Ricercatori internazionali hanno eseguito quello che potrebbe essere un lavoro molto importante in relazione ai farmaci stampati in 3D, con le loro scoperte delineate nelle ” Materie idrofiliche stampate 3D senza plastificazione ” : Texture superficiale quantitativa 3D, meccanica, gonfiore, erosione, rilascio di farmaci e Studi farmacocinetici . “
Il focus del loro studio è l’idrossipropilmetilcellulosa (HPMC), un polimero idrofilo che potrebbe avere un enorme potenziale per la fabbricazione di compresse a matrice. Qui, il team di ricerca ha analizzato matrici idrofiliche stampate in 3D prive di plastificanti con filamenti caricati con farmaci, esaminando il loro livello di prestazioni in entrambe le applicazioni in vitro e in vivo .
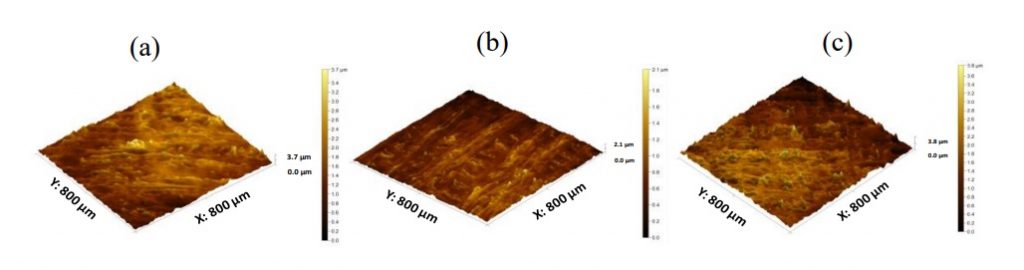
E mentre le aziende farmaceutiche di tutto il mondo potrebbero già essere in grado di produrre farmaci nella dose e forma adeguate, a volte in modo economico, con la stampa 3D possono offrire ai pazienti ciò che è innegabilmente il futuro della medicina con un trattamento specifico per il paziente. Questo è già stato documentato con l’ approvazione della FDA di Spritam , il primo farmaco per l’epilessia stampato in 3D, e molte discussioni su come tale tecnologia verrà sfruttata in futuro con il potenziale per i farmaci fai- da- te .
“Sebbene i metodi attuali siano comuni e convenienti, offrono poche opportunità di personalizzazione e produzione on-demand in quanto il cambiamento delle dimensioni, della forma e della dose di un tablet richiede modifiche in ogni fase di produzione e riattrezzamento delle macchine tablet”, ha affermato ricercatori. “Di conseguenza, è necessaria una tecnologia in grado di produrre forme di dosaggio con una varietà di punti di forza, come la stampa tridimensionale (3D), per soddisfare le esigenze terapeutiche personalizzate degli individui”.
Precedenti ricercatori hanno provato a creare farmaci stampati in 3D usando una varietà di filamenti diversi e con diversi materiali compositi e hardware. I polimeri sono una scelta estremamente comune per tali farmaci, con combinazioni come i plastificanti utilizzati per rendere l’estrusione più facile. Tali aggiunte potrebbero tuttavia influenzare negativamente l’assorbimento del farmaco. Per la stampa 3D tramite FDM, i materiali devono essere resistenti e “meccanicamente robusti” abbastanza da sopportare il processo di fabbricazione. Potrebbero sorgere problemi con la linea di giunzione e problemi con troppa porosità. Per compensare gli ostacoli precedentemente noti, il team di ricerca ha evitato l’uso di plastificanti. Hanno anche testato e valutato la tessitura superficiale, impiegando sia la porosimetria per intrusione di mercurio che la profilometria ottica a luce bianca.
“Glipizide, un farmaco antidiabetico della classe sulfonilurea indicato per il trattamento del diabete di tipo 2, è stato utilizzato come farmaco modello. Glipizide è un acido debole (pKa = 5,9), praticamente insolubile in acqua e acido, ed è altamente permeabile (sistema di classificazione biofarmaceutica, BCS II) “, hanno affermato i ricercatori. “Sembra essere un secretagogo dell’insulina efficace che raggiunge un picco di concentrazione plasmatica entro 1-3 ore dopo una singola dose orale con un’emivita di eliminazione di circa 2-4 ore. Tali farmaci rapidamente assorbiti con tassi di eliminazione rapidi con breve tempo di dimezzamento ne fanno un candidato adatto da considerare per una somministrazione sostenuta. “
Il team di ricerca ha avuto successo nella stampa 3D dei materiali HPMC senza utilizzare il plastificante.
“Nel complesso, gli spettri XRD di glipizide e di filamenti HPMC caricati con farmaci erano coerenti con i profili DSC, quindi entrambi i metodi hanno mostrato che glipizide ha una struttura cristallina, mentre i filamenti HPMC e drogati hanno natura amorfa. Ciò potrebbe potenzialmente migliorare la dissoluzione ma potrebbe avere un impatto negativo sulla stabilità “, hanno affermato i ricercatori.
In definitiva, i filamenti caricati producevano matrici idrofiliche stampate in 3D che erano tutte simili per spessore, diametro e peso; tuttavia, le superfici stampate in 3D sono risultate “considerevolmente più ruvide”.
“… si può concludere che la viscosità di HPMC ha un notevole impatto del gonfiore, dell’erosione, della dissoluzione di HPMC, del rilascio di farmaci e delle proprietà farmacocinetiche. Il grado di viscosità più elevato (K100M) tende ad avere un grado maggiore di gonfiore, riduzione della dissoluzione dell’HPMC, erosione bassa della matrice, diminuzione del rilascio di farmaco e profilo di assorbimento prolungato del farmaco “, hanno affermato i ricercatori. “Complessivamente, questo studio ha confermato la riuscita della fabbricazione di compresse a matrice di stampati 3D che hanno funzionalità analoghe alle tavolette a matrice fabbricate usando tecnologie convenzionali. Inoltre, l’attuale studio ha anche dimostrato l’utilità della tecnica FDM, fornendo una soluzione semplice per sviluppare formulazioni farmaceutiche personalizzate in un modo economico ed efficiente affrontando le sfide poste dai processi di produzione convenzionali. “