La Stampa 3D di ceramiche potrebbe aumentare l’efficienza del carburante delle turbine a gas, secondo quanto riportato da ricercatori
UNIVERSITY PARK, Pa. — I motori degli aeroplani possono raggiungere temperature superiori a 3.000 gradi Fahrenheit. Più si surriscaldano, più efficienti diventano dal punto di vista del consumo di carburante, ma l’efficienza è limitata dalla temperatura massima che i componenti metallici all’interno della turbina possono raggiungere senza deformarsi.
Un team che include ricercatori della Penn State ha recentemente stampato in 3D un componente di turbina con ceramica, che è più tollerante al calore rispetto ai metalli convenzionali. Il componente risultante ha caratteristiche di raffreddamento interno complesse che gli consentono di resistere a temperature più elevate e, di conseguenza, aumentare l’efficienza del carburante.
I ricercatori presenteranno i loro metodi e risultati alla ASME 2023 Turbomachinery Technical Conference and Exposition, che si terrà dal 26 al 30 giugno a Boston. Il loro lavoro sarà pubblicato negli atti della conferenza ed è stato anche raccomandato per la pubblicazione sull’ASME Journal of Turbomachinery.
“Ci sono numerose ricerche sui materiali ceramici per le turbine a gas, ma poche hanno generato parti realisticamente sagomate perché la fabbricazione è così difficile da realizzare”, ha dichiarato Stephen Lynch, coautore dell’articolo e professore associato di ingegneria meccanica presso la Penn State. “Questo processo è stato unico nel senso che potevamo generare parti dalla forma complessa in modo molto facile e a basso costo.”
I ricercatori hanno utilizzato l’ottimizzazione del design e una nuova tecnica di stampa 3D, nota anche come manifattura additiva, per realizzare alari resistenti al calore utilizzando un materiale ceramico derivato da polimeri. Questi componenti della turbina sono pale a forma di petalo che deviano costantemente il gas caldo all’interno del motore della turbina a gas per estrarre energia. Questa energia viene utilizzata in parte per alimentare il resto del motore e il resto viene convertito in spinta per un aeromobile o in energia per azionare un generatore elettrico.
“Abbiamo collaborato con ricercatori della Colorado School of Mines e dell’University of Wyoming che avevano inserito fibre ceramiche all’interno di ceramiche stampate in modo additivo”, ha spiegato Lynch, spiegando che queste ceramiche derivate da polimeri vengono create attraverso la cottura di una base simile alla plastica in un forno. “Abbiamo adattato questo processo per creare queste pale di turbina, ma abbiamo anche sfruttato la libertà di progettazione della stampa 3D per creare caratteristiche interne che migliorano notevolmente l’efficacia dell’aria di raffreddamento all’interno della pala.”
Utilizzando la stampa 3D in combinazione con le ceramiche derivate da polimeri, i ricercatori sono stati in grado di creare le forme esatte necessarie per resistere a temperature più elevate e ottenere prestazioni ottimali nelle turbine a gas. Il team ha testato le parti nel centro di ricerca sulla cascata ad alta velocità della Penn State, ospitato nel Laboratorio di Ricerca sulle Turbine Aeroterme Stazionarie.
“Abbiamo scoperto che con il giusto design per la parte, la forma dell’ala in ceramica che abbiamo stampato in 3D può funzionare altrettanto bene dei componenti metallici”, ha affermato Lynch. “La nostra speranza è che questa tecnologia possa essere utilizzata per sviluppare parti in ceramica che funzionino in modo simile alle parti metalliche nei motori delle turbine a gas, ma che possano tollerare temperature più elevate per una maggiore efficienza del carburante.”
Gli altri autori di questo articolo sono Andrew Fox, studente di dottorato in ingegneria meccanica alla Penn State; Jason Young e Carl Frick della Colorado School of Mines; e Jennifer Hankins, Kyle Kuhn, Stephan Brinckmann e Ray Fertig III dell’University of Wyoming. Michael Hickner, attualmente professore in Michigan State University College of Engineering e professore di scienza e ingegneria dei materiali, di ingegneria chimica e di chimica alla Penn State al momento della ricerca, ha contribuito anche al progetto.
Questo lavoro è stato finanziato dal Dipartimento dell’Energia degli Stati Uniti.
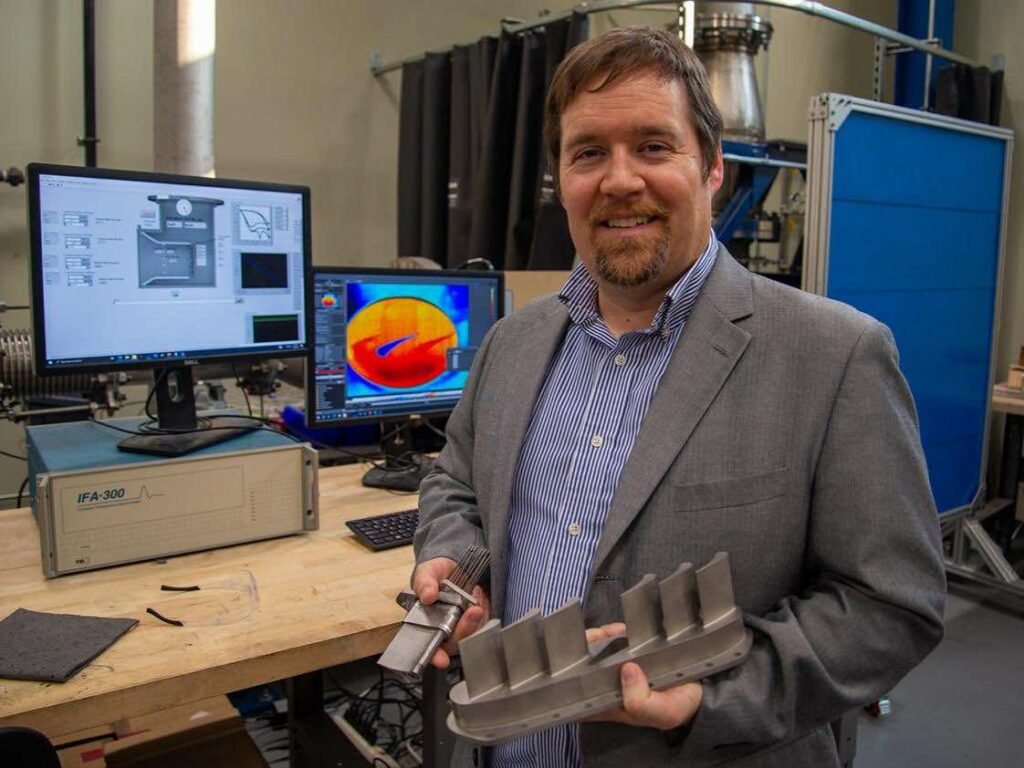
Lynch faceva parte di un team che ha stampato in 3D un componente di una turbina utilizzando la ceramica, un materiale che è più resistente al calore rispetto ai metalli tradizionali (Immagine © Kate Myers/Penn State).