Stampa 3D in Fastlane: l’azienda di tornelli utilizza la macchina Markforged per la produzione di maschere e attrezzature
Gli uomini d’affari delle grandi aziende cittadine e gli studenti delle università pubbliche spesso iniziano la giornata allo stesso modo, passando da una porta girevole, salutando gentilmente chi è alla reception, toccando una carta d’identità con un lettore elettronico e camminando attraverso l’ala di vetro barriere segnate dal marchio Fastlane Turnstiles per il resto della giornata.
Il modo in cui il marchio Fastlane è arrivato sulle pareti di vetro che aiutano Facebook, Dell, Google, Manchester University e 7 World Trade Center a proteggere i propri edifici non è stato in genere un processo facile. È stato fatto a mano ea vista e se il posizionamento del logo non fosse stato eseguito correttamente sarebbe stato necessario rimuoverlo e riposizionarlo sull’anta di vetro. Questo è stato un compito difficile da svolgere ripetutamente, che richiede tempo e occasionalmente stressante, e poi è arrivata la stampa 3D.
Il produttore di sistemi di controllo degli accessi pedonali ha adottato la tecnologia per la prima volta nel 2018, dopo aver incontrato il rivenditore britannico CREAT3D in una fiera di produzione additiva, sotto forma di una macchina Mark Two. Questa piattaforma, sviluppata da Markforged , rinforza il suo materiale Onyx con fibra di carbonio, fibra di vetro e Kevlar, ed è stata acquisita da Fastlane per snellire i suoi sforzi di ricerca e sviluppo, progettando parti a costi inferiori in meno tempo.
Lavorando con CREAT3D, sono state stampate alcune parti campione iniziali, una per controllare la forma di un componente di ricerca e sviluppo e l’altra per valutare la funzione di un componente fabbricato, con Fastlane che si dice sia stato colpito dalle proprietà di resistenza e dalla finitura superficiale e resistenza alla temperatura.
Le funzioni del reparto di ricerca e sviluppo, supporto alla produzione e miglioramenti continui sono state ampiamente supportate dalla stampa 3D.
Dopo queste parti iniziali, Fastlane ha installato la Mark Two nel suo dipartimento di ingegneria, dove è stata immediatamente utilizzata per stampare componenti di ricerca e sviluppo che normalmente sarebbero stati esternalizzati e prodotti in metallo. La stampa di questo tipo di parti stava eliminando due settimane di lead time dal processo di progettazione e presto anche il team di produzione e assemblaggio di Fastlane stava cercando di sfruttare le capacità della macchina. Da qui, l’applicazione della stampa 3D di Fastlane è esplosa, secondo Sabina Gonzalez-George e Simon Chandler di CREAT3D.
Spesso citati come il frutto a bassa pendenza '' della produzione additiva, gli aiuti alla produzione non solo hanno rappresentato una rapida vittoria per Fastlane, con riduzioni di costi e tempi ottenute rispetto a maschere e dispositivi di produzione tradizionale, ma, stampando in 3D una maschera con un
bordo di posizionamento ” per adattarsi l’esatta geometria della porta in vetro, ha anche risolto il problema del posizionamento del logo dell’azienda su quelle barriere ad ala di vetro.
“Le barriere di vetro erano tagliate a CNC, quindi sapevamo che le barriere erano abbastanza precise per il disegno [del progetto]; abbiamo modellato la maschera utilizzando i bordi piatti e curvi del vetro come riferimenti in Autodesk Investor e siamo stati in grado di stamparla abbastanza rapidamente, il che ha permesso alla produzione di attaccare facilmente il logo “, ha spiegato Mike Lau, responsabile tecnico di Fastlane. “[Inoltre], la maschera sarebbe una parte abbastanza complicata e costosa da realizzare utilizzando metodi tradizionali, con molte operazioni di configurazione e lavorazione a partire da materiale costoso, quindi, come una tantum, la stampa 3D ha senso come costo e tempo sono solo una frazione di ciò che sarebbero normalmente i metodi tradizionali. “
Questo è il tipo di utensile che Fastlane avrebbe tipicamente affidato in outsourcing per essere lavorato dall’acciaio di alluminio a un costo di circa 150 GBP e consegnato dopo due settimane. Con la stampa 3D, Fastlane ha prodotto la parte in sei ore, una riduzione del 96%, a un costo inferiore a 7 GBP; una riduzione del 95,5%; e ha registrato la prima applicazione corretta con il 100% di accuratezza del marchio sulle ali di vetro.
“Con la stampa 3D, ora di solito possiamo produrre una maschera in meno di un giorno, il che ha notevolmente ridotto i ritardi di produzione”, ha affermato Lau. “Inoltre, poiché in precedenza era molto costoso e richiedeva tempo, limitavamo la quantità di maschere che avevamo ma ora, con la facilità della stampa 3D, siamo stati in grado di creare più tipi di maschere per aiutare la produzione”.
L’applicazione della società della stampa 3D per maschere e dispositivi è ora “ampia”, secondo Lau, con parti di ricerca e sviluppo che rappresentano anche un gran numero di lavori di stampa interni. Fastlane ha anche identificato diversi componenti di produzione per uso finale che possono essere prodotti sulla Mark Two, anche se a bassi volumi, con ulteriori lavori da svolgere per accertare se le parti necessarie a volumi maggiori possono essere stampate in 3D.
Qualunque sia la categoria di parti finisce per richiedere la maggiore applicazione della tecnologia, l’uso della stampa 3D da parte di Fastlane è ora ampio in tutta l’azienda ei vantaggi della tecnologia si estendono anche a ciascuno dei suoi clienti.
“Le funzioni del dipartimento di ingegneria di ricerca e sviluppo, supporto alla produzione, progetti personalizzati e miglioramenti continui sono stati tutti ampiamente supportati dalla capacità di stampa 3D. La produzione ha tratto vantaggio dall’avere parti stampate in 3D che hanno notevolmente migliorato la facilità e il tempo di assemblaggio. I clienti hanno visto i vantaggi in quanto siamo più agili nell’integrazione di apparecchiature di terze parti nei nostri prodotti “, ha concluso Lau. “L’impatto è stato enorme.”
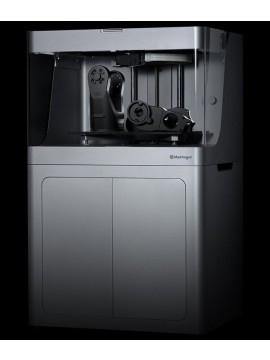