Intervista: come Briggs Automotive Company ha riprogettato una supercar con design generativo e stampa 3D
“Riesco a vederlo stampato in 3D ogni componente metallico dell’auto.”
Parcheggiato vicino alle banchine bagnate dalla pioggia di Liverpool sotto un lunatico cielo grigio e l’occhio vigile di Liver Birds, il BAC Mono sembra che avrebbe potuto essere guidato direttamente da un pannello di Gotham City – non un parco industriale di Speke a meno di 10 miglia su per la strada.
Proprio come quello sfondo non convenzionale, tipicamente nord dell’Inghilterra, che si fonde senza sforzo con l’estetica nera e argento della Mono, questa supercar monoposto non è interessata alla banale funzionalità del tipico set di quattro ruote. No, questo veicolo, come ha recentemente dichiarato alla TCT il cofondatore della Briggs Automotive Company (BAC) e direttore dello sviluppo prodotto, Ian Briggs, è stato progettato esclusivamente per lo sport della guida.
“Non dobbiamo pensare ad altre funzioni per questo prodotto oltre a, un ragazzo ci entrerà e vuole solo guidare, non vuole nemmeno andare da nessuna parte”, dice Briggs della nicchia del Mono demografico; il tipo di cliente che potrebbe già avere una mezza dozzina di hypercar nascosti nel proprio garage. “Per noi, è un obiettivo focalizzato molto semplice ed è quello di ridurre il peso, aumentare la potenza, portare la massa verso il centro del veicolo, ridurre la massa il più basso possibile”
Basandosi sul DNA di design visto per la prima volta sulla Mono R dell’azienda lo scorso anno, la nuova Mono è più leggera del suo predecessore e vanta una performance più elevata di 332 CV grazie a un motore turbo a quattro cilindri da 2,3 litri e oltre 400 Nm di coppia. Con un breve set di design per rendere l’auto “visivamente più leggera, più pulita e più semplicistica”, ciascun pannello della carrozzeria, tutto riprogettato per ridurre la massa visiva, presenta una fibra di carbonio con grafene per ridurre il peso e migliorare la resistenza.
L’argomento del peso è qualcosa su cui BAC si è concentrato in una partnership in corso con lo sviluppatore di software Autodesk dal 2014; se hai mai partecipato a un evento dell’Autodesk University di Londra , avrai probabilmente visto fuori una generazione di Mono parcheggiata all’esterno, di solito circondata da appassionati appassionati di selfie. Il prodotto più recente di questa collaborazione si trova nei cerchi in lega della nuova Mono, che sono stati genericamente progettati per accelerare il processo di iterazione e ridurre il peso, offrendo grandi vantaggi in termini di accelerazione e prestazioni.
“Il posto migliore per risparmiare peso sull’auto è la gomma. Il prossimo posto migliore è la ruota “, ha detto Briggs, spiegando il processo di pensiero dietro l’ultima iterazione del Mono. “Ma dato che la Mono è stata abbastanza ottimizzata in questo senso, abbiamo preso un foglio pulito, guardato tutto e iniziato con la parte più importante che è stata sviluppare un nuovo pneumatico con Pirelli. La prossima è stata la nostra ruota in carbonio. Vogliamo risparmiare peso sul cerchione anziché al centro della ruota inizialmente, ma una volta che hai ottenuto tutto il peso dal cerchione, allora vogliamo iniziare a concentrarci sul design dei raggi, ottenendo così tanto peso da possibile.”
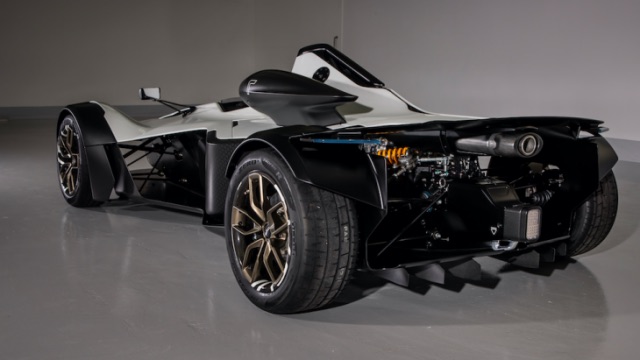
Il team ha collaborato con Autodesk Research per determinare come applicare il design generativo in Fusion 360 per esplorare rapidamente i risultati del progetto, tenendo conto dei criteri di prestazione del mondo reale, dei dati di test degli standard del produttore di ruote britannico Dymag (precedentemente utilizzato per produrre e certificare altri modelli BAC per uso su strada), metodi e materiali di fabbricazione ed estetica distintiva di BAC.
“Potremmo subito, nel giro di poche ore, vedere la versione più ottimizzata di quella ruota. Quindi possiamo tornare da quello e decidere se vogliamo andare a quel livello di complessità. Vogliamo semplificarlo? Il dipartimento di progettazione ha qualcosa da dire su come appare? ” Spiegò Briggs. “Potremmo in qualche modo tornare su di esso piuttosto che lavorare dall’altra direzione da dove inizi, fai sempre passi verso piccoli miglioramenti ogni volta e poi decidi solo per quanto tempo continui a seguire quel processo.”
A partire dalle esigenze prestazionali chiave e dai vincoli di produzione in mente, questa tecnica consente quasi agli ingegneri di lavorare all’indietro piuttosto che passare attraverso un ampio processo di iterazione per raggiungere il risultato ottimale. È un metodo che è già stato implementato nel settore automobilistico da artisti del calibro di General Motors per ridisegnare una staffa del sedile con una riduzione del peso del 40% , seguita da Volkswagen, che lo scorso anno ha usato il generativo per reinventare parti di un microbus classico del 1962 . Parlando dei vantaggi della progettazione generativa e del coinvolgimento di Autodesk nel progetto BAC, Andy Harris di Autodesk Research ha dichiarato:
“Se guardi al modo tradizionale di progettazione di un ingegnere, si concentreranno forse su uno, due, tre progetti che soddisfano i requisiti, mentre con il design generativo, quello che stiamo cercando di fare è ottenere il computer per progettare effettivamente una vasta gamma di progetti che è possibile esplorare e quindi scegliere. Ciò che abbiamo fatto in modo molto diverso con BAC, che è molto interessante per me dal punto di vista della ricerca, è dove normalmente guarderemmo le prestazioni, la massa e il costo, che il design generativo come prodotto ci dà, volevamo anche esplorare l’estetica come una quarta dimensione. Quindi, con molte indicazioni di BAC sull’identità del marchio e sul tipo di estetica che il design finale doveva avere,
Sono stati testati diversi metodi di produzione e la fresatura CNC in alluminio è stata infine identificata come l’opzione migliore con il team che va dalla fresatura a 3 assi a 5 assi presso il Technology Center di Birmingham con sede ad Autodesk . Il risultato è stato una lega di cerchi da 2,2 kg riprogettata, rifinita con il “grigio canna di fucile” firmato BAC, più leggero del 35% e conforme alle rigide normative strutturali europee. Il peso totale della ruota è ora di 4,7 kg per le ruote anteriori e di 4,9 kg per la parte posteriore, compresi i cerchi in lega e in carbonio.
“In realtà [3D] abbiamo stampato tre ruote su una terza scala”, ha spiegato Ian. “Li abbiamo stampati in plastica e abbiamo detto che questo è quello attuale, questo è quello ottimizzato per la lavorazione a 3 assi, questo è l’ideale per la lavorazione a 5 assi e questo è l’ottimale se decidessimo di stampare la ruota. Ora posso vedere se faccio una macchina a 3 assi risparmiando solo circa 250 g, se faccio una macchina a 5 assi risparmio 1,2 kg e se la stampo in 3D, risparmio solo 1,5 kg. Ottieni molto rapidamente questa panoramica per dire, beh, è tutto ciò che è comunque possibile, ma ho appena aumentato il prezzo di 10 quando posso ottenere tre quarti di strada e avere ancora un prodotto conveniente. È un modo completamente diverso di capire fino a che punto puoi e dovresti andare. È stata una grande rivelazione. “
Andy ha aggiunto: “Ti aiuta davvero ad accelerare quella fase del concept design e abbiamo notato che con BAC, dove stavamo parlando di questo progetto verso la fine dello scorso anno, e nei primi due mesi abbiamo preparato il design per la produzione, che dal punto di vista dello sviluppo delle ruote è incredibilmente veloce. “
Non sono solo le ruote dove l’aggiunta della nuova tecnologia ha portato a una riduzione di peso. Il nuovo Mono pesa solo 570 kg grazie a una serie di miglioramenti apportati al grafene e alle parti prodotte in modo additivo per uso finale, quest’ultima delle quali è stata una sorpresa per Briggs. Le capacità di stampa 3D interne sono un’aggiunta abbastanza recente all’officina BAC a seguito di un incontro con la società globale di scienza e materiali DSM in cui una leva del freno per motocicletta stampata in 3D in fibra di carbonio Novamid CF con proprietà simili a quella dell’alluminio fuso ha contribuito a rendere “mentale balzo “, afferma Briggs, per vedere la stampa 3D come uno strumento di produzione. Ora, Mono ha installato circa 40 parti stampate in 3D per uso finale.
“Immediatamente riesco a vederlo [stampa 3D] su ogni componente metallico dell’auto”, afferma Briggs. “Ora abbiamo parti in plastica stampate in 3D che supportano cose come centraline elettroniche o addirittura cose come il cablaggio. L’auto ha un motore montato solido, non è possibile avere alcun cablaggio non supportato nell’auto, vibra e alla fine non funziona. Quindi ci impegniamo a supportare il cablaggio ovunque sull’auto in questi luoghi e ora realizziamo piccole parti stampate in 3D per farlo. ”
Mentre gran parte del precedente lavoro AM di BAC è stato affidato in outsourcing a fornitori di servizi del Regno Unito come Malcolm Nicholls , che l’anno scorso ha prodotto numerosi prototipi su RPS NEO 800 , il garage BAC ora ospita una stampante 3D desktop Ultimaker S5 con una camera di costruzione chiusa da 3DGBIRE , consentendo a BAC di sfruttare i polimeri ad alte prestazioni di DSM tramite il programma Material Alliance di Ultimaker . Oltre alla prototipazione e alla ricerca e sviluppo, quelle parti per uso finale, alcune delle quali sono state stampate con HP Multi Jet Fusion, include i bordi della luce anteriore e posteriore, i bracci degli specchietti e l’alloggiamento dello specchio, le cerniere del portellone anteriore, i componenti di ingresso del motore e altro; il tipo di parti era il costo di uno strumento per stampi ad iniezione, ma non sarebbe economico per volumi così bassi. Adam Mughal, capo progettista 3D della Briggs Automotive Company ha recentemente descritto come BAC è riuscita a far scendere il costo degli specchietti retrovisori dell’auto da 60 GPB a soli 10 GBP stampandoli in 3D in due parti. Questi volumi tuttavia si prestano bene alla personalizzazione e c’è la possibilità di utilizzare la stampa 3D per aggiungere funzionalità come targhette personalizzate o numeri di parte che sono personalizzati per il cliente.
Briggs afferma di ritenere che il termine “prototipazione rapida” in passato avesse “davvero sottovalutato la tecnologia [stampa 3D]”. Mentre avverte che la stampa 3D in metallo, anche per un prodotto di lusso che lavora a volumi estremamente bassi, non sarebbe il metodo più parsimonioso di produzione per qualcosa come le ruote della Mono, ritiene che ci possa essere un posto sulla Mono per l’additivo metallico accoppiato con un design generativo in futuro.
“Nel tempo, è qualcosa che vorremmo sicuramente esaminare”, afferma Briggs, suggerendo che un supporto in titanio per il sistema di scarico potrebbe essere un progetto di test interessante. “Posso immaginare molti dei componenti delle sospensioni, molti componenti dell’auto potrebbero essere stampati una volta che diventano accessibili e devo dire che, i nostri volumi bassi e i nostri prezzi elevati, siamo una delle prime aziende che possono adottare quei tipi di tecnologia perché possiamo permetterci un prezzo elevato in cambio della mancanza di costi di attrezzamento. “
Basandosi sulle rivoluzioni che stanno avvenendo altrove nell’industria automobilistica attraverso trasmissioni e veicoli autonomi, il modo in cui pensiamo alle auto mentre i trasporti sta cambiando. Lo stesso si può dire per le auto come prodotto di lusso. I loro clienti, come BAC, sono costantemente alla ricerca della perfezione e delle ultime novità. Briggs ricorda di aver dimostrato il nuovo design delle ruote a un cliente rimasto sbalordito nel rendersi conto di poterlo raccogliere facilmente come un bicchiere d’acqua. “A loro piace essere spazzati via da tutto ciò”, aggiunge.
Briggs afferma che il team ha in mente una tabella di marcia su come potrebbe essere l’auto nei modelli futuri e mentre il design generativo è solo una piccola parte dello stile di Mono oggi, date le sue qualità strutturali ed estetiche uniche, che potrebbe non essere il caso a lungo.
“Ci sono molte rivoluzioni in arrivo nel settore automobilistico, e con un design generativo, per cambiare il modo in cui le auto sono progettate, progettate, costruite e fatte apparire. È un momento super emozionante nel settore automobilistico […] è un periodo impegnativo ma penso che sia super emozionante. ”