Comunicato Stampa
XSPECTER unisce stampanti 3D SLA e SLS per realizzare un treppiede per fotocamera da esterno
Grazie a un’idea innovativa e tanta motivazione Matthias Mähler ha colmato un gap di mercato realizzando il primo prototipo di uno speciale treppiede per fotocamera per la visione notturna e dispositivi di imaging termico portatili.
Una delle sfide principali è stata quella di implementare un design di prodotto complesso, che avrebbe
richiesto un investimento iniziale di oltre 100.000 euro in attrezzature se avesse scelto lo stampaggio a
iniezione. Senza alcuna conoscenza preliminare di come il prodotto avrebbe funzionato sul mercato, questo sarebbe stato molto rischioso per una piccola startup. Utilizzando quindi la stampa 3D nello sviluppo e successivamente nella produzione del treppiede è stato possibile evitare questo investimento. Ora, la sua azienda, XSPECTER, produce internamente il suo primo treppiede per fotocamera T-Crow XRII che vende inesclusiva con un partner.
Sviluppo di un treppiede per fotocamera controllabile a 360°
I visori notturni e i dispositivi di imaging termico portatili sono apparecchiature standard per cacciatori e
impiegati anche nel settore della sicurezza, c’è però un limite, questi dispositivi infatti non funzionano
attraverso vetri. Quando si guida un’auto di notte, i conducenti devono tenere in mano il dispositivo fuori dal finestrino aperto oppure uscire dal veicolo.
Il cacciatore ricreativo e imprenditore Matthias Mähler si è messo alla ricerca di una soluzione adatta per
montare i suoi dispositivi all’esterno della propria auto.
Dopo aver realizzato che sul mercato non c’erano supporti o treppiedi adatti, l’imprenditore ha preso in
mano la situazione. Ha iniziato con la costruzione del prototipo di un treppiede stabilizzatore e controllabile per la visione notturna e dispositivi di imaging termico, che può essere montato sul tetto o sui vetri di un’auto tramite ventose o piedini magnetici.
T-Crow XRII con diverse telecamere sul finestrino dell’auto e sul tetto dell’auto
Con una rotazione integrata di 360° e una gamma di inclinazione aggiuntiva di 55°, il treppiede T-Crow di
XSPECTER consente di seguire comodamente animali e ostacoli dall’interno del veicolo.
Screenshot dell’immagine termica mostrata all’interno dell’abitacolo.
Dai prototipi alla produzione in serie
“La stampa 3D è stata integrata nella linea di produzione per la realizzazione dei prototipi. Ha funzionato
così bene che abbiamo finito per progettare l'intero prodotto utilizzando varie tecnologie di stampa 3D e ancora oggi lo produciamo così", afferma Mähler.
Innanzitutto, Mähler ha effettuato diversi prototipi del treppiede in collaborazione con fornitori di servizi di stampa 3D su stampanti FDM. Una volta che la progettazione approssimativa del prodotto è stata
realizzata, ha contattato il partner di Formlabs AMPro 3D per ricevere un consiglio sulle tecnologie e sui
materiali di stampa 3D più adatti per la prima produzione in serie.
“Abbiamo adattato il tutto al processo SLS, perché i dettagli elevati e la mancanza di strutture di supporto offrono naturalmente molte più opzioni nella stampa SLS. Siamo passati quasi subito dal prototipo alla produzione in serie”, continua Mähler.
Un treppiede T-Crow pronto per la spedizione con l'alloggiamento prodotto con Nylon 12 Powder.
L’imprenditore ha scelto la stampante 3D SLS di Formlabs Fuse 1 e la stampante 3D SLA di grande formato.
Form 3L per avviare la produzione in serie di T-Crows attraverso parti di uso finale stampate in 3D.
” Credo che le stampanti 3D di Formlabs siano davvero le migliori stampanti attualmente disponibili sul mercato in termini di rapporto qualità-prezzo”.
Flessibilità di progettazione grazie alla stampa 3D
Per la produzione dei T-Crows, XSPECTER si affida a una combinazione di stampa 3D SLA e SLS per produrre quasi tutti i componenti per il treppiede, ad eccezione dell’elettronica.
La custodia è realizzata su Fuse 1 e, grazie al materiale Nylon 12 Powder di Formlabs, questa rimane leggera e resistente agli impatti ambientali. Per assali e ingranaggi invece, XSPECTER utilizza la Form 3L e la Durable Resin. Le proprietà flessibili, ma resistenti agli urti ea basso attrito di questo materiale, consentono di installare accoppiamenti con interferenza, necessari per il sistema di controllo a due assi.
Ingranaggi per il T-Crow realizzati in resina durevole sulla Form 3L.
Dopo che le singole parti sono state tutte stampate e post-elaborate internamente, vengono assemblate
utilizzando gli inserti filettati e sono pronte per essere spedite.
Tutti i componenti stampati in 3D del T-Crow prima dell’assemblaggio.
“Con le stampanti di cui disponiamo attualmente, potremmo produrre 1.500 T-Crows pronti per essere
consegnati, in un anno” afferma Mähler.
Flessibilità di progettazione grazie alla stampa 3D
Un vantaggio fondamentale e un fattore decisionale chiave per la produzione di stampa 3D interna è
l’enorme flessibilità che si ottiene.
“Con la stampa 3D, abbiamo semplicemente più libertà di progettazione rispetto ai metodi convenzionali
come lo stampaggio a iniezione. Lo chiamiamo un prodotto vivente. Se troviamo un bug di progettazione o riceviamo il feedback dei clienti, possiamo implementare una nuova iterazione dall’oggi al domani, aspetto che non può essere fatto con nessun altro metodo”, ha dichiarato Matthias Mahler.
Modifiche di progettazione di questo tipo vengono apportate, ad esempio, durante la personalizzazione
degli adattatori di diverse fotocamere, in modo che i treppiedi possano essere utilizzati universalmente.
Le diverse caratteristiche del design sono integrate direttamente nella custodia stampata in 3D. Quando una nuova fotocamera viene immessa sul mercato, Mähler può apportare rapidamente le modifiche
corrispondenti al suo treppiede T-Crow e distribuirlo.
XSPECTER è stato anche in grado di risparmiare un’enorme quantità di tempo e denaro reagendo più
rapidamente al cambio di fornitori per le singole parti grazie alla flessibilità della stampa 3D.
” Mi è capitato di non ricevere più l’interruttore on/off dal nostro fornitore originale e sono stato costretto a passare a un altro. Abbiamo quindi cambiato, dall’oggi al domani, l’apertura del tasto di circa due
millimetri”, spiega Mähler.
Con gli strumenti per lo stampaggio a iniezione che inizialmente erano stati quotati per circa 120.000 euro, una tale modifica dello stampo originale avrebbe richiesto molto più tempo e denaro.
“Credo che la stampa 3D sia davvero all’avanguardia, soprattutto se un’azienda vuole includere il feedback dei clienti.
“Anche se produciamo già in serie, sviluppiamo in modo costante i nostri treppiedi in base al
feedback che riceviamo”, ha concluso Matthias Mähler
Il fondatore dell’azienda sta già lavorando al suo prossimo progetto, chiamato Sea-Crow: una variante
marittima del treppiede per fotocamera, che comprende anche un proiettore che a sua volta funge da
ausilio alla navigazione notturna sull’acqua.


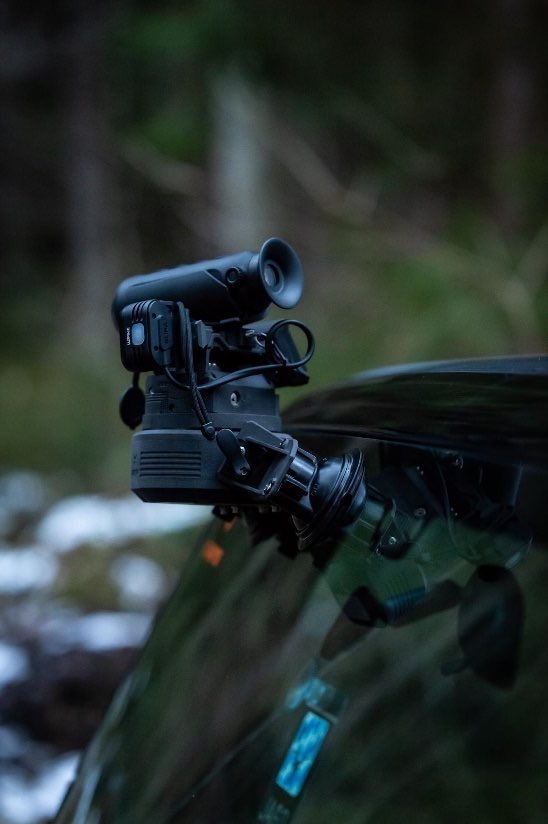



