Fraunhofer IWS sviluppa rivestimenti efficienti, veloci e sostenibili per componenti industriali
POWDERscreen controlla i flussi di polvere nel fuso laser
I processi di produzione additiva stanno giocando un ruolo crescente nell’ingegneria automobilistica, aerospaziale e altri settori: quando è necessario produrre componenti di forma complessa o pezzi unici, sempre più aziende si rivolgono alla stampa 3D industriale. Tuttavia, le curve di rodaggio possono essere ancora piuttosto lunghe, soprattutto per le piccole serie, e le percentuali di scarto possono essere elevate all’inizio. Il Fraunhofer Institute for Material and Beam Technology IWS Dresden sta quindi sviluppando una moderna tecnologia di misurazione e controllo con la quale i processi additivi possono essere utilizzati in modo molto più efficace di prima, ad esempio per linee di produzione altamente automatizzate. Ciò include il POWDERscreen, un dispositivo di misurazione della polvere unico per la saldatura a deposizione laser. Il Fraunhofer IWS dimostrerà questo sistema innovativo a maggio 2022 durante il »3.
POWDERscreen è progettato per la saldatura a deposizione laser. In questo processo di produzione additiva, rivestimento e riparazione, ugelli speciali erogano flussi concentrati di polvere metallica esattamente nel fuoco di un raggio laser. Scioglie la polvere sulla superficie del pezzo per creare complesse strutture 3D da questa fusione. In futuro, il flussometro della polvere consentirà di misurare con precisione quali metalli fluiscono nel fuoco del laser e in quale quantità. Questo approccio può ridurre i costi della saldatura a deposizione laser a base di polvere, migliorare la qualità dei componenti prodotti e rendere l’intero processo di produzione esattamente ripetibile: questo è un requisito particolarmente importante nell’industria high-tech.
Passo importante verso un processo produttivo controllato
“Finora, la saldatura a deposizione laser a base di polvere è rimasta indietro rispetto al suo potenziale”, stima Rico Hemschik. L’ingegnere di Fraunhofer IWS ha sviluppato POWDERscreen. “Con il misuratore di portata della polvere, stiamo compiendo un grande passo avanti verso un processo di produzione additiva più efficiente, controllato e automatizzato.” Per renderlo possibile, il sistema combina sensori moderni con software speciali, uno schermo e interfacce per il trasferimento dei dati. Qui, i sensori fotografici contano le particelle nel flusso di polvere e il software lo usa per calcolare le quantità convogliate. La schermata mostra all’operatore della macchina i dati elaborati.
Un vantaggio speciale è l’usabilità universale: il POWDERscreen può essere montato su qualsiasi testa di processo per la saldatura a deposizione laser di polvere. Un esempio applicativo in cui POWDERscreen mostra particolarmente bene i suoi punti di forza è l’ugello COAXquattro. Questa testa di processo è stata sviluppata presso il Fraunhofer IWS per alimentare fino a otto diverse polveri o fili in canali separati nella messa a fuoco del laser e creare lì leghe in situ. Poiché il COAXquattro supporta fino a 30 grammi al secondo per canale, qui è possibile ottenere quantità di polvere significative. A causa delle grandi portate, la combinazione di COAXquattro e POWDERscreen è particolarmente adatta per processi ad alte prestazioni in cui è necessario produrre, verniciare o riparare componenti grandi e complessi con alta qualità, riproducibilità e velocità.
Tuttavia, POWDERscreen può anche essere combinato con altri sistemi di monitoraggio del processo sviluppati dal Fraunhofer IWS. Questi includono la fotocamera Emaqs per il controllo del processo, la scatola del sensore COAXjay e il sistema di misurazione LIsec per la geometria del cono della polvere. Tramite le sue interfacce, POWDERscreen può essere integrato insieme a questi dispositivi in moderni ambienti industriali o soluzioni per l’Industrial Internet of Things (IIoT). Ad esempio, l’uscita di dati analogici è possibile tramite un’interfaccia di tensione, tramite il protocollo IIoT »Message Queuing Telemetry Transport« (MQTT) o il trasferimento di dati tramite software.
Possibile generazione automatica di “gemelli digitali”.
In futuro, tali sistemi combinati di monitoraggio del processo dovrebbero anche generare in modo indipendente gemelli digitali di componenti prodotti in modo additivo. Perché le informazioni su dove il laser si è fuso, legato e formato quale polvere in quale quantità possono in linea di principio essere anche combinate automaticamente per formare un modello virtuale del computer. Con i metodi convenzionali, sarebbe difficile se non impossibile modellare con precisione tali modifiche locali della lega all’interno di un componente.
I ricercatori del Fraunhofer IWS vedono un grande potenziale applicativo per POWDERscreen nell’industria aerospaziale, tra le altre cose. Il sistema può essere utilizzato lì, ad esempio, per riprodurre e riparare complicate pale di turbine con processi additivi con una qualità costantemente elevata. Lo stesso vale per gli strumenti di goffratura nell’ingegneria automobilistica o la produzione di prototipi in quasi tutti i settori industriali.
Se gli operatori delle macchine non devono più allestire sistemi di saldatura a deposizione laser a polvere “a mano libera” e con molti tentativi, ma sulla base di parametri di processo registrati con precisione e ripetibili, i vantaggi sono evidenti: la curva di rodaggio si accorcia, il tasso di scarto all’inizio di una piccola serie diminuisce. Inoltre, i processi diventano più efficienti e riproducibili con un’elevata qualità. Infine, ma non meno importante, possono essere documentati automaticamente in futuro, il che a sua volta può essere importante per i successivi reclami in garanzia.
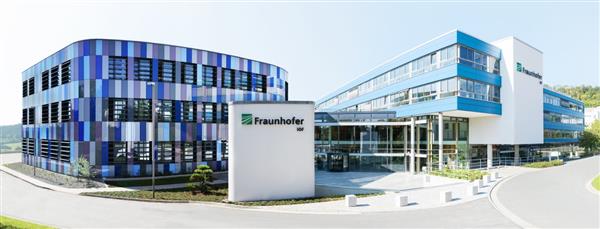