All’avanguardia nell’iper-velocità: Il prototipo di scramjet testa le capacità di manifattura additiva di Purdue
Presso il PARI Hypersonics Advanced Manufacturing Technology Center (HAMTC), un team del Purdue Applied Research Institute (PARI), nucleo di ricerca e sviluppo dell’università, sta impiegando attrezzature all’avanguardia per la manifattura additiva al fine di stampare un prototipo in scala reale e completamente funzionante di un motore scramjet (supersonic combustion ramjet). Questo tipo di motore consente aerei di raggiungere e superare la velocità di Mach 5.
I ricercatori del HAMTC ritengono che questa innovativa progettazione dello scramjet possa rendere i processi di prototipazione e produzione nell’industria ipersonica più accessibili e rapidi.
“Non esiste altra istituzione affiliata a un’università con la capacità di fabbricare e poi testare tecnologie ipersoniche in condizioni e scale rilevanti per il volo,” afferma Will DeVerter, assistente di ricerca laureato, che ha realizzato il prototipo di scramjet in scala reale con Nick Strahan, ingegnere senior dei test. “Una volta che abbiamo una parte o un sistema pronto, posso semplicemente attraversare la strada e testarlo con alcune delle migliori tecnologie di propulsione e diagnostica al mondo. Questa è una capacità unica che semplifica l’intero processo di fabbricazione e test.”
Strahan paragona la funzionalità dello scramjet all’accendere una candela in un uragano. “È necessario mantenere una fiamma in velocità dell’aria superiori a Mach 2, quindi la sfida tecnologica è creare un combustore che possa funzionare in modo efficiente e bruciare carburante con aria che viaggia a velocità molto elevate,” dice Strahan.
Mark Lewis, presidente e CEO del PARI, afferma che gli scramjet sono ancora agli inizi, “ma sono generalmente considerati il miglior modo per alimentare un missile o un aereo attraverso l’atmosfera a velocità superiori a cinque volte la velocità del suono, nel cosiddetto regno ipersonico.” Gli scramjet sono “molto semplici in principio,” dice Lewis, “ma estremamente complessi nella progettazione effettiva,” motivo per cui l’uso della manifattura additiva è stato una svolta.
Stampare e testare uno scramjet può essere costoso e richiedere molto tempo. La maggior parte dei laboratori di ricerca applicata con capacità di manifattura additiva può stampare solo versioni in scala ridotta per i test. Questi modelli sono poi utilizzati per creare scramjet in dimensioni reali, i cui pezzi devono essere stampati individualmente e poi assemblati. Tuttavia, utilizzando la tecnologia di fabbricazione avanzata disponibile presso il PARI, i ricercatori possono stampare modelli di produzione in scala reale e completamente operativi.
Il centro di manifattura additiva si trova nell’Hypersonics and Applied Research Facility del PARI e offre un punto di riferimento unico per le innovazioni manifatturiere che possono essere trasferite al mercato della difesa. Michael Sangid, direttore esecutivo dell’HAMTC e Professore Reilly di Aeronautica e Astronautica, afferma che il prototipo di scramjet in scala reale evidenzia il potenziale del centro di rivoluzionare l’industria ipersonica.
“Il progetto pilota dello scramjet è un ottimo esempio delle nostre capacità integrate verticalmente,” dice Sangid. “Possiamo trasformare la polvere grezza in dati di test rappresentativi da un prototipo sul campo in pochi mesi. Questo sfrutta la flessibilità della manifattura additiva nella progettazione del componente per aumentare l’efficienza.”
Il prototipo si distingue per la riduzione del peso e delle parti senza compromettere la funzionalità e la complessità geometrica necessaria affinché il motore funzioni. Questo sforzo è realizzato con il GE Concept Laser X Line 2000R, una stampante utilizzata per la manifattura metallica su larga scala. L’X Line 2000R impiega un processo chiamato fusione laser su letto di polvere, dove il laser nella stampante fonde e unisce le particelle per formare una parte solida. Grazie a questa capacità e alla grande capacità della stampante, sono necessarie meno parti per costruire il motore; ciò consente una prototipazione rapida con una maggiore complessità di progettazione e un montaggio semplificato.
Questo prototipo non solo utilizza le macchine del PARI ma funge anche da banco di prova per esperimenti e nuove tecnologie. Il centro di manifattura additiva è adiacente ai laboratori di propulsione Maurice J. Zucrow della Purdue University, tra i più grandi laboratori accademici di propulsione al mondo. Questo progetto integra le capacità di fabbricazione del PARI con le strutture di test di propulsione ad alta velocità di Zucrow, che possono simulare condizioni a Mach 5 e superiori, oltre a fornire diagnostiche basate su laser dei materiali ad alte velocità.
Un processo più veloce ed efficiente riduce infine i costi e contribuisce a soddisfare la richiesta nazionale per tecnologie ipersoniche più avanzate. David Bretz, manager senior del progetto, coordina tutti gli aspetti di questo progetto e ne vede il potenziale impatto sulla sicurezza nazionale e sull’industria della difesa.
“Grazie alla progettazione dello scramjet più veloce e meno costosa, saremo in grado di prototiparlo, testarlo e poi ritornare a iterare il design più facilmente, contribuendo così alla base di conoscenze ipersoniche della nazione e alle capacità aumentate,” dice Bretz. “Inoltre, gli studenti sono coinvolti in tutti gli aspetti del progetto, dalla progettazione al processo di fabbricazione ai test. Gli studenti della Purdue, dagli undergraduate ai livelli graduate, stanno imparando le competenze necessarie per lavorare nell’industria ipersonica.”
Carson Slabaugh, Professore Associato Paula Feuer di Aeronautica e Astronautica, e Sangid sono i leader accademici di questo progetto. L’efforto dello scramjet è uno dei cinque progetti finanziati dal Programma di Scienza e Tecnologia Manifatturiera dell’Office of the Secretary of Defense, in partenariato con il Naval Surface Warfare Center, Divisione di Crane, e l’acceleratore di tecnologie di sicurezza nazionale Strategic and Spectrum Missions Advanced Resilient Trusted Systems.
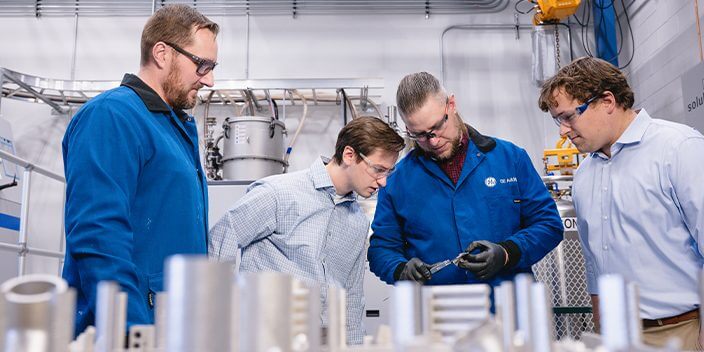
Will DeVerter, assistente di ricerca laureato in aeronautica e astronautica;
Gregg Lubas, ingegnere di elaborazione HAMTC;
Nick Strahan, ingegnere di test senior dell’HAMTC.
Qui esaminano le tolleranze dimensionali di una stampa X Line completata con calibri.
Questa stampante, utilizzata per la produzione di metalli su larga scala, è stata determinante nel lavoro scramjet del gruppo.
(Purdue/Charles Jischke)