Origine del mistero
La prima traccia di questo processo è comparsa in un post anonimo su Reddit a cura dell’utente “Weird‑League‑1844”, che ha condiviso una singola immagine e una serie di dettagli sommari su una nuova macchina per stampa 3D metallica. Non è noto il nome dell’azienda responsabile né la sua ubicazione. L’unico elemento certo è che il prototipo in fase di test utilizza una tecnologia basata sulla deposizione controllata di gocce di metallo fuso, un approccio che si avvicina all’inkjet ma con volumi di materiale decisamente superiori.
Principi di funzionamento
Il cuore del sistema è una testina multipla che rilascia, in sequenza, microlitri di lega metallica (soprattutto bronzo nelle prove iniziali) direttamente sul piano di stampa. A differenza dei tradizionali processi laser‑PBF o binder jetting, qui non è prevista alcuna fase di sinterizzazione o fusione successiva: le gocce solidificano istantaneamente appena toccano la superfice riscaldata, formando un solido coeso. Questo permette di ottenere pezzi completi già al termine dell’estrusione, riducendo tempi e consumi energetici.
Caratteristiche dei campioni realizzati
I modelli mostrati hanno un ingombro massimo di circa 22 mm per lato, con una precisione dimensionale che oscilla fra 0,2 e 0,5 mm a seconda dell’orientamento. La densità interna sembra inferiore al metallo pieno, suggerendo l’uso di una struttura parzialmente porosa che alleggerisce il componente. Il piatto di costruzione, di forma circolare e dalla superficie ruvida, punta a facilitare l’adesione delle prime gocce e potrebbe indicare un meccanismo di stampa delta, sebbene i movimenti rapidi tipici degli inkjet rendano più probabile un sistema cartesiano ottimizzato per alte velocità.
Confronto con altre soluzioni sul mercato
Alcune aziende esplorano tecniche comparabili:
-
Desktop Metal ha sviluppato processi di binder jetting seguiti da sinterizzazione, che però richiedono forni dedicati e cicli termici estesi.
-
XJet utilizza micro‑inkjet per depositare gocce di metallo o ceramica in sospensione, ma i volumi per goccia restano nell’ordine del nanolitro e necessitano di post‑processing.
-
Meltio propone un approccio di wire‑fed DED con piccolo hot‑wire e laser, ottimo per riparazioni ma meno adatto al dettaglio su piccola scala.
-
Fraunhofer IFAM studia varianti di cold spray per applicazioni industriali, senza raggiungere però risoluzioni inferiori al millimetro.
Questa nuova tecnologia si distingue per la capacità di costruire direttamente pezzi finiti, con un prezzo di produzione stimato sotto i 10.000 USD per macchina, soglia che la renderebbe appetibile a laboratori indipendenti e centri di ricerca universitari.
Software e automazione integrata
Il gruppo anonimo ha sviluppato un software di slicing proprietario, concepito per gestire traiettorie complesse e sequenze di gocce multiple. La piattaforma include algoritmi per compensare la tendenza alla deviazione delle gocce ad alta velocità, un problema noto in applicazioni inkjet avanzate. Non sono ancora chiari i requisiti ambientali: tipicamente questi sistemi richiedono camere in atmosfera controllata per evitare ossidazioni, ma la rapidità di solidificazione potrebbe ridurre il bisogno di gas inerte.
Sfide da affrontare
Per trasformare il prototipo in un prodotto maturo, servono:
-
Migliore controllo dimensionale, con feedback in tempo reale per correggere deviazioni.
-
Espansione dei materiali, testando acciai, leghe di titanio e superleghe Inconel, rilevanti in aerospazio e automotive.
-
Certificazioni per impiego in settori regolamentati, come il medicale o la difesa.
-
Scalabilità del piano di stampa, per passare dai centimetri a volumi maggiori, restando sotto la soglia di costo prefissata.
Orizzonti di sviluppo
L’annuncio lascia intendere che, una volta completata la fase di R&S, questa tecnologia potrebbe essere adottata da:
-
FabLab e università, grazie all’accessibilità economica.
-
Piccole officine che producono ricambi custom, dove la rapidità di esecuzione è cruciale.
-
Settore educativo, per dimostrazioni pratiche di manifattura additiva metallica senza forni di sinterizzazione.
Il percorso da qui in avanti includerà verosimilmente collaborazioni con specialisti di ottimizzazione del flusso, fornitori di leghe in polvere e integratori di sistemi di visione artificiale per ispezione post‑deposito.
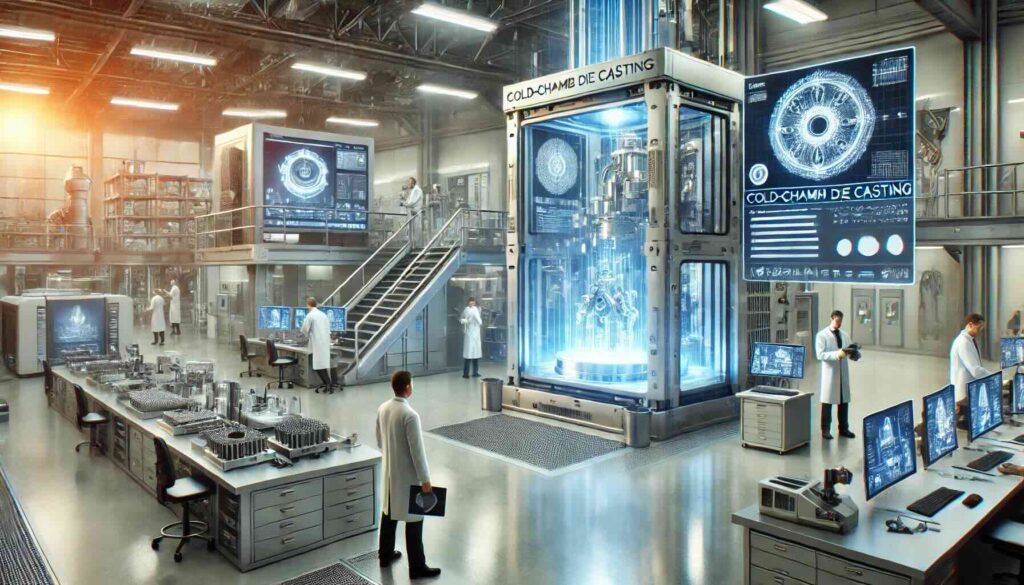