Quando si tratta di tecnologie energetiche alternative, le turbine eoliche sono facilmente le più riconoscibili. Torreggiando ad altezze di 137-259 m (450-850 piedi) con un diametro del rotore compreso tra 109-236 m (360-774 piedi), dominano l’ambiente circostante e sono spesso visibili per miglia. Se hai mai visto una turbina eolica, è probabile che sia stata prodotta da Vestas.
Vestas iniziò nella Danimarca del secondo dopoguerra come un piccolo produttore a conduzione familiare. Per molti anni, l’azienda ha costruito e fornito idraulica per autocarri leggeri. Durante gli anni ’70, ha iniziato a sviluppare soluzioni energetiche alternative, completando la sua prima turbina eolica commerciale nel 1979. Concentrandosi esclusivamente sulla produzione di turbine eoliche dal 1989, l’azienda progetta, produce, installa e fornisce servizi di turbine eoliche in tutto il mondo. Oggi, Vestas è il più grande produttore mondiale di turbine eoliche e pale per turbine eoliche on e offshore. L’azienda ha sede in Danimarca, diversi uffici regionali e oltre 15 stabilimenti di produzione in tutto il mondo.
La sfida
Le turbine eoliche sono macchine enormi e costose che devono funzionare in modo affidabile con tempi di fermo minimi per essere il più efficaci possibile. Ciò significa che non c’è spazio per errori quando si tratta di produzione e installazione. Di conseguenza, Vestas dipende da numerosi calibri di ispezione presso i suoi impianti di produzione e siti di installazione. Questi strumenti critici sono stati tradizionalmente acquistati da più fornitori in tutto il mondo sulla base di istruzioni di produzione dettagliate. Le parti finite sarebbero state inviate ai vari siti Vestas, ispezionate per verificarne la conformità e, una volta approvate, messe in uso. Sfortunatamente, alcune delle parti finali fornite dai produttori locali non erano al 100% conformi alle specifiche e non hanno superato l’ispezione finale. Ciò ha comportato ritardi nella consegna del prodotto finale e nell’installazione.
Anche quando le parti sono state prodotte attraverso il processo di ispezione specializzato, la maggior parte è stata prodotta utilizzando metodi di lavorazione tradizionali e materie prime costosi e dispendiosi in termini di tempo. Prendi, ad esempio, gli strumenti di marcatura in alto al centro (TC). Questi strumenti critici, utilizzati da Vestas per contrassegnare l’estremità della radice delle pale delle turbine per allineare il passo, richiederebbero in genere circa cinque settimane per essere prodotti. A peggiorare le cose, a causa dei limiti sui progetti lavorati, il team Vestas dovrebbe ordinare più versioni dello strumento di marcatura TC per adattarsi a una gamma di lame. Oppure, considera i recettori della punta del fulmine progettati per ridurre i danni dei fulmini. Questi recettori sono costruiti tramite la produzione sottrattiva in alluminio che richiede almeno 12 settimane per la produzione.
Strumento di marcatura Vestas TC utilizzato per contrassegnare l’estremità della radice delle pale della turbina per allineare il passo durante l’installazione.
“Vestas sta democratizzando la produzione mettendola nelle mani dei nostri utenti finali mantenendo un modello di controllo ingegneristico centralizzato”.
– Jeremy Haight, ingegnere principale, produzione additiva e concetti avanzati, Vestas
La soluzione
Il team Vestas ha iniziato a ricercare modi alternativi per migliorare il processo di produzione generale. Utilizzando la piattaforma di produzione additiva Digital Forge basata su cloud e basata sull’intelligenza artificiale di Markforged, l’azienda ha lanciato con successo il suo programma di produzione digitale diretta (DDM) nel 2021. Il programma libera i processi di produzione dall’affidarsi a fornitori esterni e fornisce una base di conoscenze per la collaborazione.
Il programma DDM include già oltre 2000 parti Vestas archiviate in un repository digitale basato su cloud Markforged Eiger™. Ciò consente ai dipendenti di qualsiasi sede Vestas, con poca o nessuna esperienza di produzione additiva, di cercare e stampare rapidamente un numero qualsiasi di parti composite rinforzate con fibre sulle loro X7™ locali e parti composite sulle loro stampanti 3D Onyx One™. Secondo Jeremy Haight, Principal Engineer for Additive Manufacturing & Advanced Concepts di Vestas, “Il nostro approccio è end-to-end. Forniamo l’articolo fisico quasi in tempo reale in una varietà di luoghi. È la cosa più vicina al teletrasporto che penso tu possa ottenere. Grazie al repository, il team Vestas sa che otterrà parti coerenti e conformi alle specifiche in un attimo, in qualsiasi parte del mondo, senza la necessità di specialisti nelle loro strutture globali. Ciò ha ridotto drasticamente i costi di spedizione e trasporto e i tempi di produzione.
Vestas considera il DDM un fattore critico per lo sviluppo di nuovi prodotti e la disponibilità di strumenti e parti per uso finale in tutta la sua attività. Nel 2022, l’azienda comincerà a implementare il DDM per gli strumenti di ispezione dei calibri oltre le sue lame per facilitare la produzione di calibri su richiesta in tutte le 23 sedi di produzione. Vestas ha anche collaborato con Würth per costruire un ecosistema additivo e gestire un inventario di pezzi di ricambio realizzati con la piattaforma The Digital Forge per supportare la manutenzione, la riparazione e le operazioni (MRO) per il supporto sul campo locale e altri fornitori.
Una volta completato il roll-out iniziale, Vestas rivolgerà la sua attenzione all’implementazione di un processo end-to-end più approfondito nei suoi siti. L’azienda sta rendendo più semplice per le persone in qualsiasi sito Vestas con le autorizzazioni giuste la scansione di un codice parte o la ricerca di una parte nei suoi sistemi EAM (Enterprise Asset Management) e pianificazione delle risorse aziendali (ERP) e inviarlo automaticamente al stampante 3D locale giusta. Questo controllo centralizzato di utenti, stampanti e ispezione delle parti, tramite Blacksmith ed Eiger Fleet™, garantirà strumenti di alta qualità e prestazioni elevate e parti di uso finale che svolgono i lavori per cui sono state progettate. Più Vestas porta la produzione internamente tramite la produzione additiva, più velocemente i suoi prodotti raggiungeranno il mercato e più tempo e denaro risparmieranno nel processo.
I membri del team Vestas AM guidano gli sforzi per garantire la qualità e le prestazioni degli strumenti e delle parti di uso finale.
Partner contraffatto
Würth
Tutti i blog e le informazioni in essi contenuti sono protetti da copyright di Markforged, Inc. e non possono essere copiati, modificati o adottati in alcun modo senza la nostra autorizzazione scritta. I nostri blog possono contenere i nostri marchi di servizio o marchi registrati, nonché quelli dei nostri affiliati. L’utilizzo dei nostri blog da parte dell’utente non costituisce alcun diritto o licenza per l’utilizzo dei nostri marchi di servizio o marchi senza la nostra previa autorizzazione. Markforged Le informazioni fornite nei nostri blog non devono essere considerate una consulenza professionale. Non abbiamo alcun obbligo di aggiornare o rivedere i blog in base a nuove informazioni, eventi successivi o altro.
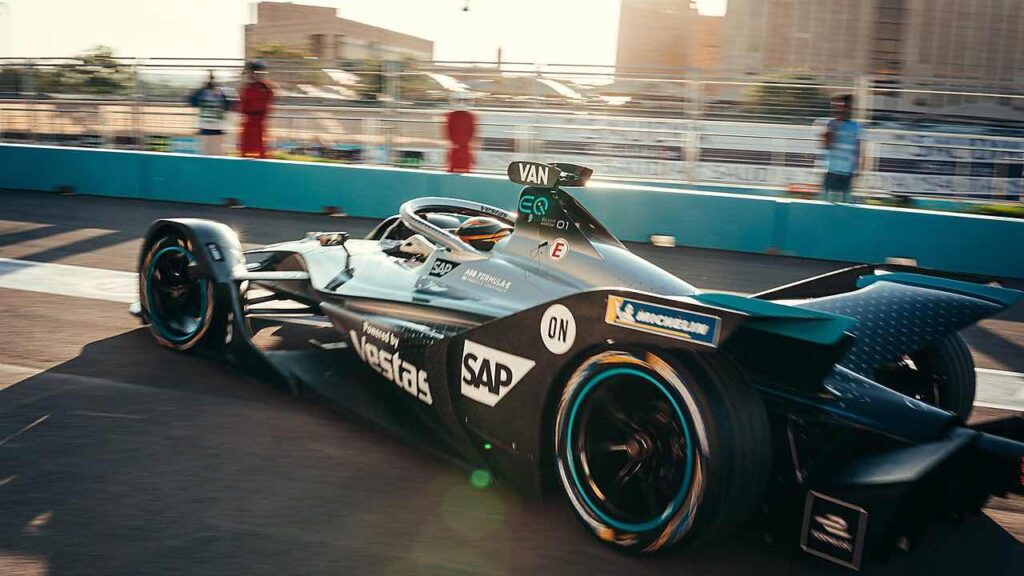