Il quad propulsore stampato in 3D di Aerojet Rocketdyne consente l’esplorazione dello spazio a basso costo
Gli ingegneri di Aerojet Rocketdyne hanno ottimizzato un componente chiave del loro quad thruster Reaction Control System (RCS) utilizzando la produzione additiva. Non solo la nuova parte del motore spaziale è più leggera del 67%, ma contribuisce anche alla riduzione del costo di produzione complessivo del propulsore del 66%
Gli ingegneri di Aerojet Rocketdyne hanno ottimizzato un componente chiave del loro quad thruster Reaction Control System (RCS) utilizzando la produzione additiva. Non solo la nuova parte del motore spaziale è più leggera del 67%, ma contribuisce anche alla riduzione del costo di produzione complessivo del propulsore del 66%, consentendo un’esplorazione lunare veloce, economica e sostenibile.
Sfondo
Sono passati quasi 50 anni dall’ultima visita dell’umanità sulla luna, con gli astronauti della missione Apollo 17 che atterrarono sulla superficie lunare l’11 dicembre 1972.
Cinque decenni dopo, il programma Artemis della NASA prepara il nostro ritorno sulla luna. L’ambizioso obiettivo finale è costruire un campo base permanente sulla superficie lunare e una stazione in orbita lunare. Ora, la domanda è: “come sarà il nostro prossimo viaggio sulla luna?” Ogni veicolo spaziale e lander lunare della missione Apollo presentava 4 quad thruster RCS posizionati attorno alla nave per controllarne l’orientamento durante il volo.
Aerojet Rocketdyne è un produttore di livello mondiale di sistemi energetici avanzati coinvolti nello sviluppo della propulsione per la navicella spaziale Orion e il sistema di lancio spaziale della NASA.
L’obiettivo del team di ingegneri è riprogettare i sistemi legacy del programma dell’era Apollo utilizzando moderne tecnologie di propulsione, progettazione e produzione per ridurre i costi, accelerare i tempi di sviluppo e produzione e migliorare le prestazioni.
“Se sfruttiamo i vantaggi che abbiamo ottenuto nell’ultimo decennio nell’ingegneria del software e nella produzione di hardware, possiamo costruire sottosistemi critici a frazioni del costo tradizionale, migliorando al contempo le prestazioni dei progetti del patrimonio”. — James Horton, Mission Architect presso Aerojet Rocketdyne
In questo caso di studio, trattiamo il processo seguito dal team per ottimizzare peso e costo dei componenti chiave del sistema di controllo della reazione (RCS). Questo sistema controlla l’altitudine e l’orientamento del veicolo spaziale e del lander lunare quando sono in volo.
Riprogettazione del sistema di controllo della reazione
L’RCS è costituito da quattro moduli di servizio posizionati attorno al veicolo spaziale e al lander lunare. Ogni modulo è dotato di quattro propulsori, ciascuno rivolto verso le quattro direzioni principali. Questa configurazione a quattro propulsori può sparare in modo indipendente per controllare la velocità, l’imbardata, il beccheggio e il rollio del veicolo spaziale, esercitando fino a 100 lbf (o 445 N).
Per il programma Apollo, la NASA ha commissionato la produzione di oltre 600 propulsori individuali per supportare 12 voli spaziali umani e test e qualifiche. La riduzione del costo di questi propulsori può intaccare in modo significativo il costo totale e l’accessibilità del programma Artemis.
“Come con qualsiasi impresa complessa, più conveniente puoi renderla, maggiore è la possibilità che tu ne garantisca il completamento e la luna non è diversa. La produzione additiva di metalli gioca un ruolo chiave nel raggiungimento di questi obiettivi”.
— James Horton, Mission Architect presso Aerojet Rocketdyne
Il design legacy del modulo RCS era un assieme che consisteva nei quattro propulsori, il collettore che alimenta il carburante e l’ossidante e un involucro multicomponente a pareti sottili per mettere insieme il tutto. James Horton, ingegnere aerospaziale e architetto di missione presso l’Aerojet Rocketdyne, e il suo team hanno identificato molte opportunità di miglioramento.
Il design del modulo quad thruster RCS: eredità contro epoca moderna
Il team ha deciso di raddoppiare la produzione additiva per migliorare l’accessibilità economica del design legacy e ridurre la complessità della build. La capacità di ridurre il numero di componenti attraverso il consolidamento di parti e funzioni riduce al minimo il costo della manodopera a contatto. Il consolidamento dell’assieme riduce anche i potenziali punti di guasto, aumentando l’affidabilità del sistema.
Gli ingegneri di Aerojet Rocketdyne hanno anche deciso di incorporare progressi nella tecnologia di propulsione a razzo per migliorare le prestazioni del sistema. Sono passati a MMH e MON-25, una nuova combinazione di combustibile per razzi e ossidante. MON-25 fornisce un riavvio più affidabile, è più facile da riporre durante i lunghi voli spaziali e richiede meno energia per prevenire il congelamento, riducendo il consumo energetico e il peso complessivi del sistema.
Tuttavia, i propulsori che utilizzano MON-25 richiedono un meccanismo di erogazione del carburante più efficiente e un design complesso per l’ugello e l’impianto idraulico del blocco iniettore.
Dall’ideazione alla qualificazione-ready
L’Aerojet Rocketdyne ha dimostrato la fattibilità di questo approccio completando i test a fuoco caldo nel 2019. Tuttavia, la prima iterazione di progettazione del blocco iniettore (o “Mark I”) non è stata ottimizzata per peso, producibilità e costo. Il team ha deciso che era necessario un ulteriore perfezionamento per rendere la loro proposta economicamente sostenibile.
“Ogni singola libbra di materiale che puoi rimuovere da un veicolo spaziale fa risparmiare sui costi di lancio. Ecco perché abbiamo utilizzato nTopology per ottimizzare il design e poi il sistema di Velo3D per realizzarlo”.
— James Horton, Mission Architect presso Aerojet Rocketdyne
I limiti di modellazione del CAD tradizionale hanno impedito ad Aerojet Rocketdyne di ottimizzare la prima iterazione del loro progetto per peso e costo
“Shell and Infill” per alleggerimento
Per la seconda iterazione, il team ha applicato un semplice concetto di alleggerimento. Innanzitutto, crea un guscio per rimuovere il materiale non necessario. Quindi, riempilo con una struttura a traliccio per garantire la producibilità e aumentare la rigidità.
L’approccio shell and infill è facile da concepire, ma era impossibile da implementare utilizzando i tradizionali software CAD a causa della complessità dei canali interni. La funzione di bombardamento fallirebbe semplicemente e il software andrebbe in crash. Il team ha trascorso molte ore cercando di risolvere questo problema senza successo durante lo sviluppo del progetto “Mark I”.
D’altra parte, con il motore di modellazione implicita di nTopology , hanno eseguito correttamente il bombardamento della parte al primo tentativo . Come bonus, è possibile aggiungere filetti a tutti i bordi per alleviare le concentrazioni di sollecitazioni e migliorare la resistenza alla fatica della parte.
Per perfezionare ulteriormente la struttura, il team di Horton ha controllato i parametri di progettazione chiave utilizzando la progettazione guidata sul campo , un’altra capacità unica di nTopology. Ad esempio, hanno creato una transizione graduale nello spessore della trave reticolare, più sottile al centro e più spessa vicino al guscio, per ridurre ulteriormente il peso della parte.
In poche ore , gli ingegneri di Aerojet Rocketdyne hanno creato un candidato progettuale pronto per la produzione con un fattore di sicurezza 2,5x basato sulla pressione massima del tubo.
Sezione trasversale del blocco iniettore ottimizzato
Dalla progettazione alla produzione
Il team ha utilizzato una stampante 3D in metallo Velo3D Sapphire per produrre la parte. Questo sistema consente la produzione di sporgenze più ripide e dettagli più fini rispetto ai tradizionali sistemi di fusione laser a letto di polvere di metallo.
Il materiale selezionato per questo progetto è stato il Titanio 6Al-4V, materiale tipico per propulsori bipropellenti. Il titanio ha circa la metà della densità dell’Inconel 718, il materiale utilizzato per produrre la precedente iterazione del progetto, contribuendo alla riduzione del peso delle parti. Tuttavia, è notoriamente più difficile stampare in 3D a causa degli effetti termici e delle screpolature.
Il blocco iniettore “Mark II” prodotto in Titanio 6Al-4V — pronto per ulteriori test
Tuttavia, il team ha stampato con successo la parte in 3D con un orientamento piatto, migliorando la qualità della superficie delle flange degli ugelli e delle facce degli iniettori. Inoltre, non era necessario alcun materiale di supporto per produrre i canali interni dell’impianto idraulico e l’intricato reticolo è stato stampato in 3D senza alcun difetto.
I prossimi passi
Il blocco iniettore prodotto in modo additivo è una parte intrinseca degli sforzi di Aerojet Rocketdyne per sviluppare un modulo RCS che sia 1/5 della massa, 1/2 delle dimensioni e 1/3 del costo delle alternative prodotte in modo convenzionale.
“Non sapevo se fosse anche possibile fare questo tipo di integrazione. Abbiamo dimostrato che questo è un percorso praticabile verso l’accessibilità, riducendo il numero di parti e toccando la manodopera. Non vedo l’ora di portare questo prodotto nello spazio”.
— James Horton, Mission Architect presso Aerojet Rocketdyne
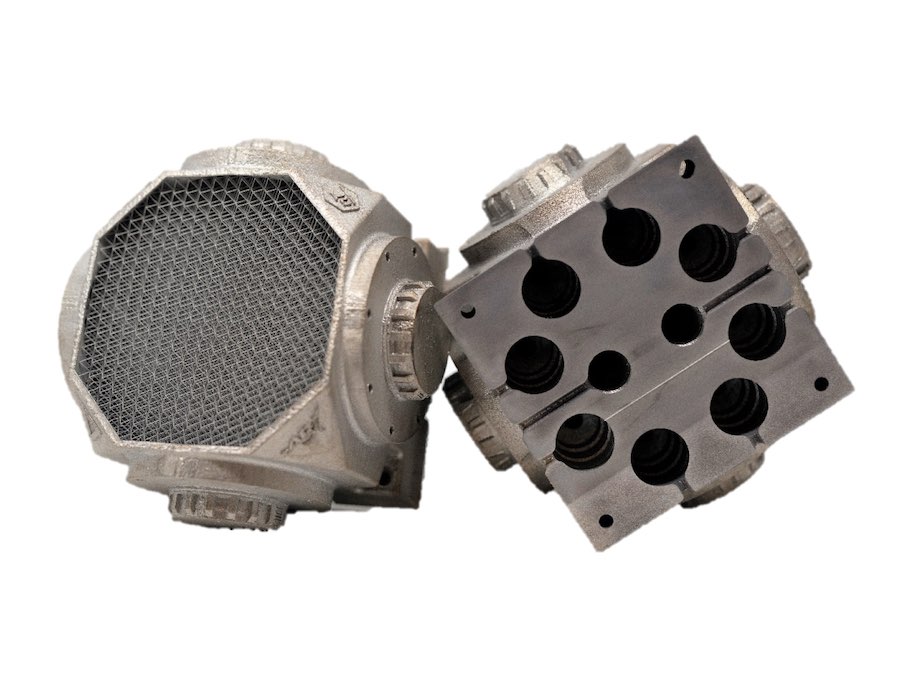