Promuovere la strategia per il processo di stampa 3D LPBF.
La tecnologia di stampa 3D metallica è in costante progresso, con un potenziale enorme nel rivoluzionare il settore manifatturiero grazie alla sua abilità di realizzare progetti complessi e ottimizzati.
Questa modalità di produzione ha già incrementato la produttività in vari settori come il petrolio e gas, la produzione d’acciaio e l’estrazione mineraria. Tra le applicazioni più recenti e interessanti della stampa 3D metallica vi è la produzione di giranti chiuse; tuttavia, la loro complessità rende la produzione con LPBF impegnativa a causa del numero di strutture di supporto richieste, che complicano sia la stampa che la post-elaborazione.
In collaborazione con EOS, TheSteelPrinters ha perfezionato un processo LPBF per la realizzazione di giranti chiuse che minimizza l’uso di strutture di supporto. Di conseguenza, queste componenti possono essere prodotte più velocemente e a costi inferiori, in quanto sono richiesti meno materiali e tempo di post-elaborazione.
SFIDE TECNICHE
La stampa 3D metallica di giranti chiuse utilizzando la tecnologia LPBF (Laser Powder Bed Fusion) presenta diverse sfide. Le giranti chiuse posseggono geometrie complesse con canali interni e caratteristiche di sbalzo a basso angolo, che richiedono l’impiego di strutture di supporto interne.
Le strutture di supporto interne aumentano i costi dei materiali e i tempi di stampa e possono essere difficili da rimuovere con la lavorazione post-elaborazione, spesso con conseguenti difetti di finitura superficiale. Inoltre, il requisito della lavorazione post-processo comporta un aumento dei costi e tempi di produzione più lunghi.
Per superare queste sfide, è quindi preferibile una strategia di stampa “senza supporto”. Il raggiungimento di questa strategia richiede una comprensione completa del processo LPBF e delle proprietà del materiale di stampa ed è essenziale sviluppare parametri di stampa su misura.
SVILUPPO DEL PROCESSO
Il dipartimento di ricerca e sviluppo di TheSteelPrinters ha condotto numerosi esperimenti volti a sviluppare una strategia di stampa 3D “senza supporto” per giranti chiuse. Questi esperimenti hanno comportato l’analisi di vari parametri di stampa, come la potenza del laser, la velocità del laser, la distanza di tratteggio e lo spessore del piumino, per ottenere diversi valori di energia del piumino per volume (J/mm3).
Attraverso questi esperimenti, il team ha sviluppato un nuovo approccio chiamato “High Energy Down Skin” (HEDS), che modifica i “parametri Downskin” per creare una zona saldata più forte in grado di resistere alle forze di ricopertura. Questo approccio ha notevolmente migliorato la producibilità degli sbalzi, consentendo la produzione di giranti chiuse senza l’uso
Di seguito è riportata una panoramica dei test di sviluppo HEDS e dei relativi risultati:
Nell’esperimento 1, abbiamo studiato cinque diverse configurazioni di parametri, ciascuna con diversi valori di energia di downskin, considerando variabili di processo come la direzione del flusso di gas e la direzione del rivestimento. I test sono stati condotti su provini con una sporgenza di 25 mm utilizzando il sistema EOS M290. Di conseguenza, tre dei cinque pezzi di prova sono stati stampati con successo.
L’esperimento 2 prevedeva il trasferimento del test a un sistema ad alta produttività, utilizzando provini con la stessa lunghezza di sporgenza di 25 mm, ma con le condizioni di processo del sistema EOS M400-4. Abbiamo studiato un totale di sette parametri di stampa, comprendenti tre dell’esperimento precedente e quattro nuovi parametri. Tuttavia, il risultato ha rivelato che solo tre dei pezzi di prova sono stati stampati con successo utilizzando le condizioni di processo M400-4.
Nell’esperimento 3, abbiamo studiato ancora una volta un totale di sette parametri di stampa, costituiti da tre dell’esperimento 2 e quattro nuovi parametri, utilizzando una EOS M400-4 e pezzi di prova con sporgenze di 35 mm. La fase di test è culminata con la stampa riuscita di due dei sette pezzi di prova, convalidando così due configurazioni dei parametri di stampa.
Infine, utilizzando i risultati dell’Esperimento 3, è stato condotto l’Esperimento 4, dove sono state testate le due configurazioni dei parametri di stampa validate producendo una girante chiusa con un diametro di 15 cm e con più angoli di sbalzo. Entrambe le configurazioni dei parametri hanno prodotto con successo giranti senza problemi di sbalzo, anche se con lievi differenze nella risoluzione della superficie.
CONCLUSIONI
Il successo dello sviluppo dell’approccio HEDS segna una pietra miliare significativa nella produzione di giranti chiuse e parti con sporgenze ad angolo basso.
Eliminando la necessità di strutture di supporto interne, le giranti chiuse possono essere prodotte con una precisione dimensionale superiore, tempi di consegna ridotti e convenienza.
L’utilizzo dell’approccio HEDS può ridurre i prezzi unitari fino al 30% per la produzione di una singola girante chiusa e fino al 45% per gli ordini all’ingrosso, rendendo così la produzione additiva una soluzione economicamente più sostenibile per la produzione di componenti per pompe e ricambi parti.
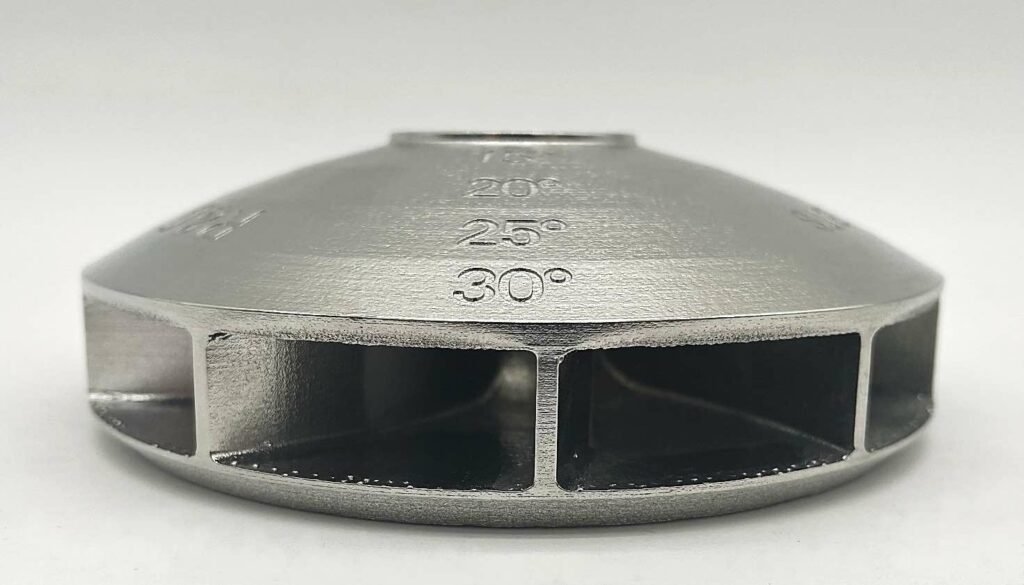