L’Istituto tedesco di ricerca sui materiali del DLR ha aperto nuove strade nella stampa 3D di sistemi propulsivi spaziali.
Nell’epoca moderna, l’interesse per il business spaziale e l’esplorazione ha visto una crescita significativa. La chiave di questa trasformazione è stata l’innovazione nella riusabilità dei razzi, un concetto portato avanti da SpaceX. Prima di questo, l’uso e il getto dei razzi rendevano l’accesso allo spazio proibitivo e limitato ai paesi più ricchi. La tecnologia dei razzi riutilizzabili ha cambiato la situazione, permettendo a più attori di entrare in gioco.
Ora, le imprese aerospaziali globali stanno velocemente sviluppando razzi riutilizzabili con diversi gradi di successo.
Uno degli elementi cruciali di questo nuovo approccio è la produzione additiva o stampa 3D. Ci sono molti vantaggi nell’uso di motori a razzo stampati in 3D, tra cui la riduzione del peso. La produzione in un’unica parte diminuisce la necessità di componenti aggiuntivi come bulloni e dadi, riducendo i punti di potenziale fallimento e migliorando la affidabilità.
Ma come si realizza precisamente un motore a razzo stampato in 3D?
Stampare qualsiasi oggetto metallico in 3D è un’operazione complessa, che richiede l’ottimizzazione di vari parametri. È particolarmente critico per i motori a razzo che devono essere efficienti e riutilizzabili.
Ecco dove entra in gioco il DLR. Hanno avviato un progetto, “3D-LoCoS” (Stampa 3D per Componenti Spaziali a Basso Costo), per svelare i segreti della stampa 3D di componenti spaziali.
Jan Haubrich, a capo del progetto DLR, illustra:
“I nuovi metodi di produzione possono elevare le prestazioni, abbassare i costi, e aprire la strada ai sistemi di lancio riutilizzabili. La stampa 3D, una tecnologia relativamente recente, permette un approccio completamente nuovo alla produzione di componenti, soprattutto per progetti complessi, rendendola più rapida ed economica.”
Come esempio, hanno creato un nuovo design per una camera di combustione in rame utilizzando un processo LBPF, che include un sistema di raffreddamento innovativo. Hanno condotto sei test a caldo su questo progetto nel loro banco di prova a Lampoldshausen, in Germania.
Questi test determineranno se il design è realmente riutilizzabile. Le tecniche sviluppate dal DLR potrebbero in futuro trovare applicazione nella produzione commerciale, contribuendo a plasmare i futuri lanci di razzi.
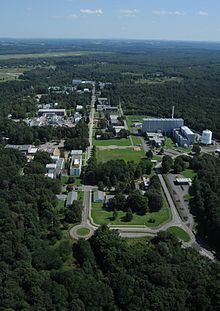