavia, il vero vantaggio è il tempo risparmiato: le parti impiegavano solo otto ore per essere stampate e potevano essere rifinite e verniciate in pochi giorni. Lo stesso processo richiederebbe a un appaltatore esterno una o due settimane.
Stampa 3D interna con la Form 3
Dopo aver internalizzato la stampa 3D con la Form 2 e aver utilizzato moltissimo le macchine, il team ha aggiornato la propria flotta acquistando tre stampanti Form 3.
Con la Form 3, Coalesce era pronta a passare da prototipi puramente estetici, all’integrazione della stampa 3D nello sviluppo dei propri dispositivi, inclusa la creazione di minuscole funzionalità interne. Grazie all’accuratezza della stampa 3D con la tecnologia diLow Force Stereolithography™ (LFS) fornita dalla Form 3, il team è stato in grado di risolvere i principali problemi che affliggono lo sviluppo degli inalatori, in particolare analizzando la distribuzione delle particelle fini delle formulazioni in polvere secca fornite utilizzando test analitici per garantire una consegna regolare e accurata di vari farmaci.
“La Form 3 ci ha permesso di stampare tratti fini e maglie delicate e di ottimizzare il dispositivo durante la fase di progettazione. In questo modo abbiamo la possibilità di modellare una parte, cambiarla al volo e avere la parte fisica in poche ore. Possiamo eliminare il fornitore ottenendo le parti più rapidamente. Le Form 3 sono assolutamente essenziali per noi”, ha dichiarato Vinnay.
Oggi, il team gestisce tre Form 3 che funzionano ininterrottamente, cinque giorni alla settimana, il che le rende una parte indispensabile del processo di sviluppo. I casi d’uso per la stampa 3D hanno continuato ad espandersi, con il team che ora stampa strumenti per testare i propri dispositivi. Un esempio è la stampa di diversi boccagli in BioMed Clear Resin, un materiale biocompatibile e sicuro per la pelle e per le prove sui pazienti. La stampa 3D consente al team di saltare la creazione di costose parti in plastica stampate a iniezione.
Vinnay ha affermato che il motivo per cui il suo team è rimasto fedele a Formlabs è perché “non esiste un’alternativa migliore alle stampanti Formlabs sul mercato. Esistono altre piattaforme, ma niente che possa fornire la qualità di stampa, l’affidabilità della macchina e la facilità d’uso a cui ci siamo abituati con Formlabs. Siamo così ben adattati all’uso di PreForm e Dashboard, che qualsiasi altra cosa non sembra all’altezza. Da quando abbiamo iniziato con la Form 2 e siamo passati alla Form 3, non abbiamo più cambiato”.
Una vasta offerta di materiali di stampa 3D SLA
Uno dei principali vantaggi della stampa 3D SLA è l’ampia offerta di materiali. Ciò consente a una singola Form 3 di svolgere più ruoli all’interno di un’organizzazione, stampando diversi tipi di parti a seconda dell’applicazione.
Per accelerare il processo di creazione delle maschere di prova, il team si è rivolto alla Draft Resin per creare parti più rapidamente. Ad esempio, i dispositivi vengono stampati in circa un’ora con Draft Resin. Il risparmio di tempo è vitale, con Vinnay che dichiara “abbiamo anche una macchina CNC interna. Avere la possibilità di testare come apparirà la parte CNC in una stampa 3D, senza dover impostare la macchina CNC, è inestimabile.”
Coalesce utilizza diversi materiali Formlabs a seconda dello scopo:
La Draft Resin viene utilizzata per testare i dispositivi prima che vengano lavorati.
La High Resin Temperature viene utilizzata per creare strumenti che funzionano in combinazione con uno strumento di termosaldatura.
La Rigid Resin viene utilizzata per gli utensili. Il team ritiene che la Rigid Resin sia perfetta per elementi piccoli e complessi che devono mantenere la loro precisione dimensionale, come piccole forme a rete che devono rimanere ferme quando soggette a forze del flusso d’aria.
La Grey Pro Resin viene utilizzata in modo simile alla Rigid Resin, essendo utilizzata principalmente per dispositivi e attrezzature.
Le Standard Resins (resina bianca e resina nera) sono entrambe utilizzate per i modelli estetici.
La resina trasparente BioMed viene utilizzata per la stampa di boccagli che vengono inviati per essere testati con pazienti reali.
Elastic 50A Resin viene utilizzata principalmente nel laboratorio chimico di Coalesce per creare adattatori personalizzati che si adattano a una macchina per la simulazione polmonare. L’adattatore deve sigillare in modo affidabile il boccaglio testato, è necessaria, quindi, una parte simile al silicone. La resina Elastic 50A può piegarsi, allungarsi, comprimersi e resistere a cicli ripetuti senza strapparsi, rendendola perfetta per gli adattatori.
La Clear Resin è usata per simulare l’effetto di un vaso per il suo aspetto traslucido. Il team assembla versioni dei propri dispositivi in Clear Resin, lucida la resina e quindi osserva come tutti i vari componenti si uniscono all’interno dell’inalatore. Ciò consente loro di misurare i dettagli interni che non sarebbero visibili durante la stampa in Black Resin o Grey Pro Resin.
La stampa 3D per i dispositivi medici
L’implementazione della stampa 3D interna può generare un valore immenso e vantaggi in termini di tempo per le aziende di sviluppo di dispositivi medici. Non solo può essere utilizzata per creare prototipi, ma può anche aiutare a ridurre l’outsourcing, aumentare la velocità di iterazione del progetto, creare strumenti vitali eliminando la necessità di stampaggio a iniezione e altro ancora.
Utilizzando le stampanti 3D di Formlabs, Coalesce Product Development ha ridotto i tempi di consegna per il casework di un dispositivo medico dell’80-90% e ha ottenuto una riduzione dei costi del 96%. Nel tempo hanno continuato a investire ed espandere le applicazioni di stampa 3D, ponendosi all’avanguardia nello sviluppo di prodotti per inalazione. I risparmi sui costi e la velocità di sviluppo hanno consentito all’azienda di sviluppare dispositivi per i propri clienti e anche di sviluppare la propria tecnologia di dispositivi per la concessione in licenza a società farmaceutiche globali con investimenti finanziari relativamente modesti.
Alla fine, Vinnay ha riassunto la sua esperienza con le stampanti Formlabs in una frase: “Per Coalesce, le stampanti 3D Formlabs sono fondamentali”.

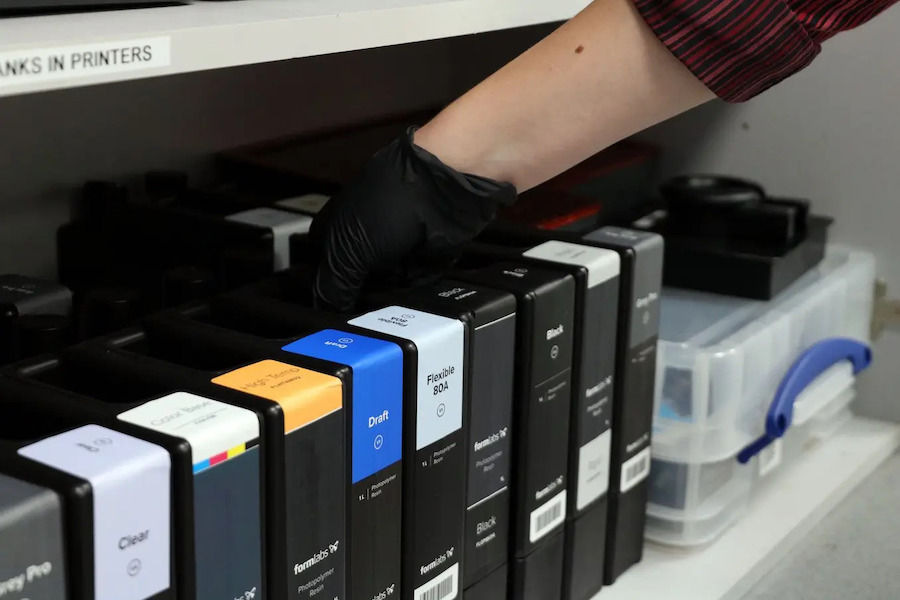
