Post-elaborazione nella stampa 3D (parte 1): la chiave per risultati di produzione realizzabili
Ci sono molti vantaggi associati all’uso dei processi di stampa 3D industriale come tecnologia di produzione. A livello intersettoriale, gli OEM continuano a trarre vantaggio dal fatto che, utilizzando la stampa 3D, sono in grado di produrre parti complesse, in un unico pezzo, in modo economicamente sostenibile. Inoltre, la stampa 3D consente la produzione di parti più resistenti e leggere, il consumo di materiale ridotto e il consolidamento dei componenti in una vasta gamma di applicazioni.
Tali vantaggi sono stati tutti giustamente evidenziati negli ultimi due decenni poiché la stampa 3D si è affermata come una tecnologia davvero dirompente. Prima nell’area della prototipazione e più recentemente nell’area della produzione. Questi vantaggi sono generalmente visti come abilitati dall’hardware di stampa 3D che costruisce le parti.
Nel mondo reale, tuttavia, questo è nel migliore dei casi un quadro parziale. Quando consideriamo specificamente l’uso della stampa 3D per applicazioni di produzione, le macchine per la stampa 3D industriale sono in realtà solo una parte di un vasto ecosistema di tecnologie che consentono la produzione di parti, sia pre che post-costruzione.
L’attenzione esclusivamente al processo di costruzione della stampa 3D significa che una parte cruciale della catena del processo di produzione viene trascurata, vale a dire le fasi di post-elaborazione una volta che le parti vengono rimosse dalla macchina da stampa 3D. Per gli OEM che stanno valutando l’uso della stampa 3D, ovviamente il punto di partenza è selezionare un processo di stampa 3D che costruisca parti che corrispondano ai requisiti dell’applicazione rilevanti per il materiale, la geometria e la funzione della parte, la dimensione della parte e i volumi delle parti richieste . Tuttavia, dopo ciò, e alcuni sostengono contemporaneamente, è necessario prendere in considerazione tutti i requisiti di post-elaborazione, altrimenti non è esagerato affermare che l’uso della stampa 3D come valida alternativa ai processi di produzione tradizionali potrebbe finire per completamente annullato in termini di tempi e costi.
Post-elaborazione delle parti PBF
3DPRINTUK è in prima linea nell’uso dei processi di stampa 3D con fusione a letto di polvere polimerica (PBF) e qui presentiamo una panoramica di tutte le opzioni di post-elaborazione disponibili per le parti in polimero PBF. Tuttavia, l’articolo si concentrerà anche in modo più specifico sulle tecnologie di finitura automatizzate che vengono sviluppate e/o perfezionate per l’uso specifico con volumi più elevati di parti stampate in 3D.
Una cosa fondamentale da capire per i processi di stampa 3D PBF di polimeri è che ci sono fasi primarie di post-elaborazione che sono necessarie da applicare una volta che le parti escono dalla macchina. Questi comportano la depolverizzazione e la pulizia delle parti. Tuttavia, ci sono anche fasi di post-elaborazione secondarie – processi opzionali – che possono fornire ulteriori vantaggi come un’estetica migliorata, caratteristiche della superficie migliorate e/o una funzionalità meccanica superiore delle parti stampate in 3D.
Post-processi primari per parti PBF
In poche parole, una volta completata la costruzione su un sistema di stampa 3D PBF in polimero, le parti devono passare attraverso il processo post-costruzione di rimozione e pulizia della polvere non fusa.
Una parte dell’auricolare VR (SLS) viene estratta dal post-raffreddamento della build.
Tradizionalmente si trattava di un processo manuale che utilizzava un getto d’aria, tuttavia ora esistono soluzioni automatizzate per questo processo. Per darti un’idea: a 3DPRINTUK lo facevamo a mano con un blaster ad aria, che richiedeva in media 1,5 ore per build. Ora abbiamo installato una serie di sistemi di pulizia automatizzati ( Powershot C di Dyemansion ), che impiegano in media 8 minuti per ciclo per rimuovere la polvere e pulire le parti. Ovviamente, le parti devono ancora essere spostate dalle stampanti 3D ai sistemi di pulizia, ma i risparmi sui costi e sulla manodopera sono considerevoli, soprattutto quando si lavora con più stampanti e volumi elevati di parti.
Quando le parti escono dal Powershot C hanno una finitura superficiale naturale. Questo è generalmente considerato “grezzo” rispetto allo stampaggio a iniezione e/o ai processi di stampa 3D a base di resina, motivo per cui per alcune applicazioni può essere richiesta un’ulteriore post-elaborazione opzionale.
All’interno del Dyemansion Power Shot C durante il processo di depolverizzazione.
La rimozione della polvere, però, non può essere garantita al 100% per ogni sua parte. Parti particolarmente complesse con fori e canali integrati. Questo è il motivo per cui le linee guida di progettazione tenendo conto del processo PBF e della post-elaborazione sono importanti.
Vale anche la pena notare qui che il polimero PBF non richiede strutture di supporto poiché la polvere polimerica non sinterizzata in qualsiasi build supporta le parti stampate in 3D. Ciò è vantaggioso in termini di post-elaborazione, poiché elimina la necessità di rimuovere il supporto.
Post-processi secondari per parti PBF
Come accennato in precedenza, dopo il processo di pulitura, le parti in polimero PBF hanno una finitura superficiale naturale “ruvida”. Per le parti funzionali questo può essere spesso abbastanza buono, in base alle proprietà meccaniche del polimero selezionato dalla macchina. Tuttavia, per le parti che richiedono una finitura superficiale più liscia e/o funzionalità avanzate, è disponibile una gamma di fasi di post-elaborazione opzionali, che includono, a titolo esemplificativo:
Lucidatura a vibrazione
pallinatura (detta anche granigliatura)
Lucidatura chimica
Tintura / colorazione
Pittura/Texture
Galvanostegia
Lavorazione
Questo elenco può essere suddiviso in due sottoinsiemi: essenzialmente i primi quattro processi hanno soluzioni automatizzate sul mercato e possono essere applicati a volumi maggiori o massicci di parti. Mentre gli ultimi tre processi nell’elenco sono processi molto personalizzati, che richiedono manodopera/tempo e non sono particolarmente adatti per elevati volumi di parti.
Per una finitura prossima allo stampaggio a iniezione, le parti possono essere lucidate a vibrazione.
Volumi più elevati di parti per la produzione in lotti sono l’obiettivo principale di 3DPRINTUK, quindi stiamo implementando soluzioni automatizzate per la post-elaborazione e possiamo testimoniarne i vantaggi. Le sezioni seguenti spiegheranno perché questo è il caso. Negli articoli di follow-up, ci concentreremo più in dettaglio sui singoli processi di post che utilizziamo, fornendo i pro ei contro di ciascuno. Discuteremo anche i processi più personalizzati e il “perché non li offriamo”, indicandoti la giusta direzione, se vuoi seguire quella strada.
Finitura automatizzata per parti stampate in 3D in polimero PBF
Fino a poco tempo, l’uso di tecnologie di finitura di massa automatizzata per le parti prodotte utilizzando la stampa 3D era alquanto incostante, con poca comprensione degli attributi unici di una parte stampata in 3D. Le parti stampate in 3D presentano tutta una serie di sfide uniche quando si guarda alla finitura di massa. La superficie naturale delle parti stampate in 3D in polimero PBF è molto più ruvida delle parti prodotte utilizzando tecnologie tradizionali come lo stampaggio a iniezione, o addirittura, processi di stampa 3D in resina come SLA / DLP / Polyjet ecc. Inoltre, un enorme vantaggio della stampa 3D come strumento di produzione, ovvero la sua capacità di produrre geometrie altamente complesse, ha tradizionalmente reso difficile la lucidatura. La necessità di soluzioni automatizzate dedicate per questo era evidente.
Negli ultimi anni l’attenzione alla ricerca di tali soluzioni è aumentata, oltre a renderle commercialmente valide.
Soluzioni emergenti di post-elaborazione ad alto volume per 3DP
È giusto dire che gli attributi unici delle parti stampate in 3D, che in genere hanno una qualità superficiale relativamente scarsa subito dopo la costruzione, non sono meglio serviti dalla maggior parte delle tecnologie di finitura di massa standard del settore. Le opzioni di finitura di massa standard sono progettate per parti e componenti prodotti dai processi di produzione tradizionali.
In uno scenario di produzione tradizionale, la prospettiva che le fasi di post-elaborazione siano responsabili di oltre il 50% dei costi delle parti sarebbe insostenibile e sicuramente insostenibile. Quindi, cosa si sta facendo per questa barriera anomala e potenzialmente proibitiva alla fattibilità della stampa 3D come tecnologia di produzione?
Bene, c’è effettivamente un movimento a tenaglia al lavoro. Da un lato, gli sviluppatori di piattaforme tecnologiche di stampa 3D perfezionano costantemente i processi per ridurre la rugosità superficiale delle parti stampate in 3D e, dall’altro, le aziende di post-elaborazione esperte ed emergenti stanno innovando e adattando le tecnologie di finitura di massa per soddisfare al meglio le parti stampate in 3D . Ciò significa concentrarsi in particolare sugli adattamenti che consentono la post-elaborazione di parti a volte estremamente geometricamente complesse.
Questo movimento a tenaglia sta effettivamente erodendo i costi e i tempi necessari per la post-elaborazione delle parti stampate in 3D e, così facendo, faciliterà la produzione di parti stampate in 3D con caratteristiche di superficie e levigatezza che rivaleggiano con quelle prodotte su processi di produzione della plastica legacy come lo stampaggio a iniezione ad un costo più competitivo. In altre parole, l’obiettivo è quello di consentire la produzione di parti di forma quasi netta con caratteristiche superficiali superiori senza compromettere l’integrità delle parti. Quando ciò sarà raggiunto, la fattibilità della stampa 3D come alternativa di produzione sarà riconosciuta da un numero crescente di aziende e la tecnologia sarà in una posizione migliore per sconvolgere il tradizionale paradigma di produzione.
Progetta e costruisci per la post-elaborazione
Vari parametri possono influenzare l’efficienza di un’operazione di post-elaborazione per le parti stampate in 3D, tutti fattori che giocano sul fatto che le operazioni di post-elaborazione dovrebbero essere considerate all’inizio della fase di progettazione. Come accennato in precedenza, la rimozione della polvere può essere un inconveniente particolare per progetti complessi o progetti con fori/canali più profondi. Comprendere questo e applicare funzionalità di progettazione attenuanti può eliminare i problemi.
Ti faccio un esempio: un cliente che ci ha contattato di recente a seguito di una raccomandazione è un produttore di sensori. Stavano cercando di produrre in batch una serie di piccoli componenti di sensori, a uno sconto di 10.000. Le parti dovevano essere di qualità per stampaggio a iniezione, ma il regolare fornitore di IM per iniezione dell’azienda ha ignorato il progetto (per qualsiasi motivo). Di conseguenza, e dopo aver sentito parlare di 3DPRINTUK ci hanno inviato dei pezzi di prova, da stampare e post-elaborare.
Le parti erano piccole e rotonde, intorno al segno di 4 cm, ma con un foro di 1 mm che attraversava tutte le parti. In termini di funzionalità e finitura, le parti si adattano perfettamente alla produzione in lotti con il polimero PBF: sarebbe economico con buoni tempi di consegna.
Tuttavia, la natura del design originale significava che c’erano problemi con la rimozione della polvere dal foro. Lavorando con il team 3DPRINTUK, questa azienda è stata ora in grado di ottimizzare il design della parte in modo che il foro rimanga libero. Ciò ha comportato modifiche agli angoli di sformo e alla forma del foro stesso. Osservando il design da un punto di vista AM, il team di 3DPRINTUK è stato in grado di porre domande sul design e ripensare i limiti che qualcuno senza una conoscenza specialistica dei processi PBF potrebbe non aver considerato.
Progettare per la parte e per come è realizzata e finita può favorire l’innovazione, il risparmio sui costi e la produzione just in time.
Con l’applicazione giusta questo approccio offre una vittoria | Vinci | Vinci la soluzione.
Dopo la pulizia della parte dell’auricolare SLS VR.
I vantaggi della finitura di massa
Quando si valutano le tecnologie di finitura di massa, è importante capire se i processi sono semplicemente processi legacy che sono stati ora applicati alla stampa 3D o se i processi sono stati adattati ai capricci delle parti stampate in 3D.
L’ambiente di post-elaborazione sta crescendo con nuove tecnologie progettate per la stampa 3D, molte delle quali utilizzano tecniche innovative per spingere la busta quando si tratta della finitura di parti stampate in 3D.
Quando si tratta di finitura di massa, tuttavia, se opportunamente adattate alle parti stampate in 3D, sono ora disponibili soluzioni di post-elaborazione vere e proprie economiche che offrono al settore della stampa 3D gli stessi vantaggi della produzione tradizionale, riducendo il prezzo per parte per volumi maggiori.
da Printuk.co.uk
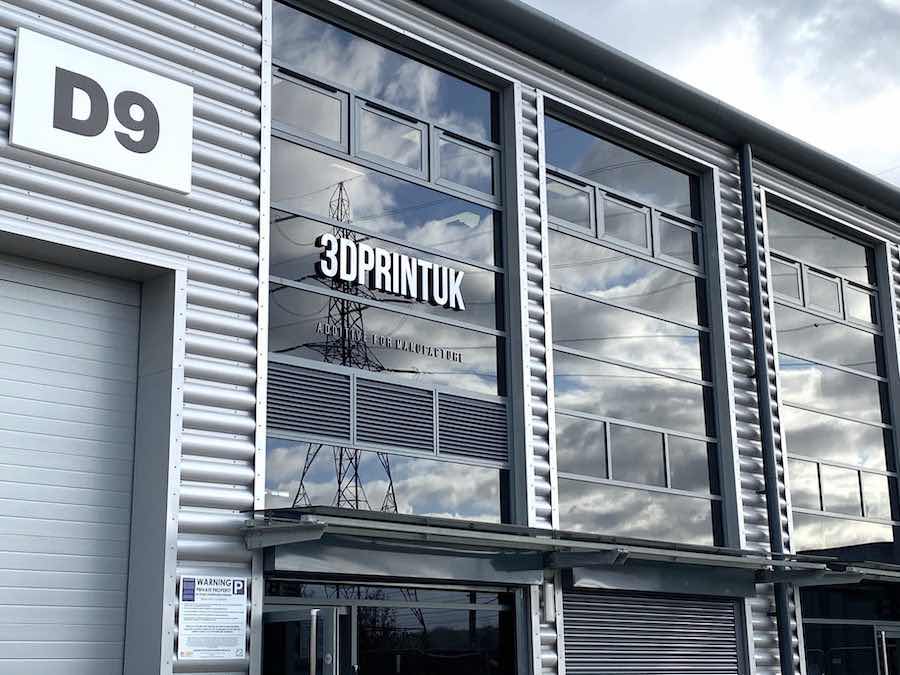