.
Introducendo una materia prima a base biologica nel processo di stampa in nanofibra di cellulosa (CNF), il team di UMaine ritiene che sia possibile ridurre del 50% i costi di produzione delle parti di grande formato. Come parte del progetto, l’ Oak Ridge National Laboratory (ORNL) integrerà anche elementi riscaldanti stampati in 3D nello stampo, poiché il gruppo di ricerca congiunto mira ad accelerare la ricerca e lo sviluppo di tecnologie energetiche verdi.
“L’Università del Maine rimane un leader nella tecnologia AM e nell’energia eolica, e questo finanziamento sfrutterà l’esperienza dei ricercatori in entrambe le aree”, ha detto la senatrice statunitense Susan Collins all’annuncio del premio. “Siamo entusiasti che il Dipartimento dell’Energia continui a investire nella ricerca all’avanguardia di UMaine”.
Sostenuti da ORNL e dal DoE, i ricercatori di UMaine hanno sviluppato il loro approccio CNF da maggio 2019. In primo luogo, la ricerca del team è incentrata sulla ricerca e sviluppo di una nuova materia prima a base di legno e sulla valutazione della sua idoneità per la stampa 3D, eseguendo più modellazione in scala e analisi del ciclo di vita della sostenibilità.
Il materiale stesso si basa sulla nanocellulosa, una variazione delle cellule presenti nelle piante verdi, che hanno la stessa resistenza alla trazione dell’alluminio e qualità non tossiche. Mentre le fibre rinnovabili sono state spesso utilizzate per fabbricare medicazioni intelligenti all’interno di applicazioni sanitarie, il team di UMaine le ha sempre più utilizzate per creare strutture più grandi, come una barca stampata in 3D di 25 piedi
Utilizzando una macchina personalizzata di grande formato creata da Ingersoll Machine Tools , i ricercatori di UMaine sono stati in grado di produrre un veicolo da 5000 libbre da record, che chiamano “3Dirigo”. Altrove, il sistema è stato implementato anche dal CCDC Soldier Center dell’esercito americano per stampare in 3D rifugi lunghi 12 piedi, ei ricercatori hanno ora scelto di collaborare di nuovo con Ingersoll, per fabbricare componenti di pale eoliche di grandi dimensioni.
Al momento, gli stampi e gli strumenti necessari per progettare e costruire pale di turbine possono costare fino a $ 10 milioni e il processo che richiede tempo richiede spesso 16-20 mesi per essere completato. Di conseguenza, nel momento in cui nuovi design arrivano sul mercato, possono già essere obsoleti, disincentivando l’innovazione in quello che è un settore in crescita.
Ecco perché l’ Advanced Structures and Composites Center di UMaine sta sviluppando un metodo più rapido e a basso costo per la stampa 3D degli stampi. Durante il progetto da 2,8 milioni di dollari, il team di UMaine intende utilizzare quella che chiamano la “più grande stampante di polimeri del mondo” insieme a materie prime riciclabili e supporti in legno, per fabbricare enormi stampi di plastica.
I ricercatori stimano che il loro nuovo processo potrebbe produrre un risparmio sui costi del 25-50%, riducendo i tempi di consegna delle pale delle turbine fino a sei mesi. Come parte di un altro premio da 4 milioni di dollari, UMaine collaborerà anche con ORNL, per sperimentare il deposito robotico di fibre di rinforzo continue nelle lame additive.
Dato che è fondamentale controllare le temperature della superficie dello stampo durante la produzione, ORNL prevede che i suoi elementi riscaldanti serviranno a fornire ulteriori riduzioni di tempi e costi. Nel complesso, i risultati del progetto potrebbero rivelarsi significativi, poiché i principali fornitori di turbine TPI Composites e Siemens Gamesa (SGRE) stanno monitorando attentamente i suoi progressi.
Se la tecnica CNF dei ricercatori può essere dimostrata con successo, potrebbe convincere SGRE e TPI ad applicarla all’interno di applicazioni per uso finale. Allo stesso modo, anche Ingersoll Machine Tools e il compoundatore di materiali Techmer PM stanno collaborando al programma, poiché il team di ricerca cerca di rendere il loro approccio più scalabile.
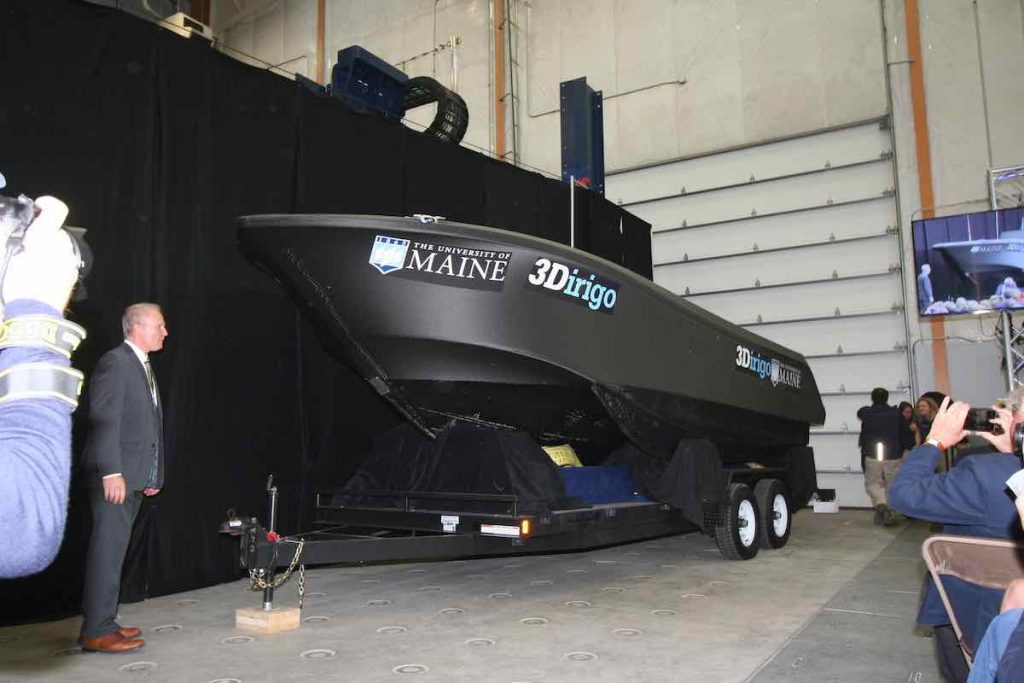