I ricercatori confrontano la microstruttura di campioni in lega di magnesio estruso, estruso a caldo e stampato in 3D
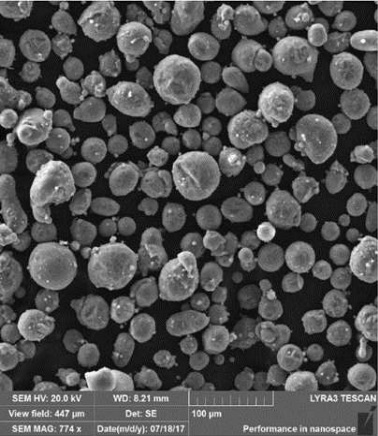
Le leghe del magnesio grigio lucido (Mg) sono caratterizzate da un elevato rapporto resistenza / peso e una bassa densità di circa 1700 kg / m3, che le rende buone opzioni per applicazioni tecniche nei settori automobilistico, aeronautico e medico . Ma è stato determinato che il loro peso può essere ulteriormente diminuito se si formano strutture porose, il che può essere ottenuto con la stampa 3D. Un team di ricercatori dell’Università di Chimica e Tecnologia di Praga e dell’Università di Tecnologia di Brno , entrambi nella Repubblica Ceca, volevano studiare la microstruttura di una particolare lega di magnesio dopo che era stata fabbricata usando tre diversi metodi: as-cast, hot -estruso e stampato in 3D con tecnologia SLM.
La stampa 3D SLM può ottenere forme geometriche complesse, ma ci sono problemi quando si tratta di fabbricare leghe di magnesio con questo processo, principalmente alta reattività della polvere di magnesio, che può portare a particelle di ossido pericolose che si formano all’interno delle parti stampate in 3D. Patrícia Krištofová, Jiří Kubásek, Dalibor Vojtěch, David Paloušek e Jan Suchý hanno recentemente pubblicato uno studio dal titolo ” Microstruttura della lega di magnesio Mg-4Y-3RE-Zr (WE43) prodotta dalla stampa 3D “, sul loro lavoro di mappatura di uno SLM 3D microstruttura in lega di magnesio stampato.
“Le leghe di magnesio realizzate sotto forma di stampa 3D sono processi di produzione relativamente nuovi”, hanno scritto i ricercatori. “Lo studio quindi questo processo rispetto ai processi attuali, che sono ora ben noti e mappati. È stata quindi studiata la microstruttura prodotta da tre diversi processi di produzione. La microstruttura e la composizione chimica delle fasi attuali sono state studiate utilizzando la microscopia elettronica a scansione (SEM) e la spettrometria Xray a dispersione di energia (EDS). Sulla base dell’esame microstrutturale, sono state riscontrate differenze significative tra i materiali prodotti da diversi processi produttivi. La microstruttura della lega as-cast consisteva di dendriti α-Mg relativamente grossolani circondati da eutettici contenenti elementi di lega ricchi di fasi intermetalliche. Durante l’estrusione a caldo, l’eutettico frammentato in particelle fini disposte in file parallele alla direzione di estrusione. La lega stampata in 3D è stata caratterizzata da una microstruttura notevolmente perfezionata a causa di un’elevata velocità di raffreddamento durante il processo SLM. Consisteva in dendriti molto fini di α-Mg e reti interdendritiche arricchite negli elementi di lega. Inoltre, c’erano anche ossidi che coprivano le particelle di polvere originali e il materiale mostrava anche una certa porosità che è una caratteristica comune delle leghe stampate in 3D “.
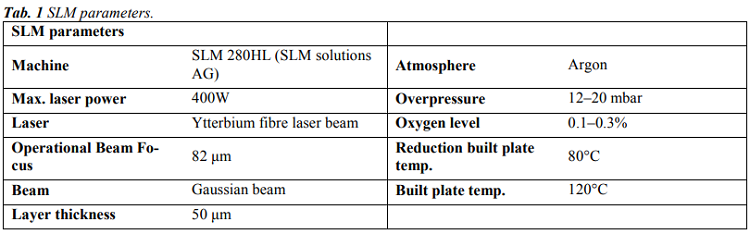
Il team ha utilizzato una stampante 3D SLH Solutions 280HL per fabbricare campioni rettangolari 15 × 5 × 60 mm di lega di magnesio WE43 e utilizzato SEM e EDS per studiare le loro microstrutture; quindi, questi sono stati confrontati con materiali identici che sono stati fabbricati attraverso la semplice fusione a gravità e l’estrusione a caldo.
“Il primo campione era un lingotto colato di dimensioni 60 × 80 × 500 mm acquistato da un fornitore industriale. Il secondo campione di lega WE43 è stato preparato mediante estrusione a caldo del lingotto. Cilindri con un diametro di 30 mm e una lunghezza di 60 mm sono stati tagliati direttamente dal lingotto e quindi estrusi a 400 ° C, velocità di estrusione di 2 mm / se rapporto di estrusione di 16. Le aste estruse risultanti avevano un diametro di 7,5 mm “, Hanno spiegato i ricercatori.
“L’analisi ha rivelato che il 10% delle particelle di polvere di lega WE43 aveva una dimensione di 26,9 μm, 50% a 39,8 μm e 90% a 57,9 μm. Pertanto, la polvere contiene una quantità sufficiente di particelle più grandi e più piccole. Per quanto riguarda le dimensioni delle particelle, la dimensione dello strato dell’edificio era 50 μm. “
Il team ha condotto osservazioni microscopiche dei campioni e si può vedere la vista delle loro microstrutture nella Figura 2.
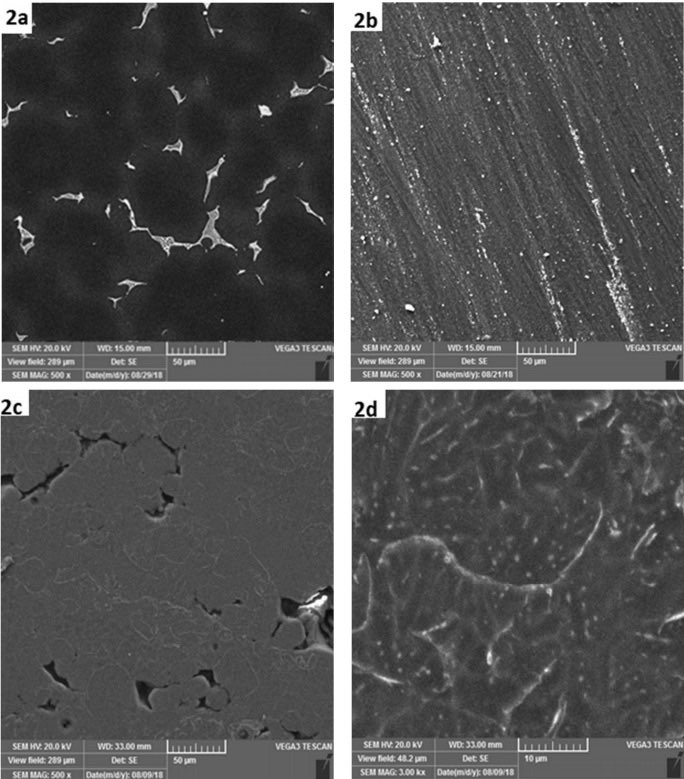
La lega pressofusa ha una microstruttura grossolana, mentre la microstruttura del campione fabbricata con estrusione a caldo è stata “considerevolmente” modificata. La microstruttura del campione stampato in 3D è completamente diversa dalle altre due, con regioni di circa 20-50 μm circondate da bordi sottili.
“Inoltre, la porosità residua viene osservata come aree scure tra le regioni grigie. La forma e la dimensione delle regioni grigie indicano che queste regioni corrispondono a particelle di polvere originali, totalmente o parzialmente fuse con raggio laser “, hanno spiegato i ricercatori. “Un’immagine più dettagliata in Fig. 2d mostra una microstruttura interna molto fine di queste particelle. Contiene dendriti α-Mg (scuri) circondati da regioni interdendritiche (chiare) arricchite in elementi Y e RE. La mediocrità dei rami dendritici è solo di ca. 3 μm, suggerendo frequenze di raffreddamento molto elevate durante il processo SLM. In letteratura focalizzata sul processo SLM, vengono spesso riportati tassi di raffreddamento di 103-106 K / s. “
I ricercatori hanno anche studiato la distribuzione degli elementi nella struttura del materiale, che ha dimostrato che sia i campioni di materiale estruso a caldo che quelli di fusione avevano una concentrazione di ossigeno molto bassa. Ma il campione stampato SLM 3D ha mostrato una storia diversa, illustrata nella Figura 5 e nella Tabella 4.
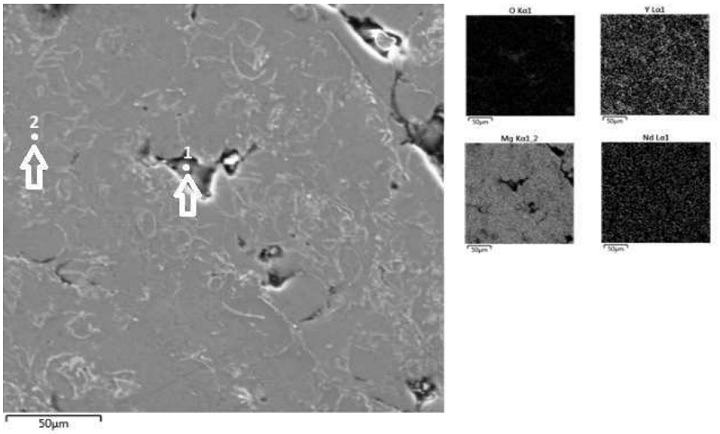
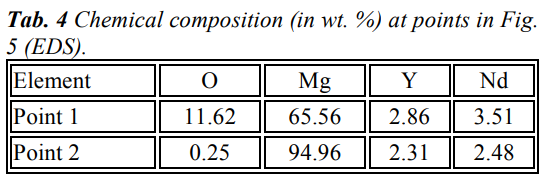
“In primo luogo, le mappe degli elementi e l’analisi dei punti dimostrano una maggiore concentrazione di ossigeno nel materiale che si trova principalmente nei pori (punto 1) e anche nei legami tra le particelle di polvere fusa. Nell’interno della particella la concentrazione di O è molto bassa (punto 2) “, hanno scritto i ricercatori. “In secondo luogo, la mappa degli elementi in Fig. 5 indica anche un aumento del contenuto di Y ai confini delle particelle di polvere. Si può presumere che l’ossidazione parziale della polvere si sia verificata durante il processo SLM all’interno della camera dell’edificio. Molto probabilmente, l’atmosfera conteneva tracce di ossigeno residuo che reagivano preferenzialmente con l’ittrio a causa dell’elevata affinità chimica di questi elementi. Per questo motivo, si osservano imperfette connessioni tra particelle di polvere e porosità. “
I risultati mostrano che la microstruttura di un materiale SLM è “estremamente fine” a causa di elevate velocità di raffreddamento e presenterà anche un’alta concentrazione di ossigeno “a causa dell’elevata affinità della lega con questo gas.” Questo crea una “connessione imperfetta” tra le particelle di polvere e porosità. I ricercatori progettano ulteriori studi su questa lega di magnesio per produrre materiale compatto privo di pori e ridurre “l’influenza dannosa dell’ossigeno residuo”.