L’agenzia italiana di servizi di produzione additiva BEAMIT ha sviluppato un nuovo processo di stampa 3D per la lega di titanio Ti6242 in grado di produrre componenti aerospaziali e per sport motoristici che offrono prestazioni migliori rispetto alle controparti prodotte in modo convenzionale.
Il processo di stampa 3D di BEAMIT laser powder bed fusion (LPBF) può produrre componenti con livelli simili di resistenza alla trazione e resistenza alla temperatura forniti da altri materiali, tuttavia sono significativamente più leggeri. Secondo l’azienda, il suo processo di nuova concezione produce anche vantaggi in termini di sostenibilità attraverso la prevenzione dei rifiuti e il riciclaggio delle polveri.
“Il nostro duro lavoro è essenzialmente orientato a posizionarci a un livello in cui possiamo produrre innovazione e cambiare le regole del gioco tecnologicamente e per le applicazioni di stampa 3D”, ha affermato Andrea Scanavini, Direttore generale del Gruppo BEAMIT. “Siamo estremamente concentrati sulle esigenze e sulla produttività dei nostri clienti e utilizziamo la nostra divisione Material and Process Engineering per rispondere con soluzioni chiavi in mano per la prossima generazione di processi di produzione”.
BEAMIT ha iniziato a sviluppare il suo processo di produzione additiva per Ti6242 nel 2019, dopo aver condotto uno studio approfondito che ha esplorato le leghe adatte alla lavorazione con LPBF. L’azienda è approdata al Ti6242 per la sua capacità di resistere alle alte temperature e produrre componenti leggeri senza comprometterne la resistenza alla trazione. Questo rende la lega ideale per applicazioni nei settori del motorsport e dell’aerospaziale, dove i componenti leggeri e ad alte prestazioni sono fondamentali.
Il team BEAMIT ha intrapreso l’ottimizzazione delle proprietà meccaniche di Ti6242l alla temperatura attraverso il processo LPBF, ottenendo una resistenza alla trazione fino a 1.000 MPa e una densità di 4,5 g / cm3.
“Lo sviluppo del processo Ti6242 è iniziato nel 2019 come parte di un progetto di tesi in collaborazione con il Politecnico di Milano”, ha affermato Alessandro Rizzi, Responsabile Materiali e Processi Speciali del Gruppo BEAMIT. “Il materiale si adattava perfettamente a LPBF, ma la nostra vera attenzione era sui trattamenti termici. Abbiamo ideato diversi cicli del vuoto per ottimizzarne le proprietà meccaniche a temperatura ambiente e ad alte temperature e abbiamo anche sviluppato il processo di trattamento termico ad alta pressione integrato “.
Di conseguenza, la lega Ti6242 presenta un elevato rapporto resistenza-peso di oltre 600 MPa fino a 550 ° C, rendendola un’opzione interessante per applicazioni che richiedono una buona resistenza meccanica e leggerezza e una valida alternativa alle superleghe di acciaio e nichel. Il team BEAMIT ha effettuato test per confrontare le proprietà meccaniche del Ti6242 stampato in 3D con il Ti6242 e un’altra lega di titanio ad alte prestazioni, IMI834, prodotta con mezzi convenzionali, come la forgiatura.
Secondo quanto riferito, i componenti stampati in 3D hanno funzionato meglio di quelli forgiati con tecnologie convenzionali e, secondo BEAMIT, il processo consolida il ruolo della produzione additiva in prima linea nello sviluppo di materiali per settori come quello automobilistico e aerospaziale. L’azienda saluta inoltre la tecnologia come rappresentante di una “rivoluzione” nella sostenibilità, consentendo la riduzione dei rifiuti utilizzando solo i materiali necessari e riciclando la polvere rimanente per progetti futuri.
“La ricerca e lo sviluppo di nuovi materiali è sempre stata di fondamentale importanza nel Gruppo BEAMIT e siamo molto orgogliosi di essere attualmente l’unica azienda in grado di offrire soluzioni tecnologiche di altissimo livello, soprattutto in settori come il motorsport, l’automotive e l’aerospaziale” Giuseppe Pisciuneri, Chief Commercial Officer di BEAMIT. “Essere pionieri di questa innovazione e utilizzare i nostri materiali nei nuovi progetti dei nostri clienti ci motiva a continuare a crescere e ci sprona a fare cose più grandi e migliori”.
La domanda è in aumento nei settori automobilistico e aerospaziale di leghe di titanio per alte temperature grazie alle loro desiderabili proprietà di resistenza al peso, tuttavia i rapporti di peso ingegneristico, le strutture complesse, la temperatura di funzionamento e la velocità di sviluppo delle parti in titanio stanno sfidando i processi di produzione convenzionali. Di conseguenza, la stampa 3D sta rapidamente diventando un’opzione interessante per i produttori di questi settori.
Per quanto riguarda il settore automobilistico, il produttore di auto di lusso Bugatti ha incorporato parti in titanio stampate in 3D all’interno di alcuni dei suoi veicoli, tra cui un tubo di scarico per il suo modello Chiron Pur Sport al fine di ottenere un risparmio di peso e migliorare la resistenza alla temperatura della parte, e una staffa di montaggio in titanio per la parte anteriore ala della sua hypercar Bolide.
Nel frattempo, lo specialista di tuning automobilistico 1016 Industries ha combinato la stampa 3D in titanio e fibra di carbonio per integrare parti di prestazioni stampate in 3D in un’edizione ultra leggera della vettura sportiva 720S della McLaren . Il veicolo in edizione speciale è quasi il nove percento più leggero del modello originale grazie alla tecnologia.
Ci sono stati anche sviluppi significativi nello sviluppo del materiale in titanio stampato in 3D nel settore aerospaziale. Ad esempio, il produttore di stampanti 3D SLM e SLS Farsoon Technologies ha annunciato lo sviluppo di un nuovo materiale in titanio ad alta temperatura , TA32, dal suo cliente, Aerospace Hiwing Titanium Industrial Co. (AHTi) progettato per l’uso con il suo sistema di stampa 3D FS271M . Le parti stampate con la lega possono tollerare temperature di esercizio fino a 550 gradi Celsius e mostrano eccellenti proprietà meccaniche di resistenza alla trazione, flessibilità e plasticità alle alte temperature.
Altrove, US produttore aerospaziale Spirit AeroSystems ha già installato un componente strutturale in titanio 3D stampata nella fusoliera anteriore di un Boeing 787, e della US Air Force Hill Air Force Base incorporato con successo una staffa in titanio 3D stampato in un F-22 jet da combattimento prodotto da Lockheed Martin, appaltatore aerospaziale e della difesa .
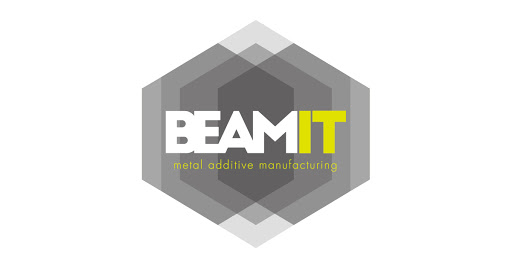