Il BMW Group punta sull’industrializzazione della stampa 3D
In un comunicato stampa, il BMW Group spiega come sta compiendo il passo successivo nell’integrazione sistematica dei processi di stampa 3D industriale . L’obiettivo è quello di industrializzare la produzione additiva e di integrarla in modo sostenibile nelle varie aree dell’azienda con un vantaggio economico. Ciò include principalmente lo sviluppo e la produzione dei veicoli. In questo modo, il BMW Group vuole sfruttare appieno i vantaggi della tecnologia – come la rapida disponibilità di componenti, flessibilità nella progettazione e produzione senza strumenti complessi.
Componenti stampati in 3D per Rolls-Royce Motor Cars
Dalla metà di quest’anno , il BMW Group produce componenti per veicoli fabbricati in modo additivo in metallo e plastica per la nuova Rolls-Royce Ghost. Questi sono prodotti lungo la catena di processo in vari luoghi della rete di produzione globale e assemblati a Goodwood, il luogo di nascita dell’auto esclusiva, nel Regno Unito. Nel corso della durata del modello, la società installerà diverse centinaia di migliaia di parti prodotte in modo additivo nella Rolls-Royce Ghost.
I componenti si trovano nella carrozzeria del veicolo e nell’abitacolo e sono altamente funzionali e rigidi. Il BMW Group ha preparato il processo per la produzione dei componenti nel suo centro di competenza interno, l’ Additive Manufacturing Campus, per l’uso nella produzione di serie automobilistica. Anche i componenti in plastica vengono prodotti lì utilizzando il processo Multi Jet Fusion e la sinterizzazione laser selettiva.
Nello stabilimento del BMW Group a Landshut, i componenti metallici vengono attualmente prodotti utilizzando il processo di fusione selettiva del raggio laser. Non lontano, nella rete di lavoro presso la sede del BMW Group a Dingolfing, più di 300 dipendenti esperti producono le singole carrozzerie delle automobili Rolls-Royce, inclusa la nuova Rolls-Royce Ghost. Le carrozzerie in alluminio di alta qualità sono state prodotte lì dal 2000 e l’inizio della produzione della BMW Z8.
I componenti metallici stampati in 3D vengono installati quasi completamente automaticamente nel processo di produzione. L’assemblaggio dei componenti in plastica prodotti nell’Additive Manufacturing Campus e il supporto metallico del pannello decorativo avverranno successivamente nella cosiddetta falegnameria e assemblaggio dello stabilimento di Goodwood.
Sviluppo di componenti utilizzando il design generativo
Anche nella prima fase di sviluppo della nuova Rolls-Royce Ghost, ingegneri, esperti di produzione e materiali hanno analizzato centinaia di componenti e verificato fino a che punto potevano essere prodotti utilizzando processi di produzione additiva. Il focus è su: vantaggi in termini di peso e geometria rispetto ai metodi tradizionali oltre che vantaggio economico. Quando si selezionano i componenti adatti per la produzione in serie additiva, gli esperti hanno definito criteri e requisiti per i componenti stampati in 3D e li hanno tradotti in “linguaggio macchina” con l’aiuto dei data scientist. Quello è stato l’inizio di un nuovo sistema di intelligenza artificiale che consente al BMW Group di identificare i potenziali componenti stampati in 3D nei veicoli futuri più rapidamente e in una fase precedente.
Con l’uso del design generativo, la progettazione di componenti con l’ausilio di algoritmi informatici, si creano in breve tempo forme che prima erano difficilmente realizzabili per ingegneri e progettisti. Esperti e computer lavorano insieme per progettare i componenti in modo che possano essere realizzati con il miglior uso possibile dei materiali.
Numerose potenziali applicazioni possono essere trasformate in realtà solo con l’aiuto del design generativo. Le tecnologie di stampa 3D sono particolarmente adatte per forme e strutture complesse che in precedenza non era possibile produrre con strumenti convenzionali.
Per la Rolls-Royce Ghost sono stati creati componenti ottimizzati per la topologia, ovvero parti che sono state ancora una volta notevolmente migliorate in termini di forma e funzionalità grazie a questo approccio progettuale. Questi componenti hanno una media di quasi il 50 percento in meno di peso rispetto a parti simili prodotte tradizionalmente. Inoltre, possono sfruttare in modo ottimale lo spazio disponibile nel veicolo. Un esempio di ciò è la staffa per l’ammortizzatore del portellone.
Campus di produzione additiva
Da giugno, il BMW Group ha riunito tutta la sua esperienza tecnologica nell’Additive Manufacturing Campus vicino a Monaco e ha formato i dipendenti di tutto il mondo per utilizzare i processi. Inoltre, qui vengono prodotti tutti i componenti del prototipo. Fino a 80 dipendenti lavorano attualmente nel centro di competenza e circa 50 impianti industriali per metallo e plastica sono già in funzione. Inoltre, più di 50 sistemi sono in uso in altri siti di produzione in tutto il mondo.
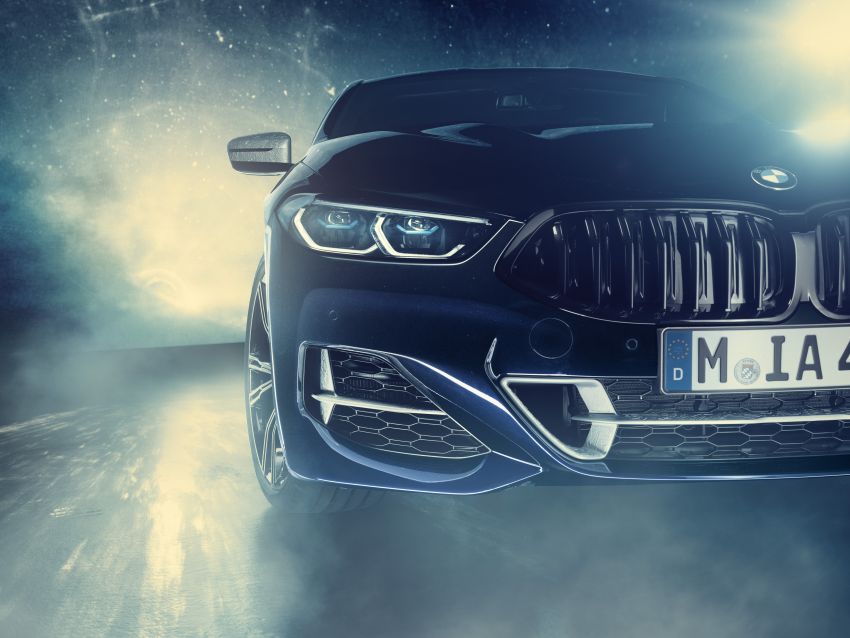