PARTIAL HAND SOLUTIONS UTILIZZA LA STAMPANTE 3D FUSE 1 PER CREARE PROTESI PEDIATRICHE
Il produttore di protesi avanzate Partial Hand Solutions (PHS) ha sfruttato la nuova stampante 3D Form 1 di Formlabs per ottimizzare il processo di produzione degli arti artificiali.
Invece di esternalizzare la produzione dei suoi impianti pediatrici M-Finger e Elbow a un’azienda di stampaggio a iniezione, PHS ora utilizza la Form 1 per creare internamente protesi specifiche per il paziente. Passando al sistema lanciato di recente da Formlabs, l’azienda è riuscita a stampare in 3D parti in nylon più durevoli in modo conveniente, riducendo i tempi di consegna da due settimane a solo un paio di giorni.
“Aspettare due giorni per una piattaforma di stampa completa di stampanti è spazzato via le settimane in cui attendevo l’arrivo delle parti per stampaggio a iniezione”, ha affermato Matthew Mikosz, fondatore di Partial Hand Solutions. “L’utilizzo di Fuse 1 ha ampliato i miei orizzonti. Ora sto pensando a come migliorare il mio lavoro e creare migliori risultati per i pazienti “.
Dal 2007, PHS ha lavorato per spingere i confini della tecnologia per gli amputati e creare protesi con nuove funzionalità per coloro che hanno amputazioni parziali della mano. Dato che molti dei clienti dell’azienda sono soldati attivi o bambini con lesioni estese, considera anche la consegna rapida di impianti personalizzati di vitale importanza per la sua attività.
Tuttavia, esternalizzando la produzione, PHS è stata in grado di offrire i suoi prodotti solo in cinque dimensioni prestabilite, il che non ha tenuto conto delle esigenze dei pazienti o ha consentito loro di massimizzare la potenziale mobilità. Inoltre, l’azienda ha già eseguito prove di SLA, FDM e processi di stampaggio a iniezione, ma ha scoperto che i prodotti economici specifici per i pazienti rimanevano fuori portata.
In particolare, l’azienda ha visto il potenziale nelle parti in nylon stampate in 3D SLS, ma secondo Mikosz, i loro costi iniziali significavano che non erano raggiungibili fino a quando non è arrivato il Fuse 1. “Ho sempre desiderato una stampante SLS, ma sono irraggiungibili al loro prezzo attuale”, ha detto Mikosz. “Fuse 1 è perfetto per le piccole imprese.”
Adottando insieme Fuse 1 e Fuse Sift, Mikosz afferma che la sua azienda è stata in grado di stabilire un nuovo flusso di lavoro di produzione più efficiente. Ad esempio, l’utilizzo delle macchine Formlabs per produrre la protesi controllabile “M-Finger” ha consentito a PHS di ottenere una bassa frequenza di aggiornamento della polvere, riducendo il costo complessivo per parte.
Infatti, occupando l’area di costruzione del sistema, Mikosz afferma di essere stato in grado di stampare 160 dita in soli due giorni. La riduzione della distanza tra le parti in movimento gli ha anche permesso di creare giunti funzionali con poca post-elaborazione, cosa che non è possibile utilizzando altre tecniche, senza aggiungere passaggi che richiedono tempo.
Inoltre, la cifra additiva di PHS in precedenza richiedeva l’uso di una presa in fibra di carbonio per connettersi al corpo di un paziente. Utilizzando il Fuse 1, l’azienda è ora in grado di fabbricare le protesi utilizzando invece polimeri, rendendole più convenienti e personalizzabili di prima, senza compromettere la qualità della superficie finale.
“SONO IMPRESSIONATO DALLA CAPACITÀ DI STAMPARE GIUNTI FUNZIONANTI. NON AVRÒ MAI PIÙ BISOGNO DI ESTERNALIZZARE QUESTE PARTI. “
Come dimostrazione finale delle capacità di Fuse 1, PHS 3D ha stampato un gomito protesico per un paziente di dieci anni. Tradizionalmente, gli amputati pediatrici sono costretti a utilizzare arti artificiali standard di dimensioni per adulti, che possono rivelarsi pesanti per i bambini man mano che crescono in essi. Utilizzando la sua nuova stampante 3D, invece, l’azienda è stata in grado di fabbricare un’alternativa a base di nylon notevolmente più leggera.
Dal punto di vista della produzione, Mikosz ha scoperto che la spalla era ancora più facile da stampare e pulire rispetto alle dita a causa delle sue dimensioni, della mancanza di fessure e della ridotta quantità di polvere rimanente. Anche se non ha rivelato con precisione quanto tempo ci è voluto per la stampa, Mikosz ha aggiunto che era più lungo di prima, ma che era “appropriato date le sue dimensioni”.
Sebbene PHS sia stato essenzialmente un utente beta pre-lancio, il case study dimostra almeno l’efficacia di Fuse 1 nel rendere più accessibile l’SLS industriale. A lungo termine, tuttavia, resta da vedere come la nuova macchina di Formlabs si confronterà con gli altri nomi affermati del settore nell’arena SLS desktop.
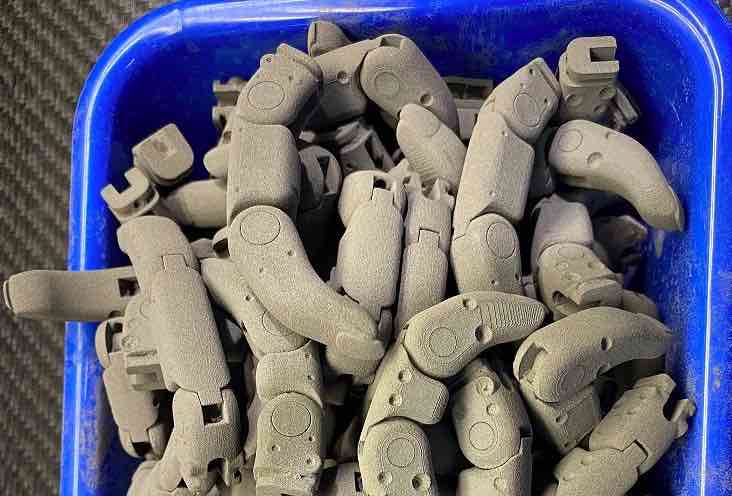