Post-elaborazione nella stampa 3D (parte 2) — Soluzioni di post-elaborazione automatizzate
In 3DPRINTUK siamo specializzati in tecnologie di stampa 3D con fusione a letto di polvere polimerica (PBF) e volumi elevati di parti, in particolare offrendo servizi di produzione in batch. Attualmente produciamo più di 1 milione di pezzi all’anno, con capacità e volume di pezzi che continuano ad aumentare costantemente. La post-elaborazione è una parte molto importante del nostro servizio, ma poiché i volumi sono aumentati, abbiamo dovuto reperire le migliori soluzioni disponibili per soddisfare le nostre esigenze e la capacità di fornire ai nostri clienti. Ciò ha significato concentrarsi sui sistemi automatizzati di post-elaborazione, come delineato nella Parte 1 di questa serie di articoli. Di conseguenza, abbiamo investito in una suite completa di macchine Dyemansion, compresi i processi di post-elaborazione sia primari che secondari. Attualmente, operiamo 2 macchine Powershot C, 2 macchine Powershot S e 3 DM 60 Dyer, insieme a una serie di macchine vibrolucidatrici di Sharmic Engineering.
Questo articolo testimonia la nostra esperienza con questa gamma di soluzioni di post-elaborazione automatizzate nel modo più aperto e onesto possibile. Non ci concentriamo su processi di post-elaborazione personalizzati alternativi, tra cui verniciatura, post-lavorazione o galvanica. Né ci concentriamo sull’assemblaggio, che probabilmente è anche considerato “post-elaborazione”.
Come spiegato nel primo articolo, suddividiamo questi processi di post automatizzati in due sottosezioni: processi primari (necessari) e processi secondari (opzionali).
Post-processi primari
Per qualsiasi parte stampata in 3D PBF è essenziale rimuovere la polvere e pulire le parti. Ci sono vari metodi disponibili qui, inclusi ma non limitati a sabbiatura ad aria, sabbiatura a getto d’acqua, ghiaccio secco e sabbiatura.
All’interno del Powershot C per la pulizia e la rimozione della polvere dalle parti stampate in 3D.
Le fasi primarie di post-elaborazione sono fornite di serie come parte del servizio 3DPRINTUK. Abbiamo investito molto nell’automazione di questo processo, in particolare utilizzando le macchine Powershot C di Dyemansion e continueremo ad estendere la nostra capacità all’aumentare della domanda. Sostanzialmente questo kit comprende una sabbiatrice di alto livello incrociata con una botte di lavatrice in grado di lavorare fino a 5 kg di pezzi per ciclo. Questo processo fornisce una “finitura naturale”: il modo in cui abbiamo sempre descritto questa finitura è come una menta extra forte, una consistenza leggermente polverosa.
È importante capire, però, che direttamente dalla macchina, le parti sono ricoperte di polvere di circa 3-4 mm di profondità, ed è piuttosto testardo. Questa macchina rimuoverà la polvere, per lasciare le parti con una finitura opaca naturale.
Parte MJF con finitura naturale.
Professionisti:
Questo è un processo semplice e veloce. Per fornire un contesto, completavamo questo processo manualmente, utilizzando una pistola ad aria compressa e aria compressa per rimuovere la polvere da ogni parte individualmente. In media, ci vorrebbe circa un’ora e mezza per ogni build. In confronto, il Powershot C pulirà un’intera build in 8 minuti.
Sebbene altri processi post abbiano un impatto trascurabile sulle dimensioni, Powershot C fornisce le dimensioni più fedeli alla stampa. È importante qui evidenziare le “dimensioni di stampa” rispetto alle dimensioni STL. La tolleranza per qualsiasi stampa è generalmente dello 0,3%, anche se in 3DPRINTUK otteniamo regolarmente risultati migliori, quindi qualsiasi parte pulita sulla Powershot C è la più vicina alla parte uscita dalla stampante. Inoltre, gli spigoli vivi e i fili sono più nitidi da questo processo.
Contro:
Relativamente allo stampaggio a iniezione, le parti che vengono solo pulite, senza post-elaborazione secondaria, hanno la finitura più ruvida. Come notato sopra, la finitura naturale ha una consistenza polverosa, una finitura opaca, per così dire.
Di conseguenza, questo tipo di finitura raccoglierà intrinsecamente i segni delle dita, il che è un problema per le parti che vengono maneggiate frequentemente.
Le parti con fori/canali possono richiedere una pulizia aggiuntiva. Per evitare ciò si consiglia un diametro minimo di 3 mm per questi tipi di caratteristiche.
Questo processo di pulizia può influire sulla qualità di qualsiasi processo di tintura secondario a causa della natura del processo stesso, per cui il mezzo di granigliatura è il vetro e minuscoli frammenti di vetro possono essere incorporati nella superficie di una parte. I frammenti di vetro sono così piccoli che non possono essere visti o percepiti, tuttavia, il vetro non si tinge. Ciò significa che le parti potrebbero mostrare incongruenze se tinte.
Post Processi Secondari
Esistono numerosi motivi per applicare la post-elaborazione opzionale alle parti, inclusi, a titolo esemplificativo ma non esaustivo, i vantaggi ottenuti in termini di estetica, prestazioni delle parti e proprietà dei materiali migliorate.
Lucidatura a vibrazione
Alla 3DPRINTUK gestiamo due macchine vibranti rotonde Sharmic automatizzate. Questi sistemi sono dotati di una gigantesca vasca vibrante di 1,4 m di diametro, riempita con trucioli di ceramica che abradono e comprimono le superfici esterne delle parti. Si noti che le dimensioni, la forma e il materiale dei chip possono influire sui tempi e sui risultati. Utilizziamo chip ceramici più grandi a forma di cono poiché abbiamo riscontrato che producono i migliori risultati complessivi con le parti stampate in 3D.
Professionisti:
Questo processo fornisce una finitura molto liscia rispetto alla finitura naturale sopra descritta. Il confronto qui è fatto intenzionalmente con la finitura naturale, ed è quindi importante capire che non si tratta di una finitura lucida paragonabile allo stampaggio a iniezione. Per continuare l’analogia con le zecche, descriveremmo questa finitura come più simile a un Mentos / Softmint.
È un processo relativamente veloce. Abbiamo identificato un ciclo di 2 ore per ottenere risultati e tempi di consegna ottimizzati. Due ore si traducono in uno smalto davvero decente. Un’ora può produrre risultati ok e c’è pochissima differenza tra le parti che escono dopo 2 ore anche fino a 8 ore.
Le macchine possono elaborare grandi volumi di parti per ciclo, in genere fino a 1000 parti per ciclo di 2 ore.
È un processo molto conveniente, in particolare in termini di prezzo per pezzo per volumi elevati. 2 ore divise per 1000 parti sono solo secondi per parte. È anche relativamente economico eseguire questo processo, i trucioli di ceramica si consumano molto lentamente e l’unico requisito aggiuntivo per l’alimentazione è l’acqua, che scorre attraverso la macchina per rimuovere la polvere in eccesso.
Contro:
Il danno è molto probabile su parti sottili e molto piccole. Per mitigare questo rischio, fissiamo limiti di 2 mm di spessore minimo in tutte le direzioni per le parti che richiedono la lucidatura. Molti dei nostri clienti scelgono di scendere al di sotto di questo limite a proprio rischio e, nella maggior parte dei casi, lucidano bene, tuttavia, non possiamo garantire che le parti con bordi affusolati o pareti non supportate non vengano danneggiate al di sotto di 2 mm.
La lucidatura a vibrazione può causare la filettatura di spigoli vivi. Le parti con angoli di 90° possono perdere alcuni decimi di mm dal loro apice. Per la maggior parte delle applicazioni questo è accettabile, ma dovresti essere consapevole che le parti possono perdere bordi perfettamente dritti con questo processo.
Durante il processo viene persa una quantità estremamente piccola di materiale dalla superficie generale delle parti, ben al di sotto dei 100 micron. Questo è molto inferiore alla precisione di ±0,3 mm della macchina, quindi può essere considerato trascurabile e non deve essere tenuto in considerazione nella progettazione della parte.
Un altro problema comune è che i trucioli di lucidatura possono rimanere bloccati all’interno dei fori, letteralmente qualsiasi foro che riescono a trovare.
Queste macchine sono molto rumorose. Se stai utilizzando un servizio di stampa 3D, questo è il nostro problema. Ma per chiunque cerchi di portare le operazioni in casa, non sottovalutarlo. Hanno bisogno del loro spazio.
pallinatura
Le parti pulite vengono post-elaborate mediante sabbiatura ad alta velocità di materiale plastico sulla superficie della parte, per migliorare la finitura superficiale. Ciò si traduce in una lucentezza semilucida o ruvida sulla parte, ed è personalmente la mia finitura preferita, nonché il miglior rapporto qualità-prezzo. Il processo di pallinatura è di natura simile al processo di pulizia descritto sopra e in realtà il kit è simile. I sistemi di pallinatura automatizzati (Dyemansion Powershot S) che utilizziamo impiegano due ugelli che sparano perle di polimero nel tamburo rotante contenente i pezzi ad alta pressione. Il punto in cui il processo differisce dal processo di pulitura, tuttavia, è il mezzo polimerico e, significativamente, la pressione di esercizio: funziona a una pressione considerevolmente più alta per la pallinatura. Quindi, per la pulizia si parla di 2-3 bar,
Professionisti:
Questo è un processo super veloce: 15 minuti per lotto di parti anziché 2 ore, anche se per essere onesti i lotti sono più piccoli.
Aspetto e finitura levigati superiori rispetto alla lucidatura. Ciò è particolarmente significativo per le parti che verranno tinte o verniciate.
Nessuna sostanza chimica è coinvolta in questo processo: viene fatta esplodere solo aria e perline di plastica.
Contro:
L’unico vero problema con questo processo è che le perline, che hanno un diametro di circa 0,5 mm, rimangono bloccate in fessure strette e canali di parti. Ciò include qualsiasi testo o logo stampato sulla parte. Per questo motivo, si consiglia di incorporare canali minimi di 0,7 mm per le parti che richiedono una finitura con pallinatura. Una soluzione alternativa consiste nell’incorporare angoli di sformo su qualsiasi testo inciso o dettagli di superficie.
Tintura
3DPRINTUK attualmente gestisce tre sistemi Dyemansion DM 60 che forniscono un processo automatizzato per la tintura profonda delle parti. Questo kit è effettivamente una grande pentola a pressione su misura per le esigenze delle parti polimeriche stampate in 3D. Le parti sono tinte sotto pressione, il che assicura che la tintura penetri più in profondità nella superficie della parte (rispetto all’ammollo in una vasca di tintura) e si traduca in un colore resistente e duraturo.
Professionisti:
Ancora una volta, è un processo relativamente veloce. Grandi lotti possono essere caricati nella macchina con il colorante selezionato, premere un pulsante e dopo 2 ore e un po’, il processo di tintura è completo e non richiede altro lavoro oltre al carico e scarico dei pezzi.
Questi sistemi automatizzati sono macchine molto pulite e sicure.
Il colorante penetra 0,25-0,5 mm nella superficie della parte, fornendo una finitura più duratura rispetto alla vernice. Ciò significa che le parti sono meno soggette a scheggiature.
La tintura delle parti con questo processo è notevolmente più economica della verniciatura.
Contro:
Le parti tinte generalmente non sono lisce come una parte dipinta, con l’avvertenza che la pittura è generalmente preceduta da levigatura, riempimento e adescamento della parte (cioè molto lavoro manuale). Se dipingi a spruzzo una parte con una finitura naturale, c’è poca o nessuna differenza visiva rispetto a una parte colorata.
I risultati con la tintura dipendono dal processo di stampa 3D utilizzato. In 3DPRINTUK sia le parti SLS che MJF possono essere colorate con successo in nero. Tuttavia, tingiamo solo le parti SLS con il colore. Ciò è dovuto al fatto che le parti SLS sono bianche e danno luogo a parti tinte di colori forti e vivaci. Le parti MJF si staccano dalla macchina in grigio e, di conseguenza, non sono così ricettive alla tintura di colore e producono colori tenui. Quando si tinge di nero le parti, MJF offre un vantaggio rispetto a SLS in quanto le parti interne sono nere, con una superficie grigia: se tinte di nero sono completamente nere. In confronto, le parti SLS bianche tinte di nero sono nere solo fino a 0,25 mm. Questo può essere un problema per le parti graffiate e scheggiate.
Questo processo successivo comporta costi di configurazione più costosi e anche i costi dei materiali di consumo sono un problema. Le cartucce di tintura a colori sono costose, quindi il ROI richiede maggiori volumi di parti per un dato colore.
Levigatura chimica
Divulgazione completa, non stiamo offrendo questo post-processo come servizio a 3DPRINTUK, per il momento! Attualmente lo stiamo testando e possiamo testimoniare la natura di questo processo e il suo valore.
Il processo prevede il rilascio di vapori chimici all’interno di un ambiente controllato, che fondono chimicamente la superficie delle parti. I vapori vengono quindi completamente evacuati e la sostanza chimica recuperata. La levigatura a vapore si traduce in una finitura lucida che è vicina allo stampaggio a iniezione.
Professionisti:
È senza dubbio la finitura più lucida di tutte e la finitura più vicina alle parti stampate a iniezione.
La parte di lisciatura del processo è completamente automatizzata e sicura.
È un processo relativamente veloce in termini di automazione, con un tempo di ciclo di 40 minuti.
La forza della parte è aumentata. Questo perché stai fondendo e riformando la superficie, il che si traduce in una superficie più omogenea e più resistente alla parte. La superficie diventa sigillata e lavabile.
Grandi lotti possono essere completati in un unico ciclo.
Contro:
Nonostante sia un processo automatizzato, sono necessarie (almeno rispetto agli altri processi di cui sopra) alcune ore di lavoro per la levigatura del vapore. Questo perché il vapore deve poter avvolgere completamente ogni parte. L’unico modo per garantirlo è appendere tutte le parti a un gancio. Ciò significa che devi mettere dei ganci nella parte o progettare ganci nella parte a cui appenderlo e quindi qualcuno deve appenderlo manualmente. Questo è laborioso e in realtà richiede esperienza in termini di comprensione del centro di gravità e delle superfici primarie, ecc.
Questo processo di finitura può esagerare eventuali imperfezioni nella parte: può trattarsi di una linea di livello o di qualsiasi piccola imperfezione della costruzione. Le finiture opache non le mostrano. Il 99,9% delle volte, questo non è un problema, ma il punto qui è che può.
Rispetto ad altri processi automatizzati non è così conveniente.
Per la produzione in lotti, il nostro consiglio è di gestire le tue aspettative quando si tratta di stampa 3D e post-elaborazione delle tue parti. Possiamo – e abbiamo – dimostrato il valore del nostro servizio. Ha consentito ai clienti di risparmiare ingenti somme di denaro come ponte tra la prototipazione e lo stampaggio a iniezione. Detto questo, è importante comprendere i processi coinvolti per la stampa 3D e la post-elaborazione, insieme alle tolleranze per la variazione. Ripeto, per il 99,99% dei pezzi di nostra produzione, le imperfezioni sono minime e non pregiudicano la funzionalità dei pezzi per l’applicazione prevista. Sono parte integrante degli articoli stampati in 3D, anche con le apparecchiature di fascia più alta oggi disponibili, è davvero importante per noi che i nostri clienti comprendano i processi e le realtà coinvolte piuttosto che essere travolti da false affermazioni su ciò che è realizzabile.
Post-elaborazione riuscita
Di seguito sono riportati un paio di risultati positivi con parti stampate in 3D post-elaborate:
Uno dei nostri clienti, Weisner Design, combina la passione per le Porsche classiche con la produzione additiva per riportare in vita parti rare e non più disponibili. In azienda, l’attenzione si concentra su parti che sono antieconomiche per lo stampaggio a iniezione in bassi volumi, soprattutto dove sono coinvolte geometrie complesse. Qui riconoscerai tutti i vantaggi che la stampa 3D può offrire e Weisner impiega intenzionalmente i punti di forza della produzione additiva per produrre parti buone come l’originale, o meglio! Ma le parti devono essere rifinite con un’alta qualità. Queste parti sono state pallinate e colorate.
Parte stampata in 3D, pallinata e tinta di nero.
Un altro cliente, che abbiamo evidenziato in precedenza, è Rogue Products , a
Consulenza creativa per il design industriale. La progettazione, lo sviluppo e la produzione di occhiali VR da parte dell’azienda ha comportato la stampa 3D con MJF PA12 e quindi la post-elaborazione con vibrolucidatura e successivamente tinti di nero.
Questi casi ti consentono di giudicare da solo i risultati che possono essere raggiunti con diversi processi post. Come sempre, tuttavia, queste scelte sono spesso determinate dall’applicazione e dal volume delle parti coinvolte, tuttavia, la comprensione delle varie opzioni, in particolare per la post-elaborazione automatizzata, ti garantirà il miglior risultato possibile per la tua applicazione.
da printuk.co.uk
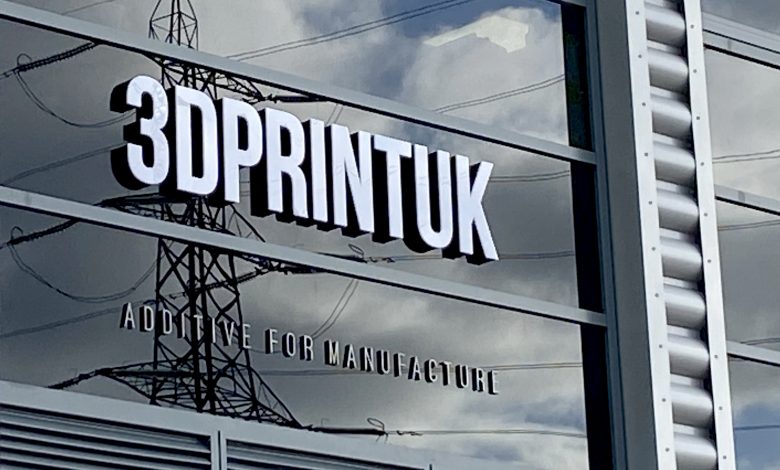