I ricercatori hanno utilizzato la diffrazione dei raggi X ad alta velocità per identificare le strutture cristalline che si formano all’interno dell’acciaio mentre viene stampato in 3D. L’angolo con cui i raggi X escono dal metallo corrisponde ai tipi di strutture cristalline all’interno.
Credito: H. König et al. via Creative Commons ( https://creativecommons.org/licenses/by/4.0 ), adattato da N. Hanacek/NIST
I ricercatori non hanno ancora trasformato completamente la produzione additiva, o la stampa 3D, dei metalli in una scienza. Le lacune nella nostra comprensione di ciò che accade all’interno del metallo durante il processo hanno reso i risultati incoerenti. Ma una nuova svolta potrebbe garantire un livello senza precedenti di padronanza della stampa 3D in metallo.
Utilizzando due diverse strutture di accelerazione di particelle, i ricercatori del National Institute of Standards and Technology (NIST), del KTH Royal Institute of Technology in Svezia e di altre istituzioni hanno scrutato la struttura interna dell’acciaio mentre veniva fuso e poi solidificato durante la stampa 3D. I risultati, pubblicati su Acta Materialia , sbloccano uno strumento computazionale per i professionisti della stampa 3D, offrendo loro una maggiore capacità di prevedere e controllare le caratteristiche delle parti stampate, migliorando potenzialmente la coerenza e la fattibilità della tecnologia per la produzione su larga scala.
Un approccio comune per la stampa di pezzi metallici prevede essenzialmente la saldatura di pool di metallo in polvere con laser, strato dopo strato, nella forma desiderata. Durante le prime fasi della stampa con una lega metallica, in cui il materiale si riscalda e si raffredda rapidamente, i suoi atomi – che possono essere un’infarinatura di elementi diversi – si raggruppano in formazioni cristalline ordinate. I cristalli determinano le proprietà, come tenacità e resistenza alla corrosione, della parte stampata. Possono emergere diverse strutture cristalline, ciascuna con i propri pro e contro.
“Fondamentalmente, se siamo in grado di controllare la microstruttura durante le fasi iniziali del processo di stampa, allora possiamo ottenere i cristalli desiderati e, in definitiva, determinare le prestazioni delle parti prodotte in modo additivo”, ha affermato Fan Zhang, fisico del NIST, coautore dello studio.
Mentre il processo di stampa spreca meno materiale e può essere utilizzato per produrre forme più complicate rispetto ai metodi di produzione tradizionali, i ricercatori hanno faticato a capire come indirizzare il metallo verso particolari tipi di cristalli rispetto ad altri.
Questa mancanza di conoscenza ha portato a risultati poco desiderabili, come parti con forme complesse che si incrinano prematuramente grazie alla loro struttura cristallina.
“Tra le migliaia di leghe comunemente prodotte, solo una manciata può essere realizzata utilizzando la produzione additiva”, ha affermato Zhang.
Stampa 3D con laser e polvere di metallo
Una stampante 3D del tipo laser powder-bed fusion, in azione. La fusione laser a letto di polvere aggiunge strati successivi di polvere metallica e quindi utilizza un laser per fondere ogni strato in posizione sulla parte che viene creata.
Parte della sfida per gli scienziati è stata che la solidificazione durante la stampa 3D in metallo avviene in un batter d’occhio.
Per catturare il fenomeno dell’alta velocità, gli autori del nuovo studio hanno utilizzato potenti raggi X generati da acceleratori di particelle cicliche, chiamati sincrotroni, presso l’Advanced Photon Source dell’Argonne National Laboratory e la Swiss Light Source del Paul Scherrer Institute .
Il team ha cercato di capire come le velocità di raffreddamento del metallo, che possono essere controllate dalla potenza del laser e dalle impostazioni di movimento, influenzano la struttura del cristallo. Quindi i ricercatori confronteranno i dati con le previsioni di un modello computazionale ampiamente utilizzato sviluppato negli anni ’80 che descrive la solidificazione delle leghe.
Sebbene il modello sia affidabile per i processi di produzione tradizionali, la giuria si è espressa sulla sua applicabilità nel contesto unico dei rapidi sbalzi di temperatura della stampa 3D.
“Gli esperimenti di sincrotrone richiedono tempo e denaro, quindi non puoi eseguirli per ogni condizione che ti interessa. Ma sono molto utili per convalidare modelli che puoi utilizzare per simulare le condizioni interessanti”, ha affermato la coautrice dello studio Greta Lindwall, professore associato di scienza dei materiali e ingegneria presso il KTH Royal Institute of Technology.
All’interno dei sincrotroni, gli autori hanno stabilito condizioni di produzione additiva per l’acciaio per utensili per lavorazione a caldo, un tipo di metallo utilizzato per realizzare, come suggerisce il nome, strumenti in grado di resistere alle alte temperature.
Quando i laser hanno liquefatto il metallo e sono emersi diversi cristalli, i raggi X hanno sondato i campioni con energia e velocità sufficienti per produrre immagini del processo fugace. I membri del team avevano bisogno di due strutture separate per supportare le velocità di raffreddamento che volevano testare, che andavano da temperature di decine di migliaia a più di un milione di kelvin al secondo.
I dati raccolti dai ricercatori hanno raffigurato il tira e molla tra due tipi di strutture cristalline, l’austenite e la ferrite delta, quest’ultima associata alla rottura delle parti stampate. Poiché le velocità di raffreddamento hanno superato 1,5 milioni di kelvin (2,7 milioni di gradi Fahrenheit) al secondo, l’austenite ha iniziato a dominare il suo rivale. Questa soglia critica era in linea con quanto previsto dal modello.
“Il modello ei dati sperimentali sono perfettamente d’accordo. Quando abbiamo visto i risultati, eravamo davvero entusiasti”, ha detto Zhang.
Il modello è stato a lungo uno strumento affidabile per la progettazione dei materiali nella produzione tradizionale e ora lo spazio della stampa 3D può ricevere lo stesso supporto.
I risultati indicano che il modello può informare scienziati e ingegneri su quali velocità di raffreddamento selezionare per le prime fasi di solidificazione del processo di stampa. In questo modo la struttura cristallina ottimale apparirebbe all’interno del materiale desiderato, rendendo la stampa 3D in metallo meno un tiro di dadi.
“Se disponiamo di dati, possiamo usarli per convalidare i modelli. È così che acceleri l’adozione diffusa della produzione additiva per uso industriale “, ha affermato Zhang.
Carta: H. König, NH Pettersson, A. Durga, SV Petegem, D. Grolimund, AC Chuang, Q. Guo, L. Chen, C. Oikonomou, F. Zhang e G. Lindwall. Modalità di solidificazione durante la produzione additiva dell’acciaio rivelate dalla diffrazione dei raggi X ad alta velocità. Acta Materialia. Pubblicato online il 23 gennaio 2023. DOI:
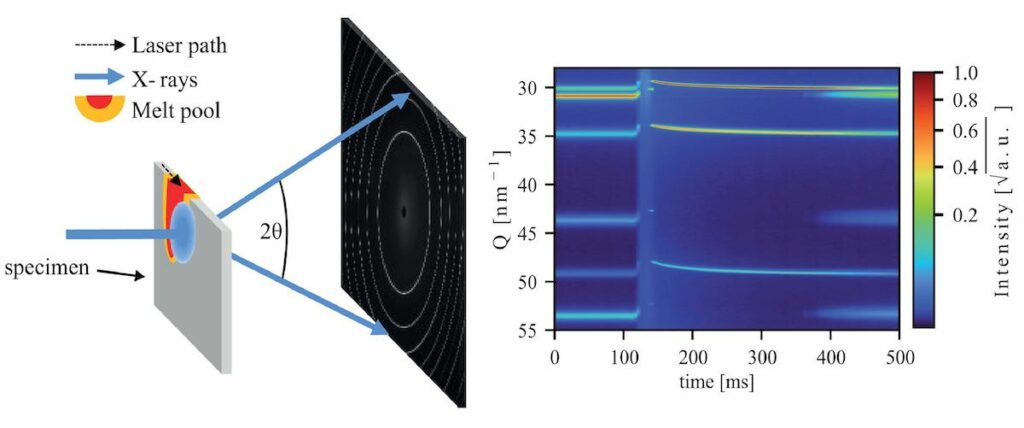
L’angolo con cui i raggi X escono dal metallo corrisponde ai tipi di strutture cristalline all’interno.
Credito: H. König et al.
via Creative Commons adattato da N. Hanacek/NIST