Le parti metalliche stampate in 3D diventano ipersoniche, a zero miglia orarie
Il termine “supersonici” indica velivoli che rompono la barriera del suono a Mach 1, come l’ormai in pensione Concord e l’emergente Boom Supersonic XB-1 , e si estende a circa Mach 5, cinque volte la velocità del suono e oltre 3.500 mph al livello del mare.
Quando viene raggiunta la velocità massima, si entra nell’ambiente ipersonico . Questo è quando iniziano ad accadere cose strane.
I ricercatori della Purdue University nell’Indiana stanno scoprendo che questo ambiente insolito può essere un perfetto banco di prova per la stampa 3D in metallo. Il recente lavoro svolto dal team dimostra che la tecnologia di produzione additiva avanzata è ora in grado di produrre parti completamente dense e per uso finale con una robustezza che supera i metodi tradizionali come la colata. Parti che possono creare condizioni ipersoniche e vivere per raccontare la storia.
“C’è una linea che si oltrepassa intorno a Mach 5”, ha detto il Professore Associato di Purdue Carson Slabaugh, il cui team di 20 persone presso gli Zucrow Laboratories ha studiato i sistemi di combustione ad alta velocità da quando ha avviato il suo laboratorio a Purdue nel 2015.
Slabaugh ha aggiunto: “Quando un veicolo vola così velocemente, si verifica una compressione e un riscaldamento estremi dell’aria che scorre intorno e all’interno della fusoliera. A Mach 5, si tratta di un aumento di circa sei volte della temperatura e di un aumento della pressione di alcune centinaia di volte. Questo tipo di carico termico e meccanico fa cambiare completamente il regime dell’aerodinamica e della meccanica strutturale rispetto ai sistemi a bassa velocità”.
Per ottenere un volo ipersonico a motore, con un aereo controllabile, un veicolo senza pilota o un missile, è necessario aggiungere un motore, ed è qui che diventa davvero intenso.
Al di sopra di Mach 5, la temperatura dell’aria atmosferica mentre scorre veloce è di migliaia di gradi e la pressione è di diverse centinaia di psi. L’aria stessa può anche diventare chimicamente reattiva se voli abbastanza velocemente. Le condizioni di flusso estreme diventano una sfida per qualsiasi sistema di propulsione del veicolo la cui spinta deriva dalla combustione di carburante.
Per affrontare questa sfida, Slabaugh e il suo team hanno collaborato con Velo3D per “stampare” iniettori di carburante con geometrie complesse che ottengono prestazioni di miscelazione aria-carburante molto elevate. I metodi di fabbricazione convenzionali non avrebbero potuto produrre tali parti, specialmente con le superleghe metalliche ad alta resistenza necessarie per sopravvivere alle condizioni di prova estreme.
“Attraverso la nostra partnership, abbiamo aiutato Velo3D a comprendere i requisiti di progettazione per i sistemi di combustione ad alta velocità e ci hanno insegnato come progettare meglio per la produzione additiva”, ha affermato Slabaugh. “Questo è il tipo di relazione reciprocamente vantaggiosa che costruiamo con i partner del settore mentre risolviamo le sfide associate alla transizione tecnologica avanzata”.
Progettare e produrre parti per condizioni ipersoniche, per non parlare di tentare di far volare veicoli che vanno a tali velocità, è comprensibilmente costoso. Gran parte della ricerca e dello sviluppo per lo sviluppo di capacità ipersoniche è stata supportata dalla NASA e dai budget a livello di difesa.
Il costo del test di volo dei sistemi significa limiti importanti su ciò che può essere effettivamente misurato a fini di ricerca. Gli ingegneri stanno ricreando le condizioni sperimentate durante il volo ipersonico e stanno provando i componenti del motore in strutture di prova a terra, come quella di Purdue per la quale il team di Slabaugh sta costruendo un razzo che non lascerà mai la Terra.
“Progettiamo componenti che sperimenteranno ambienti ipersonici andando a zero miglia orarie e rimanendo imbullonati a terra”, ha affermato Slabaugh.
Metodi come la fluidodinamica computazionale (CFD) e l’interazione fluido-struttura (FSI) possono essere utilizzati per simulare il comportamento del materiale e della struttura in risposta al flusso di aria o liquido. Ciò consente agli ingegneri di ottimizzare i progetti prima ancora di produrre qualsiasi cosa.
“Un problema fondamentale è che non possiamo prevedere in modo affidabile le condizioni di flusso e fiamma all’interno del motore in condizioni ipersoniche”, ha affermato Slabaugh.
Slabaugh ha parlato di come il team ha risolto questo problema, dicendo: “Quello su cui stiamo lavorando con Velo3D è fondamentalmente un grande masterizzatore stampato in 3D, che verrà utilizzato per creare l’ambiente ipersonico a terra in una cella di prova”.
Per creare un veicolo ipersonico a terra, devi costruire un motore a razzo con un grande ugello convergente e divergente e un pennacchio supersonico di gas estremamente caldo. Quindi qualsiasi componente viene testato viene inserito all’interno di quel pennacchio.
Slabaugh ha dichiarato: “Con Velo3D, stiamo progettando gli iniettori per quel combustore per produrre campi di flusso turbolento molto specifici che miscelano il carburante a una certa velocità e ci consentono di stabilizzare una fiamma molto potente in un volume molto compatto. Questo crea le condizioni per tutte le cose che testeremo a valle”.
La capacità di stampare rapidamente in 3D una varietà di geometrie di iniettori per il combustore di prova, in questo caso realizzato in Hastelloy X , una superlega ad alta resistenza e alta temperatura che resiste a un ambiente ipersonico, ha consentito al team di Purdue di identificare rapidamente quale progetto ha funzionato meglio.
Gli ingegneri hanno variato sottilmente i passaggi di flusso dell’iniettore con cinque diversi design. Si trattava solo di modificare il file di dati STEP che il software di preparazione della stampa del sistema VELO3D Sapphire adattava automaticamente. I progetti sono stati stampati e sono stati sottoposti a una serie di condizioni di prova rilevanti per l’ipersonico.
In sole due settimane, il team è stato in grado di isolare il più performante che avesse tutte le caratteristiche stazionarie e dinamiche che stavano cercando. L’iniettore ad alte prestazioni ha soddisfatto i parametri critici che gli ingegneri hanno apprezzato maggiormente per le prestazioni del combustore, la potenza della fiamma e la stabilità della fiamma.
Il prossimo passo per il team è ora assemblare una vasta gamma di iniettori in un combustore ancora più potente. Velo3D si sta consultando ulteriormente con i laboratori Zucrow per aiutarli a sfruttare le sue capacità di costruire tutto ciò che vuoi, integrando il set di iniettori in un unico pezzo, componente stampato in 3D.
Da lì, gli ingegneri continueranno a perfezionare e assemblare un sistema di combustione completo, puntando a una capacità di test ipersonici su vasta scala alla fine del 2022.
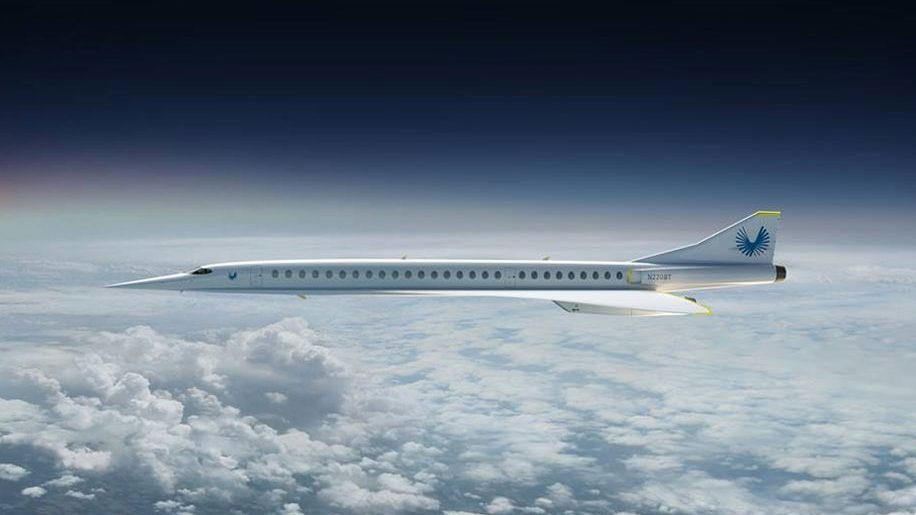