BOND3D RAGGIUNGE IL 99% DI DENSITÀ DELLE PARTI CON LA TECNOLOGIA DI STAMPA 3D PEEK SENZA VUOTI
La scorsa settimana al Formnext 2021 , la startup olandese di stampa 3D Bond3D ha presentato la sua tecnologia di stampa 3D senza vuoti per il mondo.
Fondata nel 2014, l’azienda afferma di essere la prima nel settore in grado di stampare in 3D parti funzionali per uso finale con polimeri ad alte prestazioni come il PEEK senza perdere le proprietà intrinseche del materiale.
A differenza del FFF convenzionale, la tecnologia brevettata di Bond3D è un processo di estrusione a pressione controllata, in base al quale il filamento stampato si deposita in densità della parte finale superiori al 99%. Le parti isotrope risultanti mantengono le proprietà di massa dei loro materiali di base, proprio come quelle prodotte tramite stampaggio a iniezione.
Il PEEK è uno dei termoplastici più noti della famiglia dei polimeri ad alte prestazioni PAEK (poliarileterchetone). Combinando l’elevata resistenza e la biocompatibilità con la resistenza chimica e l’eccellente stabilità termica, il materiale tuttofare trova applicazioni in quasi tutti i settori critici.
Sfortunatamente, il PEEK è notoriamente difficile da stampare in 3D pur mantenendo le sue proprietà meccaniche. A causa della forma circolare degli ugelli di stampa convenzionali, gli strati adiacenti di PEEK estruso tendono ad avere aree di contatto limitate tra loro. Ciò si traduce nella formazione di vuoti all’interno delle parti, il che significa che i componenti PEEK stampati in 3D hanno sempre una densità inferiore rispetto alle loro controparti di materiale sfuso.
Secondo Bond3D, le stampanti 3D PEEK convenzionali di solito sono in grado di raggiungere solo circa l’85% di densità delle parti, portando a una resistenza ridotta nella direzione z.
La tecnologia di Bond3D sostiene di affrontare questo problema, ma come funziona? In sostanza, il processo di stampa a pressione controllata mira a estrudere il materiale fino a riempire tutti i vuoti tra le linee precedentemente stampate. Il sistema assicura che il flusso di materiale continui fino a quando la pressione nel bagno di fusione direttamente al di sotto dell’ugello supera una certa soglia, che deriva dalla forza verso l’alto esercitata sull’ugello stesso. Una volta superata la soglia, gli strati precedenti sono stati completamente incollati e non è necessario estrudere altro materiale.
Questo sistema di feedback della pressione è stato inizialmente determinato controllando la corrente del motore richiesta per azionare l’estrusore, ma il team di Bond3D ha riscontrato che ciò era impreciso. L’azienda alla fine è passata a un’implementazione basata su sensori di forza sensibili, per cui la testina di stampa è montata sul gantry tramite un gruppo basato sulla flessione, privo di attrito e isteresi.
L’azienda afferma di essere in grado di produrre parti “praticamente prive” di vuoti microstrutturali, con densità delle parti superiori al 99%. I test interni su campioni stampati hanno rivelato carichi di snervamento di 99 MPa e resistenze alla pressione del gas nell’intervallo di 115 bar per spessori di parete di soli 1,4 mm. Oltre a rafforzare la resistenza meccanica delle parti stampate in PEEK, ciò ha importanti implicazioni per le loro proprietà di trasporto dei fluidi, che è cruciale per qualsiasi tipo di tubazione o componente del collettore.
Bond3D ha ricevuto un investimento di diversi milioni di euro dal Regno Unito con sede centrale sviluppatore polimero Victrex indietro nel 2019, ed è ora pronto a portare la sua tecnologia sul mercato in seguito allo sviluppo di otto sistemi pronti per la produzione di quest’anno. L’elenco dei potenziali casi d’uso copre applicazioni critiche in tutto, dall’aerospaziale e automobilistico agli impianti medici e all’elettronica.
Stampa PEEK senza vuoto a pressione controllata
I polimeri ad alte prestazioni come il PEEK sono difficili da stampare; è difficile garantire che le proprietà delle parti stampate si avvicinino a quelle del materiale sfuso. La start-up olandese Bond High Performance 3D Technology, tuttavia, è riuscita a sviluppare una tecnologia di stampa 3D unica, che include meccatronica del sistema, software, tecnologia di slicing e convalida dei processi, per la produzione di parti funzionali di fascia alta in PEEK. Un recente investimento da parte di Victrex, un produttore leader di PEEK, con sede nel Regno Unito, sta ora aiutando Bond 3D a portare la sua tecnologia sul mercato. Tra le altre cose, uno degli elementi chiave della tecnologia di Bond 3D, la “legabilità”, è facilitata dalla stampa senza vuoto a pressione controllata.
PEEK, polietereterchetone, il membro più noto della famiglia PAEK (poliarileterchetone) di polimeri termoplastici ad alte prestazioni, trova applicazioni in mercati di fascia alta come quello dei semiconduttori, medico, aerospaziale, energetico e automobilistico grazie alla sua combinazione di qualità: leggero, ad alta resistenza , resistività chimica, stabilità termica (da –50 a +150 °C) e biocompatibilità.
Sfida di stampa
Sfruttare la libertà di progettazione della stampa 3D può aumentare ulteriormente l’ambito di applicazione del PEEK, a condizione che le proprietà favorevoli del materiale sfuso (certificato per mercati come quello aerospaziale) siano preservate nelle parti stampate in 3D. Che dovrebbero farlo non è ovvio, poiché la stampa 3D standard che utilizza FDM (modellazione a deposizione fusa) si traduce in una densità inferiore del materiale, rispetto al materiale sfuso.
Ciò ha a che fare con l’orientamento trasversale degli strati successivi, ciascuno composto da piccoli fili paralleli, come espulsi dall’ugello di stampa. Questa struttura reticolare trasversale raggiunge una resistenza adeguata nel piano xy (orizzontale), ma ha una superficie di contatto relativamente piccola tra gli strati vicini; vedere la Figura 1. I prodotti risultanti sono anisotropi nelle loro proprietà meccaniche.
L’orientamento trasversale degli strati adiacenti di materiale stampato per una resistenza adeguata nel piano xy (orizzontale) porta a una superficie di contatto relativamente piccola (indicata dalle aree gialle a destra), con conseguente riduzione della resistenza nella direzione z (verticale) .
Di conseguenza, rispetto al materiale sfuso, i prodotti PEEK stampati in modo convenzionale hanno una resistenza drasticamente ridotta nella direzione z (verticale) e la loro densità è solo dell’85% circa. La Figura 2 mostra la sezione trasversale di un prodotto stampato prodotto con la tecnologia FDM standard o con la tecnologia Bond 3D (come spiegato di seguito), quest’ultima che mostra un risultato praticamente nullo (densità > 99 percento). Questo non è rilevante solo per la resistenza meccanica dei prodotti, ma anche per le loro proprietà di trasporto di liquidi e gas. Ad esempio, i collettori possono trarre vantaggio dalla stampa 3D a causa della libertà di progettazione che offre, consentendo soluzioni efficienti e complesse, ma queste devono essere assolutamente a tenuta stagna.
Pertanto, la sfida di Bond 3D è stata quella di sviluppare una tecnologia di stampa per la stampa senza vuoto di prodotti isotropi che mantengano le proprietà di massa dei loro materiali di base. In aggiunta all’equazione, il PEEK è difficile da stampare a causa della sua elevata viscosità allo stato fuso e della sua natura semicristallina; al momento della solidificazione, parte del materiale si ricristallizzerà, portando a ritiro, che influenzerà le proprietà meccaniche (a causa dell’accumulo di sollecitazioni interne) e l’accuratezza dimensionale dei prodotti stampati.
Sezione trasversale di un prodotto in PEEK stampato, che mostra i fili stampati che escono dal piano.
(a) Tecnologia FDM normale.
(b) Tecnologia Bond 3D.
Controllo della pressione
La tecnologia di stampa 3D Bond è un processo di estrusione. Il materiale sfuso viene alimentato alla testina di stampa dove viene riscaldato a circa 400 °C, su cui il materiale fuso viene spinto attraverso l’ugello di stampa e depositato sul piano di stampa, quindi successivamente sugli strati precedentemente depositati.
Il processo di estrusione convenzionale procede in modo controllato: il materiale viene alimentato ad una velocità proporzionale alla distanza percorsa dall’ugello. Inevitabilmente, ci sono errori. Ad esempio, variazioni nel diametro del filamento e fluttuazioni nella temperatura del materiale fuso comprimibile influenzeranno la portata del materiale altamente viscoso attraverso l’ugello. Di conseguenza, non è possibile ottenere un’estrusione perfetta; verrà depositato più o meno materiale del necessario e la distanza tra l’ugello di stampa e lo strato superiore della stampa varierà. Ciò può portare a una distribuzione disomogenea del materiale stampato, per sotto o sovraestrusione (Figura 3). In quest’ultimo caso, la testina di stampa mobile provoca una sorta di onda di prua e “solleva” il materiale depositato e solidificandosi (la solidificazione richiede solo pochi secondi,
La sovraestrusione provoca l’accumulo di materiale residuo sul lato dell’ugello, che si degraderà rapidamente sotto l’influenza della testina di stampa calda, poiché i polimeri possono resistere a temperature oltre il loro punto di fusione solo per breve tempo. Il materiale degradato potrebbe sfaldarsi in macchie nere e contaminare il prodotto stampato, deteriorandone le proprietà estetiche e meccaniche. Inoltre, le forze crescenti tra la testa di “aratura” e il prodotto da stampare possono eventualmente portare alla rimozione della stampa dalla piastra di costruzione. Le proprietà della piastra di costruzione (ad esempio acciaio) sono scelte come compromesso per quanto riguarda la forza di adesione con il materiale di stampa; cioè, abbastanza alto da contenere la stampa, ma abbastanza basso da facilitare la rimozione del prodotto finito dal tavolo di costruzione.
Poiché la sovraestrusione può terminare in modo disastroso, generalmente si preferisce la sottoestrusione e il controllo del processo viene impostato di conseguenza. Ciò, tuttavia, crea dei vuoti nel prodotto stampato (Figura 3a). La soluzione di Bond 3D è la stampa a pressione controllata (Figura 4), in cui il materiale fuso scorre per riempire completamente lo spazio tra le linee precedentemente stampate; il flusso di materiale continua fino a quando la pressione nel ‘pool di fusione’ sotto l’ugello di stampa inizia a superare il setpoint, indicando che non è possibile aggiungere altro materiale. Quindi il divario è stato colmato e le linee adiacenti sono state completamente unite: questo è ciò che Bond 3D chiama “bondability” da cui l’azienda deriva il suo nome.
La pressione può essere derivata dalla forza verso l’alto esercitata sull’ugello di stampa nella parte inferiore della testina di stampa dal materiale stampato nel bagno di fusione sottostante. Come prima implementazione, questa forza è stata derivata dalla corrente del motore richiesta per azionare l’estrusore che fornisce materiale di stampa all’ugello. Questa corrente del motore, tuttavia, fornisce un segnale piuttosto rumoroso, quindi è necessario il filtraggio, che rende lento il controllo del feedback. Come accurata alternativa al controllo della larghezza di banda elevata, Bond 3D ha progettato un montaggio della testina di stampa basato su flessione, attrito e isteresi sul gantry a cui sono collegati i sensori di forza sensibili; La Figura 5 mostra un disegno schematico.
Flusso del polimero fuso (giallo) fuori dall’ugello della testina di stampa (verde) sotto controllo del flusso, con conseguente distribuzione potenzialmente disomogenea del materiale. La direzione della testina di stampa mobile è perpendicolare al piano del disegno.
(a) Sottoestrusione.
(b) Estrusione perfetta.
(c) Sovraestrusione.
Flusso del polimero fuso fuori dall’ugello della testina di stampa sotto controllo della pressione, come sviluppato da Bond 3D, con conseguente distribuzione omogenea del materiale indipendentemente dall’ampiezza del gap che deve essere riempito.
(a) Piccolo divario.
(b) Divario moderato.
(c) Ampio divario
La pressione può essere derivata dalla forza verso l’alto esercitata sull’ugello di stampa nella parte inferiore della testina di stampa dal materiale stampato nel bagno di fusione sottostante. Come prima implementazione, questa forza è stata derivata dalla corrente del motore richiesta per azionare l’estrusore che fornisce materiale di stampa all’ugello. Questa corrente del motore, tuttavia, fornisce un segnale piuttosto rumoroso, quindi è necessario il filtraggio, che rende lento il controllo del feedback. Come accurata alternativa al controllo della larghezza di banda elevata, Bond 3D ha progettato un montaggio della testina di stampa basato su flessione, attrito e isteresi sul gantry a cui sono collegati i sensori di forza sensibili; La Figura 5 mostra un disegno schematico.
Sezionatrice
In pratica, Bond 3D applica un mix di controllo del flusso e della pressione. Metaforicamente questo può essere paragonato all’uso di un alimentatore elettrico: o impostare la corrente, che produce una certa tensione, o impostare la tensione per generare una certa corrente. Le linee di contorno delle forme da stampare possono essere semplicemente create utilizzando il controllo del flusso. Qui, il controllo della pressione non ha senso, poiché non esiste ancora una linea a cui abbinare perfettamente la nuova linea; è solo nel passaggio successivo che il divario intermedio viene riempito utilizzando il controllo della pressione. Nella stampa 3D, i modelli da stampare sono generati da un modello 3D da una cosiddetta affettatrice; suddivide il modello in strati, o sezioni, che devono essere stampati uno sopra l’altro. Ogni livello è un insieme di forme 2D, e l’affettatrice determina i percorsi che devono essere stampati (simile al ‘percorso utensile’ per altre macchine CNC) e la quantità di materiale da estrudere. Quando si utilizza la stampa a pressione controllata, l’affettatrice non ha bisogno di dettare quanto materiale deve essere estruso, ma piuttosto a quale pressione deve essere guidato l’estrusore.
Le affettatrici disponibili in commercio non sono in grado di distinguere tra controllo del flusso e della pressione, quindi Bond 3D ha deciso di sviluppare una propria affettatrice che aggiunge informazioni al profilo di affettatura, indicando se il controllo del flusso o della pressione è appropriato per la fase di stampa in corso. L’ulteriore vantaggio di un’affettatrice proprietaria è che aumenta notevolmente la flessibilità nello sviluppo del processo; nuove opzioni di affettatrice possono essere aggiunte quasi istantaneamente, migliorando ulteriormente la qualità dei prodotti stampati.
Proprietà meccaniche
La tecnologia di stampa 3D Bond può produrre sia strutture porose altamente dettagliate e accurate (Figura 6) sia prodotti privi di vuoto. La risoluzione è inferiore a 0,3 mm e le proprietà meccaniche sono eccellenti. Le misurazioni su provini di trazione stampati hanno rivelato un carico di snervamento di 99 MPa, che si confronta favorevolmente con i 98 MPa garantiti da Victrex per il suo materiale sfuso e supera di oltre un fattore due il carico di snervamento dei campioni stampati a flusso controllato.
Un test della pressione del gas su una parte stampata tipo collettore con uno spessore di parete di 1,3 mm (Figura 7) non ha mostrato guasti fino a 100 bar; il tasso di perdita era inferiore al limite di rilevamento di 3,10-6 mbar·l/s. Un’altra parte, un recipiente progettato per avere una concentrazione di sollecitazione ben definita nella posizione con il minimo spessore della parete (1,4 mm), ha resistito fino a 115 bar di pressione prima dello scoppio, equivalente a una sollecitazione di Von Mises di 89 MPa nella parete esterna ( Figura 8). La sfida ora è dimostrare che la resistenza alla fatica delle parti stampate è pari a quella dei prodotti sfusi. Per questo, la stampa senza vuoti è fondamentale, perché anche i vuoti più piccoli possono generare microcricche che si propagano attraverso la parte, portando infine a rotture per fatica. Le scansioni micro TC vengono utilizzate per dimostrare l’assenza di vuoti.
Conclusione
La stampa senza vuoto è uno degli indicatori chiave delle prestazioni nella roadmap tecnologica di Bond 3D. Lo sviluppo attuale di Bond 3D viene eseguito utilizzando tre stampanti per modelli funzionali (Figura 9). Un primo lotto di otto stampanti pronte per la produzione è previsto per questo autunno (Figura 10). La tecnologia brevettata di Bond 3D è in grado di stampare parti complesse e funzionali realizzate in PEEK con eccellenti proprietà meccaniche, anche nella direzione z. Ciò consente la produzione additiva di parti isotrope ad alta resistenza con proprietà paragonabili a quelle delle parti in PEEK stampate o lavorate in modo convenzionale, consentendo libertà di progettazione e strutture complesse che non sono possibili utilizzando le tecniche convenzionali.
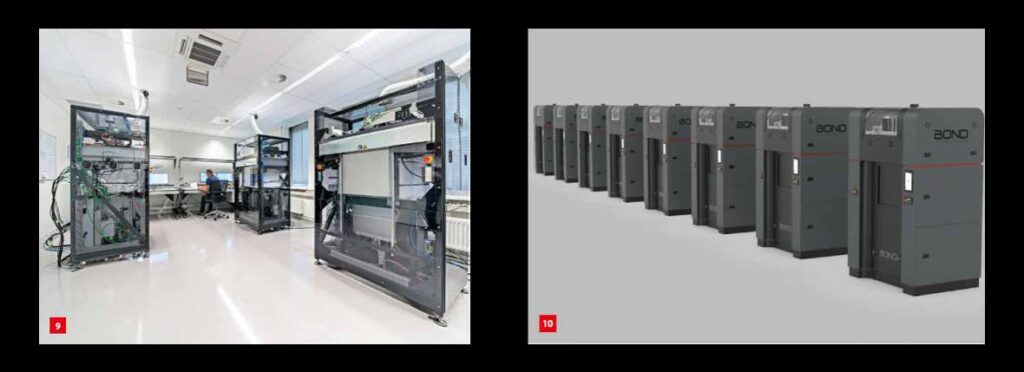
