Il NIST statunitense ha sviluppato una tecnica per misurare lo stress meccanico nelle parti metalliche stampate in 3D che potrebbe cambiare il modo in cui viene eseguita la stampa 3D.
La stampa 3D in metallo è una delle discipline più complesse del settore e uno dei motivi è dovuto all’uso di parti metalliche durevoli per la produzione. Queste parti per uso finale devono sopravvivere in una varietà di ambienti meccanici e pertanto devono soddisfare gli standard di qualità specificati.
Tuttavia, produrre stampe 3D in metallo di alta qualità è un’attività difficile, principalmente a causa di problemi termici.
Il processo di stampa 3D in metallo più popolare è il noto processo LPBF, in cui potenti laser fondono selettivamente polvere di metallo fine su un letto piano, strato per strato per costruire gradualmente un oggetto.
I problemi iniziano con il calore necessario per eseguire quella fusione. A differenza della stampa 3D polimerica, dove le temperature richieste vanno da 180 °C a 400 °C, la stampa 3D in metallo richiede un calore molto più elevato.
Con quel calore aggiunto arriva l’espansione termica e il restringimento mentre il materiale metallico si raffredda. Sfortunatamente questo riscaldamento e raffreddamento si verificano durante e dopo il lavoro di stampa e abbracciano l’intera geometria del pezzo.
Di interesse per i ricercatori del NIST è stato l’effetto di queste condizioni termiche sperimentate a livello atomico delle stampe 3D.
Hanno capito che dopo che uno strato è stato prodotto da un riscaldamento estremo, il materiale si raffredda rapidamente. Quando lo strato successivo sopra il primo strato inizia a sciogliersi, abbiamo una situazione in cui c’è caldo sopra e freddo altrove. Non va mai bene.
Il metallo di raffreddamento si restringe e tira sul materiale di metallo espanso ancora caldo, introducendo stress. Questo micro-stress può essere accumulato sull’intera stampa 3D, il che significa che la forza complessiva della stampa può essere compromessa.
Per contrastare questo, alcuni produttori di stampanti 3D hanno utilizzato quello che viene chiamato un “approccio dell’isola”. In questo metodo il livello viene segmentato in “isole”, che vengono stampate in serie. In teoria, poiché ciascuna delle isole viene stampata più velocemente della scansione raster, perderebbero meno calore e sarebbero quindi meno suscettibili al problema dello stress.
I ricercatori del NIST volevano vedere se ciò fosse effettivamente vero e sono stati in grado di misurare l’effetto dello stress in un modo molto interessante.
Hanno sparato raggi X ad alta energia in stampe di prova in metallo e misurato le lunghezze d’onda riflesse. Utilizzando alcuni calcoli, ciò ha permesso loro di determinare “con elevata precisione” la distanza effettiva tra gli atomi nel campione.
L’idea è che se la distanza tra gli atomi è maggiore, lo stress è maggiore. Pertanto, sono stati in grado di misurare con precisione lo stress meccanico residuo nelle parti stampate in 3D in metallo.
Cosa hanno trovato dopo aver testato una varietà di modelli di stampa 3D in metallo comunemente usati? Il ricercatore Thien Phan ha spiegato:
“Questo è stato molto sorprendente e sottolinea la complessità del problema. Dimostra che, sebbene la scansione dell’isola possa funzionare in molti casi, non ha funzionato nel nostro, il che evidenzia davvero il fatto che abbiamo bisogno di una modellazione accurata”.
Sebbene questo sia semplicemente uno studio di ricerca, mi sembra che un uso più ampio dell’approccio potrebbe consentire lo sviluppo di modelli di stampa 3D in metallo molto più sofisticati che potrebbero ridurre al minimo l’effetto di stress residuo. Forse questo metodo potrebbe essere commercializzato in futuro e probabilmente verrebbe fatto da un produttore di stampanti 3D in metallo esistente.
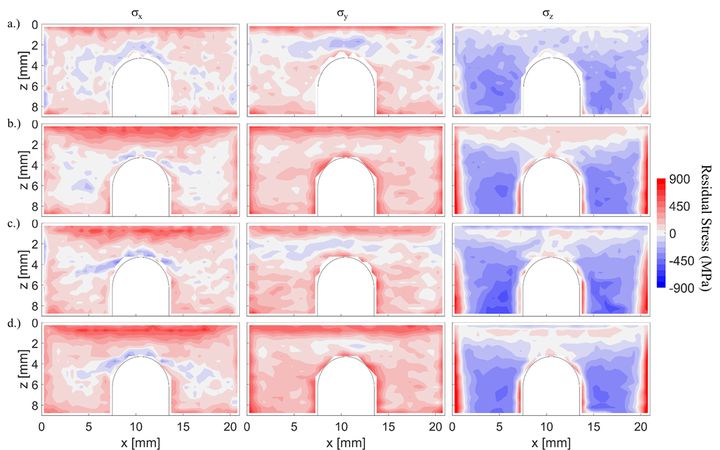