Electroimpact offre una soluzione di produzione continua di fibra di carbonio leggermente diversa dalle altre stampanti 3D CCF.
La fibra di carbonio continua (CCF) è altamente desiderabile in quanto combina un’incredibile resistenza con un peso leggero, rendendola ideale per le applicazioni aerospaziali. Tuttavia, è stato difficile stampare in 3D questo materiale.
Molte stampanti 3D esistenti offrono l’opportunità di stampare in 3D filamenti in “fibra di carbonio”, ma questi sono semplicemente un polimero mescolato con un rapporto di fibra di carbonio sminuzzata. Risultati migliori, sì, ma neanche lontanamente vicini a quelli di CCF.
Pochissime aziende hanno sviluppato stampanti 3D per inserire fili di CCF nelle stampe 3D, in particolare Markforged e Anisoprint , ma ce ne sono anche altre che lavorano su questa capacità. In alcune situazioni le parti prodotte sono resistenti quanto gli equivalenti metallici.
Electroimpact con sede a Washington adotta un approccio leggermente diverso. Sono un’azienda di 35 anni situata strategicamente vicino alla sede della Boeing, con la missione di fornire l’automazione della produzione all’industria aerospaziale. Offrono una vasta gamma di soluzioni di automazione, ma ora offrono una soluzione di stampa 3D per applicazioni CCF.
Il loro processo è chiamato “SCRAM”. Questo sta per “Scalable Composite Robotic Additive Manufacturing”, che fornisce alcuni indizi su come funziona.
SCRAM include un sistema robotico a sei assi che opera all’interno di una custodia. Non può solo stampare polimeri 3D, ma anche stabilire CCF.
Il processo SCRAM prevede la stampa 3D di una struttura polimerica con un materiale solubile. Questo viene fatto con il braccio robotico che si muove per creare una struttura strato per strato nel modo convenzionale, con un braccio robotico invece di un sistema cartesiano più tipico.
Una volta costruita la struttura polimerica, il sistema a sei assi inizia quindi a deporre CCF sui contorni della superficie della struttura polimerica. Essenzialmente stanno eseguendo un processo di stratificazione CCF, tranne per il fatto che lo stampo viene stampato in 3D immediatamente prima dell’applicazione CCF. Questo video mostra come funziona:
Una volta completata la fase CCF, la struttura polimerica viene dissolta, lasciando solo l’oggetto CCF.
La cosa interessante è che il robot a sei assi può applicare i fili CCF in direzioni arbitrarie. Ciò consente all’operatore di produrre un oggetto con la massima resistenza assicurando che i percorsi dei trefoli CCF siano allineati lungo le direzioni richieste. L’allineamento può cambiare man mano che vengono stabiliti strati aggiuntivi di CCF.
Electroimpact spiega come funziona:
“Ogni cella SCRAM è dotata non solo di un sistema di stampa rinforzato con fibre continue, ma anche di un sistema di fabbricazione rapida di utensili basato su un processo di stampa FFF avanzato. Il tradizionale layup automatizzato della fibra richiede sempre un investimento sostanziale in strumenti rigidi che siano rigidi, costosi e di lunga durata. Gli operatori di una cella SCRAM, invece, possono semplicemente stampare il loro strumento di supporto su richiesta, partendo da una semplice lastra piana. Successivamente, dopo che la parte ha terminato la stampa, il materiale dell’utensile viene sciolto. Ciò consente una rapida iterazione del progetto e consente a qualsiasi cella SCRAM di essere limitata solo dalle sue dimensioni e dall’immaginazione del progettista. Consente inoltre la creazione di geometrie di parti come canali interni che sono difficili o impossibili da produrre altrimenti. “
Se ciò non bastasse, il sistema include anche la possibilità di stampare in 3D filamenti in fibra di carbonio tagliati, proprio come molte altre stampanti 3D. Tuttavia, il sistema include un sistema di riscaldamento laser specializzato che produce “legami eccezionalmente forti tra gli strati”. Questo è piuttosto interessante ed è un approccio che altri produttori di stampanti 3D dovrebbero prendere in considerazione.
Electroimpact afferma che il componente FFF del sistema può gestire un’ampia varietà di materiali, tra cui:
Termoplastici della famiglia PAEK (PEEK, PEKK, ecc.)
Nylon e altri materiali termoplastici a bassa temperatura (PA12, ABS, ecc.)
Termoplastica idrosolubile
Fibra di carbonio
Fibra di vetro
Fibra di boro
Una domanda che ho riguarda i materiali ad alta temperatura, poiché spesso richiedono temperature della camera incredibilmente calde per evitare deformazioni, a volte ben superiori a 100 ° C. Tipicamente i sistemi con queste temperature interne isolano i componenti critici per evitare che vengano danneggiati da una ripetuta esposizione al calore.
Tuttavia, nel sistema Electoimpact sembra che l’intero sistema robotico e i materiali siano trattenuti all’interno della camera di costruzione e quindi sarebbero soggetti a calore elevato. Non sono sicuro di cosa stia succedendo qui; forse il sistema Electroimpact non raggiunge temperature della camera particolarmente elevate, a differenza di altre stampanti 3D dedicate ad alta temperatura.
Electroimpact offre anche una serie di opzioni, tra cui un estrusore di pellet e un end-effector CNC per la lavorazione di qualità della superficie.
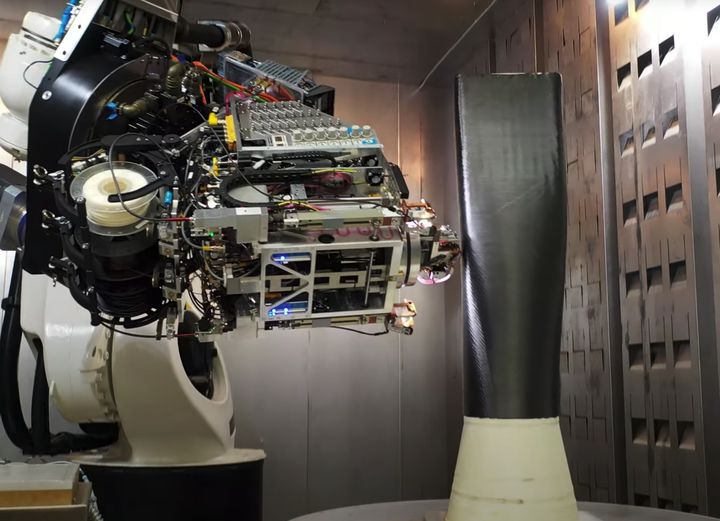
Produzione di additivi
Electroimpact ha integrato un processo AFP termoplastico in-situ out-of-autoclave e un processo di stampa 3D FFF avanzato in un sistema unificato SCRAM (Scalable Composite Robotic Additive Manufacturing). SCRAM è una vera stampante 3D rinforzata con fibre continue a 6 assi industriale, che consente la fabbricazione rapida senza strumenti di strutture composite integrate di livello aerospaziale. I materiali termoplastici ad alte prestazioni combinati con un’alta percentuale di rinforzo in fibra continua vengono utilizzati per produrre parti con proprietà dei materiali eccezionali in precedenza inaudite nel mondo della produzione additiva. Questa tecnologia non ha eguali nel settore ed è un’offerta unica disponibile solo da Electroimpact.
Stampa “True 3D”
La maggior parte dei processi di stampa 3D viene accuratamente descritta come stampa “2.5D”, poiché il materiale viene sempre depositato successivamente in fette piatte, che una volta impilate insieme formano un oggetto 3D. Il processo SCRAM, d’altra parte, può essere considerato una “vera stampa 3D”. Strati di termoplastica fibrorinforzata continua possono assumere la forma di contorni complessi, come superfici aerodinamiche e condotti per il flusso del fluido. Inoltre, poiché si tratta di un processo a 6 assi, l’orientamento delle fibre all’interno di ogni strato può essere adattato all’applicazione specifica per fornire una distribuzione ottimale della resistenza e della rigidità in tutta la parte, proprio come un sistema AFP convenzionale.
Strumenti stampati su richiesta
Ogni cella SCRAM è dotata non solo di un sistema di stampa rinforzato con fibre continue, ma anche di un sistema di fabbricazione rapida di utensili basato su un processo di stampa FFF avanzato. Il tradizionale layup automatizzato della fibra richiede sempre un investimento sostanziale in strumenti rigidi che siano rigidi, costosi e di lunga durata. Gli operatori di una cella SCRAM, invece, possono semplicemente stampare il loro strumento di supporto su richiesta, partendo da una semplice lastra piana. Successivamente, dopo che la parte ha terminato la stampa, il materiale dell’utensile viene sciolto. Ciò consente una rapida iterazione del progetto e consente a qualsiasi cella SCRAM di essere limitata solo dalle sue dimensioni e dall’immaginazione del progettista. Consente inoltre la creazione di geometrie delle parti come i canali interni che sono difficili o impossibili da produrre altrimenti.
Un sistema multi-materiale
Oltre al processo di stampa termoplastica rinforzata con fibre continue e al processo di stampa dello strumento di supporto FFF, le celle SCRAM sono dotate anche di un ugello FFF ottimizzato per la deposizione di materiale termoplastico rinforzato con fibra corta o “tagliata”. È incorporato un sistema di riscaldamento laser proprietario, che produce legami eccezionalmente forti tra gli strati. Questo processo è ideale per situazioni in cui la posa di fibra continua è geometricamente impossibile o altrimenti non ha senso.
Come il processo in fibra continua, questo è un processo di stampa “vero 3D” in cui gli strati non sono vincolati a una pila di piani. Geometrie complesse come il nucleo a densità variabile e altre strutture interne possono essere stampate direttamente su strati rinforzati con fibre continue con curvatura ampiamente variabile. Se lo si desidera, è possibile depositare strati continui rinforzati con fibre sopra la struttura centrale rinforzata con fibre tagliate, formando uno strato superiore.
Esempi di sistemi di materiali
Termoplastici della famiglia PAEK (PEEK, PEKK, ecc.)
Nylon e altri materiali termoplastici a bassa temperatura (PA12, ABS, ecc.)
Termoplastica idrosolubile
Fibra di carbonio
Fibra di vetro
Fibra di boro
Distinta base tipica della cella SCRAM
Siemens 840D CNC
Robot a 6 assi con pacchetto Accurate Robot brevettato da Electroimpact
6 ° asse robot continuo per passaggio utenze con rotazione illimitata
Interfaccia di cambio utensile che consente di prelevare e riconsegnare i dispositivi finali senza problemi
Effettore finale di deposizione multi-materiale
Piattaforma di costruzione riscaldata con piastra riscaldante rotante
Camera di costruzione riscaldata
Coupon e supporto di calibrazione
Suite software di programmazione di parti CAM
Formazione per operatori, meccanici e programmatori
Caratteristiche opzionali
Effettore finale per estrusione di pellet di plastica ad alta produttività, per depositare rapidamente strumenti di supporto di grandi dimensioni da materie prime economiche
Attuatore finale di lavorazione sottrattiva, per il taglio di parti e il condizionamento delle superfici degli utensili di supporto per una finitura e una precisione ottimali
Sistema di strumenti di supporto parzialmente riutilizzabile che incorpora uno strato sacrificale idrosolubile per brevi cicli di produzione