SQ25W: il nuovo robot di Q5D per automatizzare la produzione dei cablaggi nei veicoli
L’azienda britannica Q5D Technology, con sede a Bristol, ha sviluppato un sistema robotico pensato per trasformare il modo in cui vengono realizzati i cablaggi nei veicoli. Il robot, chiamato SQ25W, è progettato per automatizzare una delle fasi più complesse e ancora manuali dell’assemblaggio automobilistico: la posa dei fili elettrici su componenti tridimensionali già formati, come il cielo dell’auto (la parte interna del tetto) o le ali di un drone.
Pur non costruendo l’intero cablaggio da zero, il sistema è in grado di integrare fili isolati direttamente su superfici complesse già stampate in 3D, eliminando la necessità di supporti, clip o legature aggiuntive. Il processo si svolge in modo completamente digitale e automatizzato, permettendo un notevole risparmio in termini di tempo e costi.
Una possibile riduzione dei costi per unità fino a 200 dollari
Secondo le stime fornite da Q5D, l’impiego del robot SQ25W potrebbe abbattere i costi di produzione di circa 200 dollari per veicolo. In un’industria in cui i volumi di produzione si misurano in milioni di unità, anche un risparmio apparentemente contenuto per singolo veicolo può generare benefici economici su scala industriale.
Oltre al risparmio economico, la tecnologia mira a migliorare l’affidabilità e la coerenza del montaggio dei cablaggi, riducendo gli errori dovuti al lavoro manuale e facilitando il controllo qualità.
Il cablaggio: un componente essenziale e ancora realizzato per lo più a mano
Il cabling harness (fascio di cablaggi) è un elemento cruciale in ogni veicolo moderno. Conduce l’elettricità e i segnali elettronici tra le varie unità di controllo e dispositivi: luci, sensori, cruscotto, altoparlanti, e molti altri elementi. La complessità dei cablaggi, che varia da modello a modello, ha reso difficile l’automazione della loro produzione.
Attualmente, tra il 70% e il 90% dei cablaggi viene ancora assemblato manualmente. Il lavoro è lento, richiede alta precisione e può essere soggetto a errori. Inoltre, i costi di manodopera sono elevati, motivo per cui molte aziende del settore delegano la produzione a paesi in cui la manodopera è più economica. Tuttavia, questa strategia espone la catena di fornitura a rischi logistici, come ritardi o interruzioni.
SQ25W: progettato per integrare fili su componenti complessi in 3D
Il robot sviluppato da Q5D non solo gestisce la posa dei cavi, ma li deposita direttamente su pezzi tridimensionali di grandi dimensioni, come i rivestimenti interni del tetto, che possono includere microfoni, luci, sensori e anche dispositivi per la sicurezza come gli airbag.
Il sistema funziona all’interno di una cella a portale e legge direttamente i modelli digitali dei pezzi, seguendo le istruzioni attraverso un’interfaccia touch. Il robot è in grado di muoversi a quattro metri al secondo, con una velocità di posa del filo pari a un metro al secondo, il doppio rispetto alle generazioni precedenti sviluppate da Q5D.
Con un volume operativo di 2,5 metri di lunghezza, 1,5 metri di larghezza e 15 cm di altezza, il sistema è sufficientemente ampio da lavorare su componenti di dimensioni reali, come un intero headliner. Il robot fissa i fili isolati direttamente sulle superfici, li collega ai connettori previsti e sostituisce gli elementi di fissaggio tradizionali, ottimizzando così peso, ingombro e tempi di montaggio.
Versatilità di applicazione oltre il settore automobilistico
La tecnologia sviluppata da Q5D non si limita al mondo dell’auto. Il robot può essere impiegato anche per droni, aerei e altri componenti con geometrie complesse, nei quali l’installazione manuale dei fili è spesso complicata da curvature, superfici irregolari o requisiti di miniaturizzazione.
Questa flessibilità apre nuove opportunità nei settori aerospaziale e della difesa, così come nella robotica e nei dispositivi industriali avanzati.
Collaborazione diretta con costruttori e fornitori automotive
Simon Baggott, responsabile marketing di Q5D, ha spiegato che il sistema SQ25W è stato sviluppato in risposta a esigenze dirette espresse da quattro tra i principali costruttori automobilistici mondiali, oltre che da diversi fornitori Tier 1.
Queste aziende stanno puntando su automazione dei processi, produzione localizzata (onshoring) e riduzione dei costi. Il robot risponde a tutte queste priorità, offrendo anche la possibilità di essere integrato nei cicli produttivi esistenti, senza dover rivoluzionare completamente le linee di assemblaggio.
Tempistiche e prospettive di adozione
Il telaio principale del robot è già stato consegnato presso la sede di Q5D a Bristol, dove è in corso la fase finale di assemblaggio. La messa in funzione è prevista per la fine della primavera del 2025.
Una volta completato, i produttori potranno testare direttamente il robot, utilizzando i propri componenti presso il centro tecnico di Q5D. Questo passaggio consente alle aziende di valutare le performance su casi concreti, prima di decidere un’eventuale implementazione su scala industriale.
Modularità e scalabilità per le esigenze future
Uno degli aspetti distintivi del progetto è la modularità del sistema. Il robot può essere ampliato, ad esempio prolungando l’asse X, oppure configurato in versioni specializzate per esigenze specifiche. Questa flessibilità rende più semplice l’inserimento del sistema nei siti produttivi esistenti, riducendo i tempi e i costi di adattamento.
Se le promesse saranno mantenute, l’adozione di questa tecnologia potrebbe cambiare il modo in cui i cablaggi vengono realizzati nei veicoli del prossimo decennio, rendendo il processo più efficiente, tracciabile e meno dipendente dal lavoro manuale.
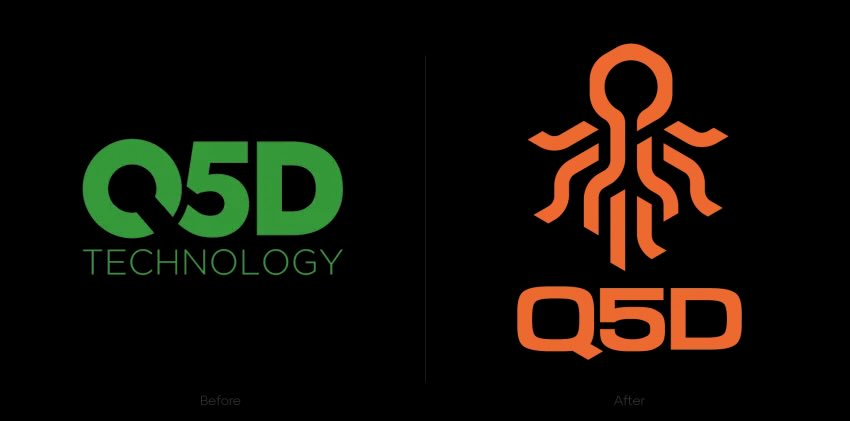