In prima linea: Baker Hughes sulla distribuzione della stampa 3D nel settore petrolifero e del gas
Firenze, Talamone, Celle, Aberdeen, Houston, Kariwa e Dhahran.
Queste sono le sette sedi in cui Baker Hughes ha implementato centri di eccellenza per la produzione additiva. Solo sette anni fa, non ne aveva.
Mentre il 2020 ha visto l’azienda sfruttare la sua capacità additiva per affrontare la carenza di dispositivi medici e DPI a seguito della pandemia COVID-19, il 2019 è stato un anno significativo, poiché ha qualificato tanti componenti fabbricati additivamente per uso finale quanti sono i cinque precedenti messi insieme . Baker Hughes ha ora una collezione di oltre 450 parti qualificate che, complessivamente, sono state prodotte in modo additivo oltre 25.000 volte.
“Senza dubbio”, afferma il Dr. Mikhail Gladkikh, Global Technology and Operations Leader per l’Additive Services Growth Venture, “siamo leader nel settore del petrolio e del gas nelle applicazioni di produzione additiva funzionale”.
Quella leadership del settore, dimostrata attraverso la sua miriade di applicazioni per macchine downhole e turbo, deriva da quelle sette strutture. Ciascuno ospita team di specialisti della produzione additiva e invita gli ingegneri delle varie linee di prodotti dell’azienda a condividere conoscenze, tecnologia e intuizioni e, infine, a sfruttare l’additivo per risolvere i problemi in tutta l’azienda.
Gladkikh descrive i centri come “catalizzatori per l’implementazione additiva”. Ad Aberdeen, il team additivo si concentra sulle applicazioni delle apparecchiature per i giacimenti petroliferi, mentre i due centri in Italia servono principalmente gli sforzi del motore turbo di Baker Hughes. Circa il 50% degli sforzi compiuti a Houston è sulla produzione additiva di parti, con un focus anche sullo sviluppo di processi e materiali, che avvengono di pari passo.
L’impianto di Dhahran è principalmente un centro di ricerca e sviluppo e ospita il primo sistema di produzione di additivi metallici per l’industria dell’Arabia Saudita, installato lo scorso anno. Un’applicazione che esce da questa struttura è un anello di backup Rock Lock, che è stato riprogettato per un processo additivo per consentire un intervallo di espansione del packer, il che significa che la parte può ora eseguire operazioni in una gamma più ampia di dimensioni del pozzo. La progettazione di questa parte non sarebbe possibile con le tecnologie tradizionali.
Nel 2013, il primo componente stampato di Baker Hughes era un cilindro di contenimento del nucleo per applicazioni a fondo pozzo, con ugelli di carburante per macchine turbo prodotti in modo additivo nello stesso periodo. Nel corso degli anni, l’applicazione della stampa 3D si è espansa in tutto il business; la prototipazione rapida, le maschere e le attrezzature costituivano la maggior parte dei primi casi d’uso, ma le parti per l’uso finale si materializzavano in turbine a gas, compressori, strumenti a fondo pozzo e anche nelle linee di prodotti di misurazione e sensori di Baker Hughes.
“Nel petrolio e nel gas, è un tipo di gioco ad alto contenuto di mix e basso volume”, dice Gladkikh. “Ecco perché l’additivo è perfetto perché puoi progettare e produrre parti in modo economico per un carico di uno – a volte è quello che dobbiamo fare. Ci sono molti componenti molto semplici che non hanno senso per l’additivo, ma ci sono anche molti assemblaggi complessi, come collettori idraulici o diversi tipi di apparecchiature di completamento, dove l’additivo ha molto senso. Qui è dove l’additivo è il migliore; dove non solo possiamo ridurre i tempi di consegna a causa del processo o dell’approccio della catena di fornitura, ma possiamo anche ridisegnare e migliorare le prestazioni funzionali perché l’additivo ci consente di aprire l’involucro del design e rendere possibili soluzioni che prima erano impossibili con il convenzionale “.
Sbloccare queste possibilità significa portare l’applicazione della stampa 3D di Baker Hughes al livello successivo. L’azienda non solo vuole ridurre peso, componenti e costi, ma vuole anche sfruttare la tecnologia per mantenere i componenti operativi e mantenere le operazioni in esecuzione.
In questo momento, sul campo, la perforazione in profondità nella superficie terrestre, è una prova del concetto di punta da trapano prodotta con una tecnica ibrida che unisce la fresatura CNC a 5 assi e la deposizione diretta di energia (DED). Questa punta da trapano è lavorata in una forma quasi netta, perché il volume di materiale necessario “non ha senso per l’additivo” – prima che il processo DED aggiunga materiale in acciaio inossidabile 17-4PH alle lame con le frese inserite successivamente. In genere, le punte per trapano a fondo pozzo come questa vengono scartate dopo alcuni utilizzi, come l’usura del componente, ma utilizzando questo approccio ibrido e l’apparecchiatura di scansione di Baker Hughes presa in prestito dalla sua attività di ispezione, la società ripristinerà la punta del trapano al suo originale forma aggiungendo materiale al substrato esistente e ridistribuire il componente.
“Se si dispone di una parte obsoleta, è necessario capire quali sono le prestazioni funzionali di quella parte”, spiega Gladkikh, “e talvolta questa verrà danneggiata. È necessario utilizzare le proprie capacità di ingegneria e i primi principi di ingegneria per ripristinarlo per assicurarsi che svolga la funzione per cui è stato progettato. Con [questo processo ibrido], puoi riportarlo a quella forma o puoi anche pensare a come possiamo migliorare la forma, in modo che svolga meglio quel ruolo funzionale “.
Questo processo è destinato ad essere applicato a una serie di prodotti di punte da trapano in tutta l’attività Baker Hughes, con la società in grado di depositare anche acciaio inossidabile 316, Inconel 17 e carburo di tungsteno utilizzando tale tecnica ibrida. Mentre la stampa 3D ha la capacità di ripristinare questi componenti per essere riutilizzati, ci sono molte occasioni in cui le parti devono essere completamente sostituite per mantenere le operazioni in movimento.
Gladkikh afferma che molti clienti Baker Hughes subiscono perdite di centinaia di migliaia di dollari al giorno quando è necessario un pezzo di ricambio ma né l’inventario è adeguatamente fornito né il produttore regionale è reattivo. Baker Hughes sta quindi configurando un’offerta di servizi di emergenza con la tecnologia di stampa 3D al centro della produzione e la scansione 3D viene nuovamente implementata per eseguire il reverse engineering delle parti una volta eseguito un processo di “design triage”. Questo servizio lavorerà per ridurre attivamente l’inventario fisico, un concetto già in azione a Baker Hughes, nonché per facilitare la produzione locale, producendo parti il più vicino possibile al punto di bisogno.
“Se un impianto o un bene è fermo, il costo del tempo di inattività è molto superiore al costo di stampa di quel pezzo di ricambio; è qui che aggiungiamo molto valore esponenziale, possiamo utilizzare rapidamente le nostre capacità di scansione 3D, reverse engineering e progettazione per additivi e stampare quei pezzi di ricambio “, spiega Gladkikh.
Baker Hughes sta godendo di questo valore aggiunto in misura leader del settore. Centinaia di parti stampate migliaia di volte sono state qualificate per gli stessi requisiti di altre migliaia di componenti fabbricati in modo convenzionale. L’azienda non sta solo ridisegnando le parti esistenti per ridurre il peso e il costo, ma sta anche cercando di ridurre gli sprechi attraverso il ripristino dei componenti esistenti e snellire le catene di fornitura di se stessa e dei clienti. Questo in diversi continenti e dozzine di paesi. E c’è di più in arrivo.
“Consideriamo sicuramente l’additivo una competenza fondamentale e una delle tecnologie chiave per il futuro. Insieme all’apprendimento automatico e all’edge computing, questo porterà avanti l’energia e siamo in prima linea “, afferma Gladkikh prima di aggiungere:” Ma dobbiamo vedere macchine più robuste, macchine di dimensioni maggiori e una maggiore varietà di materiali. Dobbiamo automatizzare per ridurre al minimo la manipolazione della polvere, dobbiamo sfruttare appieno questa capacità di libertà di progettazione e stiamo lavorando con alcuni dei nostri partner digitali, come ANSYS e Autodesk, per utilizzare la loro suite di tecnologie di progettazione generativa.
“Un’altra applicazione che stiamo esplorando, e abbiamo già prodotti in cui è implementata, è multi-materiale. Questo apre una busta completamente nuova. Un’altra opportunità sono i dispositivi intelligenti, che incorporano sensori negli strumenti e nei prodotti che oggi produciamo in modo additivo, per trasformare veramente le prestazioni di quei prodotti.
“Questo è il futuro; questo è dove stiamo andando. “
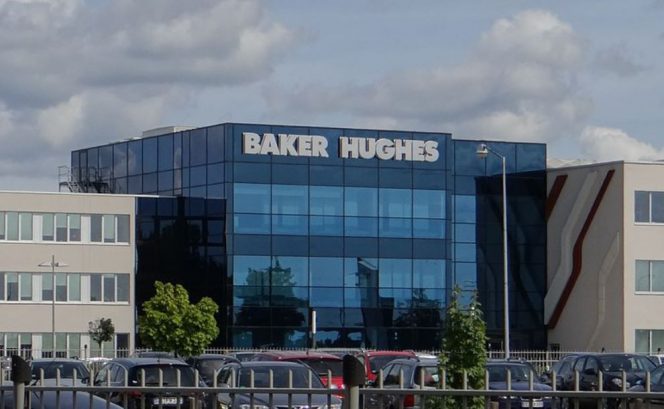