Il pioniere della tecnologia spaziale Maxar utilizza in orbita parti prodotte in modo additivo dal 2016. Da allora, la società ha lanciato più di 20 veicoli spaziali con parti stampate in 3D in alluminio, titanio e plastica, per un totale di oltre 2.500 componenti. Come parte della sua strategia di successo per incorporare parti stampate in 3D nel suo processo di produzione, Maxar ha recentemente celebrato una partnership quinquennale di successo con il produttore di stampa 3D in titanio con sede in Nuova Zelanda Zenith Tecnica . Le società hanno annunciato di aver stampato 260 parti in titanio per cinque veicoli spaziali e attualmente stanno producendo più di 270 componenti aggiuntivi per otto nuovi satelliti.
Riconosciuta come una delle principali aziende produttrici di satelliti in tutto il mondo, la cinquantenne Maxar sta seriamente incorporando tecnologie additive per semplificare la produzione di veicoli spaziali, aumentando esponenzialmente le sue parti stampate in 3D in soli tre anni. Durante questo periodo, l’azienda ha collaborato con diverse aziende leader di AM. Oltre a Zenith Tecnica, Maxar ha utilizzato anche macchine Stratasys per sviluppare i suoi satelliti di comunicazione GEO, diverse applicazioni AM e materiali specifici per lo spazio. Recentemente, Maxar ha collaborato con SWISSto12 per sfruttare l’innovativa e complessa tecnologia di stampa 3D dell’azienda per creare filtri per il mercato spaziale.
Mentre l’hype che circonda l’industria spaziale commerciale continua a crescere, questa nuova pietra miliare con Zenith Tecnica mostra come una maggiore adozione delle tecnologie AM sblocchi vantaggi significativi per la produzione di veicoli spaziali, come prestazioni migliorate e design più efficienti. I componenti stampati in 3D sono ora standard per tutti i satelliti costruiti da Maxar, con circa 1.000 parti stampate in 3D che volano su uno dei suoi veicoli spaziali. L’azienda con sede a Westminster, in Colorado, è stata una delle prime ad adottare le tecnologie di stampa 3D, istituendo il suo Centro di eccellenza additivo nel 2012. Ha convalidato l’AM come approccio innovativo e prezioso per la produzione di veicoli spaziali e ha identificato un processo per qualificare i componenti AM per il volo spaziale.
Di conseguenza, il titanio con fusione a fascio di elettroni (EBM) è stato qualificato per il volo e nel 2016 i primi componenti in titanio EBM erano in orbita. Zenith Tecnica afferma di aver intrapreso un processo di convalida e qualificazione per garantire che le tecniche e il materiale AM fossero affidabili. Alla fine, le parti in titanio stampate in 3D sono state costruite utilizzando macchine GE Additive Arcam EBM e quindi trattate termicamente, mentre le caratteristiche di assemblaggio critiche sono state lavorate. Infine, per garantire che tutte le parti fossero conformi alle specifiche, sono state eseguite ispezioni di scansione 3D.
“Il team di Zenith Tecnica opera come un’estensione del team di Maxar e fa sempre il possibile per garantire che le parti vengano consegnate con un elevato standard di qualità”, afferma Gina Ghiglieri Additive Manufacturing Technology Manager di Maxar. “Zenith Tecnica è con noi sin dai primi programmi di produzione additiva in metallo presso Maxar e ha svolto un ruolo fondamentale nell’aiutare a definire e qualificare questi processi produttivi.”
Focalizzata sulla produzione di hardware in titanio per molti settori, Zenith Tecnica sta sfruttando la personalizzazione di massa e le libertà geometriche di AM. Le sue parti in titanio stampate in 3D possono essere trovate in qualsiasi cosa, dai satelliti, agli aerei Air New Zealand , agli strumenti medici, agli impianti di ginocchio e anca, persino negli yacht dell’America’s Cup e nelle auto da corsa di Formula Uno .
I 15 ingegneri meccanici dell’azienda lavorano con almeno cinque macchine EBM GE Additive Arcam presso lo stabilimento di Auckland per ottimizzare la geometria dell’hardware e le caratteristiche termiche per specifiche caratteristiche satellitari e payload di cui i clienti, come Maxar, hanno bisogno. Come abbiamo visto accadere in molti settori, AM consente progetti precedentemente impossibili attraverso metodi di produzione tradizionali, oltre a vantaggi aggiuntivi, come massa ridotta delle parti, meno pezzi di hardware e una migliore vita in orbita..
Da quando ha introdotto l’AM nella produzione di componenti per veicoli spaziali , Maxar ha migliorato l’agilità di pianificazione, ridotto i costi di produzione e aumentato le prestazioni dei satelliti. Ha descritto brevi tempi di produzione per veicoli spaziali, circa due o tre anni, e strumenti stampati in 3D per supportare il veicolo spaziale durante l’assemblaggio e il test. Un altro vantaggio fondamentale della tecnologia è la produzione di parti personalizzate con geometrie specifiche per ciascun satellite, riducendo la massa e il numero di hardware. Maxar sa che può migliorare la vita in orbita attraverso una massa inferiore e una migliore distorsione termica e prestazioni sfruttando questa tecnologia per la produzione.
Con così tanti vantaggi per l’ industria spaziale , la tecnologia AM svolge un ruolo significativo nella produzione di veicoli spaziali. Mentre le aziende e le startup continuano a sviluppare le proprie capacità di stampa 3D in loco e a collaborare con gli uffici di servizi per ridimensionare le parti stampate in 3D, diventa sempre più chiaro che l’interruzione dell’AM in questo settore non è solo inevitabile, ma potrebbe prosperare nel prossimo decennio .
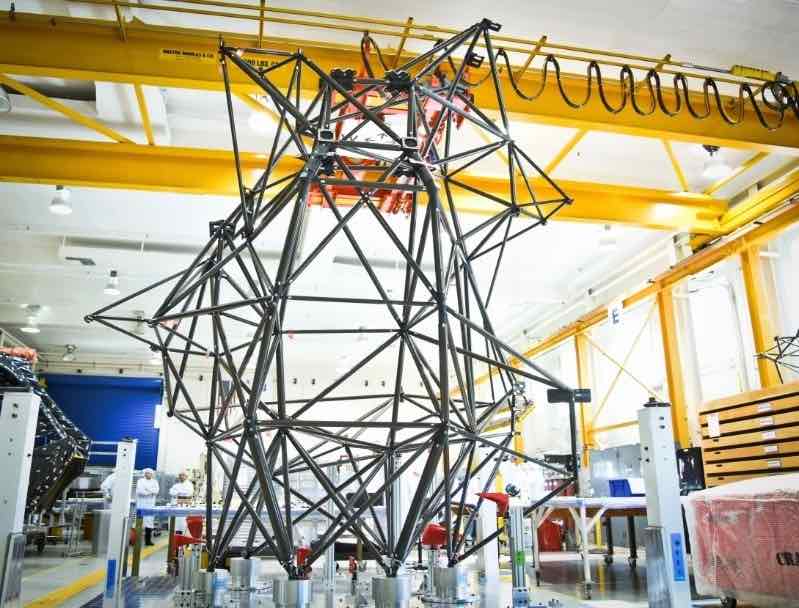