CRP TECHNOLOGY E MIRO BURONI 3D PRINT NOVEL PLEKO SCARPE CHIODATE IN FIBRA DI CARBONIO
Il fornitore di materiali e servizi di stampa 3D CRP Technology ha implementato le sue capacità di stampa 3D e il materiale in fibra di carbonio Windform SP per creare una scarpa da pista innovativa per l’atletica.
Lavorando con il mezzofondista veneziano Miro Buroni, l’azienda ha stampato in 3D la scarpa chiodata, denominata Pleko, in un unico pezzo utilizzando la sua tecnologia di sinterizzazione laser a fusione a letto di polvere (PBF).
Secondo Buroni, la flessibilità offerta dalla stampa 3D e le caratteristiche meccaniche del materiale Windform SP di CRP Technology gli hanno permesso di portare il suo progetto al “più alto livello” di personalizzazione e specializzazione.
Oltre a CRP Technology, Buroni ha anche arruolato le competenze del produttore italiano di abbigliamento sportivo Diadora per aiutare a progettare la scarpa chiodata. Hanno iniziato scansionando in 3D il piede di un atleta e conducendo un’analisi biomeccanica della corsa e del movimento del piede.
“Con questa mappatura, siamo stati in grado di modellare la scarpa sulle esigenze individuali in termini di struttura del piede e prestazioni atletiche”, ha affermato Buroni. “Inoltre, la scansione e l’analisi biomeccanica ci hanno permesso di comprendere il miglior posizionamento del sistema di trazione sotto la suola: i ‘perni'”.
Una volta completata la fase di progettazione, Buroni ha cercato CRP Technology per fornire le capacità e i materiali di stampa 3D per portare a compimento il progetto. Le scarpe Pleko richiedevano un materiale con “forti caratteristiche di resistenza alla flessione” per la fabbricazione della suola, dell’intersuola e delle strutture a coste, per garantire che la forza ottimale fosse trasmessa alle scarpe durante le corse.
“Dopo una breve ricerca, è apparso subito chiaro che CRP Technology era l’azienda perfetta per realizzare il mio progetto e che uno dei migliori materiali compositi di CRP Technology, Windform SP, era il materiale da costruzione appropriato”, ha affermato Buroni.
Windform SP è un materiale composito caricato con fibra di carbonio della gamma di compositi Windform TOP-LINE di CRP Technology per la sinterizzazione laser di PBF. L’attuale gamma Windform dell’azienda include i suoi compositi F1, XP, SP, FR, GT, LX, RL e FR2 , con la sua aggiunta più recente Windform RS , un altro materiale composito caricato con fibra di carbonio appositamente progettato per la stampa 3D PBF.
CRP Technology ha sviluppato il suo primo materiale di stampa 3D Windform nel 1996, che è stato successivamente sostituito da Windform XT nel 2005, il primo composito rinforzato con fibra di carbonio per la stampa 3D SLS. Da allora, la gamma di compositi Windform TOP-LINE è stata impiegata per un’ampia gamma di prototipi altamente impegnativi e applicazioni per uso finale, come telai portacellulare per batterie e satelliti tascabili e deployer .
Windform SP è stato precedentemente sfruttato dallo specialista della sicurezza Joyson Safety Systems per stampare in 3D un prototipo di contenitore funzionale per airbag . Il materiale necessario per mantenere una resistenza, una resistenza agli urti e una stabilità al calore sufficienti per soddisfare i severi requisiti di sicurezza della parte. Windform SP è stato anche distribuito per stampare in 3D un condotto funzionale del Comitato consultivo nazionale per l’aeronautica (NACA) per il suo veicolo Streamliner.
Le proprietà meccaniche di Windform SP hanno attratto anche Buroni durante la sua ricerca di un materiale adatto per creare le sue scarpe chiodate Pleko.
“Windform SP garantisce un’ottima resistenza anche in spessori molto sottili”, ha affermato. “Questa caratteristica mi ha permesso di creare scarpe chiodate con un perfetto avvolgimento del piede, che facilita un aumento del comfort e il miglioramento delle prestazioni.”
CRP Technology è stata incaricata di stampare in 3D non solo la suola, l’intersuola e i perni di Pleko, ma anche le “nervature” della scarpa, che hanno origine da sotto la suola e racchiudono la scarpa dove viene diretto il massimo sforzo attraverso la scarpa durante una gara.
Responsabile del trasporto dell’energia cinetica rilasciata dal movimento biomeccanico di un atleta durante una gara, la struttura a coste è progettata per abbracciare il piede dell’atleta “come una gabbia” al fine di facilitare i miglioramenti nella sua tecnica di corsa. Per ottenere questo effetto, CRP Technology ha stampato in 3D la suola, l’intersuola, i perni e le nervature come una singola unità in Windform SP.
“Grazie ai perni sotto la suola, la gabbia in Windform SP permette all’atleta di sviluppare quanta più forza possibile, senza perdere energia”, ha detto Buroni. “Ho posizionato i perni più profondi nei punti di maggiore pressione dei piedi contro il suolo. Ho anche messo dei tacchetti più piccoli in altre parti della suola: questi tacchetti sono ugualmente essenziali per la stabilità delle scarpe da pista”.
Il risultato finale ha prodotto un prototipo funzionale resistente alla deformazione anche nei suoi spessori più sottili, pur rimanendo flessibile. Il design è stato completato da una tomaia simile a un calzino che è quasi completamente staccata dalla struttura e responsabile della protezione del piede.
Una volta stampata la parte strutturale della Pleko, Buroni ha effettuato una serie di test sulla scarpa chiodata per valutarne le prestazioni.
“Le tecnologie di progettazione e produzione, combinate con Windform SP e le sue caratteristiche meccaniche, hanno reso le scarpe da pista Pleko altamente innovative, portando l’intero progetto al massimo livello di personalizzazione e specializzazione”, ha continuato Buroni. “Sono molto soddisfatto dei miei Pleko e Windform SP stampati in 3D.”
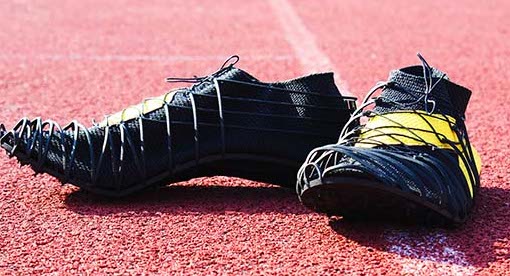