Rendere visibile l’invisibile: Come i raggi X rivelano il comportamento dello spatter durante la stampa 3D
Attraverso l’uso di tecniche avanzate di imaging a raggi X ad alta velocità, i ricercatori dell’University College London (UCL) sono riusciti a catturare e quantificare la dinamica dello spatter durante la fusione laser a letto di polvere (LPBF) in varie condizioni di lavorazione. Questo studio ha portato alla scoperta di due nuovi meccanismi di formazione dello spatter.
Scoperta dei collegamenti tra la depressione del vapore e lo spatter
La ricerca, pubblicata nell’International Journal of Extreme Manufacturing, rivela e spiega i legami tra la forma della depressione del vapore e la dinamica dello spatter durante la LPBF, operando sotto condizioni di lavorazione rilevanti per l’industria. Non solo questo lavoro quantifica lo spatter e le interazioni tra spatter e laser, ma propone anche strategie per minimizzare i difetti, migliorando così la qualità superficiale dei componenti prodotti tramite LPBF.
Lo spatter durante la LPBF può generare difetti superficiali che influiscono negativamente sulle prestazioni di fatica dei componenti fabbricati. Chu Lun Alex Leung, autore corrispondente dell’articolo e Professore Associato presso il Dipartimento di Ingegneria Meccanica della UCL, ha dichiarato: “Lo spatter è uno dei principali problemi nell’applicazione industriale della stampa 3D, poiché può contribuire alla formazione di porosità e superfici irregolari.”
Sfide e soluzioni per la LPBF
Il Professor Peter D. Lee, anche lui autore corrispondente e Professore di Ingegneria Meccanica alla UCL, ha sottolineato: “L’adozione della LPBF per applicazioni critiche per la sicurezza è ostacolata dalla difficoltà di ottenere componenti metallici di alta qualità superficiale e privi di difetti.” Attualmente, la ricerca sullo spatter durante la LPBF è limitata, e il nostro obiettivo è migliorare la comprensione dei meccanismi di formazione dello spatter utilizzando fonti di raggi X di alta energia provenienti da sincrotrone.”
La LPBF è una delle principali tecnologie di stampa 3D per metalli, con il potenziale di produrre componenti che superano le fusioni tradizionali in termini di livelli di difetti e proprietà meccaniche, quando vengono utilizzati parametri di processo adeguati. Tuttavia, al momento, questi componenti potrebbero non raggiungere la qualità superficiale e i livelli di difetti dei componenti lavorati da prodotti laminati. Ridurre i difetti (o la rugosità) nelle regioni superficiali dovrebbe portare a ulteriori miglioramenti nelle prestazioni di fatica dei componenti prodotti con LPBF.
I difetti superficiali sono spesso associati alla formazione di spatter durante la LPBF. Spatter di grandi dimensioni possono aderire alla superficie delle parti prodotte tramite manifattura additiva, aumentando sia i difetti superficiali che la rugosità; possono anche rimanere intrappolati nel letto di polvere negli strati successivi, portando a porosità dovute a mancanza di fusione. Inoltre, lo spatter può ossidarsi, riducendo la riciclabilità e la riutilizzabilità della polvere. Gli ossidi superficiali possono inibire la fusione delle particelle e promuovere la formazione di porosità, diminuendo la densità dei componenti prodotti con LPBF. Una comprensione più approfondita dell’evoluzione dello spatter è quindi essenziale per mitigare questi problemi.
Esperimenti e risultati
Gli esperimenti sono stati condotti utilizzando una macchina AM personalizzata, chiamata Quad-laser in situ and operando process replicator (Quad-ISOPR). Il Quad-ISOPR comprende quattro laser e un sistema di scansione industriale combinato con una camera ambientale su misura riempita con gas di protezione argon. Un substrato con uno spessore di 1 mm e un’altezza di 15 mm è montato nella camera, su cui viene automaticamente depositato un sottile strato di polvere.
Grazie all’imaging a raggi X ad alta velocità in situ, sia lo spatter che le dinamiche della piscina di fusione durante la LPBF possono essere catturati con una risoluzione spaziale e temporale eccezionale. Gli esperimenti in situ sono stati eseguiti presso la linea di imaging ad alta velocità dell’European Synchrotron Radiation Facility (ESRF), utilizzando un fascio di raggi X duri policromatici con un’energia media di circa 30 keV e una telecamera ad alta velocità con un frame rate di 40 kHz.
Da Guo, primo autore e post-doc presso la scuola, ha dichiarato: “Il nostro lavoro prevede il numero di spatter che si formano durante la LPBF di un sistema in lega Al-Zr-Fe. Questa previsione può essere utilizzata per la validazione futura del modello e per minimizzare lo spatter.”
I ricercatori continueranno a indagare la formazione dello spatter su diversi materiali commerciali per applicazioni di stampa 3D, con l’obiettivo di ottenere componenti LPBF di alta qualità superficiale per l’uso reale. Grazie a questi progressi, sperano di contribuire in modo significativo alla più ampia adozione della LPBF nell’industria, in particolare nelle applicazioni in cui l’integrità dei componenti è fondamentale.
Informazioni su IJEM
L’International Journal of Extreme Manufacturing (IF: 16.1, consecutivamente al primo posto nella categoria Ingegneria, Produzione) è una nuova rivista multidisciplinare, open-access e a doppio anonimato, che copre in modo unico l’intero spettro della produzione estrema. La rivista è dedicata alla pubblicazione di articoli originali e recensioni di alta qualità e impatto nelle aree legate alla scienza e alla tecnologia della produzione di dispositivi e sistemi funzionali con dimensioni estreme (molto grandi o molto piccole) e/o funzionalità estreme, spaziando dalla scienza fondamentale alle tecnologie all’avanguardia che supportano la produzione di prodotti ad alte prestazioni, coinvolgendo tecniche emergenti e superando i limiti delle teorie, dei metodi, delle scale, degli ambienti e delle prestazioni attualmente conosciuti.
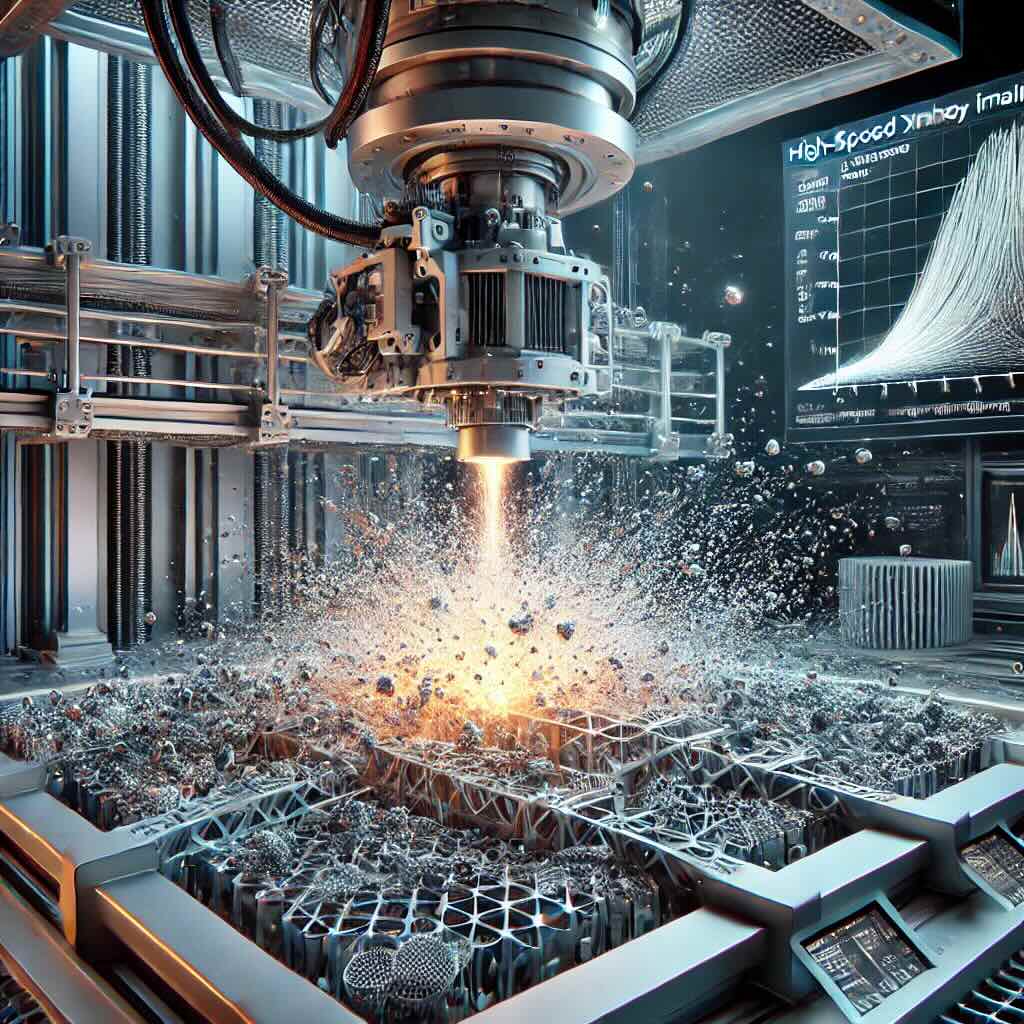