I SENSORI DI IDRATAZIONE STAMPATI IN 3D SBLOCCANO IL MONITORAGGIO REMOTO DELLE COLTURE SU LARGA SCALA
I ricercatori della Santa Clara University hanno utilizzato la stampa 3D per costruire una versione aggiornata delle unità di rilevamento dell’idratazione impiegate nei sistemi di irrigazione agricola.
Riprogettando, stampando in 3D e iterando su parti di questi sensori, gli ingegneri sono stati in grado di migliorare le loro capacità di rilevamento termico e di ridurne le dimensioni complessive. In tal modo, il team è anche riuscito a ridurre i costi, in modo che gli agricoltori possano ora utilizzare tali sensori su una scala più ampia rispetto a prima, per garantire che la preziosa vegetazione o le erbe esotiche siano annaffiate a sufficienza per prosperare.
“Aggiornando a componenti più efficienti, creando un design compatto e modulare e realizzando un guscio stampato in 3D personalizzato, la nostra unità di rilevamento (SU) è stata aggiornata in un sistema hardware molto più potente”, hanno affermato i ricercatori nel loro articolo. “Il nostro sistema di automazione dell’idratazione è stato adattato per essere una soluzione Internet of Things (IoT) molto più capace e ampiamente applicabile”.
I ricercatori hanno sollevato l’elettronica all’interno del sensore di idratazione per evitare che si bagnino in caso di maltempo. Immagine via Università di Santa Clara.
Alla scoperta dell’automazione agricola
Quando vengono implementati in ambienti esterni, i cosiddetti sistemi Internet of Things (IoT), come le tecnologie di automazione agricola, consentono efficacemente agli agricoltori di monitorare i loro raccolti da lontano. In pratica, tuttavia, tali configurazioni richiedono l’uso di nodi piccoli ma sensibili, in grado di rilevare la quantità di umidità necessaria a una determinata pianta e di trasmettere queste informazioni a un server di controllo.
Durante l’uso, queste unità di rilevamento vengono spesso lasciate esposte alla luce solare diretta, il che significa che sono soggette a umidità e sbalzi di temperatura estremi, che possono influire sulle loro prestazioni. Nel 2019, il team di Santa Clara ha tentato di superare questi potenziali problemi creando il proprio protocollo di routing interno “AB”, che consentiva alle unità di interagire con i server attraverso un sottosistema più robusto.
Tuttavia, il team ha scoperto che il loro dispositivo di rilevamento stesso “aveva ancora margini di miglioramento”, quindi ora si sono rivolti alla stampa 3D come mezzo per realizzare un design più compatto, ottimizzando le capacità di rilevamento della loro unità e rendendola efficiente dal punto di vista energetico, come oltre che più economico da produrre e in definitiva più scalabile rispetto alle alternative esistenti.
L’involucro del sensore stampato in 3D del team è stato progettato con sporgenze deliberate per evitare che l’acqua penetri all’interno. Immagine tramite Santa Clara University.
Percependo un’opportunità di mercato?
Soprannominato Sensing Unit 2.0 o “SU 2.0”, il dispositivo aggiornato dei ricercatori presenta una scheda nodo, un modulo di comunicazione, un sensore a ultrasuoni, un sensore termico, un regolatore di tensione, una batteria e un pannello solare. Alloggiati all’interno di una capsula stampata in 3D, i componenti di SU 2.0 sono divisi da separatori stampati, che consentono agli utenti di aggiornare le parti dove desiderato, senza rischiare di danneggiare i compartimenti circostanti.
Secondo il team, anche il regolatore di tensione del loro dispositivo è diventato fondamentale per il design dell’unità, poiché consente alla batteria dell’unità di funzionare a 3,6 V e al sensore a ultrasuoni di funzionare a 5 V e, grazie all’ingegnosità del rejigging, gli ingegneri sono stati in grado di far funzionare la SU 2.0 circa il 15% in più di efficienza energetica rispetto alla SU 1.0.
In termini di aggiunte hardware, uno dei più grandi aggiornamenti che i ricercatori hanno apportato al loro dispositivo è l’introduzione di un modulo termico. Lavorando in tandem con l’algoritmo di SU, il sensore può ora trasmettere qualsiasi informazione meteorologica o relativa alla temperatura a un server centrale, dove può essere analizzata e utilizzata per consigliare agli agricoltori potenziali azioni di risparmio del raccolto.
Il sensore del team di Santa Clara ha superato i test di impermeabilità (nella foto) a pieni voti. Foto via Università Santa Clara.
Allo stesso modo, dato che è probabile che la loro SU venga utilizzata all’aperto (tranne quando si coltivano determinati rimedi erboristici), il team ha stampato in 3D il suo involucro da PETG resistente alla pioggia. I sensori sono stati progettati anche per avere sporgenze sui lati, come mezzo per chiudere gli spazi necessari per l’incastro dell’unità, mentre i suoi cavi interni sono sollevati all’interno, per evitare che si bagnino durante gli acquazzoni.
Per mettere alla prova tutti questi aggiornamenti, il team ha infine sottoposto il dispositivo a valutazioni di potenza e impermeabilità. Sebbene i risultati iniziali abbiano mostrato che nessuna acqua era in grado di contattare i circuiti della capsula, era in grado di funzionare con energia immagazzinata per oltre una settimana senza luce solare e costava solo $ 62 per costruirla, i ricercatori hanno ora identificato ulteriori miglioramenti delle prestazioni per il loro sistema di allevamento .
Oltre a dotare le loro unità di Wi-Fi e connettori magnetici invece delle viti, i ricercatori stanno anche esaminando la possibilità di attingere alle tendenze dei dati e ai programmi di monitoraggio meteorologico per irrigare le colture in modo più uniforme. Nel complesso, tuttavia, considerano il SU 2.0 un netto miglioramento rispetto al loro design precedente e, grazie al suo involucro stampato in 3D, affermano che potrebbe persino avere un potenziale per il mercato di massa.
“SU 2.0 ha migliorato molte limitazioni dell’iterazione precedente come l’efficienza energetica e le dimensioni, offrendo al contempo nuove funzionalità come una migliore impermeabilità”, ha concluso il team nel loro articolo. “I miglioramenti di SU hanno consentito la produzione di massa, l’implementazione nel mondo reale e l’utilizzo di SU IoT con fattore di forma ridotto e convenienti ma sostenibili per l’automazione dell’idratazione”.
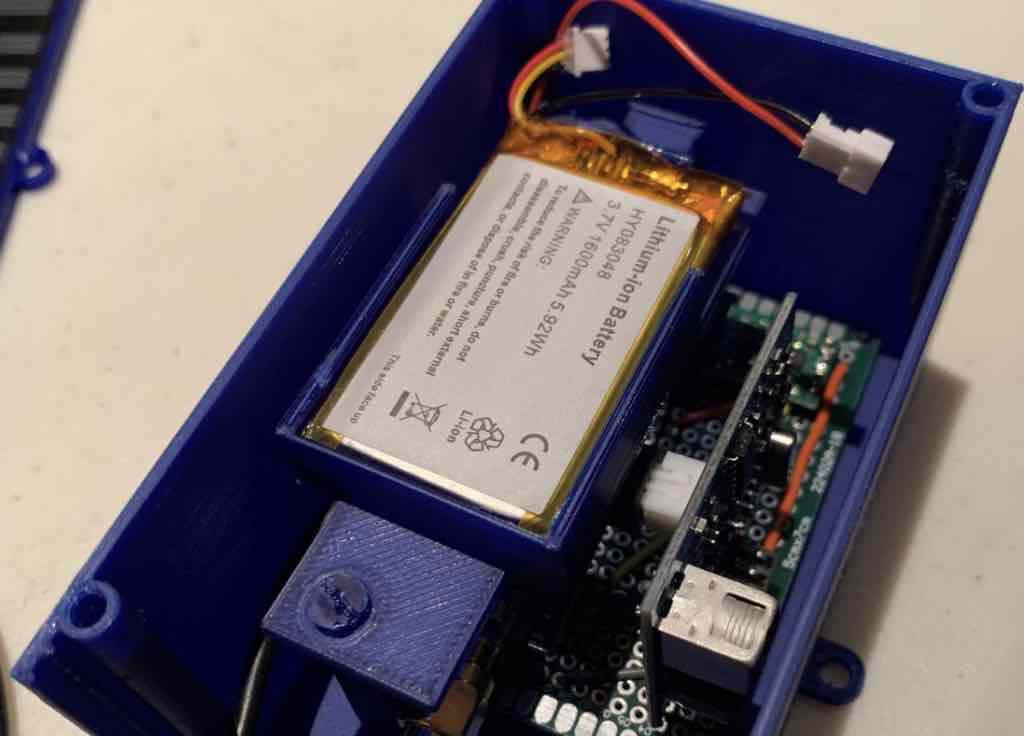