Una Storia di Innovazione nel Settore Automobilistico
Il BMW Group ha lungamente utilizzato la produzione additiva (AM), conosciuta anche come prototipazione rapida. Recentemente, l’azienda ha spinto l’innovazione oltre, introducendo tecniche avanzate di automazione per lavorare polimeri, metalli e persino sabbia, con l’obiettivo di adattare queste tecnologie alla produzione di massa.
Non si tratta solo di progressi nelle parti finali a mostrare l’impiego raffinato della stampa 3D da parte di BMW, ma anche l’uso unico dell’AM nella catena di montaggio. In particolare, le innovazioni recenti si sono concentrate sullo sviluppo e utilizzo di pinze robot personalizzate stampate in 3D, che hanno migliorato significativamente i processi di produzione nei vari stabilimenti globali dell’azienda.
Vantaggi della Produzione Additiva
Jens Ertel, responsabile della produzione additiva di BMW, evidenzia i numerosi vantaggi: “Con la produzione additiva possiamo realizzare rapidamente, a costi contenuti e con grande flessibilità i nostri ausili di produzione e dispositivi di movimentazione, che possiamo adattare individualmente alle esigenze specifiche e ottimizzarne il peso. Un peso inferiore consente velocità più elevate sulla linea di produzione, riduzione dei tempi di ciclo e minori costi. Inoltre, l’uso di robot più piccoli contribuirà a ridurre anche le emissioni di CO2 e i costi operativi.”
Pinze Robotiche Polimeriche Stampate in 3D
Presso il Centro di Costruzione Leggera e Tecnologia di Landshut, BMW impiega una combinazione di sinterizzazione laser selettiva (SLS) e fabbricazione di granuli fusi (FGF) per produrre pinze utilizzate nella fabbricazione dei tetti in polimero rinforzato con fibra di carbonio (CFRP) per la BMW M3. Queste pinze, che pesano circa il 20% in meno rispetto alle versioni tradizionali, possono essere realizzate in sole 22 ore, contribuendo a ridurre l’usura del sistema e gli intervalli di manutenzione.
Innovazioni Recenti e Futuri Sviluppi
Recentemente, BMW ha introdotto un nuovo design di pinza ancora più leggero del modello precedente, grazie all’uso di un’anima di sabbia stampata in 3D che poi viene fusa con alluminio. Questa tecnica, che riduce il peso del 25%, consente di utilizzare un singolo robot per la produzione della BMW M3, invece di tre macchine separate.
Oltre ai tetti in CFRP, BMW ha applicato FGF alle pinze di stampa 3D per la movimentazione delle porte nel suo stabilimento di Ratisbona. “Grazie a una struttura portante ottimizzata realizzata con la stampa 3D, siamo riusciti a aumentare la rigidità della pinza, riducendo allo stesso tempo il peso,” afferma Florian Riebel, responsabile della produzione di porte e ribalte.
Un Futuro Promettente per la Produzione Additiva in BMW
Markus Lehmann, responsabile dell’ingegneria impiantistica e della robotica presso lo stabilimento BMW di Monaco, riflette sui progressi: “Espandiamo continuamente l’uso di ausili alla produzione creati attraverso la produzione additiva. La stampa 3D ci permette di dotare le nostre pinze consolidate di accessori stampati individualmente, sostituendo i sistemi di presa completi con strutture portanti altamente integrate e ottimizzate in peso.”
Queste innovazioni non solo rendono la produzione più efficiente, ma anche più sostenibile, riducendo il consumo energetico e le emissioni di CO2. Con l’ampliamento dell’uso dell’AM nello stabilimento di Monaco, BMW anticipa ulteriori miglioramenti nell’efficienza energetica complessiva, un modello che potrebbe estendersi anche ad altri settori.
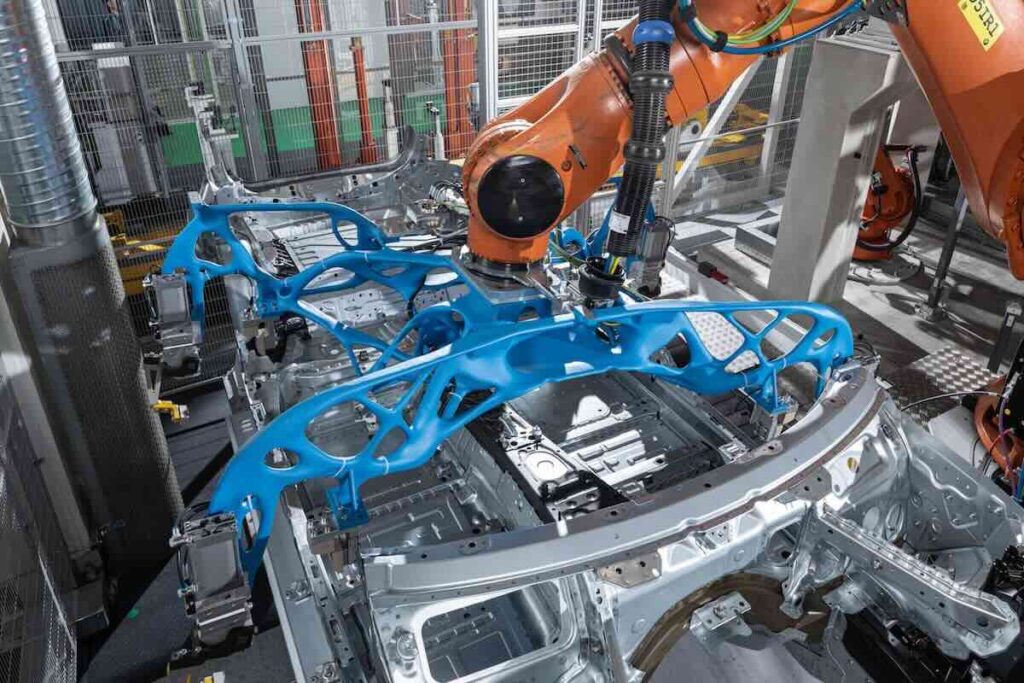