Un nuovo framework di deep learning sviluppato presso l’Oak Ridge National Laboratory del Dipartimento dell’Energia sta accelerando il processo di ispezione delle parti metalliche prodotte in modo additivo utilizzando la tomografia computerizzata a raggi X, o TC, aumentando al contempo l’accuratezza dei risultati. Si prevede che la riduzione dei costi di tempo, manodopera, manutenzione ed energia accelererà l’espansione della produzione additiva o della stampa 3D.
“La velocità di scansione riduce significativamente i costi”, ha affermato il ricercatore capo dell’ORNL Amir Ziabari. “E la qualità è maggiore, quindi l’analisi di post-elaborazione diventa molto più semplice.”
Il framework è già stato incorporato nel software utilizzato dal partner commerciale ZEISS all’interno delle sue macchine presso il Manufacturing Demonstration Facility del DOE presso ORNL, dove le aziende perfezionano i metodi di stampa 3D.
I ricercatori dell’ORNL avevano precedentemente sviluppato una tecnologia in grado di analizzare la qualità di una parte durante la stampa. L’aggiunta di un elevato livello di precisione dell’immagine dopo la stampa fornisce un ulteriore livello di fiducia nella produzione additiva, aumentando potenzialmente la produzione.
“Con questo, possiamo ispezionare ogni singola parte che esce dalle macchine per la stampa 3D”, ha affermato Pradeep Bhattad, responsabile dello sviluppo aziendale di ZEISS per la produzione additiva. “Attualmente la TC si limita alla prototipazione. Ma questo strumento può spingere la produzione additiva verso l’industrializzazione”.
La scansione TC a raggi X è importante per certificare la solidità di una parte stampata in 3D senza danneggiarla. Il processo è simile alla TC medica a raggi X. In questo caso, un oggetto posto all’interno di un armadietto viene ruotato lentamente e scansionato ad ogni angolo da potenti raggi X. Gli algoritmi informatici utilizzano la pila risultante di proiezioni bidimensionali per costruire un’immagine 3D che mostra la densità della struttura interna dell’oggetto. La TC a raggi X può essere utilizzata per rilevare difetti, analizzare guasti o certificare che un prodotto corrisponde alla composizione e alla qualità previste.
Tuttavia, la TC a raggi X non viene utilizzata su larga scala nella produzione additiva perché gli attuali metodi di scansione e analisi richiedono molto tempo e sono imprecisi. I metalli possono assorbire completamente i raggi X a bassa energia nel raggio di raggi X, creando imprecisioni nell’immagine che possono essere ulteriormente moltiplicate se l’oggetto ha una forma complessa. I difetti risultanti nell’immagine possono oscurare crepe o pori che la scansione dovrebbe rivelare. Un tecnico qualificato può correggere questi problemi durante l’analisi, ma il processo richiede tempo e lavoro.
Ziabari e il suo team hanno sviluppato un framework di deep learning che fornisce rapidamente una ricostruzione più chiara e accurata e un’analisi automatizzata. Presenterà il processo sviluppato dal suo team durante la conferenza internazionale sull’elaborazione delle immagini dell’Institute of Electrical and Electronics Engineers in ottobre.
La formazione di una rete di apprendimento profondo supervisionata per CT di solito richiede molte misurazioni costose. Poiché le parti metalliche pongono ulteriori sfide, ottenere i dati di addestramento appropriati può essere difficile. L’approccio di Ziabari fornisce un balzo in avanti generando dati di addestramento realistici senza richiedere esperimenti estesi per raccoglierli.
Un metodo generative adversarial network, o GAN, viene utilizzato per creare sinteticamente un set di dati dall’aspetto realistico per addestrare una rete neurale, sfruttando simulazioni basate sulla fisica e progettazione assistita da computer. GAN è una classe di machine learning che utilizza reti neurali in competizione tra loro come in un gioco. È stato usato raramente per applicazioni pratiche come questa, ha detto Ziabari.
Poiché questa struttura TC a raggi X necessita di scansioni con meno angoli per ottenere la precisione, ha ridotto il tempo di imaging di un fattore sei, ha affermato Ziabari, da circa un’ora a 10 minuti o meno. Lavorare così rapidamente con così pochi angoli di visualizzazione normalmente aggiungerebbe un “rumore” significativo all’immagine 3D. Ma l’algoritmo ORNL insegnato sui dati di addestramento lo corregge, migliorando anche il rilevamento di piccoli difetti di un fattore quattro o più.
Il framework sviluppato dal team di Ziabari consentirebbe ai produttori di mettere a punto rapidamente le loro build, anche cambiando design o materiali. Con questo approccio, l’analisi del campione può essere completata in un giorno anziché da sei a otto settimane, ha affermato Bhattad.
“Se posso ispezionare molto rapidamente l’intera parte in un modo molto conveniente, allora abbiamo il 100% di fiducia”, ha affermato. “Stiamo collaborando con ORNL per rendere CT uno strumento di ispezione del settore accessibile e affidabile”.
I ricercatori dell’ORNL hanno valutato le prestazioni del nuovo framework su centinaia di campioni stampati con parametri di scansione diversi, utilizzando materiali complessi e densi. Questi risultati sono stati buoni e le prove in corso presso MDF stanno lavorando per verificare che la tecnica sia ugualmente efficace con qualsiasi tipo di lega metallica, ha affermato Bhattad.
Questo è importante, perché l’approccio sviluppato dal team di Ziabari potrebbe rendere molto più semplice la certificazione di parti realizzate con nuove leghe metalliche. “Le persone non usano nuovi materiali perché non conoscono i migliori parametri di stampa”, ha detto Ziabari. “Ora, se è possibile caratterizzare questi materiali così rapidamente e ottimizzare i parametri, ciò aiuterebbe a spostare questi nuovi materiali nella produzione additiva”.
In effetti, ha affermato Ziabari, la tecnologia può essere applicata in molti campi, tra cui la difesa, la produzione automobilistica, la stampa aerospaziale ed elettronica, nonché la valutazione non distruttiva delle batterie dei veicoli elettrici.
UT-Battelle gestisce l’Oak Ridge National Laboratory per l’Office of Science del DOE, il più grande sostenitore della ricerca di base nelle scienze fisiche negli Stati Uniti. L’Office of Science del DOE sta lavorando per affrontare alcune delle sfide più urgenti del nostro tempo.
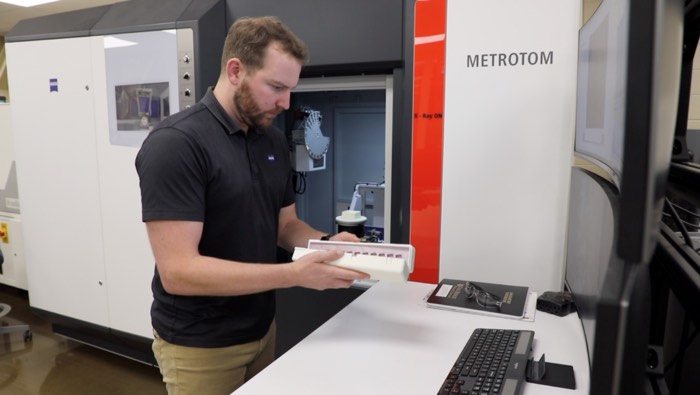
Paul Brackman carica campioni di metallo stampati in 3D in una torre per l’esame utilizzando una scansione TC a raggi X nell’impianto dimostrativo di produzione del DOE presso l’ORNL.
CREDITO
Brittany Cramer/ORNL, Dipartimento dell’Energia degli Stati Uniti