▪ Additive Manufacturing: macchine e sistemi per componenti stampati in 3D in metallo, plastica e ceramica
Elevata redditività del processo di modellazione di estrusione composita (CEM) con poliammide PA6GF30
● Serie di test all’Università di Rostock: la stampa 3D con PA6GF30 sfrutta un’elevata resistenza alla trazione
● PA6GF30 nella stampa 3D come sostituto dell’alluminio (Al)
Rostock (Germania), 29 giugno 2022: Il processo di modellazione 3D di estrusione composita mostra un grande potenziale in termini di rapporto costo-efficacia rispetto ai processi di stampa 3D alternativi. In collaborazione con l’Università di Rostock, la start-up AIM3D ha condotto una serie di test con materiale PA6GF30 (BASF Ultramid B3WG6). I campioni di prova sono stati stampati sulle macchine AIM3D ExAM 255 ed ExAM 510 e la resistenza alla trazione dei campioni è stata confrontata con processi alternativi come lo stampaggio a iniezione e la stampa 3D convenzionale. Le valutazioni dei test sui materiali sono state sorprendenti: la PA6GF30 stampata è nettamente superiore ad altri processi di stampa 3D e raggiunge quasi la resistenza alla trazione del classico stampaggio a iniezione.
La poliammide rinforzata con fibra di vetro stampata in 3D mostra un’elevata resistenza alla trazione
Oggi, il PA6GF30 è un materiale indispensabile nelle applicazioni di produzione in serie industriale, poiché combina quasi idealmente elevate proprietà meccaniche con temperatura e resistenza ai fluidi. PA6GF30 è quindi un materiale pienamente affermato per applicazioni nel settore automobilistico, nella costruzione di macchine speciali o nella tecnologia delle apparecchiature. I componenti PA6GF30 sono particolarmente adatti per applicazioni di sostituzione di parti metalliche o in alluminio ovunque le temperature di esercizio lo consentano (PA6GF30: 130°C in uso continuo, 150°C per brevi periodi). Per quanto riguarda le proprietà meccaniche, come la resistenza alla trazione, valori molto elevati sono stati ottenuti dalla stampa 3D sui sistemi AIM3D ExAM 255 ed ExAM 510 (vedi Grafico 1). Rispetto ai processi a letto di polvere o ai processi di stampa 3D che utilizzano materiali a filamento, i sistemi di processo CEM raggiungono resistenze alla trazione che si avvicinano ai classici processi di stampaggio a iniezione termoplastico.
Prove e analisi dei materiali in dettaglio
In primo luogo, le barre di trazione sono state stampate su una macchina ExAM 255 con PA6GF30 e sulla più grande ExAM 510 (che sarà lanciata a Formnext 2022) (vedi grafico 1). Anche l’orientamento dei nastri stampati in 3D era vario. 0° per un lay-up in linea con la direzione di trazione (l’orientamento delle fibre era anche in direzione di trazione) e +/- 45° per un disegno con direzione alternata di +/- 45° rispetto alla direzione di trazione. Da un lato, l’azienda con sede a Rostock ha confrontato questo con i valori delle schede tecniche per lo stampaggio a iniezione con il materiale originale e dall’altro con l’uso del filamento per filamenti PA6GF30 comparabili. Inoltre, è stato effettuato un confronto con un materiale PA12 utilizzato per la stampa 3D su letto di polvere, poiché questo materiale è spesso utilizzato come riferimento nella stampa 3D. Il grafico 1 mostra che la tecnologia CEM è molto simile allo stampaggio a iniezione ma presenta un vantaggio significativo rispetto ai filamenti. Questo fenomeno è dovuto, tra l’altro, al fatto che i granuli originali utilizzati dalla tecnologia di stampaggio a iniezione di BASF contengono effettivamente fibre di vetro lunghe fino a 3 mm che possono resistere alle forze di trazione per un periodo più lungo. In confronto, la lunghezza della fibra nei filamenti è significativamente più corta per motivi tecnologici. In genere si distingue tra fibra rinforzata (GF) e fibra (se si utilizzano solo fibre corte). Se si considerano anche altre caratteristiche della scheda tecnica del materiale Ultramid B3WG6 di BASF utilizzato nel test, è chiaro che la combinazione di elevata resistenza durante la stampa 3D e l’elevata temperatura di esercizio continuo da 130°C a 150°C significa che questo è un materiale universalmente applicabile. Insieme all’eccellente stampabilità sui sistemi CEM, in futuro sarà possibile stampare applicazioni versatili come pinze o strumenti di manipolazione. Oggi, questi componenti sono solitamente fresati da alluminio, che è ad alta intensità di materiale. Al contrario, la stampa 3D mostra un grande potenziale in termini di costi dei materiali, risparmio di risorse, peso dei componenti, produzione rapida dei componenti e, in definitiva, una maggiore efficienza energetica. Non va dimenticato un approccio generale nella stampa di questi componenti: l’applicazione di approcci di progettazione bionica può aumentare le prestazioni dei componenti stampati in 3D per quanto riguarda le loro proprietà meccaniche. In sintesi, ci sono numerosi aspetti positivi in termini di costi (costi unitari) nonché di parametri prestazionali migliorati di un componente stampato in 3D. I risultati delle indagini presso l’Università di Rostock faranno parte di una pubblicazione scientifica.
Vantaggi in termini di costi ottenuti grazie all’integrazione funzionale nella stampa 3D
Rispetto ai componenti fabbricati in modo convenzionale, il fascino particolare della stampa 3D risiede nella cosiddetta integrazione funzionale attraverso approcci di progettazione compatibili con la stampa 3D. L’integrazione funzionale significa che gli assiemi possono essere prodotti in un unico processo di stampa, solo uno dei vantaggi strategici della stampa 3D. AIM3D ha prodotto un alloggiamento dell’estrusore dotato di montaggio su motore in PA6GF30 come dimostrazione del processo. Il supporto del motore, due condotti dell’aria instradati nelle pareti, un’uscita di ventilazione e un supporto per i sensori sono stati tutti integrati nell’alloggiamento come un unico componente. Nel caso di una strategia di produzione convenzionale con parti fresate in alluminio, avrebbero dovuto essere fresate da 3 a 4 parti da un blocco, con conseguente spreco di materie prime. Inoltre, durante la fase di progettazione, sarebbe necessario del tempo per escogitare una soluzione alternativa per evitare l’uso di strumenti speciali come trapani a fessura ecc. e per implementare un’adeguata connessione aderente dei componenti. Viene inoltre eliminato il tempo dedicato alla scrittura dei programmi di fresatura CAM, soprattutto per la produzione di piccoli lotti. Il lavoro di assemblaggio manuale è notevolmente ridotto, il che ha anche un effetto positivo sul calcolo dei costi delle parti.
Il processo CEM: Efficienze di costo convincenti
PA6GF30 è solitamente difficile da usare per la stampa 3D. È piuttosto difficile da ottenere e, dove è disponibile, da 20 a 30 volte il prezzo di altri materiali (riferimento: 500 g di Owens Corning XSTRAND PA6GF30 | 3dmensionals filamento costa circa EUR 86). Nella lavorazione con filamenti devono essere utilizzati anche additivi, che possono avere un’influenza sfavorevole sia sul prezzo che sulla certificazione. I granulati originali, utilizzati nelle classiche applicazioni di stampaggio ad iniezione, costituiscono il riferimento per costi intorno ai 5 – 6 EUR/kg. Il processo CEM è unico nel consentire l’uso di granuli disponibili in commercio senza filamenti in cui i costi di approvvigionamento del materiale sono gli stessi dello stampaggio a iniezione ma senza i costi di attrezzaggio. Tuttavia, come processo di stampa 3D, è più probabile che si trovi nel segmento della produzione in serie di piccole e medie dimensioni. Inoltre, ci sono le libertà della stampa 3D in termini di libertà geometrica (come sottosquadri), design bionici o densità selettive (diversi punti di forza, risparmio di materiale, elasticità selettiva, ecc.). Il Dr. Vincent Morrison, CEO di AIM3D: “Il prezzo paragonabile allo stampaggio a iniezione di materie prime che non contengono filamenti è un enorme vantaggio per la nostra tecnologia dei sistemi di stampa 3D CEM. Utilizzando PA6GF30, la nostra macchina ExAM 255 è in grado di produrre sia parti complesse e delicate con una risoluzione di stampa fine, sia componenti strutturali di grandi dimensioni con spessori di strato maggiori, con conseguente massima economicità con la stampa 3D all’avanguardia”.
PA6GF30 in sostituzione dell’alluminio (Al) nella stampa 3D
Naturalmente, un processo di stampa 3D all’avanguardia non può eguagliare i risparmi sui costi dello stampaggio a iniezione per serie di medie o grandi serie. I suoi vantaggi risiedono maggiormente nella produzione di lotti più piccoli e negli approcci di progettazione bionica. Tuttavia, la stampa 3D ha il sopravvento nel caso di produzioni di piccole e medie dimensioni e di prototipazione rapida, poiché qui i costi degli strumenti costituiscono una parte sproporzionata del calcolo dei prezzi. Soprattutto, la sostituzione del processo CEM per le soluzioni di produzione di alluminio fresato ha un potenziale elevato, come spiega il Dr. Vincent Morrison: “L’alluminio come materiale è relativamente costoso a causa della sua produzione ad alta intensità energetica. “Spesso le parti in alluminio vengono fresate da un blocco pieno. Questo esercita una grande pressione sui prezzi. A ciò si aggiungono le attuali carenze di materie prime. Il materiale PA6GF30 stampato con la nostra tecnologia CEM come soluzione di produzione alternativa crea dimensioni completamente nuove in termini di efficienza dei costi. Ciò vale ancora di più quando entrano in gioco approcci di progettazione bionica per aumentare le prestazioni dei componenti”.
Modellazione di estrusione composita
Il processo di modellazione dell’estrusione di compositi (CEM) combina il processo di stampaggio a iniezione di metalli (MIM), già affermato in tutto il mondo, con le tecnologie di processo della produzione additiva.
Questo si basa sia sul processo di modellazione a deposizione fusa (FDM) che sul processo di fusione laser selettiva (SLM), creando così una combinazione ottimale di metodi di produzione convenzionali e produzione additiva innovativa.
Il risultato è un processo molto semplice, basato su pellet per stampaggio a iniezione poco costosi e ampiamente disponibili, offrendo al contempo la libertà della produzione additiva senza la necessità di stampi. Il processo CEM non solo riduce significativamente i costi dei materiali, ma riduce anche drasticamente i costi delle macchine. I problemi comuni nella produzione dei metalli, come le sollecitazioni residue, vengono notevolmente ridotti con il processo CEM.
Modellazione del granulato fuso
La modellazione del granulato fuso (FGM) è un processo di produzione additiva e si basa sul processo dello strato fuso termoplastico ampiamente utilizzato (FDM/FFF).
La testina di stampa elabora i pellet in un sottile filo fuso e lo applica all’area di costruzione. Grazie alla generazione automatica del materiale di supporto è possibile realizzare anche forme più complesse, consentendo la produzione su misura o la produzione di prototipi con tecnologia di stampaggio ad iniezione. In contrasto con i comuni processi di strato fuso, come la fabbricazione di filamenti fusi (FFF), FGM non utilizza un filamento prodotto in modo elaborato, ma pellet per stampaggio a iniezione termoplastici convenzionali di produzione in serie.
AIM3D: Panoramica ████████████████████████████████████
AIM3D GmbH è stata fondata nel 2017 come spin-off dell’Università di Rostock (Chair for Fluid Technology and Microfluid Technology) a Rostock, in Germania. L’azienda produce stampanti 3D industriali che utilizzano il processo di modellazione di estrusione composita (CEM).
Ciò consente la produzione di componenti e prototipi sulla base di pellet per stampaggio a iniezione disponibili in commercio per metallo, termoplastiche (riempite) e ceramica senza la necessità di retrofit su un sistema di stampa 3D multimateriale dirompente.
I sistemi di stampa universali di AIM3D vanno oltre i normali limiti dei materiali, consentendo l’uso di materiali convenzionali per stampaggio a iniezione e offrendo quindi un approccio estremamente conveniente alla produzione additiva.
Come punto vendita unico, queste stampanti 3D sono dotate di un AIM3D CEM-E-1-Extruder® brevettato in grado di elaborare quasi tutti i pellet per stampaggio a iniezione fino a una lunghezza/diametro di 3 mm. L’elevata compressione consente di ottenere risultati di stampa sempre coerenti.
Le stampanti 3D di AIM3D non sono in alcun modo inferiori alle stampanti FDM e FFF disponibili sul mercato e offrono un’opzione conveniente rispetto alle stampanti 3D convenzionali, poiché non funzionano utilizzando polveri sferiche o filamenti di plastica. Ciò significa che il materiale del prototipo può quindi essere identico a quello del componente finale. La macchina è dotata di un’alimentazione del materiale automatica e utilizza fino a un litro di materiale per estrusore. Ciò corrisponde a ca. 1,2 kg di ABS o fino a 4,4 kg di acciaio inossidabile. La tramoggia del materiale può essere ricaricata durante il processo di stampa.
Per la post-elaborazione, AIM3D fornisce un forno di sinterizzazione ExSO che stacca e sinterizza parti metalliche direttamente dopo il processo di stampa 3D sulla macchina ExAM. Con la semplice pressione di un pulsante, entrambi i processi vengono eseguiti in modo completamente automatico in un unico sistema, producendo parti metalliche ad alta densità utilizzando il processo CEM. La generazione delicata e omogenea della struttura metallica nel forno di sinterizzazione si traduce in parti metalliche con una struttura simile a quella della ghisa, che sono quasi completamente esenti da sollecitazioni residue.
AIM3D fa parte di una rete globale di tecnologia e ricerca, in collaborazione con università e industria.
HZG Management GmbH, Coburg (Germania), è azionista dal 2021. Questa holding è gestita da Frank Herzog, pioniere del processo LaserCusing® e fondatore di Concept Laser, Lichtenfels (Germania).
Tecnologia di produzione additiva multimateriale oltre i limiti.
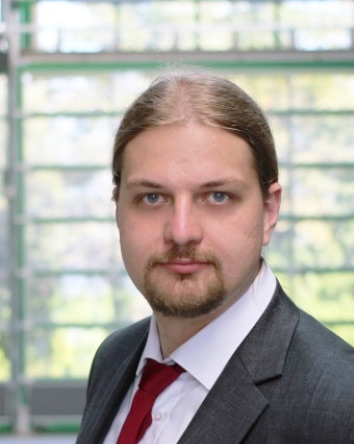





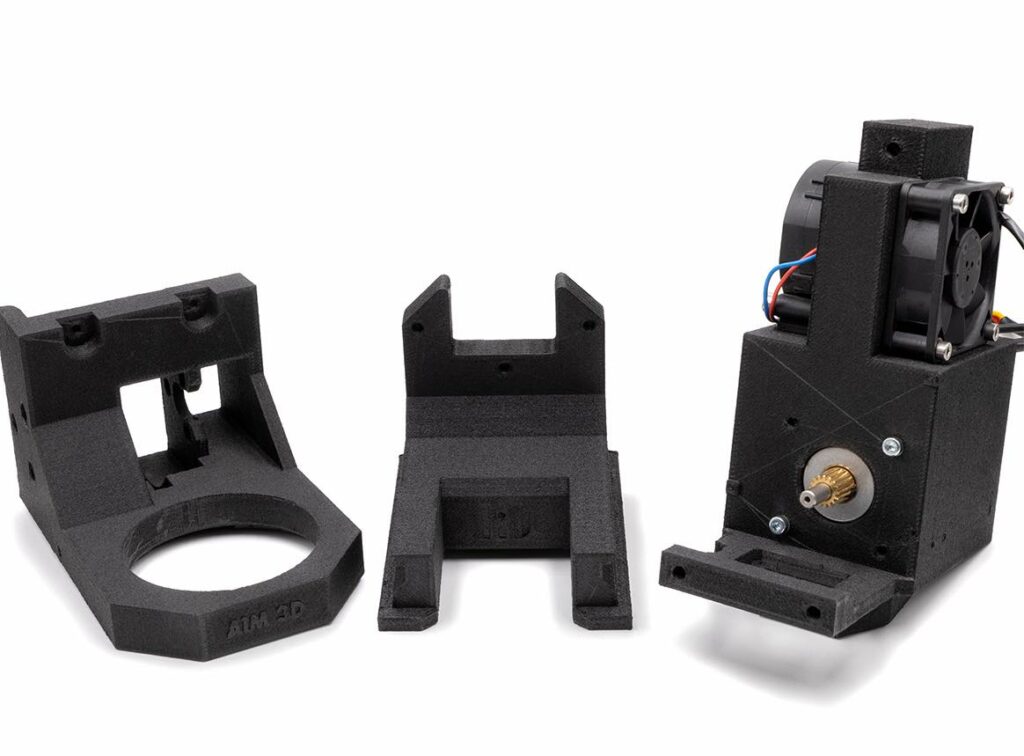