Royal Dutch Navy, Ultimaker e Covestro testano la forza della parte stampata in 3D sollevando un carro armato da 12 tonnellate
Gli ingegneri hanno adottato un approccio non convenzionale per testare la forza di una parte in plastica stampata in 3D di due chilogrammi contro un veicolo blindato, 6000 volte più pesante
Quando gli ingegneri vogliono misurare la resistenza di un materiale, in genere lo fanno utilizzando una macchina per prove di trazione. Un piccolo campione viene stampato e sottoposto a una grande forza finché non scatta. La forza proiettata sulla parte divisa per la superficie del centro di intersezione al momento della rottura ne esprimerà la forza.
Ma per i team di Ultimaker, Covestro e della Royal Dutch Navy, hanno deciso di adottare un approccio non convenzionale per comprendere appieno quanto possano essere forti le parti stampate in 3D. E per illustrare meglio il loro test, avevano bisogno di sollevare qualcosa di pesante. Ma cosa funzionerebbe? Pesi da palestra? Una motocicletta? Un’automobile? Forse una grossa jeep? E poi la Royal Dutch Navy ha chiesto: “Perché non un veicolo blindato?”
Progettare la parte giusta per il lavoro giusto
Per sollevare un veicolo pesante utilizzando una parte stampata in 3D, gli ingegneri dovevano prima analizzare l’hardware. La Royal Dutch Navy aveva a sua disposizione uno speciale serbatoio di sollevamento che utilizzava due anelli di acciaio apribili per il collegamento alla propria gru e ai cavi attaccati al veicolo sollevato. Un collegamento allungato a forma di O sarebbe in grado di collegare questi due anelli di metallo e sollevare il veicolo pesante.
Dopo aver importato la geometria degli anelli d’acciaio nel software CAD, l’ingegnere applicativo di Ultimaker Lars de Jongh è stato in grado di creare il progetto iniziale per il collegamento. Affinché il design funzionasse, il collegamento richiedeva un lato piatto per una stampa 3D stabile e doveva essere stampato con linee di livello nella stessa direzione delle forze proiettate sulla parte. Inoltre, la superficie di interazione tra la parte stampata e gli anelli di metallo dovrebbe essere la più ampia possibile per distribuire le forze in modo uniforme.
Una volta completato il progetto, gli ingegneri avevano bisogno di un materiale che fosse estremamente resistente e in grado di assorbire brevi picchi di forza. Passando attraverso Ultimaker Marketplace, che è pieno di centinaia di materiali, ciascuno con una combinazione unica di proprietà, sono arrivati su Addigy® F1030 CF10 di Covestro carbo, che soddisfaceva i requisiti stabiliti. Questo polimero a base di nylon è caricato con fibra di carbonio e può essere stampato utilizzando Ultimaker S5 e il print core CC.
Misura due volte, taglia una
volta. Per stampare in 3D un solido collegamento da 2 chilogrammi, occorre meno tempo rispetto a produrlo con i metodi tradizionali. Tuttavia, il numero di iterazioni necessarie per convalidare la giusta geometria significava che il tempo era ancora un fattore determinante. Ecco perché il design è stato ottimizzato prima della stampa utilizzando simulazioni al computer.
Covestro ha applicato digitalmente le forze sul progetto utilizzando un software che conosce le esatte proprietà fisiche del suo materiale in nylon in fibra di carbonio. Eseguendo simulazioni, gli ingegneri sono stati in grado di identificare dove era necessario adattare il progetto e dove era possibile rimuovere il materiale. Ciò ha creato un design ottimizzato che potrebbe sollevare più peso, pur richiedendo meno materiale, con conseguente tempi di produzione più rapidi con meno costi.
Prima di poter sollevare il veicolo pesante, gli ingegneri dovevano verificare fisicamente la resistenza calcolata della parte stampata. Sono stati generati due modelli per due dimensioni. Il primo era un collegamento di 1 chilogrammo che si stima potesse resistere a 12 tonnellate. Si stima che il secondo del peso di circa 3 chilogrammi fosse in grado di resistere a 38 tonnellate. La Royal Dutch Navy dispone di un tester di trazione industriale in loco in grado di proiettare fino a 343 kilonewton di forza su un oggetto. Sono state testate sia la versione iniziale che quella ottimizzata, per la versione grande e piccola.
La differenza tra i risultati testati e i numeri simulati era estremamente vicina, essendo in media solo l’1% di sconto. Ciò ha reso questo flusso di lavoro accurato e redditizio in termini di time-to-market e prestazioni migliorate.
Sollevare veicoli militari con parti in plastica stampate in 3D
Dopo diversi mesi di progettazione, stampa, test e pianificazione, era tempo di agire. Due collegamenti stavano per sollevare un veicolo pesante militare. In una base dell’esercito olandese nel sud dei Paesi Bassi, la 13a brigata di rinoceronti leggeri ha assistito le squadre con il loro veicolo corazzato da recupero. Il loro Leopard 2 “Buffalo” ha una gru montata sulla parte anteriore ed è progettato per recuperare veicoli pesanti come camion e carri armati.
Come riscaldamento, il collegamento da 1 chilo è stato utilizzato per sollevare una versione militare di una jeep Mercedes del peso di oltre due tonnellate. Questo non è stato affatto un problema e il veicolo è stato facilmente sollevato. Poi è arrivato il momento di qualcosa di più grande.
Il collegamento in nylon rinforzato con fibra di carbonio solido da 2 kg è stato posizionato tra il veicolo blindato M113 e la gru Buffalo. Gli anelli di metallo sono stati serrati in posizione e quattro cavi sono stati fissati dal gancio inferiore al veicolo. La gru ha iniziato lentamente a salire, mettendo in tensione i cavi e la parte stampata in 3D. Quindi, il veicolo da 12 tonnellate si è sollevato lentamente, in bilico sopra il suolo, appeso a un collegamento stampato in 3D. Il Buffalo girava, indietro, avanti, girandosi, ma il collegamento resisteva perfettamente.
La collaborazione ha prodotto un risultato di grande successo. Leggi l’intera storia e gli insegnamenti di questo test qui . Scopri altre applicazioni di stampa 3D per la Difesa clicca qui .
A proposito di Ultimaker
Ultimaker ha la missione di accelerare la trasformazione del mondo verso soluzioni flessibili, responsabilizzanti e sostenibili con una piattaforma che consente ai clienti di sfruttare diversi prodotti e servizi di stampa 3D.
Nel settembre 2022 Ultimaker ha annunciato di aver completato la fusione con MakerBot con sede negli Stati Uniti. Con il nuovo marchio UltiMaker, l’azienda mira a fornire hardware, software e materiali di stampa 3D facili da usare e accessibili per qualsiasi applicazione, guidando il settore verso uno stato futuro di produzione responsabile e sostenibile.



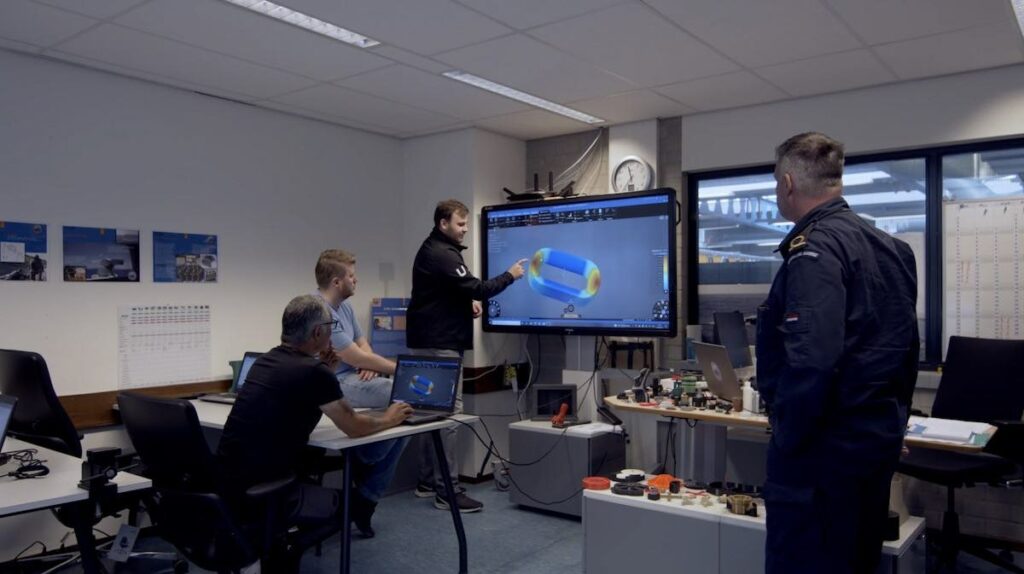