Un gruppo di ricercatori dell’Università del Nebraska-Lincoln , della Drexel University , della Navajo Technical University e di SigmaLabs ha sviluppato un nuovo processo per rilevare i difetti nelle parti stampate in 3D con fusione a letto di polvere laser (LPBF) che utilizzano gemelli digitali.
In un nuovo documento, il team delinea una strategia del gemello digitale che integra fisica e dati per fornire il rilevamento in tempo reale dei difetti mentre si formano durante il processo di stampa LPBF. Combinando le misurazioni della temperatura del meltpool in situ con le previsioni computazionali, i ricercatori sono stati in grado di rilevare e identificare tre diversi tipi di difetti nelle giranti in acciaio inossidabile.
L’obiettivo dello studio era affrontare le preoccupazioni relative alla tendenza del processo a creare difetti al fine di renderlo adatto a settori orientati alla precisione come l’aerospaziale e la biomedicina, proteggendo al contempo dalle minacce alla sicurezza informatica come la manomissione dei processi.
Nonostante le libertà geometriche e i significativi risparmi in termini di costi e tempo che la stampa 3D LPBF può ottenere, le industrie di alta precisione come quella aerospaziale e medica hanno finora esitato ad adottare la tecnologia per realizzare parti critiche per la sicurezza, a causa della sua tendenza a creare difetti.
I rischi per la sicurezza informatica sono diventati anche un’altra preoccupazione emergente non solo all’interno di LPBF ma anche in altri processi di stampa 3D, con parti malintenzionate potenzialmente in grado di manomettere i parametri di processo e i difetti dell’impianto all’interno di una parte per comprometterne le prestazioni.
È in corso una ricerca crescente per affrontare questi problemi e ridurre la possibilità di difetti all’interno del processo LPBF. Le cause del microcracking in alcuni metalli sono state studiate per migliorare il processo, così come gli effetti del beam-shaping .
Texas A&M , in particolare, ha svolto molto lavoro in questo settore, avendo lavorato con l’ Argonne National Laboratory per implementare l’apprendimento automatico per prevedere i difetti nelle parti stampate in 3D e stabilendo anche un “limite di velocità” LPBF al quale difetti come J è meno probabile che si formino bolle a forma di sulle parti stampate in 3D.
Proprio il mese scorso, gli scienziati di Texas A&M hanno introdotto un metodo universale di stampa 3D LPBF di parti metalliche impeccabili basato su dati di stampa a traccia singola e apprendimento automatico. Il team afferma che il suo metodo è meno costoso, dispendioso in termini di tempo e più semplice rispetto ai metodi di ottimizzazione dei parametri esistenti, il che lo rende adatto alle applicazioni aerospaziali, automobilistiche e della difesa.
I difetti tendono a formarsi durante i processi LPBF a causa di eventi termici durante la fusione, il raffreddamento, la solidificazione e la rifusione della polvere da parte del laser. Alla microscala, la fusione della polvere crea una scia di materiale fuso, chiamata meltpool, all’interno della quale la distribuzione della temperatura, il flusso e gli spruzzi influenzano la microstruttura, la porosità e la fessurazione della parte.
Alla macroscala, la rapida azione di scansione del laser e la continua fusione del materiale ad alte temperature provoca cicli di riscaldamento e raffreddamento che possono portare a sollecitazioni residue e deformazioni dei pezzi.
Per affrontare questo problema, l’ultimo studio mira a sviluppare e applicare una strategia integrata di dati e fisica per il monitoraggio e il rilevamento online della formazione di difetti nelle parti LPBF. Per fare ciò, il team ha combinato le misurazioni della temperatura del meltpool in situ con un modello di simulazione termica che prevede rapidamente la distribuzione della temperatura in una parte.
Secondo i ricercatori, la novità del loro approccio risiede nelle previsioni di distribuzione della temperatura fornite dal modello, che vengono aggiornate strato per strato con le misurazioni della temperatura del meltpool in situ. Pertanto, gli scienziati chiamano il loro metodo l’approccio del “gemello digitale” per rilevare la formazione di difetti.
La strategia del gemello digitale è in grado di fornire feedback per la correzione di anomalie nelle parti, riducendo così gli sprechi derivanti da build fallite. I ricercatori stanno offrendo la loro strategia come alternativa alle tecniche di monitoraggio dei processi puramente basate sui dati al fine di superare gli svantaggi di questi processi, vale a dire ritardi nel rilevamento, scarsa generalizzabilità dei modelli basati sui dati alle forme delle parti e la spesa e l’uso intensivo di risorse natura dell’acquisizione dei dati.
Inoltre, poiché il gemello digitale incorpora sia l’effetto su macroscala della forma della parte sulla storia termica che l’effetto su microscala dell’interazione laser-materiale sotto forma di temperatura del meltpool, può incapsulare l’effetto di diversi parametri di lavorazione, come il modello di scansione, la spaziatura del tratteggio, la potenza del laser e la velocità.
Per testare il loro metodo, il team ha stampato in 3D quattro parti a forma di girante in acciaio inossidabile utilizzando un sistema EOS M290 LPBF che presentava diversi tipi di difetti che coprivano derive del processo, delaminazione delle lenti e intrusioni informatiche. Per creare i difetti, i ricercatori hanno apportato modifiche ai parametri di elaborazione, provocato malfunzionamenti relativi alla macchina e deliberatamente manomesso il processo per creare difetti all’interno della parte.
Il team ha scelto di stampare parti della girante per dimostrare il loro gemello digitale poiché è divisibile in tre regioni distinte lungo la direzione di costruzione: le sezioni di base, media e aletta. Ognuna di queste sezioni include caratteristiche complesse difficili da stampare, come un canale di raffreddamento interno a forma di lacrima, che ha comportato tempi di raffreddamento diversi tra gli strati e, di conseguenza, una storia termica complessa.
Durante la costruzione, il processo è stato monitorato continuamente utilizzando una serie di tre fotorilevatori coassiali integrati nel percorso laser. I segnali ottenuti dall’array di sensori sono stati elaborati per creare due tipi di misurazioni, vale a dire l’energia termica planck (TEP) e la densità di energia termica (TED). La firma TEP è stata correlata alla temperatura del meltpool, mentre TED ha catturato la radiazione della camera a banda larga.
Queste firme sono state quindi incorporate nel modello della teoria dei grafi per aggiornarlo continuamente con l’attività su microscala del meltpool durante tutto il processo.
Il gemello digitale è stato in grado di rilevare tutti e tre i tipi di difetto nelle parti della girante stampate in 3D durante il processo LPBF. Secondo i ricercatori, i risultati hanno dimostrato che il metodo ha consentito un rilevamento preciso e interpretabile della formazione di difetti rispetto all’uso dei soli dati del sensore. A tal fine, l’approccio del gemello digitale supera la necessità di trasferire le firme dei sensori a un algoritmo di analisi dei dati separato e quindi previene i ritardi nel rilevamento dei difetti.
In futuro, il team cercherà di estendere le capacità del suo gemello digitale per rilevare altri tipi di difetti, come la distorsione. Verranno inoltre testati l’approccio con diversi parametri di elaborazione, strategie di scansione e forme delle parti.
Ulteriori informazioni sullo studio possono essere trovate nel documento intitolato: “Produzione additiva digitalmente gemellata: rilevamento dei difetti nella fusione del letto di polvere laser combinando simulazioni termiche con dati del sensore meltpool in situ”, pubblicato sulla rivista Materials and Design. Lo studio è co-autore di R. Yavari, A. Riensche, E. Tekerek, L. Jacquemetton, H. Halliday, M. Vandever, A. Tenequer, V. Perumal, A. Kontsos, Z. Smoqi, K. Cole , e P. Rao.
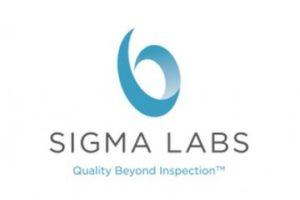