Gli ingegneri del Lawrence Livermore National Laboratory (LLNL) hanno sviluppato un modo per ottimizzare le proprietà di qualsiasi parte prodotta tramite la stampa 3D Liquid Metal Jet (LMJ).
Invece di adottare un costoso approccio basato sulla videografia ad alta velocità, il team LLNL ha escogitato un mezzo per combinare il rilevamento del campo vicino con la simulazione, per concentrarsi su un solo parametro durante l’analisi dei materiali a getto. Sfruttando la loro metodologia, i ricercatori affermano che è possibile identificare le cause dei problemi degli ugelli in tempo reale, prima di regolare le impostazioni di una stampante per “garantire la qualità delle parti”.
“I nostri risultati dimostrano che il monitoraggio in situ di LMJ è possibile con metodi di rilevamento a onde millimetriche”, ha affermato l’autore principale dello studio Tammy Chang. “Questo è entusiasmante perché significa che potremmo sostituire la diagnostica ottica ad alta velocità e ad alta risoluzione computazionalmente costosa per consentire la valutazione delle prestazioni in tempo reale e il controllo del feedback, per garantire parti metalliche stampate di alta qualità”.
Diagnosi dei problemi di LMJ in situ
“Liquid Metal Jetting” descrive un processo in cui minuscole goccioline di metallo vengono sparate ad alta velocità da un ugello, per formare strati che possono essere accumulati in parti omogenee, in un approccio simile a quello delle stampanti a getto d’inchiostro. Rispetto ai sistemi basati su laser, tuttavia, le macchine LMJ non richiedono l’uso di polveri metalliche pericolose, quindi offrono potenzialmente un mezzo più sicuro per raggiungere gli stessi obiettivi.
Poiché la tecnologia ha continuato a trovare nuove applicazioni, anche le sue prestazioni sono state oggetto di un esame più approfondito e l’individuazione di set di parametri ottimali si è rivelata difficile in determinate applicazioni. Ciò è in gran parte dovuto al fatto che i materiali a getto possono essere influenzati da una moltitudine di fattori, che vanno dalla dimensione delle gocce e dalla tempistica del getto, alla velocità, alla portata e alla temperatura.
Mentre la videografia ad alta velocità viene spesso utilizzata per analizzare LMJ in azione, l’approccio può essere utilizzato solo per pochi secondi, poiché a causa delle restrizioni di elaborazione, i grandi volumi di dati richiedono giorni per essere esaminati. Per rendere più plausibile l’analisi in tempo reale, il team LLNL ha quindi sviluppato un approccio scalabile, che si basa più sulla simulazione che sull’acquisizione di gigabyte di informazioni.
Configurazione diagnostica del getto di materiale sperimentale del team LLNL. Immagine tramite il Journal of Applied Physics.
Monitoraggio LMJ pronto in fabbrica?
L’approccio diagnostico rivisto dagli ingegneri prevede il posizionamento di una guida d’onda aperta perpendicolare a una stampante durante la produzione, in modo che eventuali goccioline a getto passino attraverso il campo elettromagnetico della sua apertura. In tal modo, è possibile catturare la dinamica delle goccioline di metallo in situ, in un modo che richiede la raccolta di molti meno dati di quelli necessari quando si utilizza la sola analisi video.
Per mettere in pratica il loro metodo, il team LLNL ha inserito una guida d’onda in alluminio nella camera di costruzione di una stampante 3D LMJ e ha installato telecamere ai lati opposti del sistema per acquisire i risultati. È interessante notare che, concentrandosi su un parametro alla volta, i ricercatori sono stati in grado di accumulare dati sufficienti per ottenere affascinanti informazioni sul comportamento delle goccioline tramite simulazioni elettromagnetiche.
Durante il getto, ad esempio, il team è stato in grado di identificare in modo non invasivo l’impatto preciso che la distanza e il diametro delle gocce hanno sulle proprietà degli strati stampati. Attraverso un’ulteriore valutazione dei loro dati, gli ingegneri sono stati anche in grado di trovare il motivo dietro un ugello di stampa intasato che si è verificato nel loro esperimento, poiché c’era una “variazione osservabile” nelle lunghezze d’onda catturate quando si è verificata.
Come si è scoperto, sulla superficie dell’ugello si era accumulata una tensione che ha impedito al materiale di essere sparato e ha fatto sì che la goccia si attaccasse in posizione fino a quando l’impulso successivo della stampante non la espelleva. Se implementato all’interno di un ambiente di fabbrica, i ricercatori ritengono quindi che il loro approccio potrebbe essere utilizzato per determinare la qualità delle gocce depositate in tempo reale, consentendo ai produttori di ridurre al minimo gli errori di stampa.
“Ottenere un’espulsione pulita di una singola goccia che cade verso il basso è la chiave per ottenere una buona qualità di stampa”, ha concluso il coautore dello studio Andy Pascall. “La videografia ad alta velocità funziona bene in un ambiente su scala di laboratorio in cui stiamo testando nuovi parametri di stampa, ma non funzionerà mai in produzione. Questo tipo di diagnostica sarà molto utile in un ambiente di produzione”.
Mentre lo strumento diagnostico LLNL è attualmente in grado di rilevare caratteristiche fino a una dimensione di 400-500 μm, il team afferma che la frequenza della loro configurazione potrebbe essere aumentata in futuro per consentire il monitoraggio di gocce da 50-100 μm. In alternativa, utilizzando altri metodi di elaborazione del segnale, potrebbe anche essere possibile trasformarlo in un sistema a circuito chiuso, in cui i dati possono essere utilizzati per regolare al volo i parametri di stampa.
Come molti processi di produzione avanzati, la stampa 3D a getto di materiale è oggetto di costante ricerca e sviluppo, in cui gli ingegneri stanno tentando di affinare le sue capacità di produzione di massa. Detto questo, sarebbe un errore pensare che la tecnologia non abbia già trovato applicazioni per l’uso finale, poiché diverse aziende del settore ora commercializzano tecnologie che potrebbero essere giustamente chiamate “material jetting”.
Stratasys , ad esempio, continua a fare progressi significativi con la sua tecnologia Polyjet e ha scelto di lanciare il desktop J35 Pro all’inizio di quest’anno. Progettato per rendere accessibile il processo di getto di materiale dell’azienda a coloro che lavorano in un ufficio, il sistema è ideale per la prototipazione di beni di consumo ed elettronici, nonché per applicazioni accademiche.
Con Multi Jet Fusion (MJF), HP ha sviluppato un’altra tecnologia di getto di materiale ben nota, adottata dai fornitori di stampa 3D di tutto il mondo. Inoltre, poiché la compatibilità delle sue macchine si è ampliata, così anche le loro applicazioni, e aziende come Materialise hanno già lanciato materiali dedicati progettati per sbloccare il potenziale dei sistemi HP.
Altrove, lo specialista del getto di materiale XJet ha trovato applicazioni dentali per uso finale per la sua stampante 3D Carmel 1400 compatibile con la ceramica , tramite una collaborazione con Straumann . Si dice che l’elevata produttività del sistema e la compatibilità del supporto solubile siano vantaggiose per l’azienda, in quanto i suoi professionisti del settore dentale sono ora in grado di trascorrere più tempo con i pazienti, poiché non devono preoccuparsi delle parti stampate post-elaborazione.
I risultati dei ricercatori sono dettagliati nel loro articolo intitolato ” Monitoraggio elettromagnetico a onde millimetriche per la stampa su richiesta di gocce di metallo liquido “, che è stato co-autore di T. Changa, S. Mukherjee, NN Watkins, E. Benavidez, AM Gilmore , AJ Pascall e DM Stobbe.
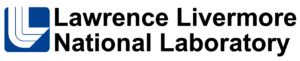