Gli studenti dell’Università di Scienze Applicate del Nordovest della Svizzera (FHNW) hanno costruito un rover funzionale per Marte utilizzando parti stampate in 3D con la tecnologia SLS e si sono classificati al 6 ° posto all’European Mars Rover Challenge (ERC) in Polonia.
Concorso internazionale di spazio e robotica
Per la prima volta nella storia dell’Università di Scienze Applicate del Nordovest della Svizzera FHNW, un team di nove studenti di laurea provenienti da tre diverse aree di studio ha partecipato con successo all’European Rover Challenge (ERC). Nel giro di un anno, gli studenti hanno costruito un rover per Marte e si sono classificati al 6 ° posto nella competizione su 19 squadre provenienti da tutta Europa, essendo gli unici debuttanti nei primi 10. “È stato un po’ come essere un pesce fuor d’acqua, perché non avevamo conoscenze interne sulla competizione”, spiega Nadine Richard. La studentessa del quinto semestre di ingegneria meccanica si è occupata del gripper, del campionamento profondo e del braccio robotico.
Successo con gli obiettivi giusti
Per la prima partecipazione all’ERC, era importante per il team FHNW poter competere con un rover funzionante. Nelle quattro discipline di navigazione, esplorazione, manutenzione e scienza, il rover di Marte doveva dimostrare le sue competenze. “Nello sviluppo, ci siamo concentrati soprattutto sulla trasmissione e sul manipolatore (braccio robotico e gripper), poiché questi due componenti sono fondamentali per tutte e quattro le attività della competizione”, sottolinea Nadine.
Componenti dalla stampante 3D
La stampa 3D ha svolto un ruolo chiave nello sviluppo del rover. “Un grande vantaggio della produzione additiva è la complessità delle parti che si possono progettare, così come le diverse tecnologie e materiali pronti all’uso”, spiega Nadine. Per le ruote e il pennone del segnale, la squadra ha utilizzato le stampanti FDM disponibili all’università. A causa delle alte richieste sul gripper, la sinterizzazione laser selettiva (SLS) è stata utilizzata come altra tecnologia di stampa 3D. L’elevata durata – a causa delle forze da tutte le direzioni – e l’estrema leggerezza – a causa del centro di gravità del gripper che è molto lontano – hanno portato gli studenti a scegliere Sintratec. “I componenti sponsorizzati da Sintratec hanno superato tutti i nostri requisiti stabiliti e si sono comportati in modo eccellente in tutte e quattro le attività della competizione”, afferma Nadine con soddisfazione.
L’equipaggio è stato in grado di costruire il rover in un solo anno, utilizzando componenti stampati in 3D in SLS per parti essenziali come le ruote e la presa robotica. La SLS si è dimostrata particolarmente utile per la realizzazione della presa robotica, poiché offre una durabilità elevata e una leggerezza estrema, dovuta al centro di gravità della presa robotica. Il team ha utilizzato una Sintratec S2 per la stampa in 3D con SLS di parti in PA12. La precisione di questa tecnologia ha permesso di ottenere componenti di elevata qualità, in grado di superare tutti i requisiti stabiliti e di performare eccellentemente in tutte le quattro sfide della competizione.
Non solo l’accuratezza e la stabilità dei componenti stampati in 3D con tecnologia SLS hanno convinto il team di Nadine Richard, ma anche la possibilità di utilizzare questi componenti non solo come prototipi, ma anche come parti funzionanti, senza alcun tipo di restrizione.
L’esperienza di successo del team di FHNW dimostra come la tecnologia SLS abbia il potenziale per migliorare significativamente i processi di produzione e di progettazione nell’ambito dell’esplorazione spaziale, consentendo una maggiore precisione e una maggiore leggerezza nei componenti. La stampa 3D con tecnologia SLS, inoltre, può aiutare a ridurre i costi di produzione e a semplificare la catena di fornitura, grazie alla possibilità di produrre parti complesse in un unico passaggio e senza la necessità di creare costosi strumenti di produzione.
L’equipaggio è stato in grado di costruire il rover in un solo anno, utilizzando componenti stampati in 3D in SLS per parti essenziali come le ruote e la presa robotica. La SLS si è dimostrata particolarmente utile per la realizzazione della presa robotica, poiché offre una durabilità elevata e una leggerezza estrema, dovuta al centro di gravità della presa robotica. Il team ha utilizzato una Sintratec S2 per la stampa in 3D con SLS di parti in PA12. La precisione di questa tecnologia ha permesso di ottenere componenti di elevata qualità, in grado di superare tutti i requisiti stabiliti e di performare eccellentemente in tutte le quattro sfide della competizione.
Non solo l’accuratezza e la stabilità dei componenti stampati in 3D con tecnologia SLS hanno convinto il team di Nadine Richard, ma anche la possibilità di utilizzare questi componenti non solo come prototipi, ma anche come parti funzionanti, senza alcun tipo di restrizione.
L’esperienza di successo del team di FHNW dimostra come la tecnologia SLS abbia il potenziale per migliorare significativamente i processi di produzione e di progettazione nell’ambito dell’esplorazione spaziale, consentendo una maggiore precisione e una maggiore leggerezza nei componenti. La stampa 3D con tecnologia SLS, inoltre, può aiutare a ridurre i costi di produzione e a semplificare la catena di fornitura, grazie alla possibilità di produrre parti complesse in un unico passaggio e senza la necessità di creare costosi strumenti di produzione.
SLS convince gli ingegneri del futuro
Non solo l’elevata durata e stabilità dei componenti SLS stampati in PA12 sulla Sintratec S2 hanno convinto il team di Nadine Richard. “Il maggior vantaggio della tecnologia SLS è l’incredibile precisione e durata dei componenti.”
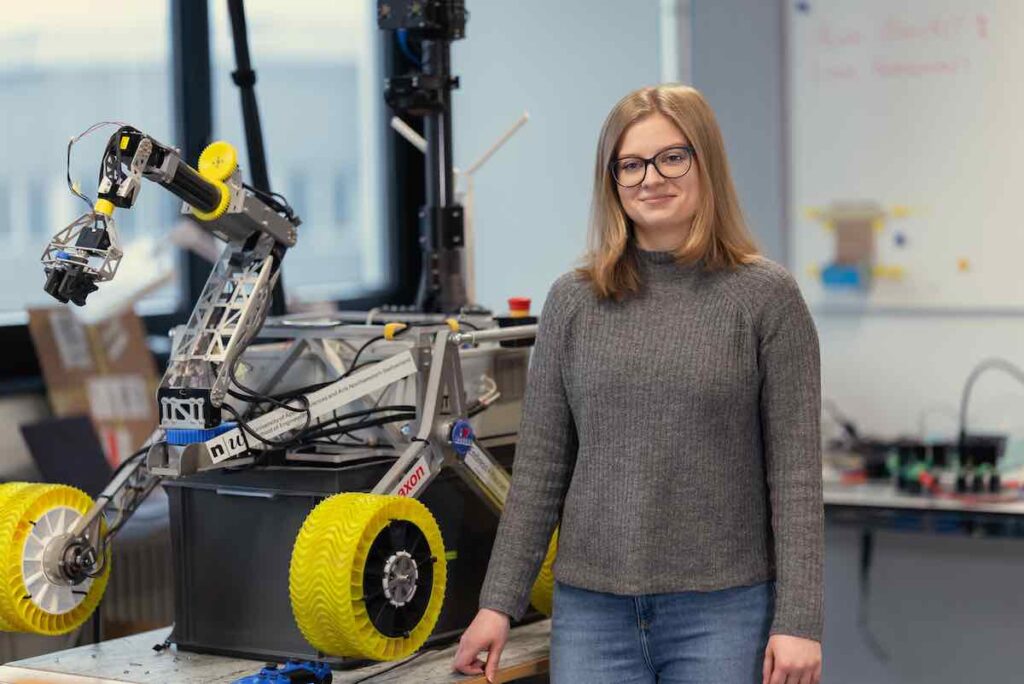
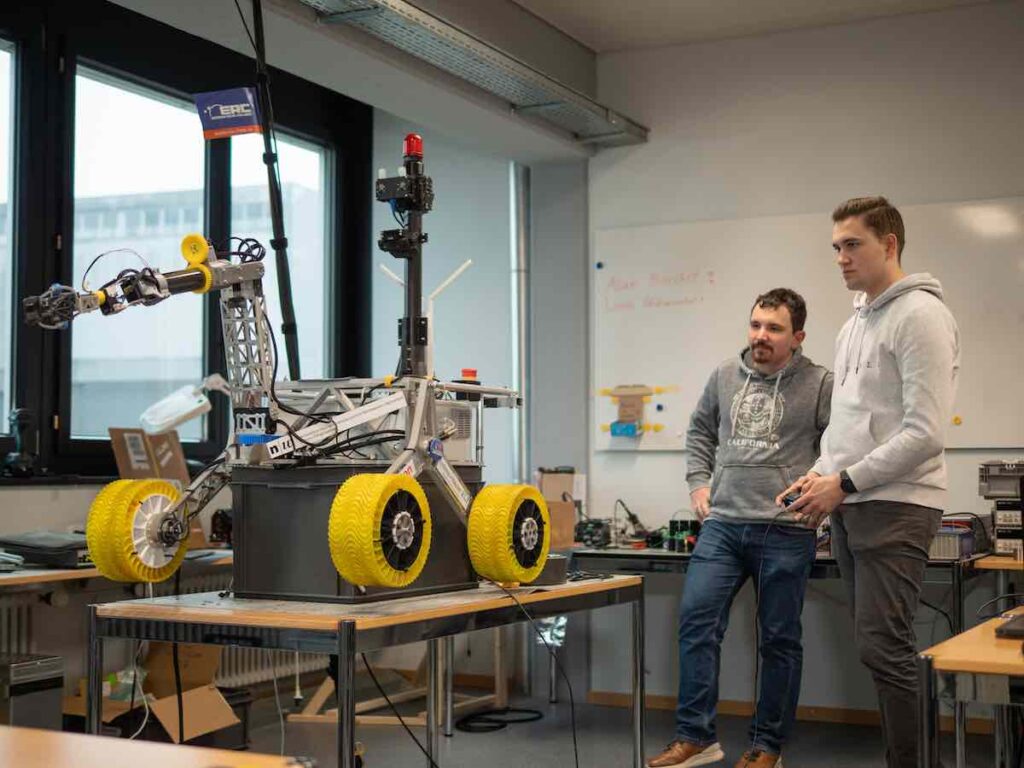
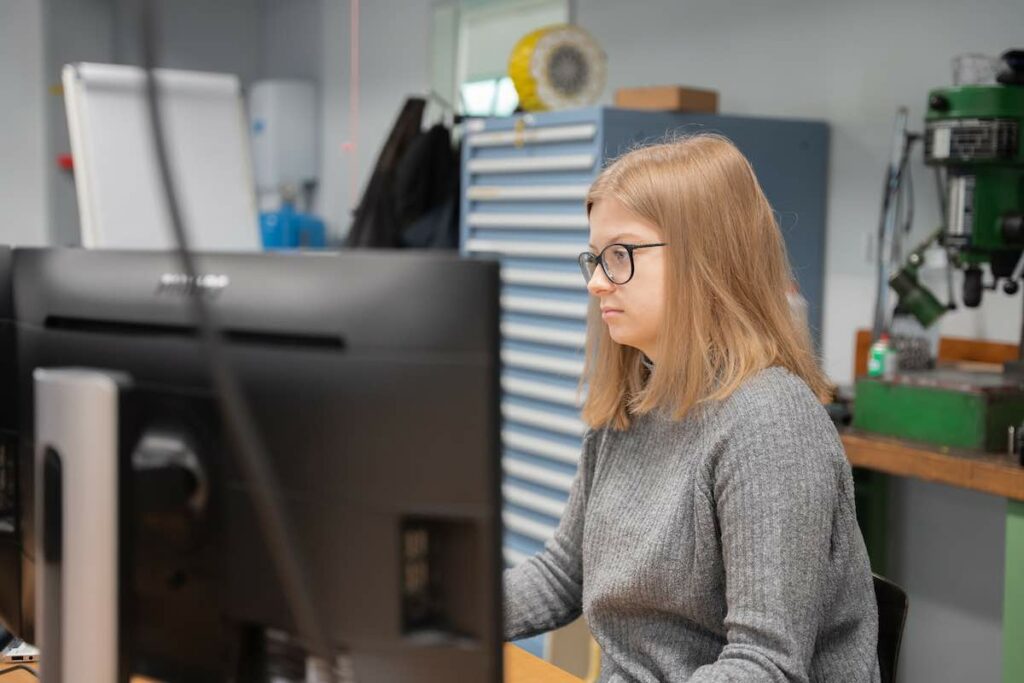
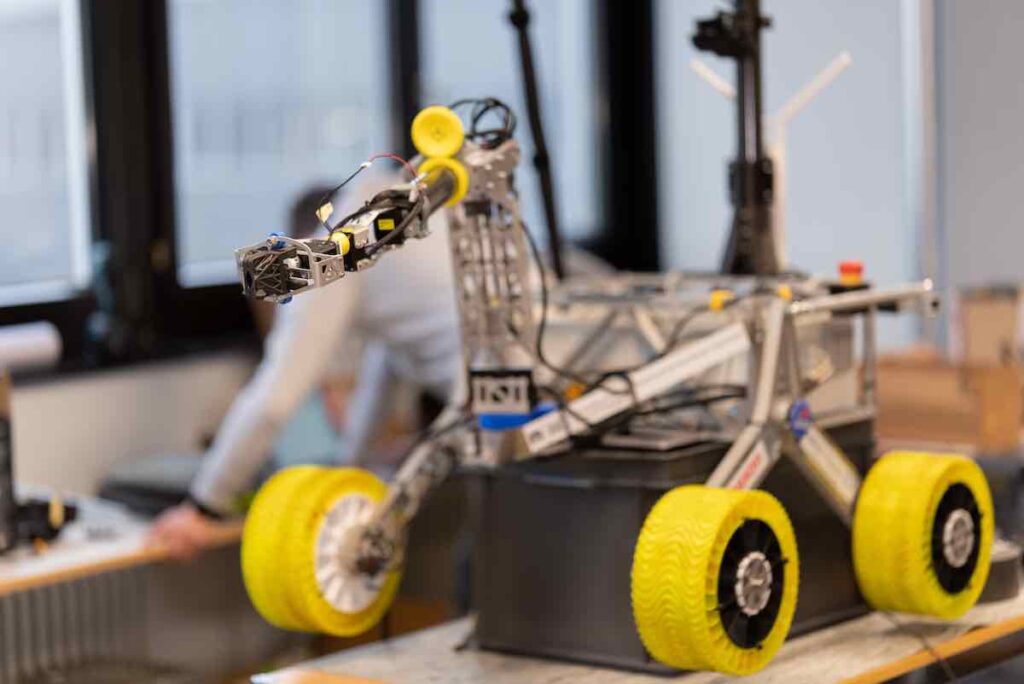
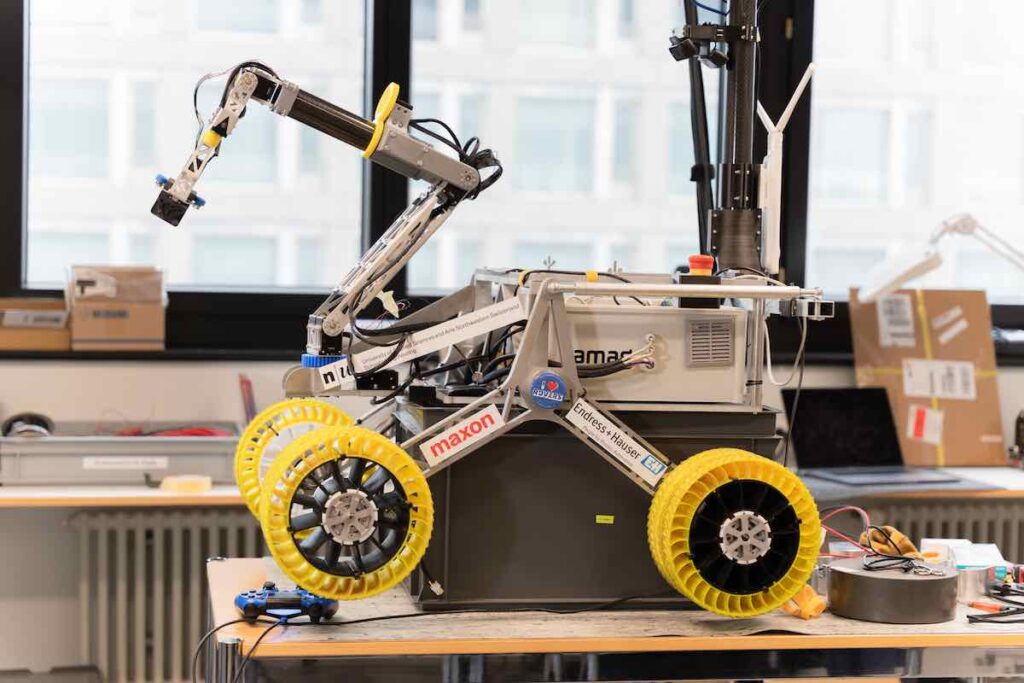
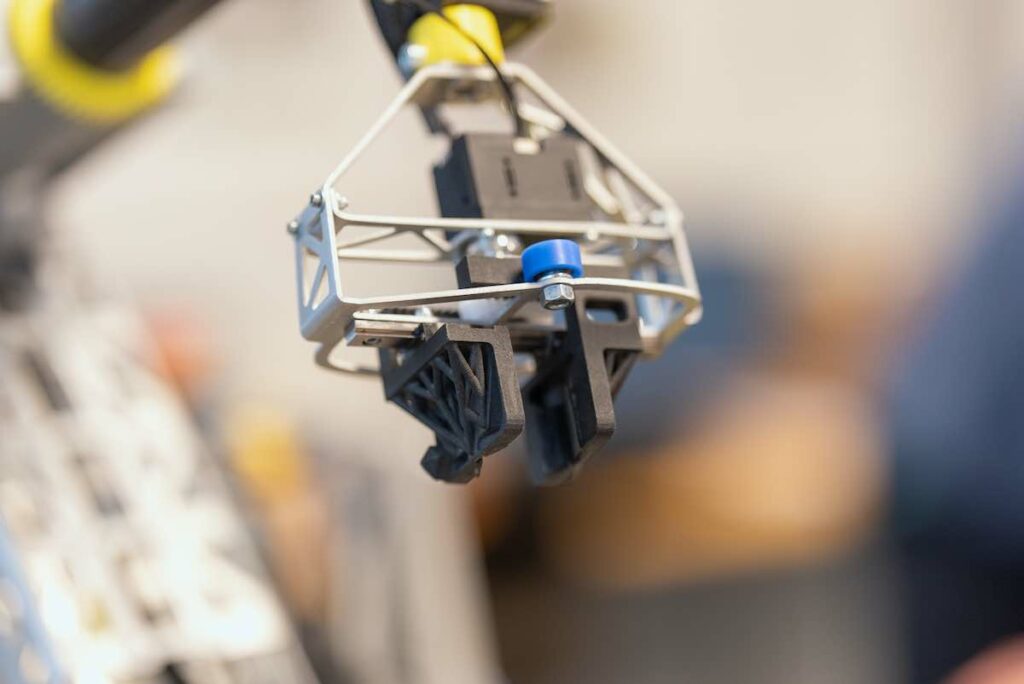
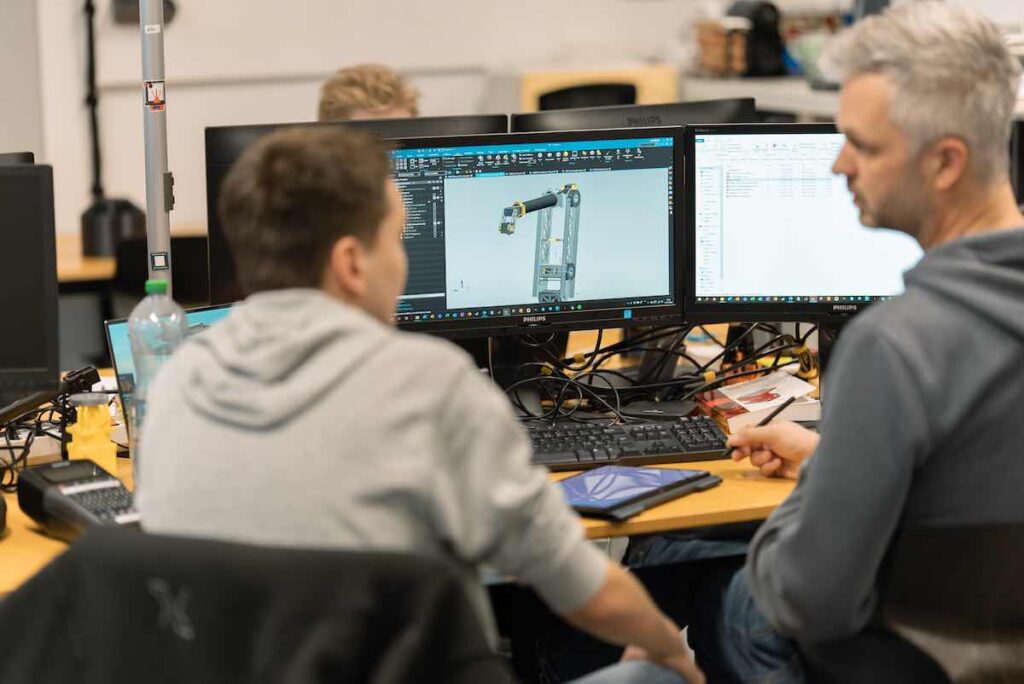
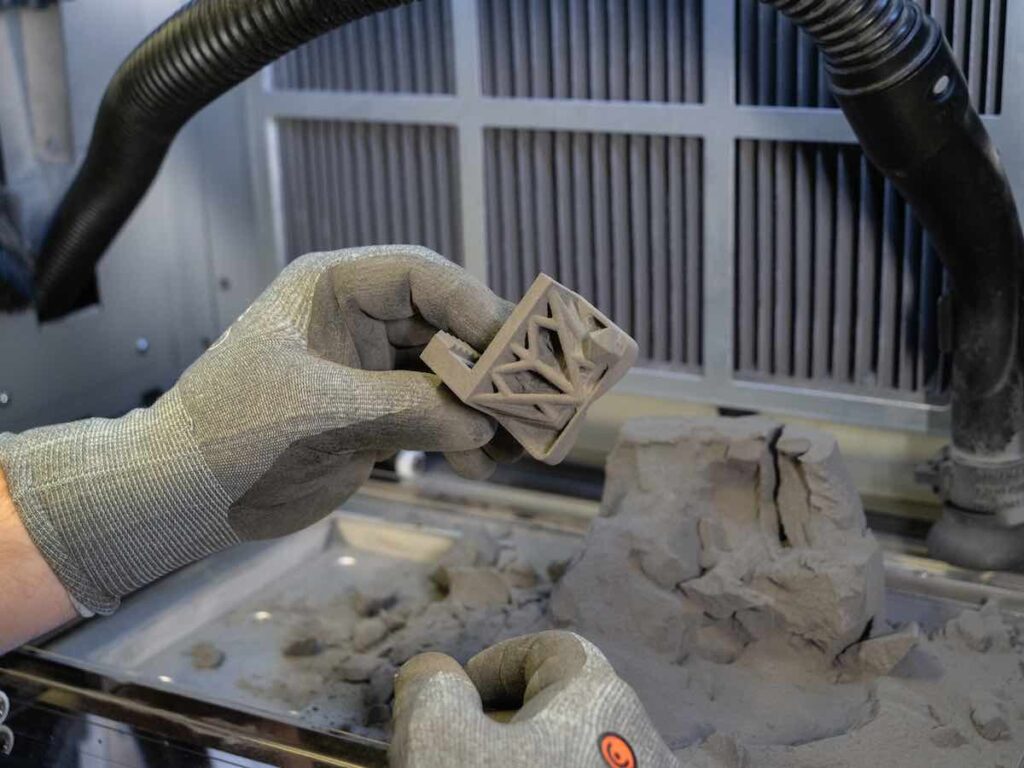
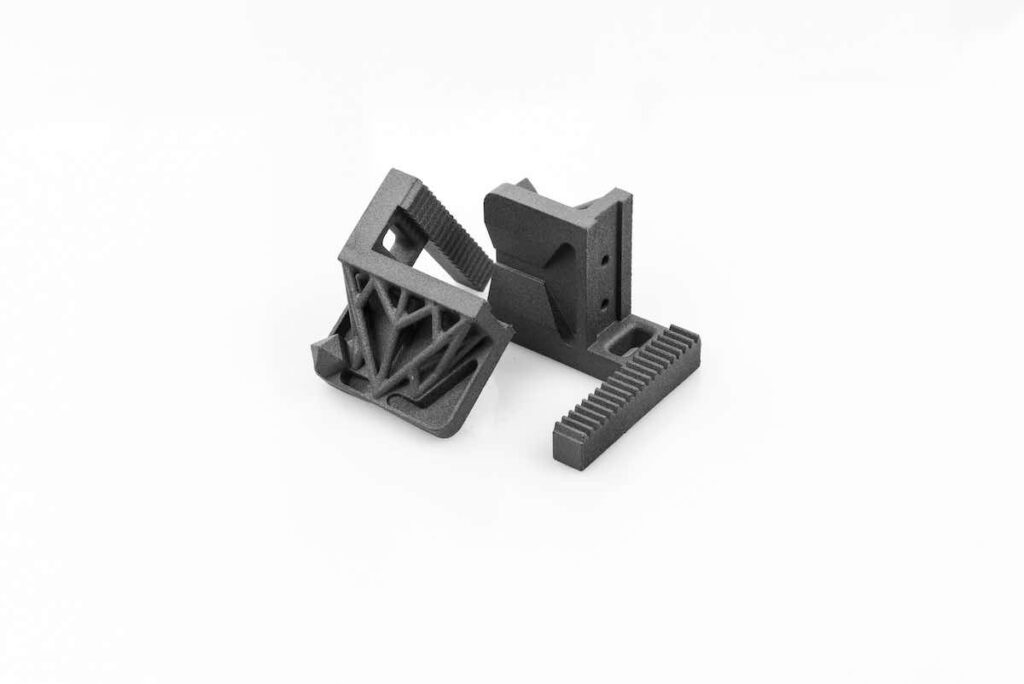
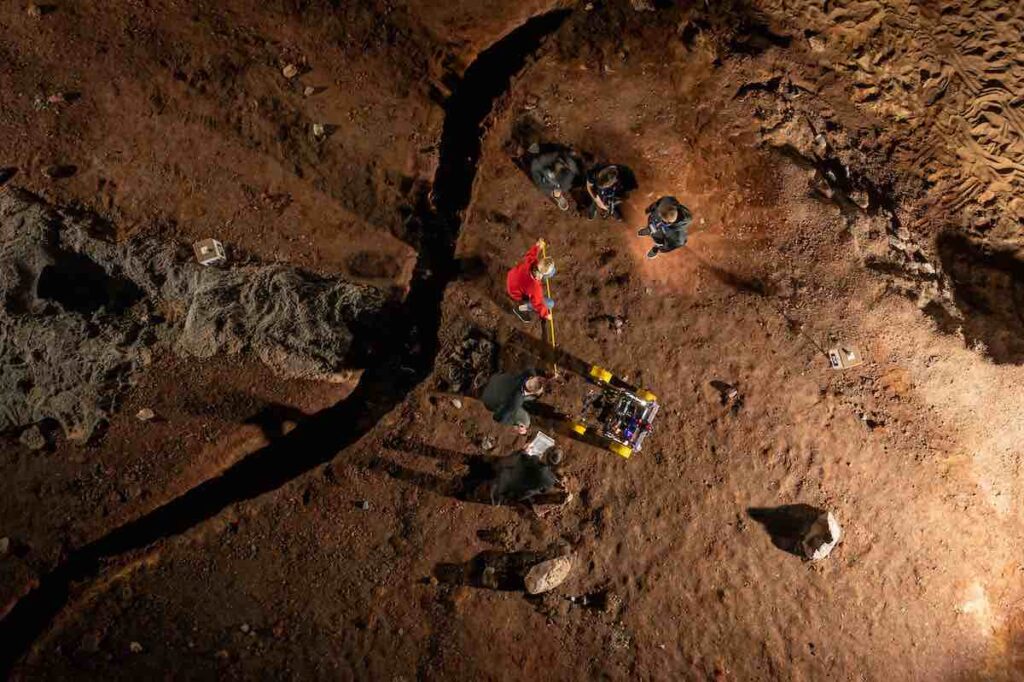
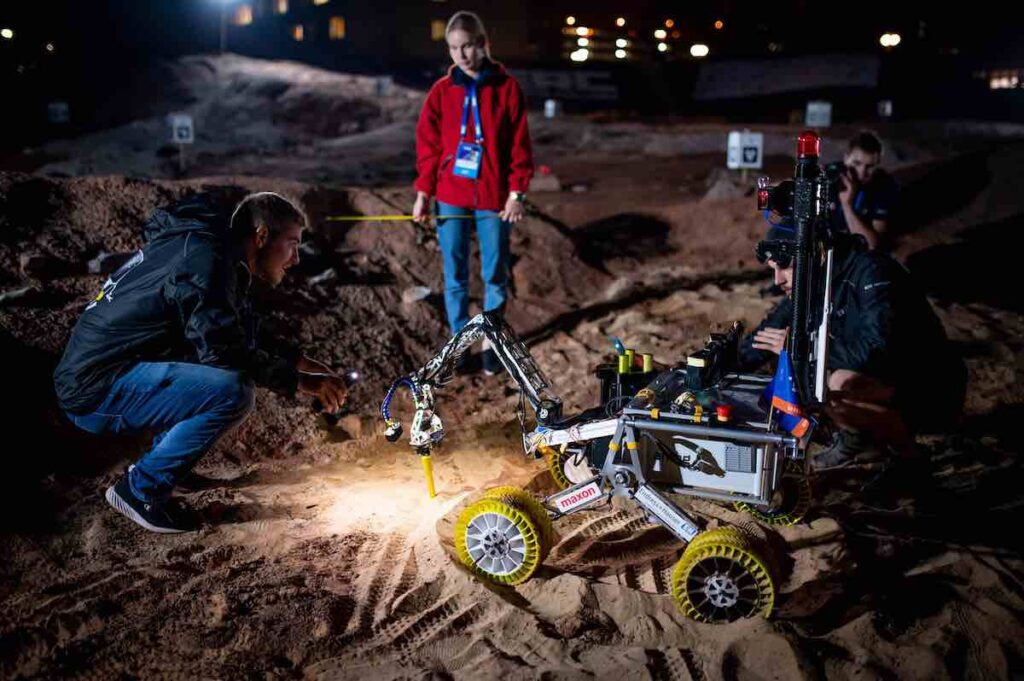
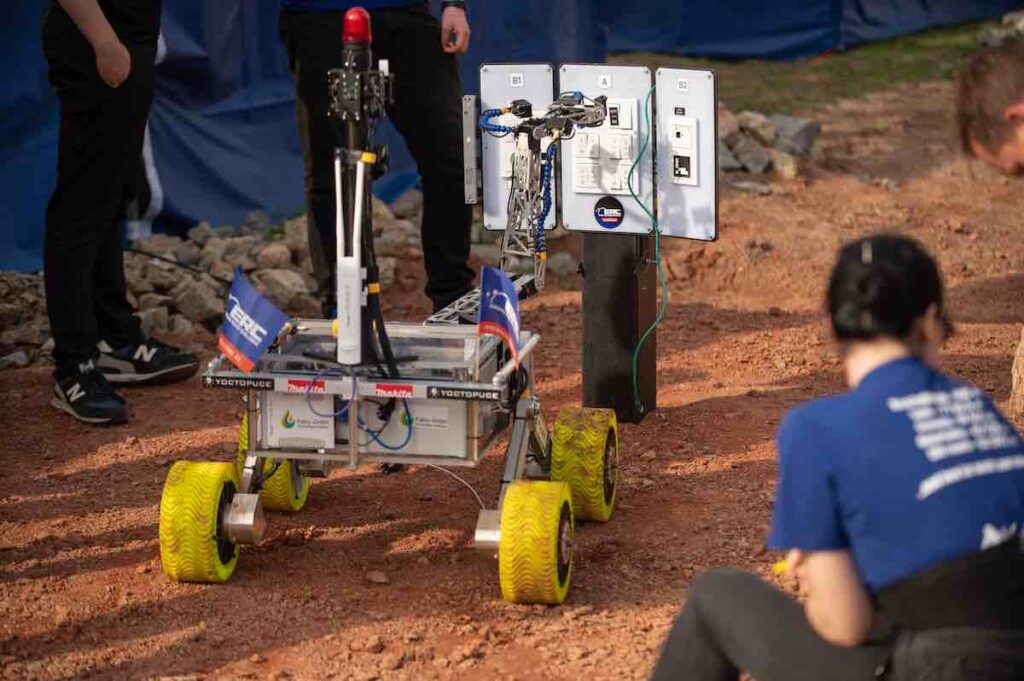
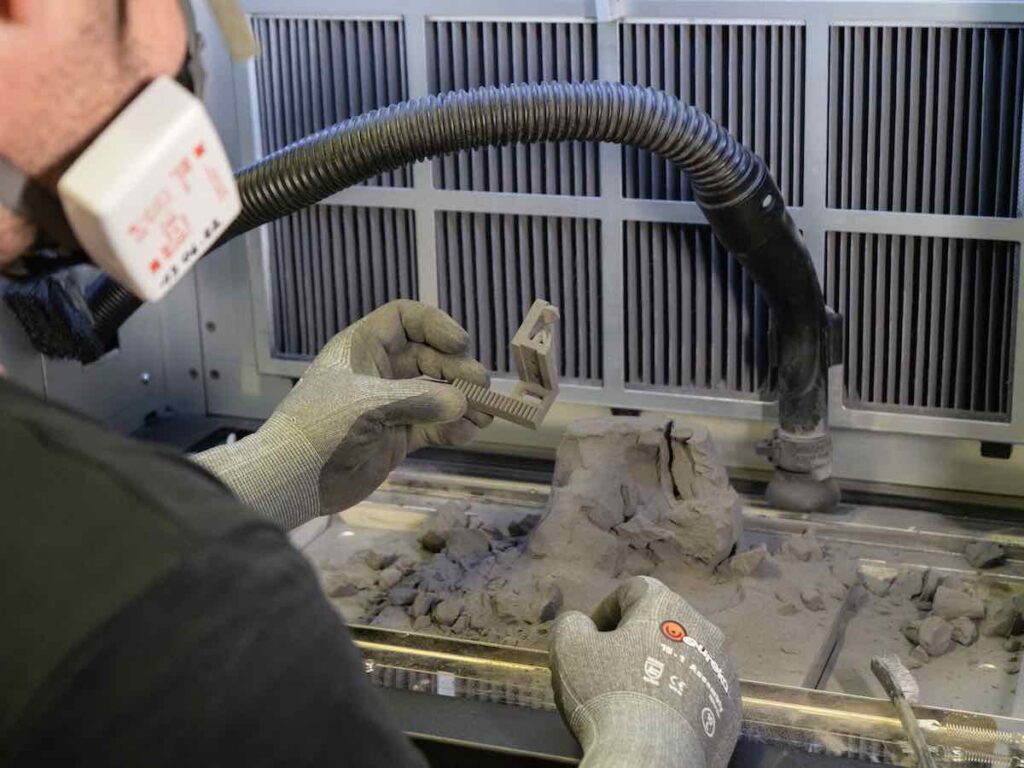
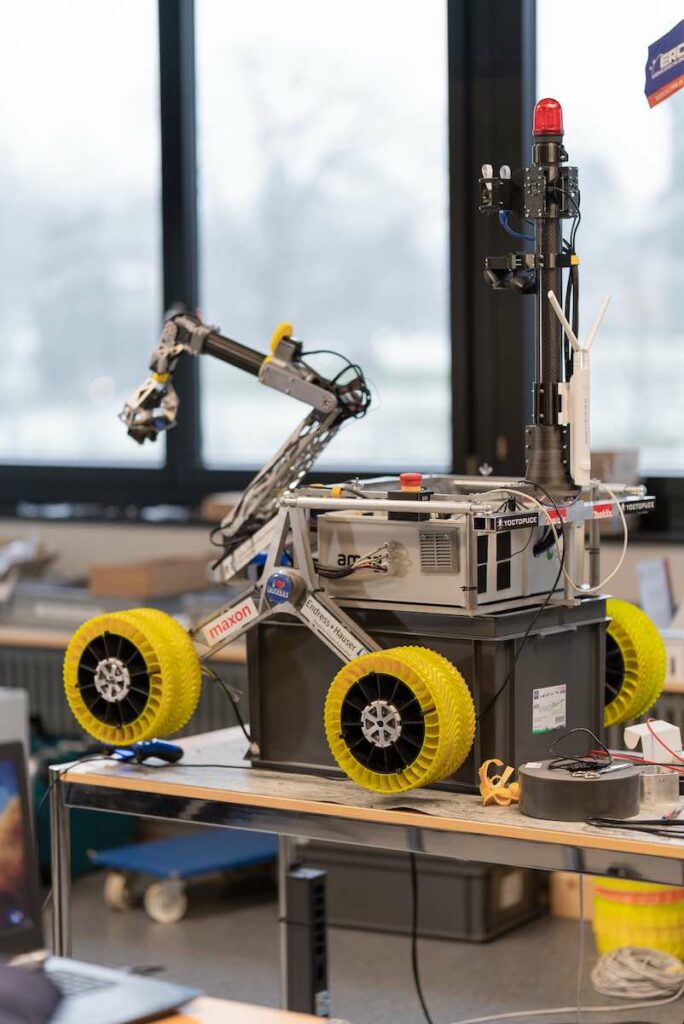
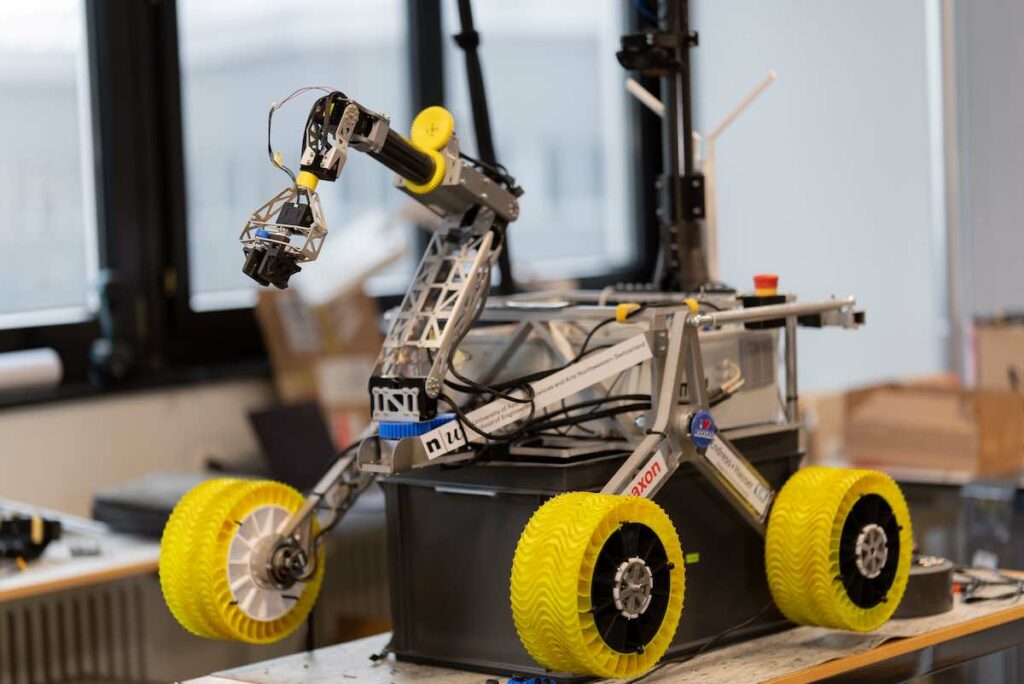
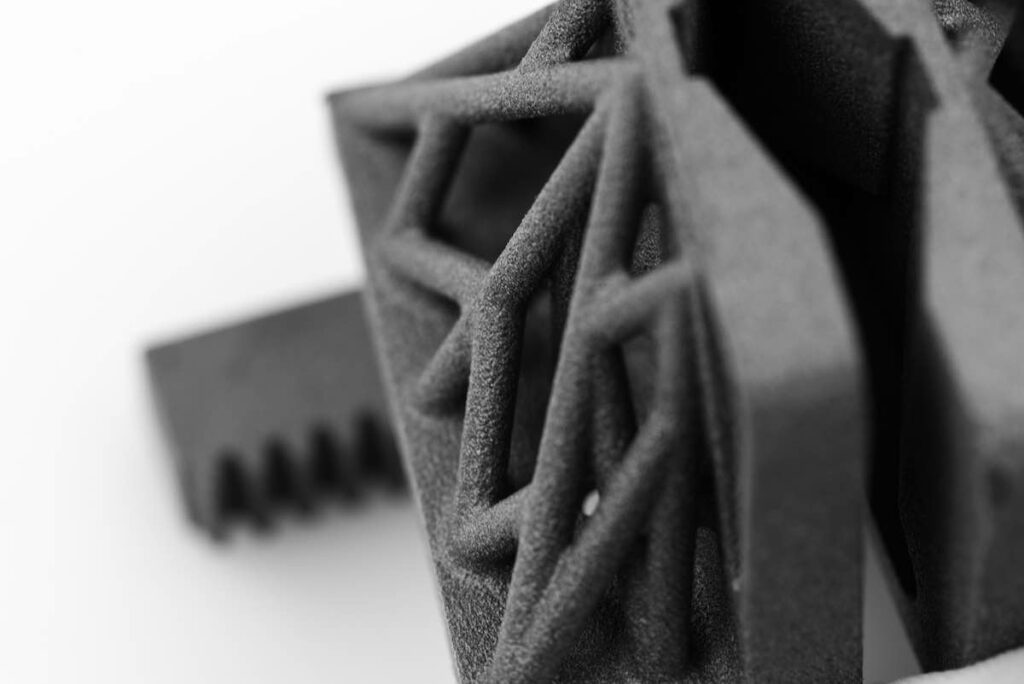