La società di produzione additiva Norsk Titanium US Inc. (Norsk) è specializzata in componenti strutturali in titanio di grado aerospaziale ed è stata in realtà la prima ad avere i suoi componenti strutturali in titanio stampati in 3D approvati dalla Federal Aviation Administration per essere utilizzati in un aereo commerciale , il Boeing Dreamliner, nel 2017. Ora, la società ha annunciato le consegne di produzione di nuovi componenti stampati in 3D per il Boeing 787 Dreamliner allo stabilimento di Grottaglie, con sede nel sud Italia di Leonardo, che fa parte della sua divisione Aerostrutture.
Queste nuove parti Boeing sono state realizzate utilizzando il processo AM brevettato di deposizione rapida di plasma (RPD) di Norsk , che ha svelato pubblicamente al mondo nel 2015. La tecnologia proprietaria, che ho visto chiamare sia metodo dell’arco al plasma che DED, utilizza un ambiente di gas inerte, come l’argon, per fondere il filo di titanio. Quindi, proprio come altre tecnologie di stampa 3D, il materiale riscaldato viene accumulato rapidamente negli strati successivi per creare la parte finale a forma di rete. Per garantire l’accuratezza, il processo RPD viene monitorato più di 600 volte al secondo per scopi di garanzia della qualità.
La Norsk da tempo dedica grande attenzione alla metallurgia. Mentre altri materiali metallici, comprese le leghe di nichel, l’acciaio per utensili e l’acciaio inossidabile, possono funzionare tutti con la piattaforma RPD, l’azienda – un fornitore di primo livello per OEM di motori e telai di aerei commerciali e un partner popolare per le aziende aerospaziali – utilizza molto spesso il filo di titanio , al fine di soddisfare i numerosi e rigorosi requisiti del settore aerospaziale altamente regolamentato .
Si dice che la stampa RPD renda il flusso del processo più semplice, oltre a essere in grado di produrre più forte, più durevole. Inoltre, secondo il sito web di Norsk , l’RPD si traduce in “una lavorazione notevolmente inferiore” rispetto a quella richiesta per i metodi di produzione convenzionali basati su forgia, il che può portare a un notevole miglioramento del 50-75% nel rapporto buy-to-fly … molto utile in ambienti su richiesta come il settore aerospaziale che producono componenti strutturali e critici per la sicurezza.
“La riduzione della lavorazione porta anche a un minore utilizzo di utensili e di energia, che sono fattori di costo significativi per le parti in titanio. Il risultato finale è una riduzione dei costi di produzione per la finitura delle parti in titanio, a vantaggio del cliente ”, continua il sito web.
Questa consegna appena annunciata è ora il terzo cliente di produzione dell’azienda nello spazio aerostrutturale commerciale. Inoltre, è anche rappresentativo del primo ordine ricorrente da una società aerospaziale con sede nell’Unione europea per Norsk.
“Siamo lieti di essere il fornitore di Leonardo. Questa consegna segna un aumento significativo del numero di parti prodotte in modo additivo precedentemente prodotte con lastre di titanio. È anche un passo importante verso la nostra missione di fornire un’alternativa ai forgiati in titanio nelle applicazioni aerospaziali “, ha affermato Karl Fossum, direttore dei programmi per i clienti di Norsk, in merito alla consegna.
Norsk ha utilizzato il suo processo RPD industriale per progettare e stampare in 3D preforme in Ti-6Al-4V, una comune lega di titanio con grande resistenza alla corrosione. Utilizzando Rapid Plasma Deposition, l’azienda è stata in grado di ottenere una riduzione di oltre il 40% del fabbisogno di materie prime, oltre a mantenere le proprietà dei materiali e il controllo del processo necessari.
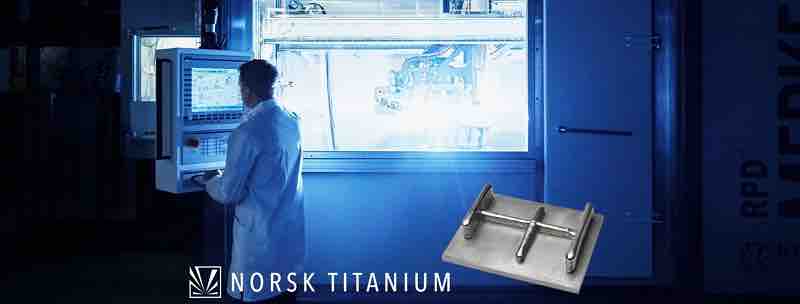