Questa azienda sta rivoluzionando la produzione additiva con gli ultrasuoni
Cosa c’è di diverso nella tecnologia UAM brevettata da Fabrisonic?
La stampa 3D sta entrando nel suo quarto decennio , con molte nuove tecnologie in fase di sviluppo. Attualmente, il più popolare tra questi è la modellazione a deposizione fusa (FDM), nota anche come fabbricazione di filamenti fusi (FFF), un metodo rapido ed economico per la produzione di modelli fisici.
Tuttavia, FDM produce parti che mancano di resistenza e hanno finiture superficiali relativamente ruvide. Il dettaglio delle stampe finite è limitato dalla dimensione dell’ugello, quindi la tecnologia non è in grado di fornire finiture con dettagli più elevati. Inoltre, la resistenza delle parti finite è limitata perché ogni strato è unito allo strato sottostante. Questo vale anche per altre forme di stampa 3D come la sinterizzazione laser selettiva (SLS), la stereolitografia (SLA) e altri processi.
Entra in Fabrisonic e nella sua esclusiva tecnologia di produzione additiva ad ultrasuoni (UAM). Engineering.com ha incontrato il CEO Mark Norfolk per discutere di come è nata l’idea, cosa la rende diversa, le sue applicazioni e i suoi limiti e cosa riserva il futuro per l’azienda.
Che cos’è la produzione additiva ad ultrasuoni?
Fabrisonic è stata costituita nel 2011 per consolidare la proprietà intellettuale di Edison Welding Institute (EWI) e Solidica, una società a scopo di lucro con sede nel Michigan. “La loro missione sociale è creare nuove tecnologie di produzione”, afferma Norfolk. “Quello che stavano guardando è, come saldiamo più strati di lamina di metallo per creare qualcosa?”
Quando è nata quella tecnologia, è stata ulteriormente sviluppata in una tecnica di stampa 3D, culminata nella prima macchina di Fabrisonic, la SonicLayer 7200. Il suo successo ha portato allo sviluppo di una macchina più piccola, la SonicLayer R200, e un modello di produzione di medie dimensioni, la SonicLayer 4000.
Fabrisonic controlla nove brevetti che coprono tutti gli aspetti di UAM. Norfolk spiega il processo: “Prendiamo fogli sottili nell’intervallo da 125 a 250 micron e li adagiamo. Li giriamo sopra con un dispositivo chiamato clacson. Mentre si ribalta, vibra a sinistra oa destra nell’ordine dei micron, come 20 micron”.
Le vibrazioni rimuovono lo strato di ossido dalle lamiere, consentendo loro di legarsi insieme a temperature inferiori a 200°F. “Quella vibrazione sta prendendo quei metalli e li sta sfregando”, dice Norfolk. “Ci permette di pulire la superficie del metallo, in modo da avere metallo pulito su metallo pulito. Metti un po’ di pressione lì e otterrai un legame a stato solido”.
Gli Emirati Arabi Uniti sono un processo ibrido, in cui tutti i sistemi sono mulini CNC a cui è stata aggiunta la capacità di saldatura. “In questo modo possiamo saldare per un po’, fresare per un po’, saldare per un po’, fresare per un po’”, dice Norfolk.
UAM esegue la saldatura ad ultrasuoni su base semicontinua in cui oggetti metallici solidi vengono costruiti in una forma tridimensionale attraverso una successione di nastri metallici saldati. Attraverso operazioni di lavorazione periodiche, le caratteristiche dettagliate vengono fresate nell’oggetto fino a creare una geometria finale rimuovendo il materiale in eccesso. UAM combina i vantaggi degli approcci di fabbricazione additiva e sottrattiva per consentire la formazione di parti 3D con elevata precisione, superfici lisce e passaggi interni complessi.
Come mostrato nella figura che segue, la macchina è costituita da un sistema di saldatura ad ultrasuoni rotante composto da due trasduttori ad ultrasuoni da 20.000 Hz e dal sonotrodo di saldatura. Le vibrazioni ultrasoniche ad alta frequenza vengono applicate localmente su lamine metalliche e tenute insieme sotto pressione per creare una saldatura. Le vibrazioni del trasduttore vengono trasmesse al sonotrodo di saldatura a forma di disco, che a sua volta crea una saldatura ultrasonica allo stato solido tra il sottile nastro metallico e il substrato. Il continuo rotolamento del sonotrodo sulla piastra salda l’intero nastro alla piastra. Gli strati successivi vengono saldati insieme per aumentare l’altezza. Questo processo viene ripetuto fino a quando non viene creato un componente solido. La fresatura di contorni CNC viene quindi utilizzata per ottenere la forma e la finitura superficiale richieste.
Cosa differenzia l’UAM dalle altre tecnologie?
La natura allo stato solido è un vantaggio chiave delle saldature a ultrasuoni. “Il fattore chiave di differenziazione è che non ci stiamo sciogliendo”, afferma Norfolk. “Se fondete un metallo e lo risolidificate, cambiate totalmente la struttura del grano.” Ciò significa che le proprietà del materiale non vengono affatto modificate, il che aiuta a mantenerne l’integrità.
“Se fondi e risolidifica i metalli e mescoli due metalli diversi, ciò che risolidifica spesso non è desiderabile”, aggiunge Norfolk. “È tipicamente un intermetallico, che è molto fragile.”
Poiché il processo non utilizza la fusione, è possibile combinare metalli diversi, come il titanio con acciaio, Inconel o alluminio, e tutti nella stessa parte senza creare microstrutture dannose o metallurgia fragile indesiderabile. Il risultato è una parte con tutte le migliori proprietà dei diversi materiali. Ad esempio, strati di molibdeno e Invar possono essere stampati in uno scambiatore di calore in alluminio per adattarsi al coefficiente di espansione termica (CTE) di un circuito elettronico montato.
Un altro aspetto che distingue UAM è la sua capacità di incorporare elettronica e sensori. “Poiché non ci stiamo sciogliendo in nessun momento, possiamo fermarci, inserire un pacchetto di elettronica o un sensore per il monitoraggio della salute e quindi continuare a saldare sopra di esso”, afferma Norfolk. Fabrisonic è stata in grado di incorporare con successo molti componenti elettronici in parti metalliche solide utilizzando UAM, inclusi microprocessori, sensori e telemetria.
Poiché i materiali sono solo leggermente riscaldati, non subiscono cambiamenti nella dimensione del grano, nelle reazioni di precipitazione o nei cambiamenti di fase. Le proprietà della materia prima in entrata sono le stesse della parte finale. Il legame a bassa temperatura consente inoltre di incorporare componenti delicati nel metallo solido senza i danni subiti in processi additivi a base di fusione comparabili.
Ci sono anche notevoli risparmi sui costi. “Succede tutto essenzialmente a temperatura ambiente”, afferma Norfolk. “Elimina la necessità di gas di protezione per il vuoto.”
L’intero processo viene eseguito in un ambiente aperto, riducendo i costi. I fogli di metallo sono anche facilmente disponibili in commercio. “Stiamo acquistando fogli di alluminio dal mercato aperto”, afferma Norfolk. “Stiamo pagando $ 6 la libbra per 6061, un comune alluminio aerospaziale per la forza lavoro”. In confronto, le polveri sono centinaia di dollari al chilo. L’economia aiuta Fabrisonic a realizzare parti particolarmente grandi.
Quali sono i limiti?
“Il nostro processo si basa su una certa forza”, afferma Norfolk. “Stiamo premendo con forse 500-1.000 libbre.” Di conseguenza, strutture delicate come i reticoli crollerebbe. Le geometrie devono essere più solide di qualcosa che si fa tipicamente su un letto di polvere.
Il processo utilizza anche le vibrazioni allo stesso tempo, quindi è necessario considerare la risonanza. “Un muro alto e magro con un rapporto altezza-larghezza di 0,8 ha una frequenza naturale di 20 kHz, che è dove stiamo mettendo la nostra energia”, dice Norfolk. “Caratteristiche così alte e magre, in genere ingrasseremo e poi macineremo alla fine”.
Ci sono varie applicazioni per la tecnologia.
Un grezzo saldato su misura. (Immagine per gentile concessione di Fabrisonic.)
“Un esempio è, come è noto nell’industria automobilistica, un grezzo saldato su misura”, afferma Norfolk. “Quello che stiamo facendo è aggiungere materiale solo nella regione che ha bisogno di rinforzo”.
La stampa 3D a stato solido può essere utilizzata per costruire materiale in regioni specifiche di prodotti in fogli per aumentarne la capacità di carico. L’aggiunta di materiale proprio dove è necessario si traduce in un risparmio sui costi di materiale ed energia, rispetto all’inizio con una lastra più spessa e alla fresatura. “Quindi, invece di acquistare una lastra da 3 mm, acquistano una lastra da 1 mm e noi stampiamo un ponte da 2 mm su di essa, quindi è davvero interessante dal punto di vista economico”.
Un nuovo entusiasmante approccio è un altro tipo di ibrido. “Alcune parti sono una combinazione di fusione a letto di polvere e additivo ad ultrasuoni”, afferma Norfolk. “Tra quindici anni avrai un sistema DED, un sistema UAM e un sistema a letto di polvere. Quindi, stiamo già esaminando come combinare processi additivi per ottenere la realizzazione più efficiente del desiderio di un cliente”.
Un esempio è il metallo multiprocesso. In primo luogo, gli ultrasuoni sono stati utilizzati per stampare il rame sull’alluminio perché era necessario un metallo diverso. “Ma il resto della geometria era alquanto fragile”, afferma Norfolk. “Quindi, abbiamo preso quella lastra che abbiamo stampato con la nostra tecnologia, l’abbiamo messa in un letto di polvere e abbiamo stampato il resto della geometria”.
Un’altra applicazione, già utilizzata dai clienti nella produzione, è l’elettronica incorporata. “Abbiamo incorporato estensimetri a fibra ottica nella piastra di base di un sistema a letto di polvere”, afferma Norfolk. “Se si lavora molto nel letto di polvere, si accumulano molte deformazioni residue che a volte complicano le build, provocando delaminazioni da quella sollecitazione residua”. Incorporando i sensori in quella piastra di base, i clienti ottengono i dati dall’accumulo nel loro letto di polvere mentre si accumulano. Ciò ha uno scopo aggiuntivo come strumento di qualità live per il letto di polvere.
Tecnologia di nicchia
Esistono altri processi allo stato solido che non comportano la fusione. Questi si ottengono costruendo il metallo utilizzando meccanismi come l’attrito e la velocità, con i metodi più comuni tra cui la saldatura ad attrito, lo spray freddo, la laminazione della lamiera e un metodo alimentato dall’aria compressa dell’officina. Indipendentemente da ciò, i processi sono abbastanza diversi da non invadere le reciproche aree.
Indubbiamente, la tecnologia UAM di Fabrisonic è ancora in fase nascente. L’azienda dovrà affrontare problemi iniziali come tutte le nuove tecnologie. Tuttavia, ha suscitato scalpore nel mercato e sembra essere qui per restare.
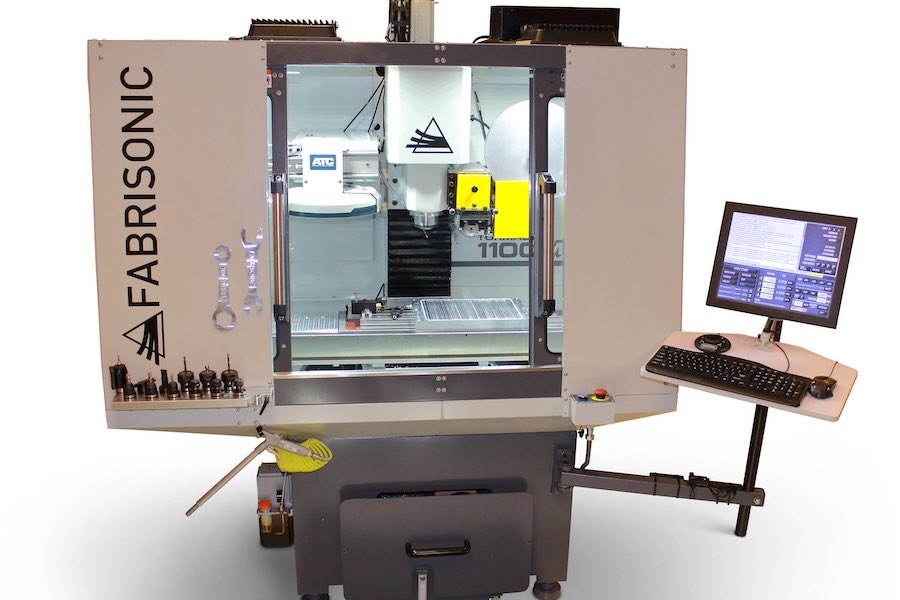