Avevano un obiettivo ambizioso: industrializzare la produzione additiva sia per gli OEM che per le PMI. Per raggiungerlo, i partner dell’industria insieme agli Istituti Fraunhofer per la tecnologia laser ILT e per la tecnologia di produzione IPT e la RWTH Aachen University hanno lanciato tre anni fa il progetto congiunto BMBF “IDEA – Industrializzazione dell’ingegneria digitale e della produzione additiva”. Nell’ambito del progetto, hanno costruito due linee di produzione additiva automatizzate per la stampa 3D in metallo con prestazioni esemplari per produrre potenti componenti di fascia alta come quelli per le turbine a gas. E lo hanno fatto con successo: a Berlino e Georgensgmünd, i componenti metallici sono stati recentemente prodotti con la stampa 3D, dimostrando come non solo le grandi aziende, ma anche le PMI possano produrre in modo additivo componenti personalizzati in lotti di medie dimensioni in modo economico.
© toolcraft AG.Capannone di produzione additiva presso Toolcraft a Georgensgmünd.
© Siemens Digital Industries.Pianificazione delle linee di produzione tramite Tecnomatix® Plant Simulation.
© Fraunhofer ILT, Aquisgrana, Germania.Dimostratore di un’aletta di guida per turbina prodotta con esposizione del contorno a onda continua (cw, sinistra) e pulsata (pw, destra) con risoluzione dei dettagli migliorata.
“La produzione in serie di componenti prodotti in modo additivo (AM) con la stampa 3D in metallo richiede troppo tempo, non può essere automatizzata ed è troppo costosa. Pertanto, solo i gruppi di tecnologia aerospaziale o medica possono permettersi questo lusso”. Undici aziende industriali e quattro istituti di ricerca di Aquisgrana hanno confutato l’argomentazione esaminando la catena di processo AM nella sua interezza all’interno del progetto IDEA, completato nell’ottobre 2022. Finanziato nell’ambito della “Linea integrazione dei processi di produzione additiva (LAF)” del BMBF finanziamento, il consorzio del progetto ha sviluppato una linea di produzione pilota industriale su larga scala presso l’impianto di turbine a gas Siemens Energy a Berlino e una linea di produzione per le PMI presso la toolcraft AG di Georgensgmünd. Il gemello digitale della fabbrica, sviluppato per le PMI e la produzione in serie su larga scala,
Siemens Energy e toolcraft: lezione appresa per ulteriori passi
Dopo aver sviluppato e implementato intensamente molti sottoprocessi lungo la catena di produzione additiva, i partner hanno creato due linee di produzione automatizzate e modulari per dimostrare la maturità della produzione additiva come tecnologia di produzione industriale. Ciò incoraggerà le aziende manifatturiere a utilizzare la produzione additiva digitale nella produzione in serie. Il feedback positivo degli operatori delle linee dimostra che i singoli prodotti di media serie possono essere prodotti in serie utilizzando Laser Power Bed Fusion (LPBF). Secondo Julius Schurb, responsabile del progetto IDEA, dell’impianto di turbine a gas Siemens Energy di Berlino: “Siamo stati in grado di dimostrare per il nostro componente dimostrativo, un’aletta di guida della turbina, che le riduzioni pianificate dei tempi di sviluppo e di produzione di circa il 50% possono essere ottenute adottando una visione olistica della catena di produzione dalla progettazione al prodotto finito. Questi risultati ci consentiranno di far progredire ulteriormente l’industrializzazione della produzione additiva e di offrire componenti chiave delle nostre turbine a gas a costi competitivi, anche in piccole quantità”.
Tuttavia, la stampa 3D metallica non è solo un’opzione per le grandi aziende, ma anche per le piccole e medie imprese. Questa affermazione può essere supportata da Toolcraft, un’azienda di medie dimensioni che utilizza processi di produzione additiva per la produzione in serie. Questa azienda è specializzata nella produzione di utensili e parti stampate a iniezione, nonché componenti e assiemi di precisione per l’industria aerospaziale, l’industria dei semiconduttori e la tecnologia medica.
“Nel progetto IDEA, siamo riusciti a completare importanti fasi di sviluppo, tra cui la possibilità di mappare meglio una catena di produzione integrata, end-to-end, composta da sottoprocessi”, sottolinea Markus Langer, responsabile della trasformazione digitale / tecnologia e sviluppo Promozione su toolcraft. Fornisce una panoramica dei risultati del progetto: “Le fasi di lavoro manuali sono state sostituite da soluzioni di automazione, che ci hanno aiutato a raggiungere una maggiore stabilità e qualità del processo. Per utilizzare virtualmente i dati reali, dobbiamo anche evidenziare la digitalizzazione, che deve essere considerata a livello globale per la produzione di componenti fabbricati in modo additivo. Era anche importante, ad esempio, utilizzare gli occhiali VR per trasferire i dati analogici, come ulteriormente sviluppato in IDEA, ai piani di lavoro digitali, per lavorare e testare le istruzioni e la formazione interattiva.
Collaborazione interdisciplinare: raggiungere l’obiettivo insieme
La composizione interdisciplinare del team del progetto IDEA ha riunito esperti in turbomacchine, digitalizzazione, automazione, tecnologia aeronautica, post-elaborazione, tecnologia di stampa laser e 3D, tra gli altri: questa combinazione si è rivelata un fattore chiave per il successo del progetto. Gli utenti non dovevano ricominciare da capo il progetto. Ciò è stato assicurato, ad esempio, dagli esperti del Fraunhofer ILT di Aquisgrana, che hanno contribuito al consorzio con la loro esperienza nel campo della LPBF sviluppata in precedenti progetti di ricerca.
Qualità dei componenti sotto controllo con il controllo di processo
Thomas Laag, ricercatore associato presso Fraunhofer ILT, spiega l’importanza del controllo di processo: “Poiché l’industria aerospaziale ha standard di sicurezza molto elevati, l’applicazione della fusione del raggio laser affonda o nuota con un’intensa garanzia di qualità lungo la catena di processo. All’interno di IDEA, i partner si sono concentrati in particolare sul monitoraggio basato su regole delle condizioni della polvere, sulla solida qualificazione del processo di macchine multi-laser e sull’ulteriore sviluppo di soluzioni per il monitoraggio automatizzato del processo. Fraunhofer ILT ha sviluppato un sistema di controllo del processo con radiazione laser pulsata per LPBF, un sistema che può migliorare la risoluzione dei dettagli e prevenire meno deviazioni di forma. Riduce anche lo sforzo richiesto per la post-elaborazione e rende possibile, ad esempio, la produzione di geometrie complesse che hanno non solo una maggiore risoluzione dei dettagli,
Inoltre, presso il Fraunhofer ILT è stato sviluppato e valutato un nuovo sistema di monitoraggio delle immagini. Una telecamera stereo ad alta risoluzione può rilevare le instabilità del processo come la distorsione dei componenti o i difetti del letto di polvere. Poiché il sistema di telecamere è montato sul verniciatore, in linea di principio può essere installato anche su macchine esistenti. In collaborazione con il partner Jenoptik, Fraunhofer ILT ha dimostrato una valutazione basata sull’intelligenza artificiale dei dati di misurazione.
Focus sull’intera catena di processo fisico e digitale
Nonostante le loro diverse mansioni, le due linee di produzione hanno molte cose in comune. L’obiettivo di IDEA era quello di trasformare digitalmente l’intera catena di processo sotto il titolo dell’ingegneria digitale: l’automazione mirata, in combinazione con i gemelli digitali e i moderni sistemi di controllo del prodotto, garantisce che tutti i dati di produzione rilevanti vengano registrati e utilizzati continuamente. Le linee differiscono quindi in modo significativo dai sistemi di stampa 3D convenzionali poiché questi ultimi hanno fasi di processo ampiamente isolate e richiedono molti interventi manuali, entrambi i quali possono facilmente portare a una produzione “per tentativi ed errori” e costi elevati dei componenti.
“Nel campo della produzione additiva, il gemello digitale sta rivoluzionando i processi lungo l’intera catena del valore”, sottolinea il dott. Karsten Heuser, vicepresidente della produzione additiva presso Siemens Digital Industries. “Come immagine virtuale del componente additivo, del processo di produzione o delle prestazioni, ci consente di collegare senza soluzione di continuità le singole fasi del processo. Utilizzando il gemello digitale, potremmo aumentare costantemente l’efficienza delle due linee industriali, ridurre al minimo il tasso di errore e abbreviare i cicli di sviluppo”.
Una particolarità di entrambe le linee di produzione è la mappatura sia fisica che digitale della catena di processo additiva. Ciò include metodi di misurazione automatizzati per il monitoraggio della geometria dei componenti, la riparazione additiva delle palette di guida delle turbine e la finitura automatizzata di componenti prodotti in modo additivo.
Fraunhofer ILT al formnext 2022
Le parti interessate possono scoprire di più sulle attuali attività di ricerca di ILT in LPBF al formnext 2022 a Francoforte sul Meno dal 15 al 18 novembre 2022, presso lo stand B32 di Fraunhofer ILT nel padiglione 11.0. Secondo Laag, “Mostreremo vari spunti interessanti sui nuovi sviluppi e applicazioni della tecnologia LPBF”.
Il progetto “IDEA – Industrializzazione dell’ingegneria digitale e della produzione additiva”, che va dal 1 aprile 2019 al 31 ottobre 2022, è stato finanziato dal Ministero federale tedesco dell’Istruzione e della ricerca BMBF (Photonik Forschung Deutschland). IDEA fa parte dell’iniziativa “Integrazione di linea dei processi di produzione additiva (LAF)”, finanziata con 27,5 milioni di euro.
Partner del progetto:
Siemens Energy (Berlino, leader del consorzio), Siemens Digital Industries (Norimberga), MTU Aero Engines AG (Monaco di Baviera), toolcraft AG (Georgensgmünd), Liebherr-Aerospace Lindenberg GmbH (Lindenberg im Allgäu), TRUMPF Laser- und Systemtechnik GmbH (Ditzingen) , EOS GmbH Electro Optical Systems (Krailing), Jenoptik Industrial Metrology Germany GmbH (Villingen-Schwenningen), BCT Steuerungs- und DV-Systeme GmbH (Dortmund), ModuleWorks GmbH (Aachen), Allmatic-Jakob Spannsysteme GmbH (Unterthingau), Chair for Produzione additiva digitale DAP, RWTH Aachen University (Aachen), Machine Tool Laboratory (WZL), RWTH Aachen University (Aachen), Fraunhofer Institute for Laser Technology ILT (Aachen), Fraunhofer Institute for Production Technology IPT (Aachen).
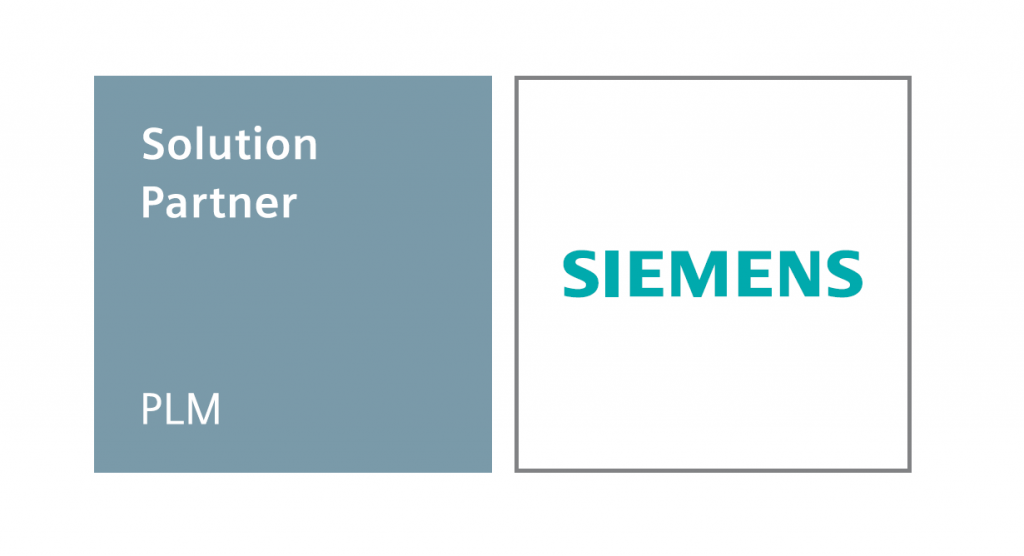