Ricorderemo questo giorno’ – Stratasys sul lancio delle nuove stampanti 3D SAF, P3 e FDM
“Non ci sono offerte paragonabili oggi.
“Questa è una rivoluzione.
“Questo è il vero affare.
“E ricorderemo questo giorno.”
Queste sono state le conclusioni a cui è arrivato il CEO di Stratasys Yoav Zeif quando la società ha annunciato il lancio della sua macchina F770 FDM, una versione aggiornata di Origin One e del sistema H350 alimentato da SAF, rispettivamente. Ha aperto una conferenza stampa virtuale, con la partecipazione di diversi dipendenti e clienti di Stratasys, che presentavano ogni prodotto, ne dettagliavano le capacità e offrono approfondimenti dagli utenti finali.
Ha agito come la presentazione ufficiale di quello che Stratasys ora ritiene essere il miglior portafoglio di stampa 3D polimerica in circolazione. Con prodotti progettati per produrre prototipi funzionali in multicolore, a macchine più adatte alla produzione di componenti per utensili, a sistemi destinati ad applicazioni di produzione di massa, Stratasys ritiene di avere ora l’offerta più completa nel campo dei polimeri. E c’è la certezza che l’azienda accelererà la maturazione della stampa 3D come tecnologia di produzione.
“Queste nuove tecnologie serviranno alla nostra ulteriore espansione e alla crescita dei nostri ricavi nelle applicazioni di produzione”, ha dichiarato a TCT Andy Langfeld, Presidente di Stratasys EMEA, dopo la conferenza stampa. “Con il portafoglio storico che avevamo, c’erano dei limiti alla scala. Sebbene stiamo ancora aumentando l’adozione di Polyjet e FDM, abbiamo riconosciuto che richiede un nuovo set di tecnologie per espandersi di nuovo in più applicazioni di grado di produzione con volumi più elevati, entrando anche in applicazioni che sostituiscono parti di stampaggio a iniezione “.
In prima linea in questa ambizione c’è la tecnologia SAF, etichettata nella conferenza stampa come una delle due tecnologie Stratasys in grado di consentire applicazioni di produzione di massa. Ha trovato la sua strada nel business di Stratasys tramite una joint venture con Xaar 3D, una divisione di Xaar in cui Stratasys detiene attualmente una partecipazione del 45% e ha la possibilità di assumerne il pieno controllo . La società ha annunciato il mese scorso che avrebbe lanciato una linea di macchine basate sulla tecnologia e questa settimana ha presentato la H350 come la prima della sua serie SAF.
SAF, o Selective Absorption Fusion, utilizza testine di stampa che si spostano da sinistra a destra sul letto di polvere per depositare un fluido assorbente sulla polvere, seguita rapidamente da una lampada a infrarossi per irradiare la superficie e fondere le particelle di particelle. Un rullo rotante spinge quindi lo strato successivo di polvere sulla parte superiore, con le parti che si accumulano man mano che il ciclo si ripete. A differenza di altre piattaforme di fusione a letto di polvere che utilizzano i laser per fondere insieme le particelle, l’architettura del processo SAF garantisce che tutte le particelle di polvere sperimentino gli stessi profili di temperatura e siano fuse allo stesso tempo. Sebbene ciò rallenti le velocità di stampa di cui sarebbe capace SAF, si traduce in un processo di stampa più coerente, qualcosa che Hopkinson è stato felice di dare la priorità.
“C’è un piccolo costo in termini di velocità e produttività”, ha detto Hopkinson, “ma pensiamo che sia un prezzo che vale la pena pagare perché se si ottiene una maggiore coerenza, si ottiene una maggiore resa dalle parti e l’economia si accumula molto meglio con una maggiore coerenza che forse andando a grande velocità. La coerenza ne è il cuore “.
Sebbene SAF sia in fase di sviluppo da oltre un decennio, negli ultimi anni Hopkinson e il suo team si sono concentrati intensamente sull’eliminazione delle incongruenze nel processo prima del suo lancio sul mercato. Il sistema di polvere Big Wave è un altro aspetto di questo. Tipicamente durante un processo di fusione del letto di polvere, la polvere che viene depositata sulla parte superiore del letto è più fredda della polvere ora sotto di esso, ma Big Wave mantiene uno stampo termicamente stabile di polvere con il materiale traboccante che viene rapidamente ricircolato per ridurre al minimo l’esposizione termica e la polvere invecchiamento.
Il livello di controllo che SAF ha sulla termodinamica, così come l’elevata riciclabilità della polvere, consente inoltre agli utenti di imballare le parti più densamente nel volume di costruzione. Le parti possono essere posizionate più vicine tra loro senza riscaldare la polvere inutilizzata in modo così aggressivo, e questo significa che gli utenti possono aumentare la loro produttività. Sono queste capacità che hanno convinto Stratasys ad aggiungere la tecnologia al suo portafoglio e perché Zeif l’ha descritta come il “ vero affare ” all’inizio di questa settimana, ma SAF non è solo pronta per il ridimensionamento dei volumi di produzione, ma può anche negoziare funzionalità di qualità e grandi anche disegni piatti.
“Questo è qualcosa di cui sono particolarmente orgoglioso”, dice Hopkinson. “Nelle tecnologie di fusione a letto di polvere, in particolare quando si realizzano grandi aree piane, può essere difficile perché nel momento in cui si è riscaldato [le particelle] iniziano a raffreddarsi. E se si raffreddano troppo, in particolare quando mettono il successivo strato di polvere sopra, possono deformarsi. E poiché il tempo tra la fusione e la deposizione dello strato successivo è lo stesso nel nostro sistema, non abbiamo aree in cui ci sia molto tempo tra quella fusione e la deposizione. Ciò rende istantaneamente le nostre parti meno soggette al raffreddamento che porta a questo fenomeno noto come arricciatura.
“Abbiamo avuto i nostri clienti che guardavano [parti] semplicemente sbalorditi dal fatto che questa grande area piatta venga prodotta senza alcuna indicazione di sollevamento, cosa che si aspetterebbero di vedere”, afferma Hopkinson. “È stato molto gratificante per me, perché è la prova che il nostro concetto di controllo termico funziona perfettamente.”
Come risultato del suo concetto di controllo termico, l’azienda si è sentita incoraggiata a presentarsi sul mercato con una polvere PA11 come primo materiale disponibile. La polvere PA11 è una plastica a base biologica composta da materie prime rinnovabili derivate dall’olio di ricino e si dice che abbia un impatto ambientale inferiore e una resistenza termica superiore rispetto al PA12, pur essendo meno fragile. Ha anche superato i test ISO 10993-5 per la citotossicità e UL94 HB per l’infiammabilità. Materiali aggiuntivi, come elastomeri e tecnopolimeri, sono in fase di sviluppo in collaborazione con fornitori di terze parti e saranno annunciati quando saranno pronti per l’uso.
Essendo in azienda da 12 anni, posso solo tornare indietro a quei 12 anni, ma per me è davvero il giorno più emozionante.
Più opzioni di materiali apriranno opportunità di applicazione e Hopkinson afferma che fin dall’inizio del progetto di sinterizzazione ad alta velocità, questa è stata vista come una “soluzione di produzione”. Ciò non solo ha portato Hopkinson ei suoi colleghi a concentrarsi sulla coerenza e la produttività, ma ha anche influenzato le loro idee sul modello di business. In quanto tali, le testine di stampa sono di livello industriale e non sono qualcosa che si aspettano di essere cambiate come una questione di routine. Ciò riduce il costo di sostituzione delle parti, rende i costi più prevedibili ed è utile per i produttori di settori come quello aerospaziale.
“Ne siamo stati molto consapevoli sin dall’inizio, quando i clienti stanno cercando di realizzare una produzione certificata, avranno una configurazione e la configurazione include cose come il monitoraggio dei materiali e quale testina di stampa è nella macchina”, ha spiegato Hopkinson. “Se si cambiano quelle testine di stampa, è necessario riconfigurare e ripetere l’intero processo da capo. E poi questo è un costo aggiuntivo che devi ammortizzare nell’intero processo di produzione “.
Dopo aver intrapreso questi passi, Hopkinson e Stratasys credono di portare sul mercato uno strumento di produzione di massa in buona fede. Questa convinzione è stata confermata durante il beta test della macchina in cui i fornitori di servizi di produzione, come Götz Maschinenbau in Germania, hanno implementato l’H350 per produrre parti in volumi di produzione medio-bassi, accettando ordini di migliaia di componenti.
È per questo che Stratasys si è rapidamente posizionata in prima fila per aiutare a commercializzare la tecnologia che ora conosciamo come SAF. Dopo averlo integrato nel portafoglio di prodotti, l’azienda ha messo in atto investimenti in ricerca e sviluppo, come ha fatto con tutte le tecnologie in arrivo, per alimentare lo sviluppo di stampanti e materiali. E, con una partecipazione del 45% in Xaar 3D, si prevede che Stratasys assumerà presto il pieno controllo.
“Stiamo lavorando in modalità joint venture con noi per portare il prodotto sul mercato e tutti gli altri passaggi verranno annunciati una volta finalizzati”, afferma Langfeld. “Quando Xaar plc ha pubblicato i risultati [finanziari], ha annunciato discussioni avanzate per cedere Xaar 3D o l’investimento 3D. Ecco dove siamo nelle discussioni. E quando avremo notizie, le condivideremo “.
Mentre la notizia della macchina H350, che verrà spedita nel terzo trimestre del 2021, procede a qualsiasi acquisizione formale di Xaar 3D, il lancio di una piattaforma Origin One migliorata segue un accordo di acquisizione concluso lo scorso anno . I 100 miglioramenti del design che sono stati apportati a Origin One sono i primi risultati di questa fusione e includono un aumento del volume di costruzione nell’asse Z, velocità di stampa più elevate del 10-30%, una migliore facilità di manutenzione e una migliore ergonomia. Gli aggiornamenti software saranno disponibili per gli utenti esistenti tramite il cloud una volta che il nuovo Origin One inizierà la spedizione nel quarto trimestre del 2021.
“Stratasys ha dato al team di Origin l’opportunità di accelerare il lancio di questa straordinaria tecnologia per trasformare veramente la produzione in tutti i settori, dai prodotti dentali a quelli industriali”, ha commentato Chris Prucha, VP di P3 ricerca e sviluppo e gestione dei prodotti presso Stratasys. “In effetti, sta già accadendo, con feedback positivi dei clienti e indicazioni molto forti della domanda”.
La piattaforma Origin One è già stata utilizzata per stampare un milione di componenti e Stratasys prevede che questi miglioramenti consentiranno agli utenti della tecnologia di implementare la tecnologia P3 per la produzione di massa. TE Connectivity , che utilizza la stampa 3D dagli anni ’90, cita Origin One come una tecnologia che le ha permesso di “abbracciare la produzione in serie di migliaia e decine di migliaia di parti”. In qualità di azienda che produce 192 miliardi di parti all’anno per una varietà di settori, si appoggia a Origin per affrontare tirature di produzione a basso volume e alto mix. Tra le applicazioni c’è un supporto per connettori progettato per aiutare i connettori all’interno degli aeroplani a rimanere accoppiati. Questa è la prima parte di produzione aerospaziale stampata in 3D dell’azienda, ma si aspetta che non sarà l’ultima.
“Ci siamo concentrati sul laser per soddisfare rigorosi criteri di accuratezza e ripetibilità per i connettori che richiedono una precisione del micron a due cifre”, ha commentato Mark Savage, Global Center of Excellence Leader e Senior Manager di AM presso TE, che si è detto ‘sbalordito’ dalla tecnologia P3 alla conferenza stampa virtuale all’inizio di questa settimana. “Stratasys e Origin sono stati ottimi partner nell’aiutarci a raggiungere questi obiettivi e nel dimostrare le possibilità di utilizzare la produzione additiva su scala di decine di migliaia di parti. Riteniamo che questo contribuisca a rendere TE Connectivity un partner più agile ed economico per molti dei principali OEM mondiali nei settori dall’automotive all’aerospaziale agli elettrodomestici, mentre lavoriamo per costruire un futuro più connesso “.
A completare la serie di lanci di prodotti di Stratasys è stata la macchina F770, con la camera di costruzione completamente riscaldata più lunga sul mercato a 46 pollici sulla diagonale. Con un prezzo inferiore a $ 100.000, l’F770 è disponibile con materiali ASA avorio o ABS-M30 nero ed è dotato di un volume di costruzione di 1000 x 610 x 610 mm. È adatto per la produzione di grandi maschere e attrezzature, grandi prototipi funzionali e grandi vassoi di piccole parti di produzione. Sub-Zero Group , un produttore di elettrodomestici di lusso, è stato un cliente beta per l’F770 e si dice che abbia ottenuto risparmi sui costi tra il 30 e il 40% producendo internamente parti di grandi dimensioni.
“Man mano che il mercato si sviluppa, si nota una mercificazione in alcune applicazioni. Ed è qui che è necessario offrire capacità sufficienti a un prezzo accettabile “, ha affermato Langfeld. “Ciò che stiamo abilitando con questa piattaforma sono ancora strumenti di grandi dimensioni, ma se lo guardi dal punto di vista degli investimenti, dal punto di vista del cliente e anche dei costi di esercizio e del costo per parte, è un punto di svolta che sta chiudendo un divario. Se lo confronti con altre piattaforme di grandi dimensioni che abbiamo, non è confrontabile in base alle applicazioni. Se prendi un F900, ti piacciono di più le parti di uso finale di livello industriale che sono certificabili, dove hai la ripetibilità. Non puoi davvero confrontarlo. “
Questi tre lanci si uniscono per aiutare a rappresentare quello che Stratasys ha definito il portafoglio di stampa 3D polimerico più completo disponibile. E se la profondità delle serie PolyJet e FDM è qualcosa su cui basarsi, ci saranno molte altre stampanti stereolitografiche SAF, P3 e RPS NEO in arrivo. La missione dell’azienda è garantire che possa affrontare il maggior numero possibile di sfide che i produttori di parti in polimero devono affrontare. Si sta sforzando di replicare la reputazione che si è costruita fornendo strumenti per la prototipazione rapida e componenti di attrezzamento nella produzione di massa. Ed è per questo che l’azienda ritiene che il lancio di queste tre macchine sia un giorno da ricordare.
“Essendo in azienda da 12 anni, posso solo tornare indietro a quei 12 anni, ma per me è davvero il giorno più emozionante sotto molti aspetti”, ha concluso Langfeld. “Quando si esamina la strategia dell’azienda e dove vogliamo andare, ora c’è la narrazione della produzione 2.0. Ma se conti fino a due, devi superare uno. Siamo stati in questo spazio in cui tutto questo era prototipazione e quando ho iniziato, ho visto parti e ho pensato, chi diavolo le sta usando? E ora vedi parti che volano su un Airbus A350, vedi parti utilizzate in chirurgia dal vivo, vedi che l’interruzione della catena di fornitura viene davvero affrontata con la produzione additiva. [Questi lanci], è una trasformazione per noi come azienda, ma sta anche consentendo la trasformazione dei mercati e del modo in cui i clienti producono le cose “.
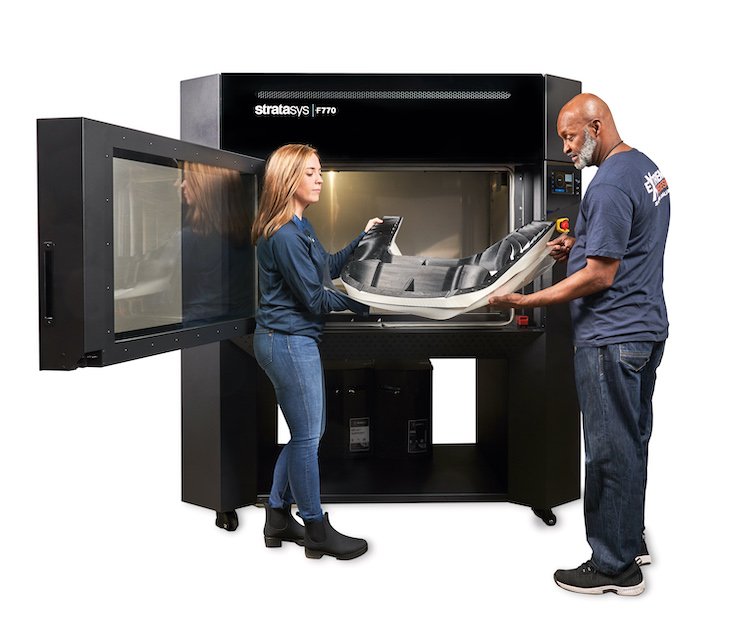